- お役立ち記事
- Counteracting Oxidation in Manufacturing and Management Methods
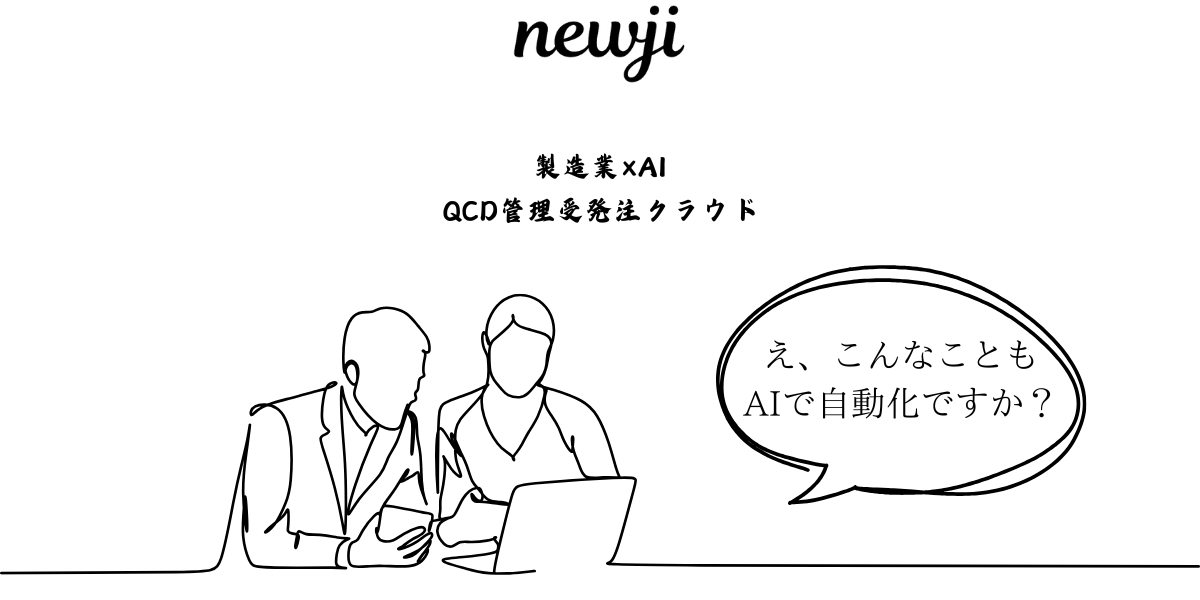
Counteracting Oxidation in Manufacturing and Management Methods
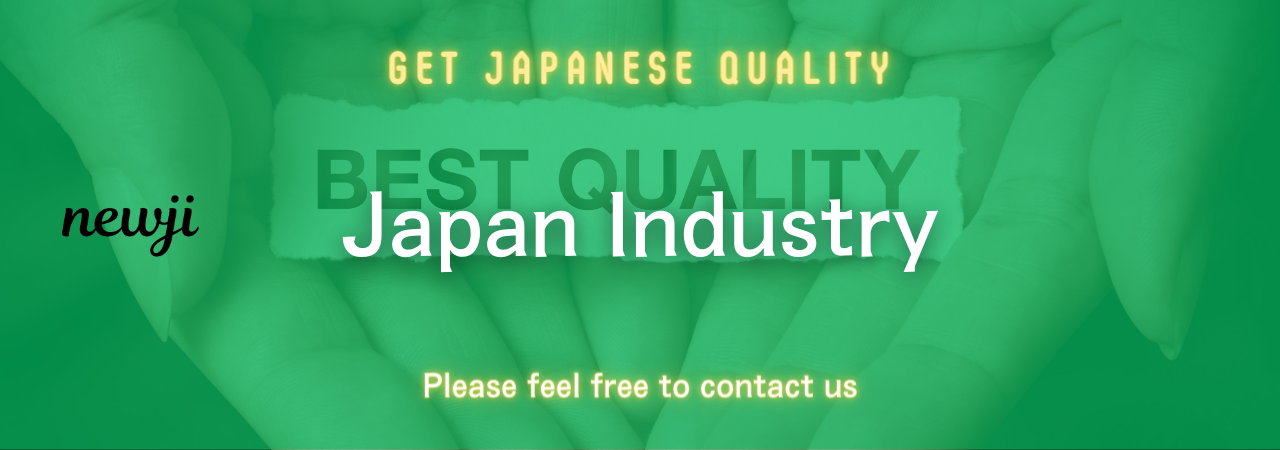
目次
Understanding Oxidation in the Manufacturing Process
Oxidation is a natural chemical reaction that occurs when materials interact with oxygen in the environment.
In the context of manufacturing, oxidation can have detrimental effects on materials, leading to issues such as corrosion, rust, and degradation of quality.
Understanding the oxidation process is crucial for developing strategies to counteract these effects and maintain the integrity of products.
What Happens During Oxidation?
During oxidation, electrons from a substance are transferred to an oxidizing agent, usually oxygen.
This process changes the chemical composition of the material.
For example, when iron oxidizes, it forms iron oxide, commonly known as rust.
This transformation weakens the material, reducing its strength and durability.
Oxidation isn’t limited to metals; it can affect other materials like plastics and rubber.
For instance, when the surface of rubber is exposed to oxygen and ozone, it becomes brittle and cracks.
In the manufacturing industry, this can be particularly problematic, leading to product failures and costly repairs.
Effects of Oxidation on Different Materials
Different materials react to oxidation in various ways.
