- お役立ち記事
- Considerations for Procurement Departments When Upgrading Processing Equipment
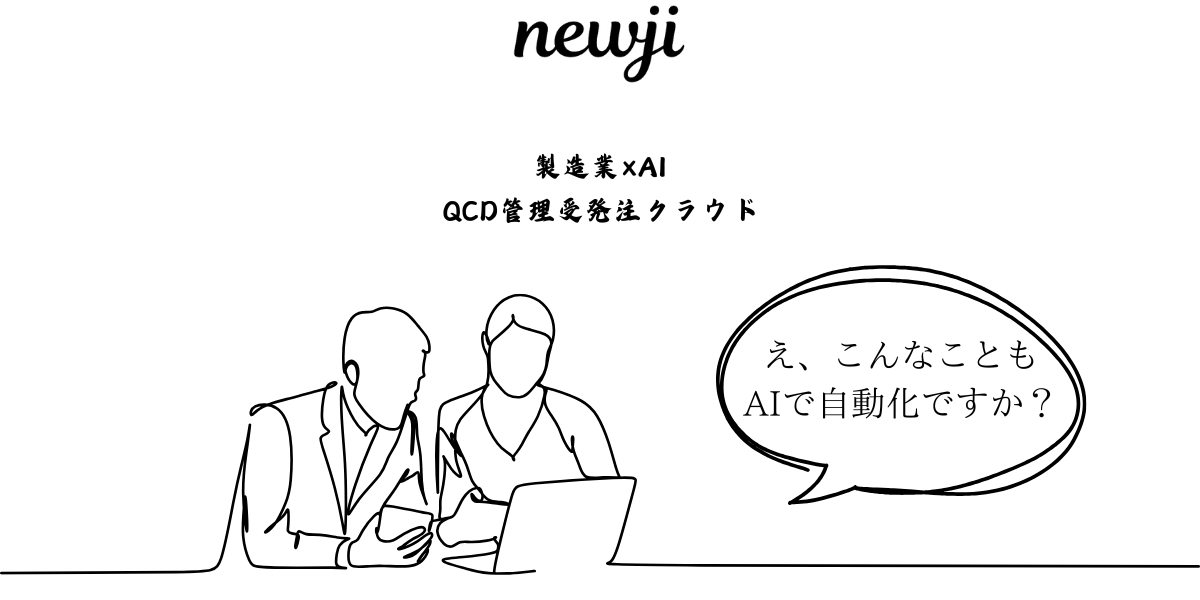
Considerations for Procurement Departments When Upgrading Processing Equipment
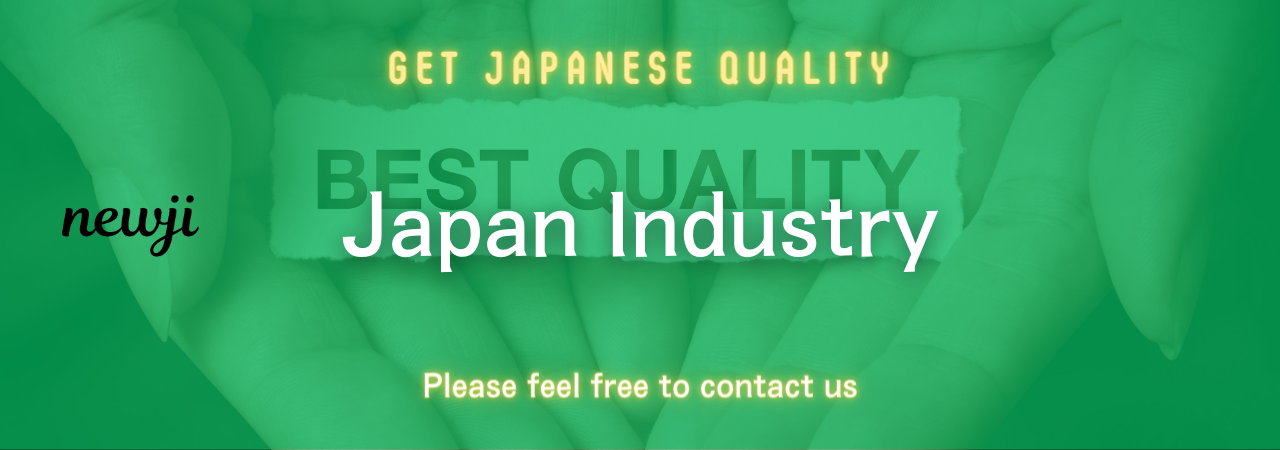
When procurement departments decide to upgrade processing equipment, they face a series of considerations that can impact the entire organization. The decision needs to be well-thought-out to ensure that the new equipment meets operational requirements, aligns with budgetary constraints, and ultimately contributes to the company’s objectives. Below, we delve into the key factors procurement teams should evaluate for a successful upgrade.
目次
Assessing Current Equipment Performance
The first step in the upgrade process is to thoroughly assess the performance of your current equipment. Analyze its efficiency, reliability, and the frequency of repairs. Look into metrics such as uptime, downtime, and maintenance costs. Compare this data against industry benchmarks to understand if your existing machinery is lagging behind modern standards.
