- お役立ち記事
- Causes of Defects in Precision Injection Molding and How to Prevent Them
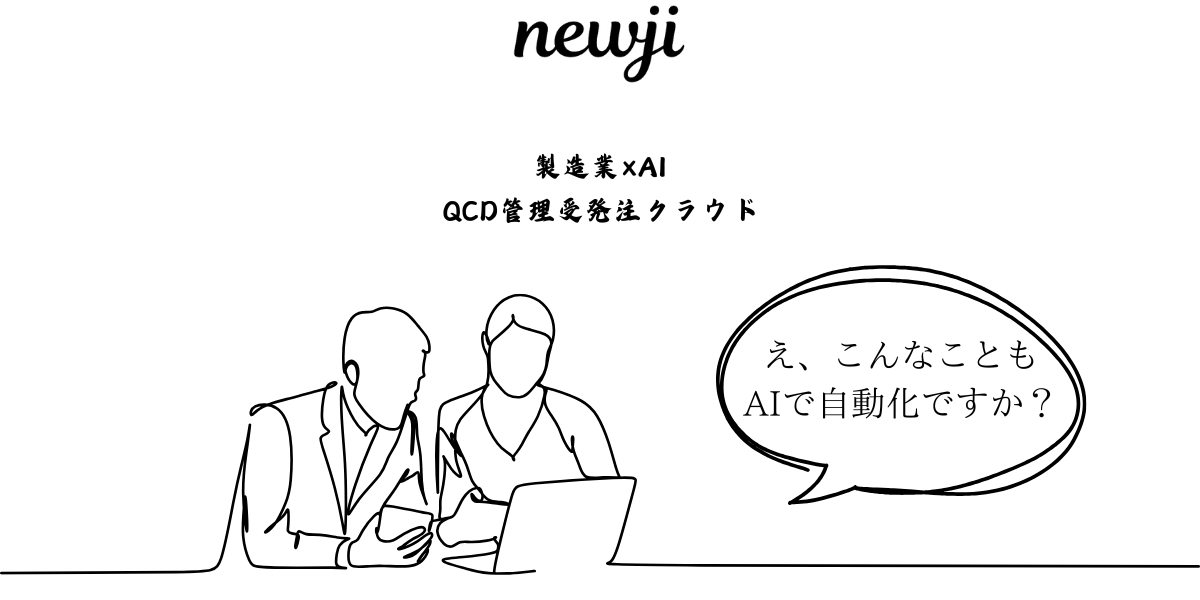
Causes of Defects in Precision Injection Molding and How to Prevent Them
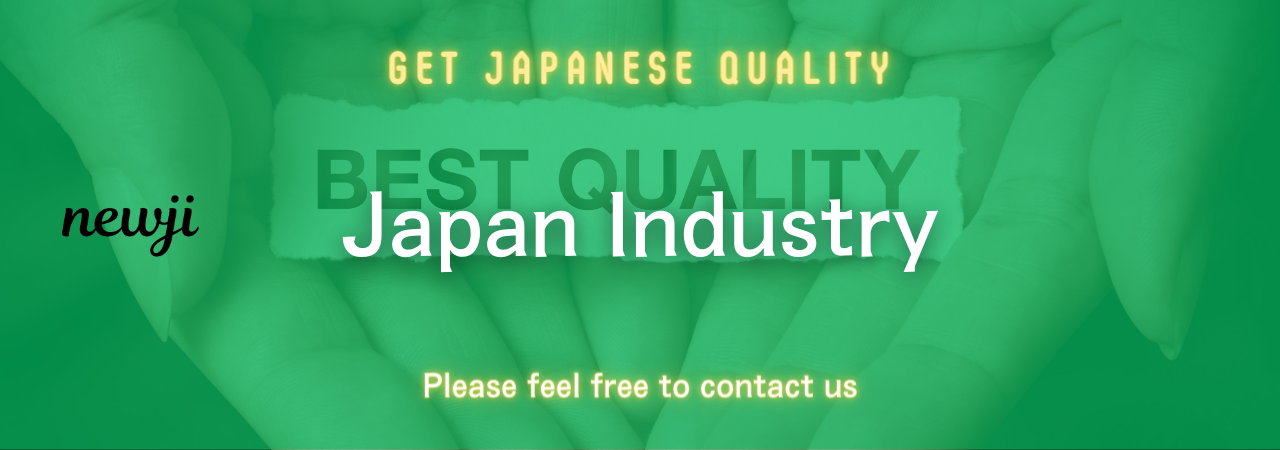
目次
Understanding Precision Injection Molding
Precision injection molding is a manufacturing process used to produce intricate and precise plastic parts.
It involves injecting molten plastic into a mold, where it cools and takes the shape of the cavity.
This process is used across various industries, including automotive, aerospace, medical, and electronics, due to its ability to produce complex parts with high accuracy.
However, achieving such precision requires strict control over several parameters, and any deviation can lead to defects.
Common Defects in Precision Injection Molding
Identifying and understanding common defects is crucial for improving the quality of molded parts.
Some of the most prevalent defects include:
1. Warping
Warping occurs when there is uneven shrinkage within a molded part, leading to distortion and deformation.
