- お役立ち記事
- Causes and Prevention of Purchasing Errors: Improve procurement processes to control product quality and delivery time
Causes and Prevention of Purchasing Errors: Improve procurement processes to control product quality and delivery time
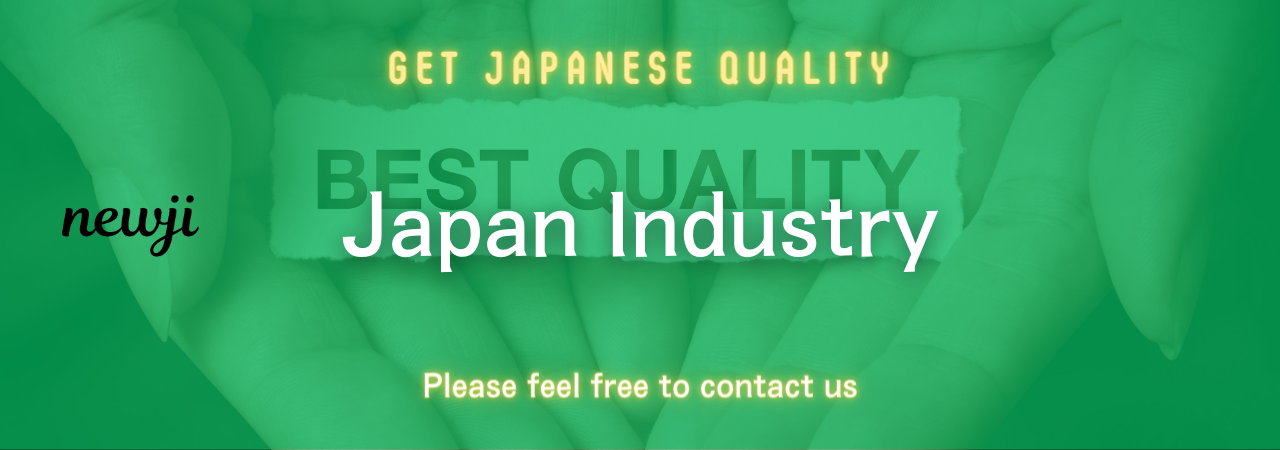
Understanding the reasons behind purchasing errors is crucial for any business.
In today’s competitive market, improving procurement processes not only controls product quality but also ensures timely delivery.
Let’s dive into the causes and prevention strategies that can help you reduce purchasing mistakes.
目次
Common Causes of Purchasing Errors
1. Inaccurate Requirements
One of the most prevalent issues in the procurement process is inaccurate requirements.
When the information provided for a purchase is incomplete or incorrect, it leads to buying the wrong products or services.
This can result in wasted time and resources.
2. Lack of Supplier Communication
Effective communication with suppliers is crucial for a smooth procurement process.
Misunderstandings or lack of clarity between your business and suppliers can lead to errors in the products or services delivered.
This can also affect delivery times and product quality.
3. Poor Inventory Management
Another common cause of purchasing errors is poor inventory management.
Without a clear understanding of what is already available and what is needed, businesses might over-purchase or under-purchase, leading to inefficiencies and increased costs.
4. Inadequate Vendor Assessment
Choosing the wrong vendor can have significant repercussions.
Failure to assess vendors properly can lead to substandard products, delayed deliveries, and other purchasing errors.
It’s essential to vet your vendors thoroughly.
5. Human Errors
Human mistakes are inevitable but can be minimized.
Errors such as data entry mistakes, misinterpretation of information, or simply overlooking details can lead to purchasing issues.
Implementing processes to catch these errors can help.
Strategies for Preventing Purchasing Errors
1. Clear and Accurate Requirements
The first step to preventing purchasing errors is ensuring that the procurement requirements are clear and accurate.
Use detailed specifications and double-check for any inaccuracies.
Involve all relevant stakeholders to ensure that the requirements meet the actual needs.
2. Enhance Supplier Communication
Improve your communication with suppliers by establishing clear and open lines of communication.
Regular meetings and updates can help ensure that both parties are on the same page.
Using collaborative tools can also bridge communication gaps.
3. Implement Robust Inventory Management Systems
Investing in robust inventory management systems can greatly reduce purchasing errors.
