- お役立ち記事
- Complete Understanding of Laser Welding and Joining: Fundamentals and Applications
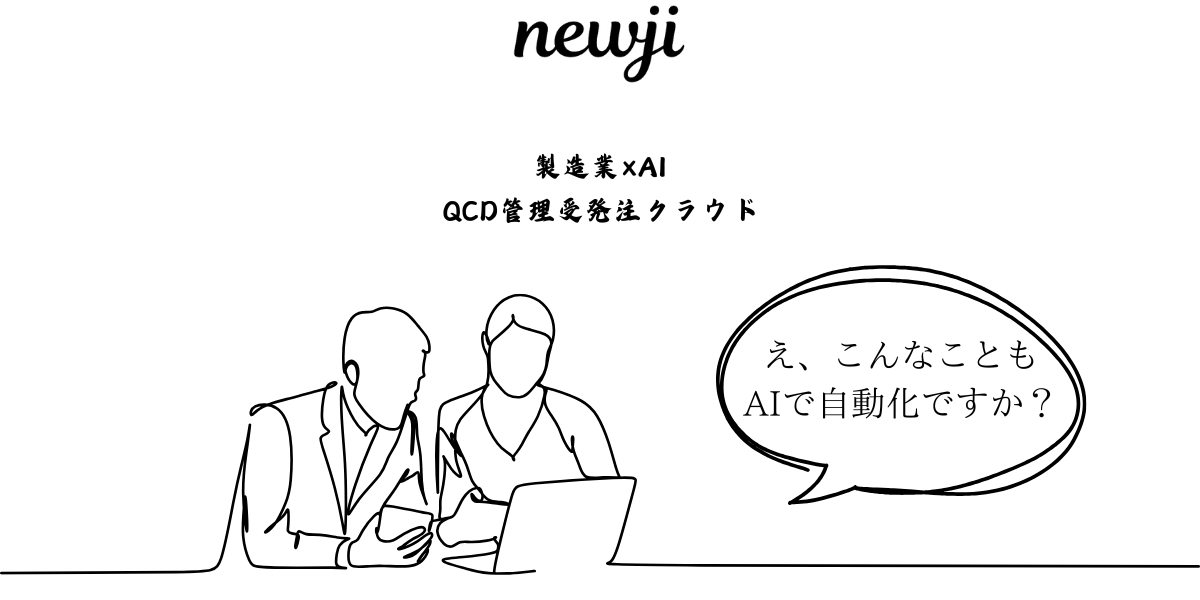
Complete Understanding of Laser Welding and Joining: Fundamentals and Applications
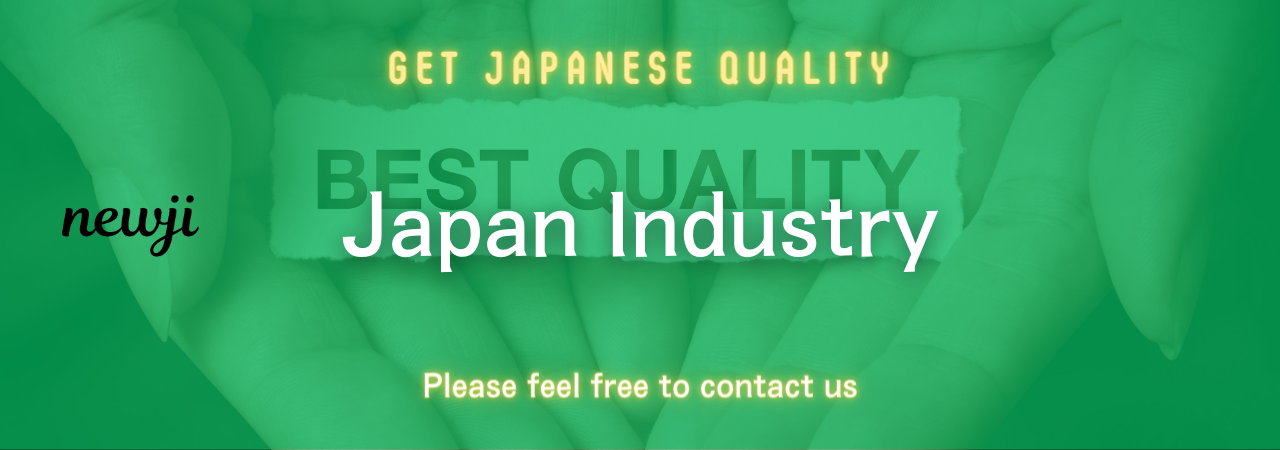
Laser welding and joining have revolutionized the manufacturing industry, providing a versatile and efficient means of combining materials.
These advanced techniques are widely used in sectors ranging from automotive to aerospace, and even electronics.
Understanding the fundamentals and applications of laser welding and joining is critical to appreciating their role in modern manufacturing.
目次
What is Laser Welding?
Laser welding is a technique that uses a focused laser beam to heat and join materials together.
The laser’s intense energy melts the materials at the welding point, creating a strong bond as they cool and solidify.
Basic Principles
The fundamental principle of laser welding lies in using a high-energy laser beam to create a powerful heat source.
This heat is sufficient to melt metals or other materials, allowing them to fuse together seamlessly.
The laser beam is precisely controlled and can be directed to specific points, producing a clean and efficient weld with minimal distortion.
Types of Lasers
There are several types of lasers used in welding, each with its own unique properties and applications.
