- お役立ち記事
- Coating Wire Technology and Its Applications in Manufacturing
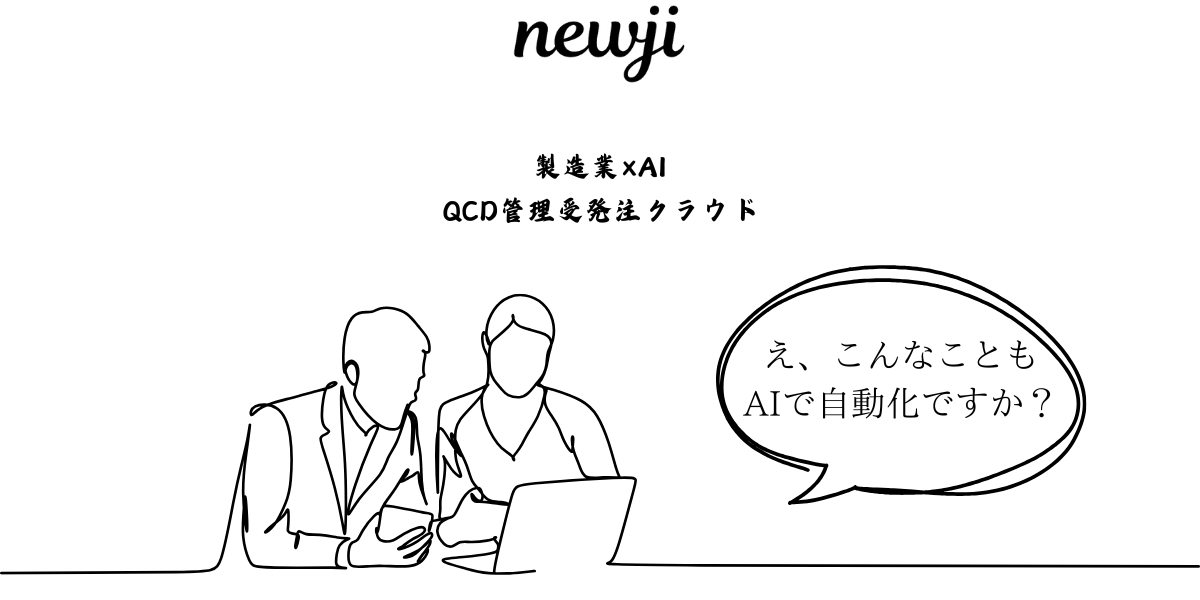
Coating Wire Technology and Its Applications in Manufacturing
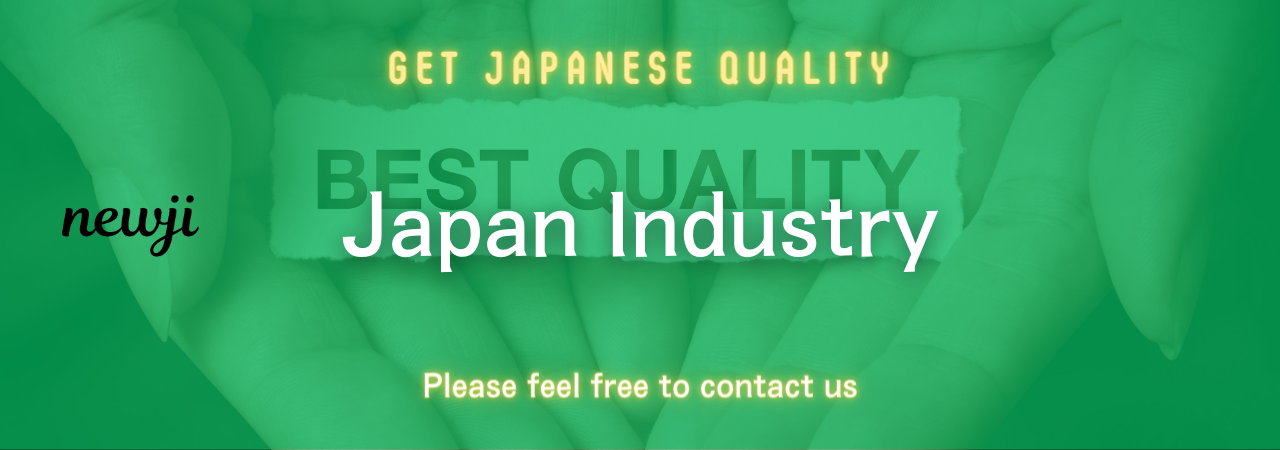
目次
Introduction to Coating Wire Technology
Coating wire technology is essential in modern manufacturing processes. By applying a protective layer to metal wires, manufacturers can improve the wire’s performance and durability. This technology is crucial in various industries, from electronics to automotive.
What Is Coating Wire Technology?
Coating wire technology involves applying a thin layer of a protective material to the surface of a metal wire. The coating can be made from different materials, such as plastic, rubber, or metal alloys. This process enhances the wire’s properties, making it more resistant to corrosion, abrasion, and temperature changes.
