- お役立ち記事
- Cost Efficiency Improvement Strategies for Foundry Processing Providers
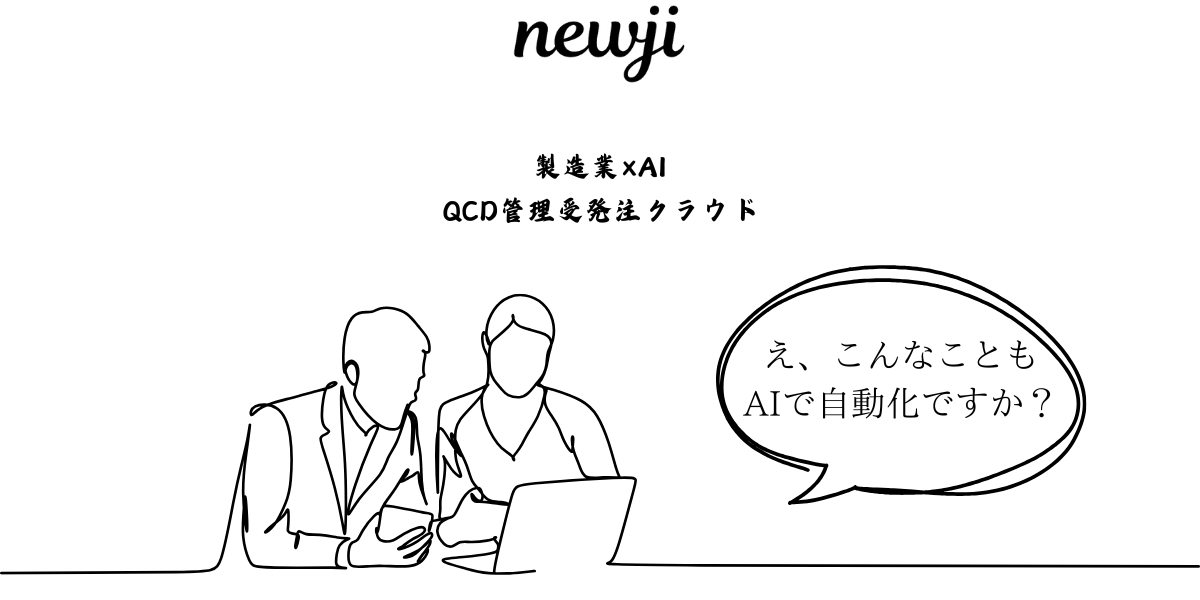
Cost Efficiency Improvement Strategies for Foundry Processing Providers
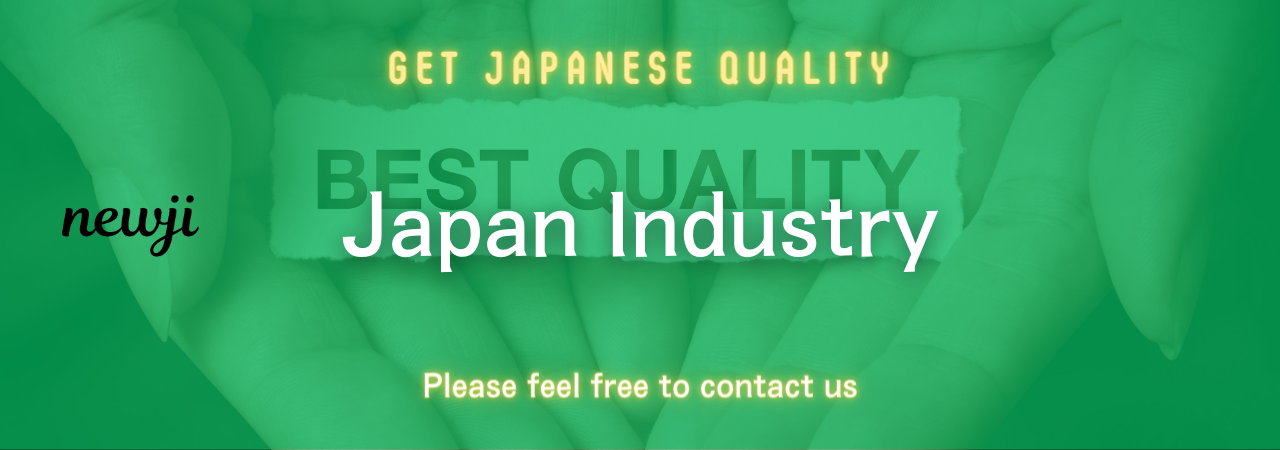
Foundry processing providers are essential players in the manufacturing industry, supplying critical components to a variety of sectors. However, the rising costs of raw materials, labor, and energy present ongoing challenges. This article explores cost efficiency improvement strategies to help foundry processing providers remain competitive while maintaining high-quality standards.
目次
Optimizing Raw Material Usage
Efficient use of raw materials is crucial for foundry providers. By optimizing the raw material mix and utilizing recycled materials when possible, companies can significantly lower costs.
