- お役立ち記事
- Common points between the Toyota Production System and LEAN production that automation technology departments should know
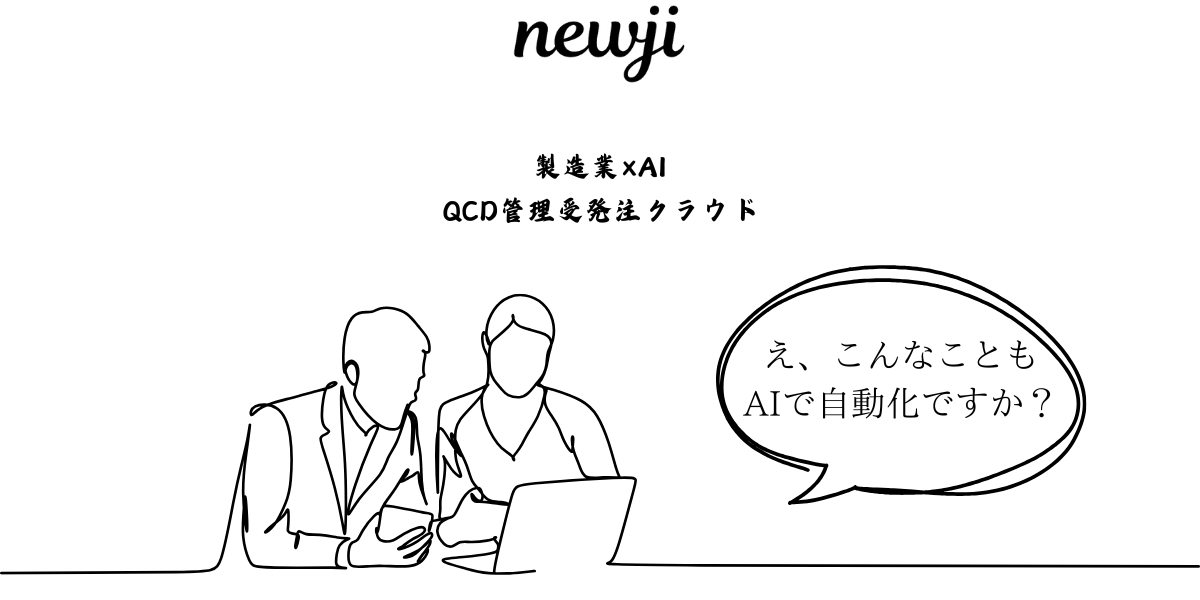
Common points between the Toyota Production System and LEAN production that automation technology departments should know
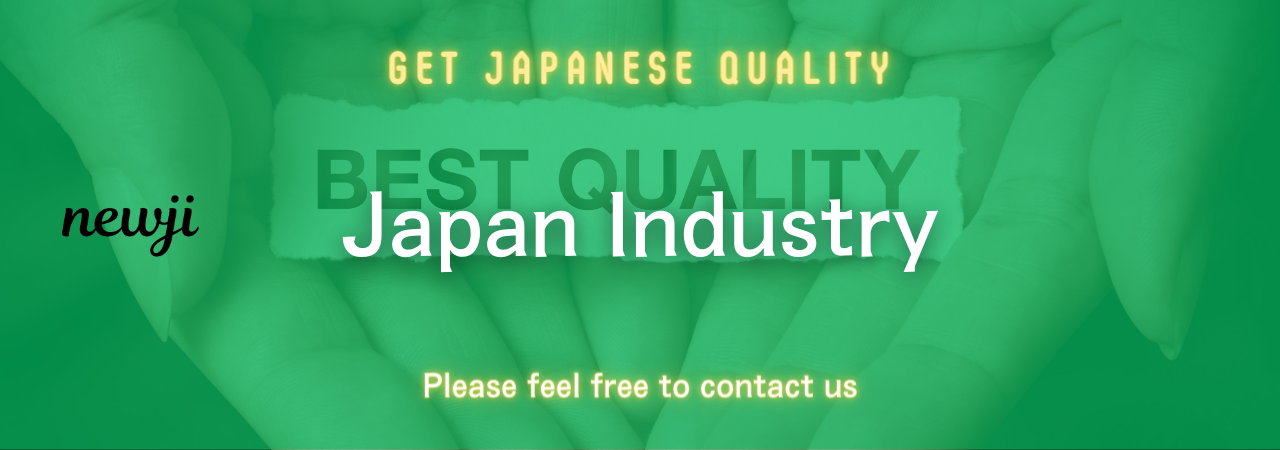
目次
Understanding the Basics of the Toyota Production System
The Toyota Production System (TPS) is a manufacturing approach developed by Toyota, designed to improve efficiency and eliminate waste.
It focuses on creating a smooth production flow by integrating various practices that ensure resources are used optimally.
At the heart of TPS are two main concepts: Just-In-Time (JIT) and Jidoka.