These systems can track inventory levels, generate accurate reports, and forecast future needs, ensuring that you buy exactly what is required.
4. Conduct Thorough Vendor Assessments
Ensure you’ll get the best vendors on board by conducting thorough assessments.
Evaluate vendors based on quality, reliability, delivery times, and overall performance.
Regular reviews and feedback loops can help maintain high standards.
5. Minimize Human Errors
Human errors can be minimized through training and automation.
Provide regular training sessions for your procurement team to ensure they are well-versed in best practices.
Utilize automation tools to reduce manual data entry and other repetitive tasks.
Improving Procurement Processes
1. Utilize Technology
Leveraging technology can significantly streamline your procurement processes.
Procurement software can automate many tasks, reducing the chances of errors and improving efficiency.
These tools can help with everything from sourcing suppliers to managing contracts.
2. Standardize Procedures
Standardizing procurement procedures ensures consistency and reduces errors.
Create clear guidelines and procedures for every step of the procurement process.
This makes it easier for employees to follow best practices and reduces variability.
3. Implement Performance Metrics
Introduce performance metrics to measure the effectiveness of your procurement process.
Metrics such as delivery times, cost savings, and error rates can provide valuable insights.
Use these metrics to identify areas for improvement and track progress over time.
4. Foster Collaboration
Encourage collaboration between different departments involved in procurement.
Inter-departmental collaboration can lead to better decision-making and more accurate requirements.
Regular meetings and collaborative tools can facilitate this.
5. Continuous Improvement
Adopt a culture of continuous improvement within your procurement team.
Regularly review and refine your processes to adapt to changes in the market.
Encourage feedback from employees and stakeholders to identify potential areas for improvement.
Benefits of Reducing Purchasing Errors
1. Cost Savings
Reducing purchasing errors can lead to significant cost savings.
Accurate purchases mean less waste and fewer returns, ultimately saving money.
Efficient procurement processes can also reduce operational costs.
2. Improved Product Quality
By eliminating errors, the quality of products and services purchased will likely improve.
This leads to higher customer satisfaction and fewer issues to address later.
3. Timely Deliveries
Effective procurement reduces delays and ensures timely deliveries.
This helps to maintain smooth operations and meet customer expectations.
4. Enhanced Supplier Relationships
Reducing purchasing errors fosters better relationships with suppliers.
Suppliers appreciate clear communication and accurate orders, strengthening your partnership.
5. Operational Efficiency
A streamlined procurement process leads to greater operational efficiency.
Teams can focus on strategic activities rather than firefighting issues.
Understanding the causes and implementing prevention strategies is crucial for improving procurement processes.
By addressing the common causes of purchasing errors, businesses can ensure higher product quality, timely deliveries, and cost savings.
Investing in technology, standardizing procedures, and fostering collaboration are key steps toward a more efficient procurement system.
By continuously refining and improving these processes, businesses can maintain a competitive edge in the market.
資料ダウンロード
QCD調達購買管理クラウド「newji」は、調達購買部門で必要なQCD管理全てを備えた、現場特化型兼クラウド型の今世紀最高の購買管理システムとなります。
ユーザー登録
調達購買業務の効率化だけでなく、システムを導入することで、コスト削減や製品・資材のステータス可視化のほか、属人化していた購買情報の共有化による内部不正防止や統制にも役立ちます。
NEWJI DX
製造業に特化したデジタルトランスフォーメーション(DX)の実現を目指す請負開発型のコンサルティングサービスです。AI、iPaaS、および先端の技術を駆使して、製造プロセスの効率化、業務効率化、チームワーク強化、コスト削減、品質向上を実現します。このサービスは、製造業の課題を深く理解し、それに対する最適なデジタルソリューションを提供することで、企業が持続的な成長とイノベーションを達成できるようサポートします。
オンライン講座
製造業、主に購買・調達部門にお勤めの方々に向けた情報を配信しております。
新任の方やベテランの方、管理職を対象とした幅広いコンテンツをご用意しております。
お問い合わせ
コストダウンが利益に直結する術だと理解していても、なかなか前に進めることができない状況。そんな時は、newjiのコストダウン自動化機能で大きく利益貢献しよう!
(Β版非公開)