Material Substitution
Substituting expensive raw materials with less costly alternatives can cut down expenses. For instance, in some applications, replacing steel with aluminum can save money without compromising quality.
Recycling Scrap
Recycling scrap metal within the foundry can also lead to substantial savings. Implementing a robust recycling protocol means reclaiming valuable materials that would otherwise go to waste.
Improving Energy Efficiency
Energy costs can account for a significant portion of a foundry’s expenses. Adopting energy-efficient practices and technologies can reduce these costs.
Upgrading Equipment
Modernizing outdated machinery with energy-efficient models can result in both immediate and long-term energy savings. High-efficiency furnaces, for example, consume less power and contribute to lower utility bills.
Optimizing Production Schedules
Optimizing production schedules to run energy-intensive processes during off-peak hours can also lead to cost savings. Many utility companies offer lower rates during non-peak times, making this a viable strategy for reducing energy costs.
Enhancing Labor Efficiency
Labor is another major cost for foundry processing providers. Streamlining workflow and improving labor productivity can help optimize this expense.
Employee Training
Investing in employee training ensures that workers are skilled and efficient. Well-trained staff can operate machinery more effectively, leading to reduced downtime and fewer errors.
Automation
Automating repetitive tasks can also boost productivity and reduce labor costs. Robotics and automated systems can handle tasks like casting and molding, allowing human workers to focus on more complex operations.
Incorporating Technology for Operational Efficiency
Leveraging modern technology can improve operational efficiency and cut costs.
Implementing ERP Systems
Enterprise Resource Planning (ERP) systems can provide real-time insights into inventory, production schedules, and supply chain management. These systems help foundry providers optimize operations, reduce waste, and manage costs effectively.
Adopting IoT
The Internet of Things (IoT) can offer predictive maintenance for machinery, reducing unexpected downtime. Sensors and connected devices provide data that help in preventing malfunctions, thereby minimizing repair costs and extending equipment lifespan.
Reducing Waste
Minimizing waste not only helps the environment but also cuts costs for foundry processing providers.
Lean Manufacturing
Adopting lean manufacturing principles helps identify and eliminate waste in production processes. Techniques such as value stream mapping can pinpoint areas where resources are being wasted and suggest improvements.
Inventory Management
Effective inventory management ensures that materials are available when needed, without overstocking. Just-in-time inventory systems minimize holding costs and reduce waste associated with excess materials.
Strategic Sourcing and Supplier Relationships
Strong relationships with suppliers and strategic sourcing can lead to better terms and reduced costs.
Negotiating Terms
Negotiating favorable terms with suppliers can result in cost savings. This includes discounts for bulk purchasing or long-term contracts that offer stability and predictability.
Supplier Diversification
Diversifying suppliers reduces dependence on a single source and can lead to more competitive pricing. It also mitigates risks associated with supply chain disruptions.
Implementing Quality Control
High-quality standards reduce rework, scrap, and warranty costs, saving money in the long run.
Quality Assurance Programs
Implementing robust quality assurance programs ensures that defects are caught and addressed early. Techniques like Six Sigma and Total Quality Management (TQM) can help improve overall product quality.
Continuous Improvement
Encouraging a culture of continuous improvement allows for ongoing assessments and refinements of processes. Employee suggestions and feedback loops can lead to innovative solutions that enhance efficiency and reduce costs.
Conclusion
Improving cost efficiency is essential for foundry processing providers to stay competitive in a challenging market. By optimizing raw material usage, enhancing energy and labor efficiency, leveraging technology, reducing waste, and fostering strong supplier relationships, foundries can achieve significant cost savings. Implementing these strategies requires effort and investment but can result in long-term benefits, ensuring sustainable growth and profitability.
資料ダウンロード
QCD調達購買管理クラウド「newji」は、調達購買部門で必要なQCD管理全てを備えた、現場特化型兼クラウド型の今世紀最高の購買管理システムとなります。
ユーザー登録
調達購買業務の効率化だけでなく、システムを導入することで、コスト削減や製品・資材のステータス可視化のほか、属人化していた購買情報の共有化による内部不正防止や統制にも役立ちます。
NEWJI DX
製造業に特化したデジタルトランスフォーメーション(DX)の実現を目指す請負開発型のコンサルティングサービスです。AI、iPaaS、および先端の技術を駆使して、製造プロセスの効率化、業務効率化、チームワーク強化、コスト削減、品質向上を実現します。このサービスは、製造業の課題を深く理解し、それに対する最適なデジタルソリューションを提供することで、企業が持続的な成長とイノベーションを達成できるようサポートします。
オンライン講座
製造業、主に購買・調達部門にお勤めの方々に向けた情報を配信しております。
新任の方やベテランの方、管理職を対象とした幅広いコンテンツをご用意しております。
お問い合わせ
コストダウンが利益に直結する術だと理解していても、なかなか前に進めることができない状況。そんな時は、newjiのコストダウン自動化機能で大きく利益貢献しよう!
(Β版非公開)