- お役立ち記事
- Challenges and Solutions for SMEs in Bending Process Efficiency
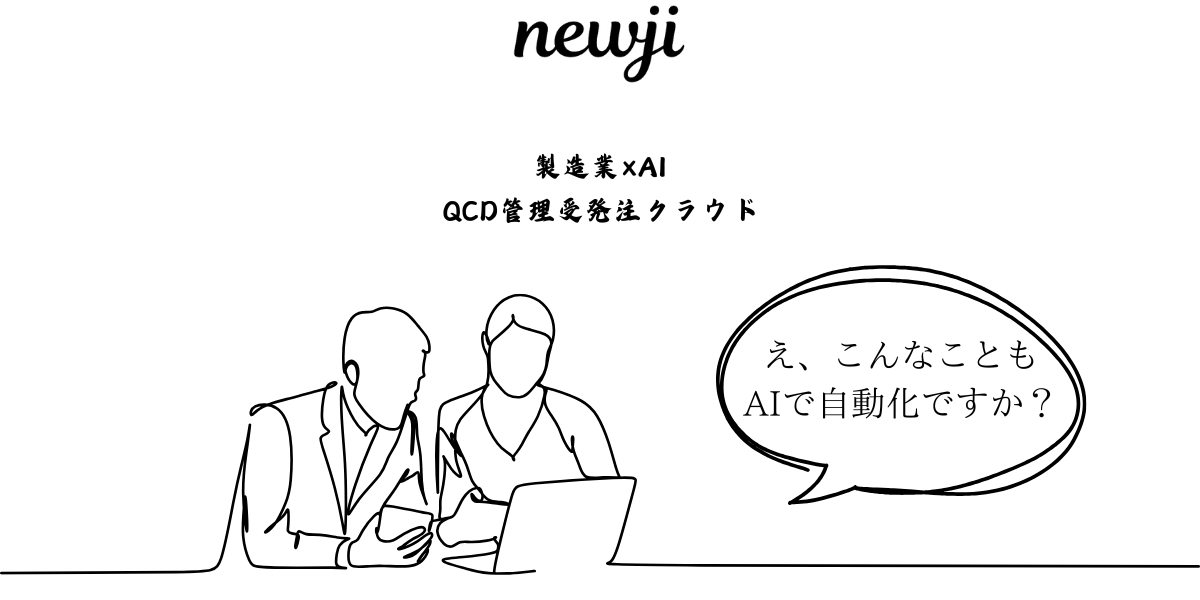
Challenges and Solutions for SMEs in Bending Process Efficiency
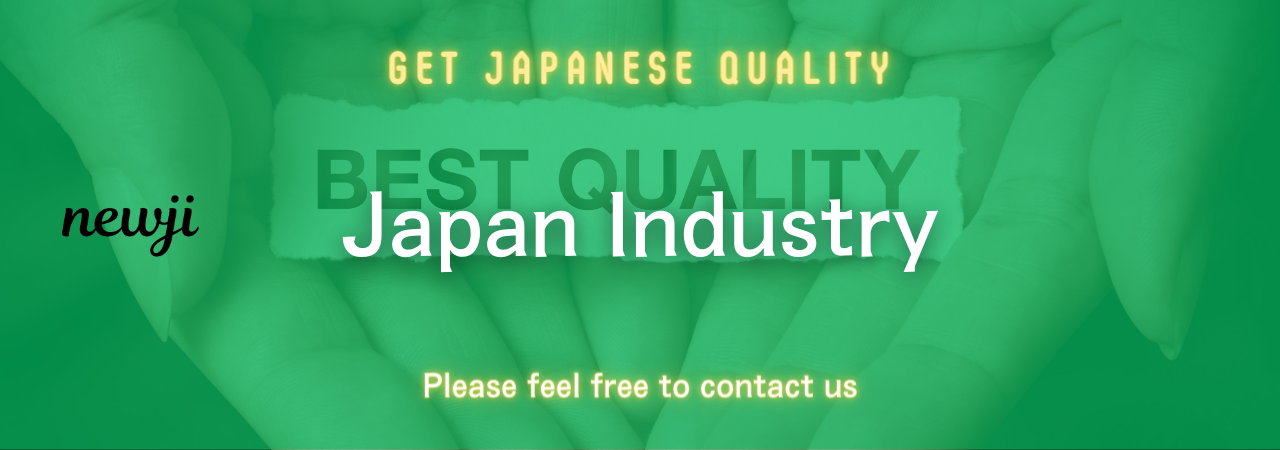
The bending process is a critical operation for many small and medium-sized enterprises (SMEs) involved in manufacturing and metalworking.
It can present various challenges that, if not addressed, can significantly impact productivity and profitability.
Fortunately, several solutions can help SMEs improve bending process efficiency.
目次
Understanding the Importance of Bending Process Efficiency
The bending process involves molding metal sheets into desired shapes using tools such as press brakes and bending machines.
Efficient bending is crucial because it affects the quality of the final product, the speed of production, and overall costs.
When SMEs optimize this process, they can reduce waste, improve turnaround times, and ensure consistent product quality.
Common Challenges in the Bending Process for SMEs
Several obstacles frequently hamper the efficiency of the bending process for SMEs.
