- お役立ち記事
- Causes of Weld Lines and Their Solutions in Manufacturing
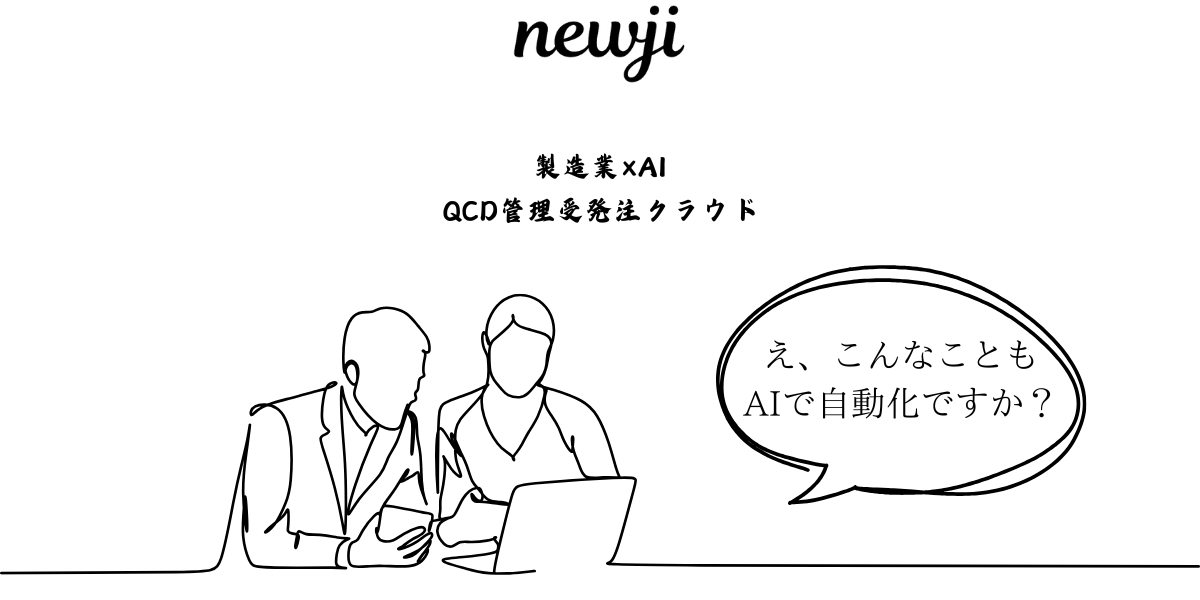
Causes of Weld Lines and Their Solutions in Manufacturing
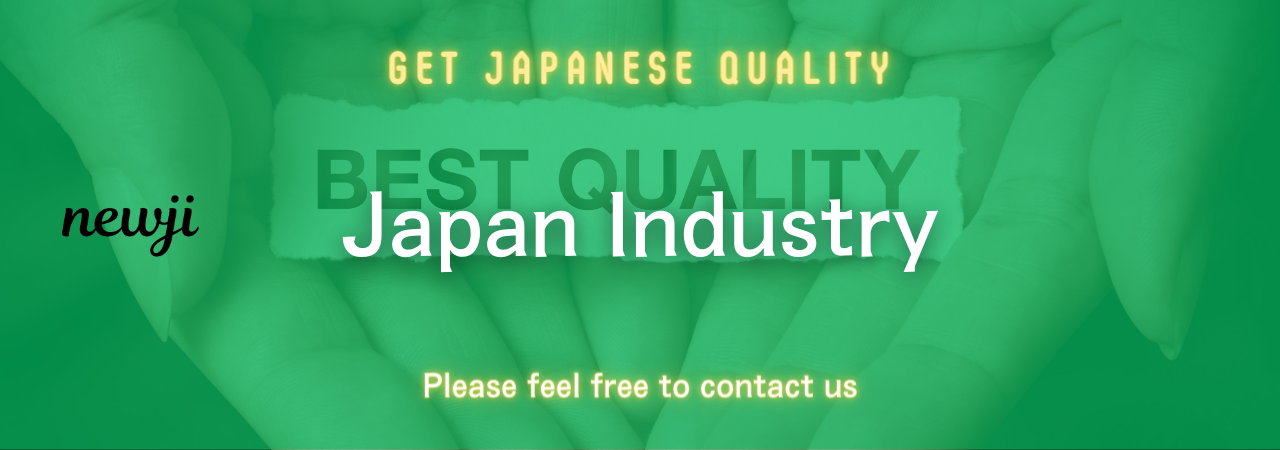
Weld lines, also known as knit lines or meld lines, are a common issue in the manufacturing world.
They can hinder the aesthetic appeal and structural integrity of products.
Understanding the causes and solutions of weld lines can help manufacturers improve product quality.
We’ll explore the primary reasons for weld lines and how to address them effectively.
目次
What Are Weld Lines?
Weld lines occur when two or more flows of molten material converge but do not bond perfectly.
This issue is especially prevalent in injection molding, where different material streams meet while forming a product.
The result is a visible line or defect on the surface, often weaker than the surrounding material.