The most commonly used lasers include:
– **Fiber Lasers**: Known for their high efficiency and excellent beam quality, fiber lasers are suitable for welding thin materials and intricate components.
– **CO2 Lasers**: These lasers are ideal for cutting and welding thicker materials, thanks to their high power output and longer wavelength.
– **Nd:YAG Lasers**: Offering a good balance of power and precision, Nd:YAG lasers are often used in applications requiring fine detail and high-quality welds.
Advantages of Laser Welding
Laser welding offers numerous advantages over traditional welding techniques, making it a preferred choice in many applications.
Precision and Accuracy
One of the most significant benefits of laser welding is its unmatched precision and accuracy.
The focused laser beam allows for highly targeted heat application, resulting in minimal distortion and precise welds.
This level of accuracy is particularly valuable in industries where even minor imperfections can have significant consequences.
Speed and Efficiency
Laser welding is known for its fast processing times, allowing for high-speed production without sacrificing quality.
The quick cooling process further enhances efficiency, enabling continuous operation with minimal downtime.
Versatility
Laser welding can be used with a wide range of materials, including metals, plastics, and ceramics.
This versatility makes it suitable for various industries and applications, from delicate electronic components to large automotive assemblies.
Non-Contact Process
Laser welding is a non-contact process, meaning that the laser beam itself does not physically touch the materials being welded.
This reduces the risk of contamination and wear, leading to longer-lasting equipment and higher-quality welds.
Minimal Heat-Affected Zone
The localized heating provided by the laser beam results in a minimal heat-affected zone (HAZ).
This restricts the thermal impact to a small area, preserving the integrity and properties of the surrounding material.
Applications of Laser Welding
The versatility and efficiency of laser welding make it ideal for a diverse range of applications.
Automotive Industry
The automotive industry has embraced laser welding for its ability to produce strong, durable welds with minimal distortion.
Laser welding is commonly used in the production of car bodies, engine components, and exhaust systems.
Its precision ensures high-quality welds, even in complex and demanding applications.
Aerospace Industry
In the aerospace industry, where performance and reliability are paramount, laser welding plays a critical role.
It is used in the manufacture of aircraft components, including fuel tanks, turbine blades, and structural elements.
The non-contact nature of laser welding minimizes the risk of defects and ensures the integrity of the finished product.
Electronics Industry
The precise and clean nature of laser welding makes it ideal for the electronics industry.
It is used in the assembly of printed circuit boards (PCBs), battery packs, and microelectronics.
Laser welding enables the reliable connection of small and delicate components, ensuring the functionality and longevity of electronic devices.
Medical Devices
The medical device industry relies on laser welding for its ability to produce strong, reliable, and biocompatible joints.
The technique is used in the manufacture of surgical instruments, implants, and medical equipment.
The precision and cleanliness of laser welding are especially important in applications where hygiene and safety are critical.
Jewelry and Fine Arts
Laser welding is also popular in the jewelry and fine arts industries, where precision and aesthetics are important.
It is used to repair and create intricate pieces, such as rings, earrings, and sculptures.
The non-contact nature of laser welding preserves the integrity of delicate materials, ensuring high-quality and beautiful results.
Challenges and Considerations
While laser welding offers numerous advantages, there are also some challenges and considerations to keep in mind.
Initial Cost
The initial investment for laser welding equipment can be high, particularly for high-power or specialized lasers.
However, the long-term benefits, including increased efficiency and reduced maintenance costs, can offset this initial expense.
Expertise and Training
Laser welding requires a certain level of expertise and training to achieve optimal results.
Operators must understand the specific properties and requirements of different materials, as well as the technical aspects of the laser welding process.
Material Compatibility
Not all materials are equally suited to laser welding.
Some materials, such as highly reflective metals like copper and aluminum, can present challenges due to their tendency to reflect the laser beam.
It is essential to understand the compatibility of different materials and adjust the process parameters accordingly.
Safety Considerations
The intense energy of laser beams requires strict safety measures to prevent accidents and injuries.
Protective eyewear, proper ventilation, and safety interlocks are necessary to ensure a safe working environment.
By understanding the fundamentals and applications of laser welding, manufacturers can harness the full potential of this powerful technology to produce high-quality, reliable, and efficient joints across a wide range of industries.
資料ダウンロード
QCD調達購買管理クラウド「newji」は、調達購買部門で必要なQCD管理全てを備えた、現場特化型兼クラウド型の今世紀最高の購買管理システムとなります。
ユーザー登録
調達購買業務の効率化だけでなく、システムを導入することで、コスト削減や製品・資材のステータス可視化のほか、属人化していた購買情報の共有化による内部不正防止や統制にも役立ちます。
NEWJI DX
製造業に特化したデジタルトランスフォーメーション(DX)の実現を目指す請負開発型のコンサルティングサービスです。AI、iPaaS、および先端の技術を駆使して、製造プロセスの効率化、業務効率化、チームワーク強化、コスト削減、品質向上を実現します。このサービスは、製造業の課題を深く理解し、それに対する最適なデジタルソリューションを提供することで、企業が持続的な成長とイノベーションを達成できるようサポートします。
オンライン講座
製造業、主に購買・調達部門にお勤めの方々に向けた情報を配信しております。
新任の方やベテランの方、管理職を対象とした幅広いコンテンツをご用意しております。
お問い合わせ
コストダウンが利益に直結する術だと理解していても、なかなか前に進めることができない状況。そんな時は、newjiのコストダウン自動化機能で大きく利益貢献しよう!
(Β版非公開)