High Setup Times
One of the primary challenges is the high setup time required to prepare the machinery for different bending operations.
SMEs often handle smaller production runs, meaning they need to change setups more frequently.
Each setup change can be time-consuming, leading to delays and increased labor costs.
Lack of Skilled Labor
Another significant challenge is the shortage of skilled labor.
Bending processes often require experienced operators who understand the nuances of different materials and machine settings.
A lack of skilled workers can result in subpar products and an inefficient use of resources.
Material Waste
Material waste is a considerable concern for SMEs.
Overbending, underbending, and inaccuracies in measuring can lead to wasted materials.
This not only increases costs but also reflects poorly on the company’s efficiency and commitment to sustainability.
Inconsistent Quality
Consistency is key in manufacturing.
Inconsistent bending quality can result in products that do not meet specifications, leading to rework or scrap.
This inconsistency can stem from variations in material properties, improper machine calibration, or operator errors.
Effective Solutions to Improve Bending Process Efficiency
Addressing these challenges requires a combination of technology, training, and process adjustments.
Invest in Modern Machinery
One of the most effective ways to improve bending efficiency is by investing in modern machinery.
Advanced bending machines with automated features can significantly reduce setup times.
Computer Numerical Control (CNC) machines, for example, can store multiple programs, allowing for quick transitions between different bending operations.
Implement Training Programs
Ensuring that operators are well-trained is essential for maximizing efficiency.
SMEs should invest in regular training programs to keep workers up-to-date with the latest techniques and technologies.
Training can minimize errors, improve product quality, and make better use of available resources.
Utilize Simulation Software
Simulation software can be a game-changer for SMEs.
These tools allow companies to virtually model bending processes before actual production.
This helps in identifying potential issues and optimizing parameters to reduce material waste and improve accuracy.
Adopt Lean Manufacturing Principles
Lean manufacturing principles focus on reducing waste and improving processes.
By adopting lean practices, SMEs can streamline their production workflows, reduce unnecessary steps, and improve overall efficiency.
Techniques like Value Stream Mapping (VSM) can help identify areas where improvements can be made.
Standardize Processes
Standardizing processes can significantly reduce variability in production quality.
Creating detailed standard operating procedures (SOPs) for different bending operations can help ensure that all operators follow best practices.
This consistency leads to fewer errors and more predictable outcomes.
Monitor and Analyze Performance
Ongoing monitoring and analysis of the bending process can provide valuable insights into areas needing improvement.
SMEs should regularly collect data on machine performance, product quality, and cycle times.
Using this data, companies can make informed decisions about where to make adjustments.
Future Trends in Bending Process Efficiency
As technology continues to evolve, SMEs can expect new opportunities to enhance their bending processes.
Industry 4.0 and Smart Manufacturing
The rise of Industry 4.0 and smart manufacturing presents exciting possibilities.
Integrating IoT (Internet of Things) devices with bending machinery can enable real-time monitoring and predictive maintenance.
These technologies can help prevent downtime and ensure machines are always operating optimally.
Advanced Materials
Developments in materials science can also contribute to improved bending efficiency.
New materials with better properties, such as higher strength-to-weight ratios, can reduce the difficulty and time required for bending operations.
Collaborative Robots
Collaborative robots, or cobots, can work alongside human operators to enhance productivity.
These robots can handle repetitive tasks, allowing skilled workers to focus on more complex aspects of the bending process.
Conclusion
Improving bending process efficiency requires SMEs to tackle several challenges head-on.
High setup times, a lack of skilled labor, material waste, and inconsistent quality are all significant concerns.
However, by investing in modern machinery, implementing training programs, utilizing simulation software, adopting lean manufacturing principles, standardizing processes, and monitoring performance, SMEs can overcome these hurdles.
Embracing future trends like Industry 4.0, advanced materials, and collaborative robots will further ensure that SMEs remain competitive in the ever-evolving manufacturing landscape.
Efficient bending processes ultimately lead to better products, reduced costs, and a stronger bottom line.
資料ダウンロード
QCD調達購買管理クラウド「newji」は、調達購買部門で必要なQCD管理全てを備えた、現場特化型兼クラウド型の今世紀最高の購買管理システムとなります。
ユーザー登録
調達購買業務の効率化だけでなく、システムを導入することで、コスト削減や製品・資材のステータス可視化のほか、属人化していた購買情報の共有化による内部不正防止や統制にも役立ちます。
NEWJI DX
製造業に特化したデジタルトランスフォーメーション(DX)の実現を目指す請負開発型のコンサルティングサービスです。AI、iPaaS、および先端の技術を駆使して、製造プロセスの効率化、業務効率化、チームワーク強化、コスト削減、品質向上を実現します。このサービスは、製造業の課題を深く理解し、それに対する最適なデジタルソリューションを提供することで、企業が持続的な成長とイノベーションを達成できるようサポートします。
オンライン講座
製造業、主に購買・調達部門にお勤めの方々に向けた情報を配信しております。
新任の方やベテランの方、管理職を対象とした幅広いコンテンツをご用意しております。
お問い合わせ
コストダウンが利益に直結する術だと理解していても、なかなか前に進めることができない状況。そんな時は、newjiのコストダウン自動化機能で大きく利益貢献しよう!
(Β版非公開)