JIT ensures that each process produces only what is needed, when it is needed, thus minimizing excess inventory.
Jidoka, on the other hand, involves the automation of quality checks within the production line, empowering machines and workers to stop work when a problem is detected.
This prevents defects from passing on to the next stage of production.
The Pillars of TPS
TPS is built on principles like continuous improvement, respect for people, and standardization.
Continuous improvement, or Kaizen, encourages the regular evaluation and improvement of processes.
Workers are trained to identify inefficiencies and contribute ideas for enhancing operations.
Respect for people emphasizes the role of employees in the production process, treating them as valuable assets to the organization.
Standardization ensures consistency, enabling easier identification of deviations and facilitating improvements.
Exploring LEAN Production
LEAN production is an approach to manufacturing that seeks to enhance value by reducing waste and improving processes.
Originating from TPS, LEAN borrows many principles from its predecessor, focusing on maximizing productivity with minimal resources.
LEAN production identifies eight types of waste: defects, overproduction, waiting, non-utilized talent, transportation, inventory, motion, and extra processing.
By targeting these, LEAN aims to create more value for the customer while using fewer resources.
Key LEAN Principles
LEAN production is grounded in principles that promote efficiency and customer satisfaction.
One such principle is value stream mapping, which involves analyzing the steps involved in production to identify areas for improvement.
Another principle is creating flow, which ensures that work moves smoothly through various stages, reducing delays and bottlenecks.
Pull systems are also integral to LEAN, focusing on producing only what is needed based on customer demand, preventing overproduction.
Commonalities Between TPS and LEAN Production
Both TPS and LEAN production share a commitment to eliminating waste and improving efficiency.
They aim to streamline operations and focus on delivering maximum value to the customer.
The emphasis on continuous improvement is a key similarity, as both systems encourage regularly revisiting and refining processes.
The focus on creating a smooth flow of production is also a shared goal, ensuring that resources move seamlessly through various stages without unnecessary hold-ups.
Technology’s Role in Modern Production Systems
With the evolution of technology, automation plays a crucial role in both TPS and LEAN production.
Automation makes it possible to implement Jidoka principles more effectively, as machines can now identify and address defects autonomously.
Automation also supports Just-In-Time production by enabling precise control over manufacturing schedules and inventory levels.
In LEAN, technology helps in the efficient mapping and analyzing of value streams, allowing for quicker adaptations to changing market demands.
Why Automation Technology Departments Should Care
Understanding the principles of TPS and LEAN production is crucial for automation technology departments aiming to enhance manufacturing efficiency.
Automation technology can directly align with these methodologies to optimize production processes.
By implementing automated systems that adhere to JIT and Jidoka principles, companies can increase productivity and reduce costs.
Furthermore, technology departments can support continuous improvement by developing solutions that monitor and analyze performance data, identifying areas for enhancement.
Strategies for Implementation
For automation technology departments looking to integrate TPS and LEAN principles, a strategic approach is necessary.
Begin by conducting a thorough analysis of current production processes to identify inefficiencies.
Automation solutions should be designed with flexibility in mind, allowing for future modifications as the production environment evolves.
Collaboration between technology experts and production teams is essential, ensuring that automated solutions align with lean principles and support ongoing improvement efforts.
Conclusion
The commonalities between the Toyota Production System and LEAN production provide a blueprint for maximizing manufacturing efficiency.
By marrying these philosophies with modern automation technologies, companies can significantly enhance their operations.
For automation technology departments, this involves understanding and implementing strategies that support waste elimination, continuous improvement, and value creation.
As automation continues to evolve, its integration with TPS and LEAN principles will be pivotal in shaping the future of manufacturing.
資料ダウンロード
QCD調達購買管理クラウド「newji」は、調達購買部門で必要なQCD管理全てを備えた、現場特化型兼クラウド型の今世紀最高の購買管理システムとなります。
ユーザー登録
調達購買業務の効率化だけでなく、システムを導入することで、コスト削減や製品・資材のステータス可視化のほか、属人化していた購買情報の共有化による内部不正防止や統制にも役立ちます。
NEWJI DX
製造業に特化したデジタルトランスフォーメーション(DX)の実現を目指す請負開発型のコンサルティングサービスです。AI、iPaaS、および先端の技術を駆使して、製造プロセスの効率化、業務効率化、チームワーク強化、コスト削減、品質向上を実現します。このサービスは、製造業の課題を深く理解し、それに対する最適なデジタルソリューションを提供することで、企業が持続的な成長とイノベーションを達成できるようサポートします。
オンライン講座
製造業、主に購買・調達部門にお勤めの方々に向けた情報を配信しております。
新任の方やベテランの方、管理職を対象とした幅広いコンテンツをご用意しております。
お問い合わせ
コストダウンが利益に直結する術だと理解していても、なかなか前に進めることができない状況。そんな時は、newjiのコストダウン自動化機能で大きく利益貢献しよう!
(Β版非公開)