This defect typically arises when there is an inconsistency in wall thickness, temperature disparities, or unequal cooling rates.
It can significantly affect the functionality and appearance of the final product.
2. Sink Marks
Sink marks are localized depressions typically found on thicker sections of a molded part.
These defects occur due to uneven cooling or insufficient packing pressure, preventing the plastic from filling out the mold completely.
The presence of sink marks can diminish the aesthetic value and structural integrity of a part.
3. Flash
Flash is the excess material that protrudes from the edges of the molded part, often forming thin burrs.
It usually results from excessive injection pressure, misaligned molds, or damage to the mold.
Flash must be trimmed or removed post-molding, which can increase production time and costs.
4. Short Shots
Short shots occur when the mold cavity is not fully filled with plastic, leading to incomplete parts.
This defect can be caused by inadequate material feed, low injection pressure, or blockages in the mold or runners.
Short shots result in unusable products and wasted material.
5. Burn Marks
Burn marks appear as discolorations, often brown or black, and are caused by overheating or trapped air within the mold.
This defect can compromise the mechanical properties of the part and is usually attributed to high injection speeds or insufficient venting.
Factors Contributing to Defects
Several factors can contribute to defects in precision injection molding.
Understanding these factors can help in preventing such issues:
1. Material Selection
The choice of material plays a significant role in the quality of the final product.
Different materials have varying flow behaviors, shrinkage rates, and thermal properties.
Inadequate material selection can lead to defects such as warping, sink marks, and burn marks.
It’s crucial to choose materials that are compatible with the design and function of the part.
2. Mold Design
An effective mold design ensures uniform flow and cooling throughout the part.
Poor mold design can lead to uneven pressure distribution, inconsistent thickness, and problems with venting.
Factors such as gate location, runner layout, and cooling system play a vital role and need to be carefully planned.
3. Process Parameters
Precise control over process parameters such as temperature, pressure, and cooling time is essential.
Incorrect settings can cause a wide range of defects.
For instance, low injection pressure might lead to short shots, while high temperatures can result in burn marks.
4. Machine Maintenance
Regular maintenance of the injection molding machine ensures optimal performance.
Worn or damaged parts, clogging, or misalignment can affect the molding process and result in defects.
Routine checks are essential to prevent downtimes and maintain consistency in production.
Preventive Measures for Defect Reduction
Implementing preventive measures can significantly reduce the occurrence of defects in precision injection molding:
1. Optimize Design
Design optimization is key to minimizing defects.
Utilizing design for manufacturability (DFM) principles can address potential issues at the design stage.
Tools such as simulation software can predict flow, cooling, and shrinkage, allowing for design modifications before production begins.
2. Material Testing
Conduct rigorous testing of materials to evaluate their suitability.
This includes assessing their mechanical properties, thermal behavior, and shrinkage rates.
Select materials that align well with the design specifications and intended application.
3. Calibration and Monitoring
Regularly calibrate machines to ensure all parameters are set and maintained correctly.
Use monitoring systems to detect any deviations in real-time, allowing for immediate adjustments.
This approach helps in maintaining consistent quality throughout the production run.
4. Improve Venting
Enhancing mold venting is crucial to preventing trapped air, which leads to burn marks and incomplete filling.
Ensure that vents are clean and appropriately sized to allow gases to escape without affecting the product.
5. Train Personnel
Proper training of personnel involved in the injection molding process is essential.
Ensure they have a thorough understanding of the machinery, materials, and potential defects.
Skilled operators can quickly identify problems and perform necessary adjustments to maintain quality.
Conclusion
Precision injection molding is a complex process with a high demand for accuracy and quality.
Understanding the causes of defects and implementing preventive measures can significantly improve the outcome of molded parts.
By focusing on material selection, mold design, process optimization, and regular maintenance, manufacturers can minimize defects and enhance the production efficiency of precision injection molding.
資料ダウンロード
QCD調達購買管理クラウド「newji」は、調達購買部門で必要なQCD管理全てを備えた、現場特化型兼クラウド型の今世紀最高の購買管理システムとなります。
ユーザー登録
調達購買業務の効率化だけでなく、システムを導入することで、コスト削減や製品・資材のステータス可視化のほか、属人化していた購買情報の共有化による内部不正防止や統制にも役立ちます。
NEWJI DX
製造業に特化したデジタルトランスフォーメーション(DX)の実現を目指す請負開発型のコンサルティングサービスです。AI、iPaaS、および先端の技術を駆使して、製造プロセスの効率化、業務効率化、チームワーク強化、コスト削減、品質向上を実現します。このサービスは、製造業の課題を深く理解し、それに対する最適なデジタルソリューションを提供することで、企業が持続的な成長とイノベーションを達成できるようサポートします。
オンライン講座
製造業、主に購買・調達部門にお勤めの方々に向けた情報を配信しております。
新任の方やベテランの方、管理職を対象とした幅広いコンテンツをご用意しております。
お問い合わせ
コストダウンが利益に直結する術だと理解していても、なかなか前に進めることができない状況。そんな時は、newjiのコストダウン自動化機能で大きく利益貢献しよう!
(Β版非公開)