Types of Coatings
There are several types of coatings used in wire technology. Each type serves specific purposes and has unique properties. Some common coatings include:
1. **Plastic Coating**: This type of coating is frequently used for electrical wires. It provides insulation and protects the wire from environmental factors.
2. **Rubber Coating**: Rubber coatings are flexible and durable, making them ideal for applications requiring wire movement and bending.
3. **Metal Alloy Coating**: Metal alloys are used to add strength and resistance to wear and tear. Common metal alloys used include copper, silver, and nickel.
4. **Ceramic Coating**: These coatings provide excellent heat resistance and are often used in high-temperature applications.
Benefits of Wire Coatings
Applying coatings to wires offers numerous benefits:
– **Corrosion Resistance**: Coatings protect the wire from rust and corrosion, extending its lifespan.
– **Electrical Insulation**: Insulating coatings prevent electrical shorts and improve safety in electrical applications.
– **Heat Resistance**: Certain coatings can withstand high temperatures, making them suitable for use in extreme environments.
– **Durability**: Coated wires are more resistant to wear and tear, reducing the need for frequent replacements.
Applications of Coating Wire Technology
Coating wire technology plays a vital role in various industries. Here are some of its key applications:
Electronics
In the electronics industry, coated wires are essential for creating reliable and safe electrical connections. Insulated wires are used in devices like computers, smartphones, and household appliances to prevent electrical hazards and ensure proper functioning.
Automotive Industry
The automotive industry relies heavily on coated wires for various applications. These include battery cables, engine wiring, and sensor wires. Coated wires in vehicles provide resistance to high temperatures, chemicals, and mechanical stress, ensuring the longevity and reliability of automotive components.
Aerospace
In the aerospace sector, coated wires are used in the construction of airplanes and spacecraft. Coatings provide essential protection against extreme temperatures, vibration, and corrosion, critical factors in ensuring the safety and performance of aerospace vehicles.
Construction
In construction, coated wires are used in building infrastructures, such as bridges and buildings. These wires are designed to withstand environmental challenges like moisture, ultraviolet radiation, and temperature fluctuations.
Medical Devices
The medical field also benefits from coating wire technology. Medical devices like catheters, surgical instruments, and diagnostic equipment use coated wires to ensure biocompatibility, flexibility, and durability.
Future Trends in Coating Wire Technology
As technology advances, the demand for more efficient and durable coated wires continues to grow. Some emerging trends in this field include:
Nanotechnology
Nanotechnology is becoming increasingly important in coating wire technology. Nanocoatings can provide enhanced properties, such as increased electrical conductivity and improved resistance to environmental factors. These advanced coatings can revolutionize wire performance in various applications.
Eco-Friendly Coatings
There is a growing emphasis on developing environmentally friendly coatings. Researchers are working on biodegradable and non-toxic coatings to reduce the environmental impact of wire manufacturing processes.
Smart Coatings
Smart coatings are a promising area of research. These coatings can change their properties in response to external stimuli, such as temperature or pressure. For instance, smart coatings could be used to create wires that automatically repair themselves when damaged.
Conclusion
Coating wire technology is a vital element in modern manufacturing, offering enhanced performance and durability across numerous industries.
From electronics to aerospace, the applications of coated wires are vast and continually expanding.
As research and innovation continue, we can expect to see even more advanced and eco-friendly coatings in the future, further pushing the boundaries of what coated wires can achieve.
With these technological advancements, manufacturers can create more efficient, reliable, and sustainable products, benefiting industries worldwide.
資料ダウンロード
QCD調達購買管理クラウド「newji」は、調達購買部門で必要なQCD管理全てを備えた、現場特化型兼クラウド型の今世紀最高の購買管理システムとなります。
ユーザー登録
調達購買業務の効率化だけでなく、システムを導入することで、コスト削減や製品・資材のステータス可視化のほか、属人化していた購買情報の共有化による内部不正防止や統制にも役立ちます。
NEWJI DX
製造業に特化したデジタルトランスフォーメーション(DX)の実現を目指す請負開発型のコンサルティングサービスです。AI、iPaaS、および先端の技術を駆使して、製造プロセスの効率化、業務効率化、チームワーク強化、コスト削減、品質向上を実現します。このサービスは、製造業の課題を深く理解し、それに対する最適なデジタルソリューションを提供することで、企業が持続的な成長とイノベーションを達成できるようサポートします。
オンライン講座
製造業、主に購買・調達部門にお勤めの方々に向けた情報を配信しております。
新任の方やベテランの方、管理職を対象とした幅広いコンテンツをご用意しております。
お問い合わせ
コストダウンが利益に直結する術だと理解していても、なかなか前に進めることができない状況。そんな時は、newjiのコストダウン自動化機能で大きく利益貢献しよう!
(Β版非公開)