- お役立ち記事
- Cost Efficiency Strategies for Success in Casting Processing
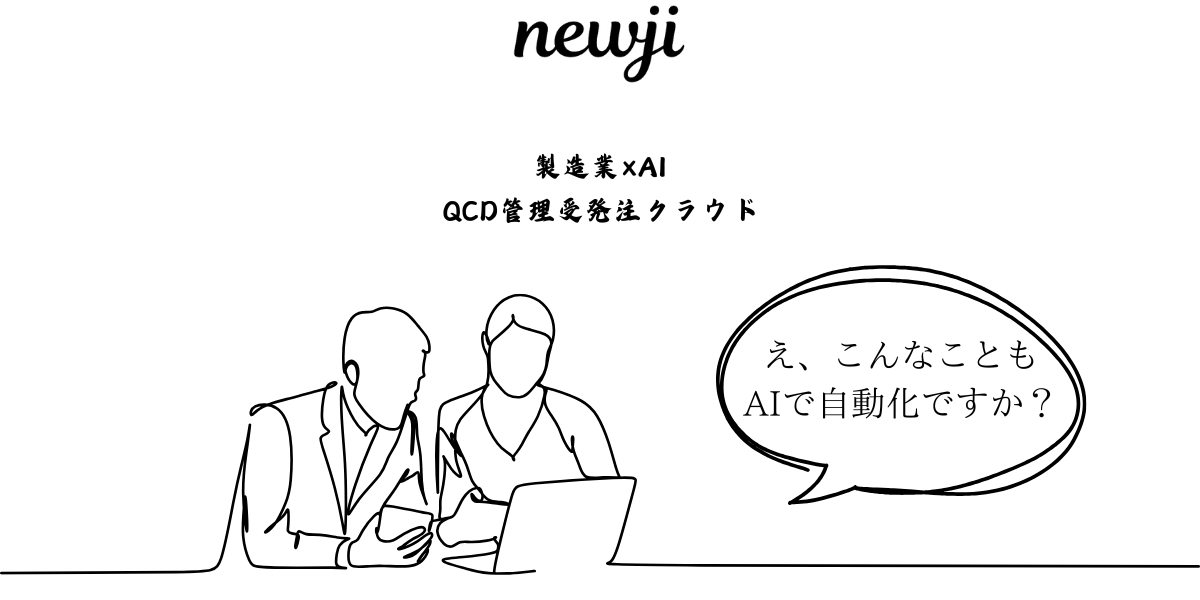
Cost Efficiency Strategies for Success in Casting Processing
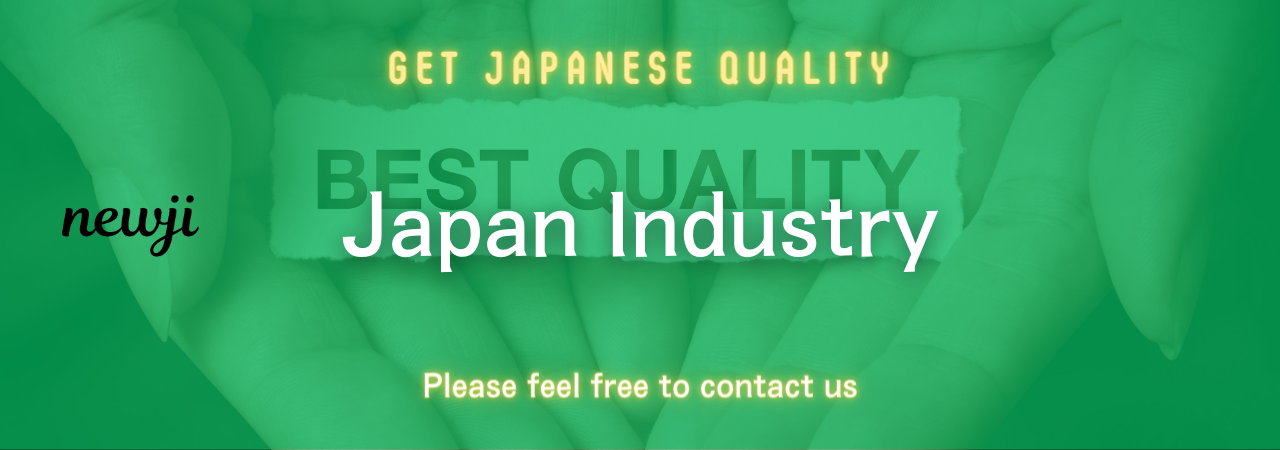
Casting processing is a crucial part of many manufacturing operations.
However, it can be costly if not managed properly.
Implementing cost efficiency strategies can lead to significant savings and success in this industry.
This article explores some effective strategies to enhance cost efficiency in casting processing.
目次
Understanding Casting Processing
Casting processing involves pouring liquid material into a mold, where it solidifies into a specific shape.
