- お役立ち記事
- Criteria for selecting certified suppliers in the aerospace industry
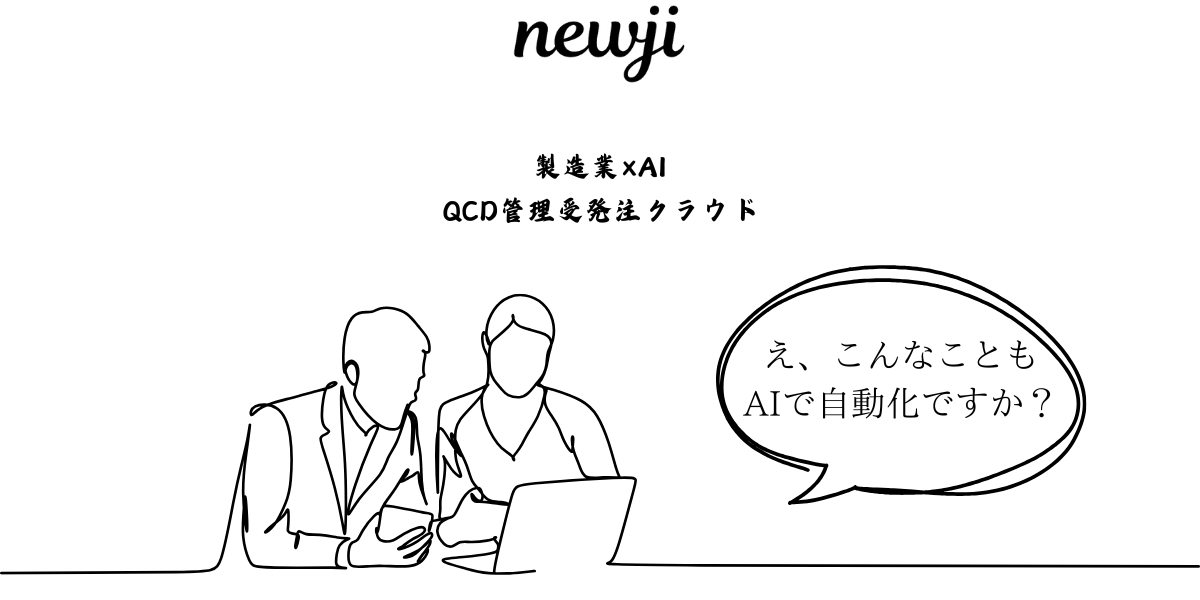
Criteria for selecting certified suppliers in the aerospace industry
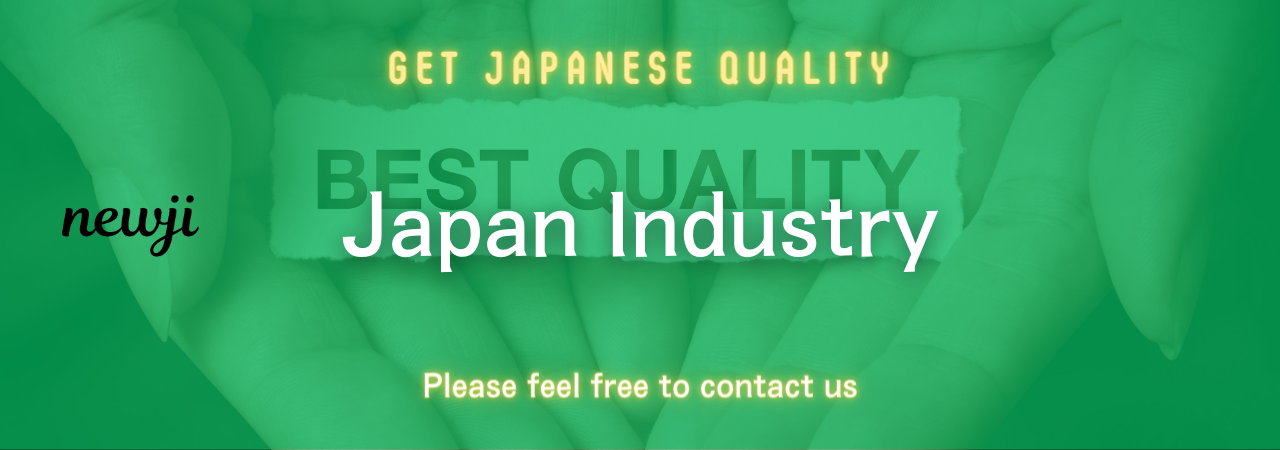
目次
Understanding Certified Suppliers in the Aerospace Industry
The aerospace industry is a complex field that demands high levels of precision, safety, and quality assurance.
One of the key components ensuring these standards are met is the selection of certified suppliers.
These suppliers must meet stringent criteria to provide materials and services essential for aircraft manufacturing and maintenance.
But what exactly makes a supplier certified, and why is it crucial in aerospace?
Let’s dive deeper to understand the criteria and how they play a vital role in the industry.
Why Certification Matters in Aerospace
Certification in the aerospace industry is not merely a formality; it serves numerous critical functions.
Firstly, it ensures safety by meeting regulatory and industry standards.