Understanding these reactions helps in implementing specific methods to manage and counteract oxidation.
Metals
Metals are particularly susceptible to oxidation.
Iron, copper, and aluminum, among others, form oxides when they contact oxygen.
Rust is the most commonly recognized form of oxidation in metals.
It not only weakens the metal but also makes it less aesthetically pleasing.
In sectors such as construction and automotive, managing metal oxidation is crucial to ensure the longevity of structures and vehicles.
Polymers and Plastics
Plastics and polymers undergo a process called oxidative degradation.
This occurs when environmental factors like ultraviolet (UV) light and oxygen cause the molecular chains in these materials to deteriorate.
Products may become discolored, lose flexibility, or even crack.
This is significant in industries where plastic is used extensively, such as packaging, consumer goods, and electronics.
Semiconductors
Oxidation in semiconductors can impact their performance.
For instance, silicon dioxide layers form on silicon wafers during the manufacturing of electronic components.
While specific oxidation processes are essential for creating insulative barriers, unintended oxidation can damage circuits.
Therefore, controlling the oxidation levels in semiconductor manufacturing is critical for ensuring the efficiency and performance of electronic devices.
Methods to Counteract Oxidation in Manufacturing
Several strategies can be implemented to mitigate the effects of oxidation in the manufacturing process.
Protective Coatings
Applying protective coatings is one of the most effective methods to prevent oxidation.
These coatings create a barrier between the material and the environment.
Common protective coatings include paint, galvanization, and anodization.
Paint can act as a barrier, preventing moisture and oxygen from reaching the metal surface.
Galvanization involves coating the metal with a layer of zinc, providing both a physical barrier and sacrificial protection.
Anodization, typically used for aluminum, forms a thick, protective oxide layer through an electrochemical process.
Environmental Controls
Controlling the environment where manufacturing processes occur can significantly reduce the risk of oxidation.
This includes regulating temperature, humidity, and exposure to oxygen.
For instance, manufacturing in a controlled environment with low humidity and minimal oxygen can prevent oxidation.
Using vacuum chambers or inert gas atmospheres (like argon or nitrogen) during production creates an environment where oxidation is less likely to occur.
Using Anti-Oxidation Additives
Adding anti-oxidation compounds during the manufacturing process can help protect materials from oxidation.
For example, polymers and plastics can be mixed with anti-oxidant additives that extend their lifespan by preventing oxidative degradation.
In the case of lubricants and oils used in machinery, incorporating anti-oxidant chemicals can prevent the oils from breaking down over time, maintaining the efficiency and longevity of the equipment.
Regular Maintenance and Inspection
Regular maintenance and inspection of manufacturing equipment and products help in early detection and prevention of oxidation-related damage.
Routine checks can identify signs of oxidation, such as discoloration or surface pitting, allowing for timely corrective measures.
Implementing scheduled maintenance routines and employing predictive maintenance technologies can prevent oxidation from causing severe damage.
Advanced Technologies for Oxidation Control
Continuous advancements in technology provide more sophisticated methods to counteract oxidation.
Nanotechnology
Nanotechnology offers promising solutions for preventing oxidation.
Applying nano-coatings to materials can create super-hydrophobic surfaces that repel water and resist oxidation.
These coatings are highly durable and provide long-lasting protection, even in harsh environmental conditions.
Laser Treatments
Laser treatments can alter the surface properties of materials to enhance their resistance to oxidation.
Laser surface melting and laser alloying techniques modify the surface composition, creating protective layers that inhibit oxidation.
Electrochemical Methods
Electrochemical methods, such as cathodic protection, involve applying an electrical current to the material to prevent oxidation.
This technique is commonly used in pipelines and underground structures to prevent corrosion and ensure structural integrity.
Conclusion
Counteracting oxidation is a crucial aspect of manufacturing to maintain the quality and durability of products.
By understanding the oxidation process and its effects on different materials, manufacturers can implement effective strategies to mitigate these risks.
From applying protective coatings to utilizing advanced technologies like nanotechnology and laser treatments, there are various methods available to combat oxidation.
Regular maintenance and inspection further ensure that oxidation-related issues are addressed promptly.
With a comprehensive approach to managing oxidation, manufacturers can enhance the longevity and performance of their products, contributing to overall business success.
資料ダウンロード
QCD調達購買管理クラウド「newji」は、調達購買部門で必要なQCD管理全てを備えた、現場特化型兼クラウド型の今世紀最高の購買管理システムとなります。
ユーザー登録
調達購買業務の効率化だけでなく、システムを導入することで、コスト削減や製品・資材のステータス可視化のほか、属人化していた購買情報の共有化による内部不正防止や統制にも役立ちます。
NEWJI DX
製造業に特化したデジタルトランスフォーメーション(DX)の実現を目指す請負開発型のコンサルティングサービスです。AI、iPaaS、および先端の技術を駆使して、製造プロセスの効率化、業務効率化、チームワーク強化、コスト削減、品質向上を実現します。このサービスは、製造業の課題を深く理解し、それに対する最適なデジタルソリューションを提供することで、企業が持続的な成長とイノベーションを達成できるようサポートします。
オンライン講座
製造業、主に購買・調達部門にお勤めの方々に向けた情報を配信しております。
新任の方やベテランの方、管理職を対象とした幅広いコンテンツをご用意しております。
お問い合わせ
コストダウンが利益に直結する術だと理解していても、なかなか前に進めることができない状況。そんな時は、newjiのコストダウン自動化機能で大きく利益貢献しよう!
(Β版非公開)