Common materials used in casting are metals, plastic resins, and plaster.
Understanding the intricacies of the casting procedure is the first step in identifying areas for cost reduction.
Complex designs and poor material choices can drive up costs and lead to defects.
Invest in Quality Equipment
Choose High-Precision Molds
The quality of molds used in casting has a direct impact on the final product.
Investing in high-precision molds ensures fewer defects and lower waste.
Though the initial cost may be higher, precision molds lead to long-term savings by reducing the need for rework.
Regular Maintenance
Equipment maintenance is crucial for smooth operations.
Regular checks and timely repairs can prevent costly breakdowns.
Scheduled maintenance helps in identifying issues before they escalate into major problems, ensuring uninterrupted production.
Optimize Material Usage
Select the Right Materials
Material selection plays a pivotal role in cost efficiency.
Using the right materials not only ensures quality but also minimizes waste.
Evaluate the properties required for your products and choose materials that meet those criteria without excessive costs.
Recycle and Reuse
Recycling and reusing materials can significantly cut down costs.
Metal scraps, for instance, can be melted and used again.
Implement a system for collecting and repurposing waste materials to maximize resource utilization.
Enhance Energy Efficiency
Upgrade to Energy-Efficient Equipment
Energy costs contribute significantly to overall casting expenses.
Upgrading to energy-efficient furnaces and machinery can reduce these costs.
Energy-efficient equipment not only lowers power consumption but also often lasts longer, providing dual benefits.
Implement Energy-Saving Practices
Train employees on energy-saving practices.
Simple steps like turning off equipment when not in use or optimizing operation schedules can lead to noticeable savings.
Regular energy audits can help identify further areas for improvement.
Improve Process Efficiency
Implement Lean Manufacturing Principles
Lean manufacturing principles focus on minimizing waste without sacrificing productivity.
Techniques such as Just-in-Time (JIT) production ensure that materials are used only when needed, reducing inventory costs.
Streamlining processes to eliminate redundancies can lead to smoother and faster production cycles.
Automate Where Possible
Automation offers precise control over casting processes, reducing human error and increasing efficiency.
While the initial investment in automation can be high, the long-term benefits in terms of consistent quality and reduced labor costs make it worthwhile.
Automated systems can handle repetitive tasks, freeing up skilled workers for more complex duties.
Implement Quality Control Measures
Regular Inspections
Quality control is essential to prevent costly defects.
Regular inspections at various stages of the casting process can identify issues early.
This allows for timely corrections and avoids the expense of reworking or scrapping defective products.
Testing and Validation
Conduct thorough testing and validation of products before they leave the factory.
Advanced techniques like non-destructive testing (NDT) can identify hidden flaws without damaging the product.
Ensuring that only quality products reach customers reduces returns and maintains a good reputation.
Focus on Training and Development
Skilled Workforce
A well-trained workforce is more efficient and less prone to errors.
Invest in regular training programs to keep employees updated with the latest techniques and safety practices.
Skilled workers are better at identifying potential issues and ensuring high-quality output.
Encourage Continuous Improvement
Create a culture of continuous improvement within the organization.
Encourage employees to suggest improvements in processes and equipment usage.
Implementing valuable suggestions from those on the production floor can lead to innovative cost-saving measures.
Conclusion
Cost efficiency in casting processing is achievable by investing in quality equipment, optimizing material usage, enhancing energy efficiency, improving process efficiency, implementing robust quality control measures, and focusing on training and development.
By adopting these strategies, manufacturers can significantly reduce costs while maintaining high-quality output.
This approach not only leads to immediate savings but also positions the company for long-term success in the competitive casting industry.
資料ダウンロード
QCD調達購買管理クラウド「newji」は、調達購買部門で必要なQCD管理全てを備えた、現場特化型兼クラウド型の今世紀最高の購買管理システムとなります。
ユーザー登録
調達購買業務の効率化だけでなく、システムを導入することで、コスト削減や製品・資材のステータス可視化のほか、属人化していた購買情報の共有化による内部不正防止や統制にも役立ちます。
NEWJI DX
製造業に特化したデジタルトランスフォーメーション(DX)の実現を目指す請負開発型のコンサルティングサービスです。AI、iPaaS、および先端の技術を駆使して、製造プロセスの効率化、業務効率化、チームワーク強化、コスト削減、品質向上を実現します。このサービスは、製造業の課題を深く理解し、それに対する最適なデジタルソリューションを提供することで、企業が持続的な成長とイノベーションを達成できるようサポートします。
オンライン講座
製造業、主に購買・調達部門にお勤めの方々に向けた情報を配信しております。
新任の方やベテランの方、管理職を対象とした幅広いコンテンツをご用意しております。
お問い合わせ
コストダウンが利益に直結する術だと理解していても、なかなか前に進めることができない状況。そんな時は、newjiのコストダウン自動化機能で大きく利益貢献しよう!
(Β版非公開)