Common Causes of Weld Lines
Several factors contribute to the formation of weld lines.
Understanding these causes can lead to more effective solutions.
Low Melt Temperature
One of the main causes of weld lines is a low melt temperature.
When the material isn’t hot enough, it doesn’t flow well, leading to poor bonding at the convergence point.
This insufficient bonding results in visible weld lines.
Inadequate Injection Pressure
Insufficient injection pressure can also contribute to weld lines.
When the pressure is too low, the material flow is weak and doesn’t combine properly at the meeting point.
This irregular flow forms visible and structurally weak weld lines.
Improper Gate Location
The location of the gate (the entry point for molten material) plays a critical role.
If the gates are not appropriately positioned, the material flows might meet at angles that do not promote optimal bonding.
Incorrect gate positioning leads to weld lines forming at these junctions.
Material Viscosity
Material viscosity affects how well the molten material flows and merges.
High-viscosity materials, which are thicker, don’t flow as easily.
This difficulty in flowing impacts the ability of the material to blend seamlessly.
Hence, weld lines are more likely to form.
Mold Design
The design of the mold also influences the likelihood of weld lines.
Complex geometries or sharp angles in the mold can disrupt the even flow of molten material.
This disruption causes uneven bonding at the convergence points, forming weld lines.
Solutions to Weld Lines
Fortunately, various methods can help address and minimize the occurrence of weld lines.
These solutions target the root causes and improve the overall quality of manufactured products.
Optimize Melt Temperature
Increasing the melt temperature can enhance the flow characteristics of the material.
When the material flows more smoothly, it bonds better at the convergence points, reducing the formation of weld lines.
Monitoring and adjusting the temperature settings during the injection process is crucial.
Adjust Injection Pressure
Increasing the injection pressure ensures that the molten material flows adequately.
It also helps the material merge more effectively at the meeting points.
By optimizing the injection pressure, manufacturers can significantly reduce or eliminate weld lines.
Reposition Gates
Reevaluating and repositioning gates can ensure a more uniform material flow.
Strategically placing gates can help achieve better bonding.
When the material flows meet at more favorable angles, the likelihood of weld lines decreases.
Use Low-Viscosity Materials
Opting for materials with lower viscosity can improve flow characteristics and merging capabilities.
Lower-viscosity materials flow more easily and blend better at convergence points.
This adjustment can be an effective solution to reducing weld lines.
Improve Mold Design
Simplifying the mold design or smoothing out sharp angles can promote better material flow.
A well-designed mold ensures a more even flow of molten material, reducing disruptions at convergence points.
Thus, improving mold design can help in minimizing weld lines.
Additional Techniques
Besides addressing the primary causes, manufacturers can also use specific techniques to mitigate weld lines.
Mold Venting
Proper mold venting allows trapped gases to escape, reducing the chances of weld lines.
Effective venting ensures smoother material flow and better bonding at the convergence points.
Regularly checking and maintaining mold vents can improve product quality.
Using Weld Line Agents
Some materials and chemical agents can facilitate better bonding at the convergence points.
Using these agents can strengthen the areas where the material flows meet.
This method can be particularly useful for complex molds or high-viscosity materials.
Post-Processing Techniques
In some cases, post-processing methods such as surface finishing or coating can mask weld lines.
Although this does not solve the underlying issue, it can improve the appearance and functionality of the product.
Conclusion
Understanding the causes and solutions for weld lines is essential for manufacturers aiming to improve product quality.
By optimizing melt temperatures, adjusting injection pressures, repositioning gates, using lower viscosity materials, and enhancing mold designs, manufacturers can effectively reduce weld lines.
Additional techniques like mold venting, using weld line agents, and post-processing can further mitigate this issue.
Proactively addressing these factors ensures the production of aesthetically appealing and structurally sound products.
資料ダウンロード
QCD調達購買管理クラウド「newji」は、調達購買部門で必要なQCD管理全てを備えた、現場特化型兼クラウド型の今世紀最高の購買管理システムとなります。
ユーザー登録
調達購買業務の効率化だけでなく、システムを導入することで、コスト削減や製品・資材のステータス可視化のほか、属人化していた購買情報の共有化による内部不正防止や統制にも役立ちます。
NEWJI DX
製造業に特化したデジタルトランスフォーメーション(DX)の実現を目指す請負開発型のコンサルティングサービスです。AI、iPaaS、および先端の技術を駆使して、製造プロセスの効率化、業務効率化、チームワーク強化、コスト削減、品質向上を実現します。このサービスは、製造業の課題を深く理解し、それに対する最適なデジタルソリューションを提供することで、企業が持続的な成長とイノベーションを達成できるようサポートします。
オンライン講座
製造業、主に購買・調達部門にお勤めの方々に向けた情報を配信しております。
新任の方やベテランの方、管理職を対象とした幅広いコンテンツをご用意しております。
お問い合わせ
コストダウンが利益に直結する術だと理解していても、なかなか前に進めることができない状況。そんな時は、newjiのコストダウン自動化機能で大きく利益貢献しよう!
(Β版非公開)