When suppliers are certified, it means they comply with all the necessary safety protocols, reducing the risk of failures in aircraft components.
Secondly, certification fosters trust and reliability in the supply chain, which is crucial for maintaining efficient and smooth operations.
Certified suppliers are recognized for their consistency in delivering high-quality products that meet the precise specifications required in the aerospace sector.
These certifications are a testament to a supplier’s ability to adhere to strict quality management systems, which are essential for the intricate components used in aircraft.
The Role of International Standards
A significant aspect of supplier certification involves adherence to international standards.
Organizations such as the International Organization for Standardization (ISO) and the Aerospace Standardization Committee (AS) set benchmarks that suppliers must meet.
Standards like ISO 9001:2015 and AS9100 focus on quality management systems tailored specifically for the aerospace industry.
These standards guide suppliers in implementing processes that ensure consistent production quality, risk management, and customer satisfaction.
Certification to these standards indicates a supplier’s commitment to maintaining the high-quality benchmarks crucial for aerospace components and services.
Key Criteria for Selecting Certified Suppliers
When selecting certified suppliers in the aerospace industry, several key criteria are evaluated.
These criteria encompass quality assurance, operational capabilities, regulatory compliance, and experience.
Understanding these elements helps businesses choose the right partners for their supply chain.
Quality Assurance
Quality assurance is the cornerstone of certified suppliers.
Suppliers must demonstrate a robust quality management system that conforms to aerospace standards.
This includes rigorous testing and inspection procedures to ensure every product meets the necessary specifications.
Any deviation from these standards could lead to catastrophic failures, hence the emphasis on impeccable quality control.
Operational Capabilities
The operational capabilities of a supplier are crucial to meeting the demands of the aerospace industry.
This includes their production capacity, technology, and ability to deliver products on time.
Suppliers must have the technical expertise and infrastructure to handle complex aerospace projects.
Their operational strength determines whether they can consistently meet the industry’s high demands and adapt to any changes or emergencies.
Regulatory Compliance
Regulatory compliance is another critical criterion for certified suppliers.
Suppliers must adhere to aviation regulations from bodies such as the Federal Aviation Administration (FAA) and the European Union Aviation Safety Agency (EASA).
Compliance ensures all components and materials supplied are legally approved for use in aircraft.
This adherence is validated through certifications that assure regulatory standards are consistently met.
Experience and Track Record
The experience and track record of a supplier are vital indicators of their reliability and expertise.
A proven history of working with major aerospace companies or on significant projects often reflects a supplier’s ability to perform at the required level.
Experience in the industry generally means a better understanding of its challenges, leading to more efficient and effective solutions.
Challenges in Supplier Certification
While certification is crucial, it is not without its challenges.
The process of becoming a certified supplier can be rigorous and costly.
Suppliers must invest in quality systems and comply with numerous audits and inspections.
Additionally, staying updated with evolving standards and regulations requires ongoing effort and resources.
These challenges, however, are necessary to ensure the safety and reliability of aerospace operations.
The Future of Supplier Certification
As technology and regulations evolve, so too will the criteria for certified suppliers.
Emerging technologies such as 3D printing and advanced composites will require new standards and certification processes.
Moreover, the increasing emphasis on sustainability will likely shape future certification criteria, focusing on environmentally friendly practices.
Remaining adaptable and responsive to these changes will be a priority for suppliers looking to maintain certification in the aerospace industry.
Conclusion
In conclusion, certified suppliers play a pivotal role in ensuring the safety and quality of aerospace operations.
By meeting strict criteria involving quality assurance, operational capabilities, regulatory compliance, and experience, these suppliers uphold the standards critical to the industry’s success.
The process is challenging but crucial, guaranteeing that aerospace components and services are reliable and safe.
As the industry progresses, maintaining a focus on robust certification processes will remain integral to advancing aerospace technology and operations safely and efficiently.
資料ダウンロード
QCD調達購買管理クラウド「newji」は、調達購買部門で必要なQCD管理全てを備えた、現場特化型兼クラウド型の今世紀最高の購買管理システムとなります。
ユーザー登録
調達購買業務の効率化だけでなく、システムを導入することで、コスト削減や製品・資材のステータス可視化のほか、属人化していた購買情報の共有化による内部不正防止や統制にも役立ちます。
NEWJI DX
製造業に特化したデジタルトランスフォーメーション(DX)の実現を目指す請負開発型のコンサルティングサービスです。AI、iPaaS、および先端の技術を駆使して、製造プロセスの効率化、業務効率化、チームワーク強化、コスト削減、品質向上を実現します。このサービスは、製造業の課題を深く理解し、それに対する最適なデジタルソリューションを提供することで、企業が持続的な成長とイノベーションを達成できるようサポートします。
オンライン講座
製造業、主に購買・調達部門にお勤めの方々に向けた情報を配信しております。
新任の方やベテランの方、管理職を対象とした幅広いコンテンツをご用意しております。
お問い合わせ
コストダウンが利益に直結する術だと理解していても、なかなか前に進めることができない状況。そんな時は、newjiのコストダウン自動化機能で大きく利益貢献しよう!
(Β版非公開)