- お役立ち記事
- Building Purchasing Strategies to Support Lean Production
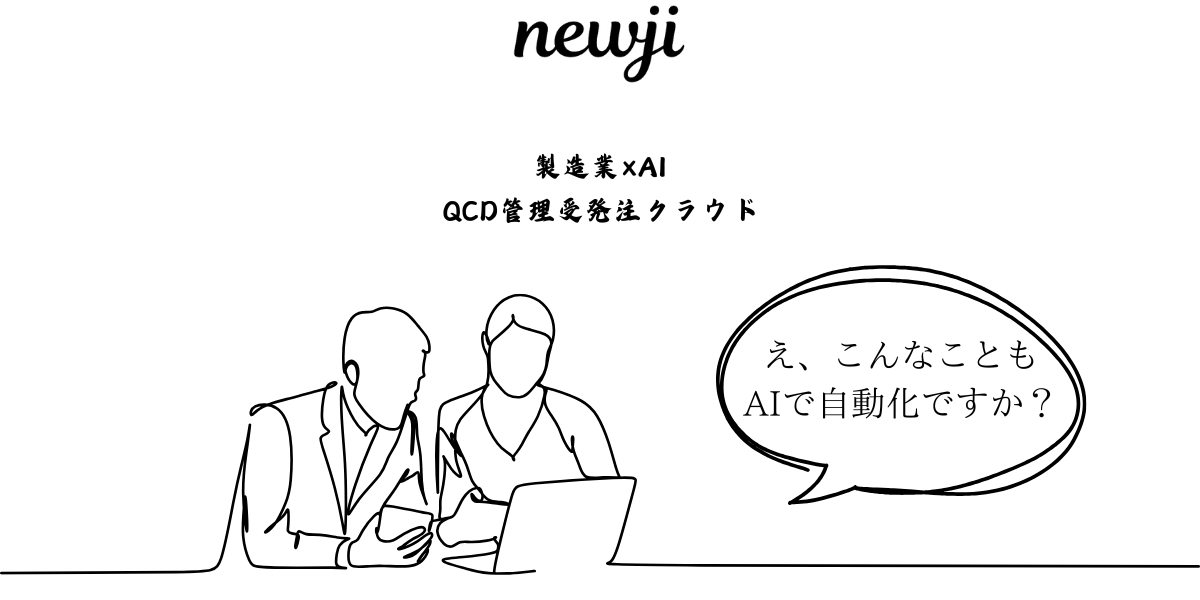
Building Purchasing Strategies to Support Lean Production
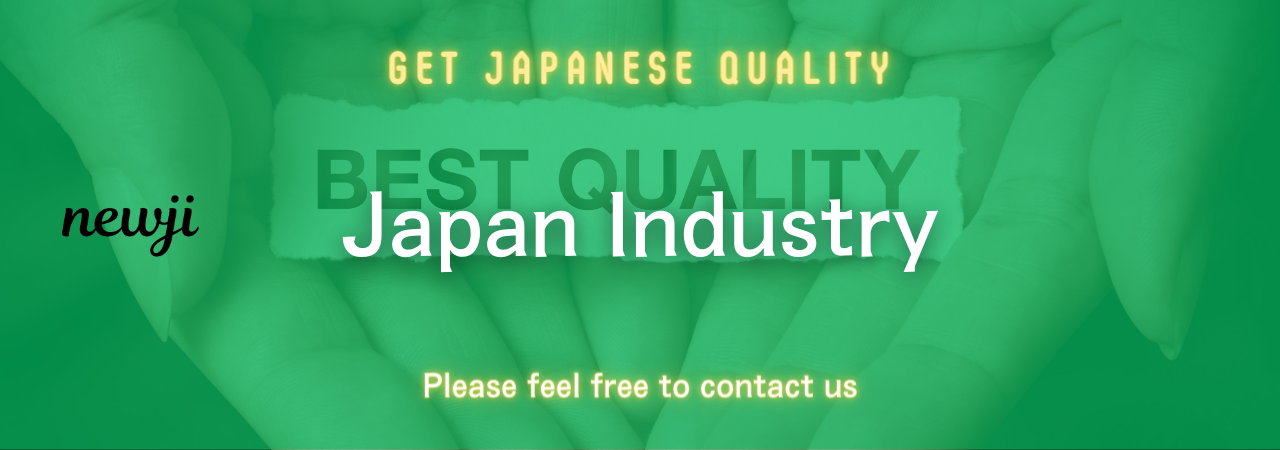
Lean production is an approach to manufacturing that emphasizes efficiency, reducing waste, and enhancing value for the customer.
One of the key elements of lean production is an effective purchasing strategy.
In this article, we will discuss how to build purchasing strategies that align with lean production principles.
目次
Understanding Lean Production
Lean production, also known as lean manufacturing, has its roots in the Toyota Production System.
The central tenet of lean production is to maximize customer value while minimizing waste.
This involves streamlining operations, eliminating unnecessary steps, and focusing on continual improvement.
Lean production is more than just a set of tools and techniques; it is a mindset and a culture that permeates every part of an organization.
It requires a commitment to improving processes, involving employees at all levels, and understanding customer needs in depth.
One crucial component of lean production is the relationship between manufacturing and suppliers.
Purchasing decisions can significantly impact production efficiency, cost control, and overall profitability.
Developing a Lean Purchasing Strategy
Aligning Goals with Lean Principles
To build an effective purchasing strategy, it is essential to align purchasing goals with lean principles.
Start by identifying the specific goals of your lean production system, such as reducing inventory levels, improving quality, and enhancing flow.
Purchasing goals should support these objectives by focusing on acquiring materials and services that meet quality standards, are delivered just in time, and are cost-effective.
Establishing clear communication and shared goals between the purchasing team and other departments is crucial.