Identify Pain Points
Identify the specific problems your current equipment is facing. Are there frequent breakdowns? Are maintenance costs rising each year? Is the equipment not meeting the production requirements? A clear list of pain points will help you determine if an upgrade is truly necessary.
Benchmarking Against Competitors
Understanding how your equipment performs compared to industry standards and competitors provides valuable insights. This benchmarking helps in making an informed decision about whether you are obtaining satisfactory efficiency or if an upgrade could offer competitive advantages.
Understanding Technological Advancements
Technological progress can dramatically enhance processing capabilities. Staying updated on the latest innovations is crucial.
Automation and AI Integration
Modern processing equipment often comes with features like automation and AI integration. These advancements can improve efficiency, reduce manual labor, and enhance accuracy. Evaluate if these technologies can be beneficial for your operations and if the investment justifies the benefits.
Energy Efficiency
Newer equipment is often more energy-efficient, leading to cost savings on utility bills and a lower environmental impact. Assess the energy consumption of potential new equipment and compare it to your current models.
Budget Constraints and Financial Planning
Upgrading processing equipment involves a significant financial outlay, making it vital to conduct a detailed cost analysis.
Total Cost of Ownership (TCO)
When evaluating new equipment, consider the Total Cost of Ownership, which includes initial purchase price, installation, maintenance, and operational costs. A thorough TCO analysis can prevent unexpected expenses and provide a clearer picture of long-term financial commitments.
Return on Investment (ROI)
Calculate the expected ROI from the upgrade. How long will it take for the new equipment to pay for itself through efficiencies gained, increased production, or reduced maintenance costs? Presenting a strong ROI case can facilitate approval from upper management.
Vendor Selection and Equipment Quality
Choosing the right vendor is as important as selecting the right equipment.
Vendor Reputation
Research potential vendors extensively. Look into their industry reputation, customer reviews, and case studies. A vendor known for reliable products and excellent customer service can significantly impact the success of your equipment upgrade.
Warranty and Support
Examine the warranty and after-sales support offered by each vendor. Ensure that comprehensive support packages, including regular servicing and quick replacement of faulty parts, are part of the deal. After-sales support can be crucial in minimizing downtime during equipment failures.
Compliance and Safety Standards
New processing equipment must comply with industry standards and safety regulations.
Regulatory Compliance
Make sure the equipment you plan to purchase complies with local, national, and international regulations. Non-compliance can result in hefty fines and operational disruptions.
Safety Features
Evaluate the safety features of the new equipment. Features such as emergency stop buttons, protective guards, and automatic shutoff mechanisms are vital for ensuring the safety of your workforce.
Training and Employee Readiness
An often-overlooked aspect of upgrading processing equipment is employee training.
Training Programs
Organize comprehensive training programs to familiarize staff with the new equipment. Effective training ensures smooth integration into daily operations and maximizes the benefits of the new technology.
Operator Buy-In
Gaining buy-in from operators is essential. They should be involved in the selection process when possible, as their hands-on experience can provide valuable insights into practical considerations. Engaging operators early can also ease the transition and boost morale.
Scalability and Future Needs
It’s not just about meeting current needs; the new equipment should be scalable to meet future demands.
Production Capacity
Consider the production capacity of the new equipment. Ensure it can handle projected future growth without needing another upgrade in the near term.
Flexibility
Look for equipment that offers flexibility in usage. Machinery that can adapt to different processes or products gives you greater operational agility and helps future-proof your investment.
Conclusion
Upgrading processing equipment is a multifaceted decision that requires careful consideration of current performance, technological advancements, budget constraints, vendor quality, compliance standards, employee readiness, and future needs. By meticulously analyzing these factors, procurement departments can make informed choices that drive efficiency, safety, and overall organizational growth.
資料ダウンロード
QCD調達購買管理クラウド「newji」は、調達購買部門で必要なQCD管理全てを備えた、現場特化型兼クラウド型の今世紀最高の購買管理システムとなります。
ユーザー登録
調達購買業務の効率化だけでなく、システムを導入することで、コスト削減や製品・資材のステータス可視化のほか、属人化していた購買情報の共有化による内部不正防止や統制にも役立ちます。
NEWJI DX
製造業に特化したデジタルトランスフォーメーション(DX)の実現を目指す請負開発型のコンサルティングサービスです。AI、iPaaS、および先端の技術を駆使して、製造プロセスの効率化、業務効率化、チームワーク強化、コスト削減、品質向上を実現します。このサービスは、製造業の課題を深く理解し、それに対する最適なデジタルソリューションを提供することで、企業が持続的な成長とイノベーションを達成できるようサポートします。
オンライン講座
製造業、主に購買・調達部門にお勤めの方々に向けた情報を配信しております。
新任の方やベテランの方、管理職を対象とした幅広いコンテンツをご用意しております。
お問い合わせ
コストダウンが利益に直結する術だと理解していても、なかなか前に進めることができない状況。そんな時は、newjiのコストダウン自動化機能で大きく利益貢献しよう!
(Β版非公開)