Selecting the Right Suppliers
Supplier selection plays a vital role in achieving lean production.
Choose suppliers who understand lean principles and are willing to collaborate closely.
Look for suppliers with a proven track record of quality, reliability, and flexibility.
Building long-term relationships with a smaller number of trusted suppliers often yields better results than constantly switching between multiple vendors.
One effective strategy is to engage in Supplier Relationship Management (SRM).
This approach involves collaboration, communication, and continuous improvement efforts with suppliers.
By working together, both parties can identify areas for cost reduction, quality improvement, and process optimization.
Consider conducting supplier assessments to evaluate their capabilities and alignment with your lean production goals.
Implementing Just-in-Time (JIT) Purchasing
Just-in-Time (JIT) purchasing is a core component of lean production.
JIT aims to reduce inventory levels by aligning material deliveries closely with production schedules.
This minimizes waste, reduces storage costs, and improves cash flow.
Work closely with suppliers to develop JIT delivery schedules and ensure that materials arrive exactly when needed.
To implement JIT purchasing successfully, maintain clear and consistent communication with suppliers.
Use electronic data interchange (EDI) and other technology solutions to streamline ordering and tracking processes.
Regularly review and adjust JIT schedules based on production changes and demand forecasts.
Enhancing Supplier Collaboration
Effective collaboration with suppliers can lead to significant benefits in a lean production environment.
Encourage open communication and transparency with your suppliers.
Share your production schedules, demand forecasts, and any changes in requirements in real time.
Collaborative planning can help suppliers better understand your needs and adjust their processes accordingly.
Involving key suppliers in product design and development can also lead to more efficient production processes and higher-quality materials.
Consider holding regular meetings, workshops, and joint improvement initiatives with suppliers to foster a culture of continuous improvement.
Monitoring and Measuring Performance
Key Performance Indicators (KPIs)
To ensure that your purchasing strategy supports lean production effectively, it is crucial to monitor and measure performance regularly.
Implement key performance indicators (KPIs) to track various aspects of your purchasing process.
Some crucial KPIs to consider include:
– **Supplier On-Time Delivery**: Measure the percentage of deliveries that arrive on schedule.
This helps assess the reliability of your suppliers.
– **Quality of Materials**: Track the percentage of materials that meet quality standards.
Poor-quality materials can lead to production delays and increased costs.
– **Inventory Turnover**: Measure how quickly inventory is used and replenished.
Higher turnover rates indicate efficient inventory management.
– **Cost Reduction**: Monitor cost savings achieved through negotiations, bulk purchasing, and process improvements.
– **Lead Time**: Measure the time it takes from placing an order to receiving the materials.
Shorter lead times contribute to increased flexibility and agility in production.
Regular Audits and Reviews
Conduct regular audits and reviews of your purchasing processes and supplier performance.
Identify areas where improvements can be made and implement corrective actions as needed.
Engage in continuous improvement by leveraging feedback from both internal teams and suppliers.
Using Technology to Support Lean Purchasing
Effective use of technology can significantly enhance your lean purchasing strategy.
Implementing robust software systems can streamline purchasing processes, improve data accuracy, and enhance collaboration.
Consider the following technology solutions to support lean purchasing:
Purchasing Management Systems
Invest in a purchasing management system that integrates with your existing enterprise resource planning (ERP) system.
This ensures that purchasing data is captured accurately and allows for real-time visibility into inventory levels, order status, and supplier performance.
Automated workflows can reduce manual errors and speed up the purchasing process.
Supply Chain Visibility Tools
Utilize supply chain visibility tools to gain insights into the entire supply chain.
These tools provide real-time information on material availability, lead times, and potential disruptions.
Enhanced visibility allows for better decision-making and proactive problem-solving.
Advance supply chain analytics can also help identify trends and optimize purchasing strategies.
Collaboration Platforms
Collaboration platforms enable seamless communication and information sharing between your organization and suppliers.
These platforms facilitate collaborative planning, forecasting, and replenishment (CPFR), which can lead to better demand management and reduced inventory levels.
Effective collaboration ensures that both parties are aligned and can respond quickly to changes in demand or production schedules.
In conclusion, building purchasing strategies to support lean production involves aligning purchasing goals with lean principles, selecting the right suppliers, implementing JIT purchasing, enhancing supplier collaboration, monitoring performance, and leveraging technology.
By adopting these approaches, organizations can create an efficient, cost-effective, and resilient supply chain that supports their lean production goals.
資料ダウンロード
QCD調達購買管理クラウド「newji」は、調達購買部門で必要なQCD管理全てを備えた、現場特化型兼クラウド型の今世紀最高の購買管理システムとなります。
ユーザー登録
調達購買業務の効率化だけでなく、システムを導入することで、コスト削減や製品・資材のステータス可視化のほか、属人化していた購買情報の共有化による内部不正防止や統制にも役立ちます。
NEWJI DX
製造業に特化したデジタルトランスフォーメーション(DX)の実現を目指す請負開発型のコンサルティングサービスです。AI、iPaaS、および先端の技術を駆使して、製造プロセスの効率化、業務効率化、チームワーク強化、コスト削減、品質向上を実現します。このサービスは、製造業の課題を深く理解し、それに対する最適なデジタルソリューションを提供することで、企業が持続的な成長とイノベーションを達成できるようサポートします。
オンライン講座
製造業、主に購買・調達部門にお勤めの方々に向けた情報を配信しております。
新任の方やベテランの方、管理職を対象とした幅広いコンテンツをご用意しております。
お問い合わせ
コストダウンが利益に直結する術だと理解していても、なかなか前に進めることができない状況。そんな時は、newjiのコストダウン自動化機能で大きく利益貢献しよう!
(Β版非公開)