- お役立ち記事
- Cutting Board Manufacturing Process and Durability Improvement
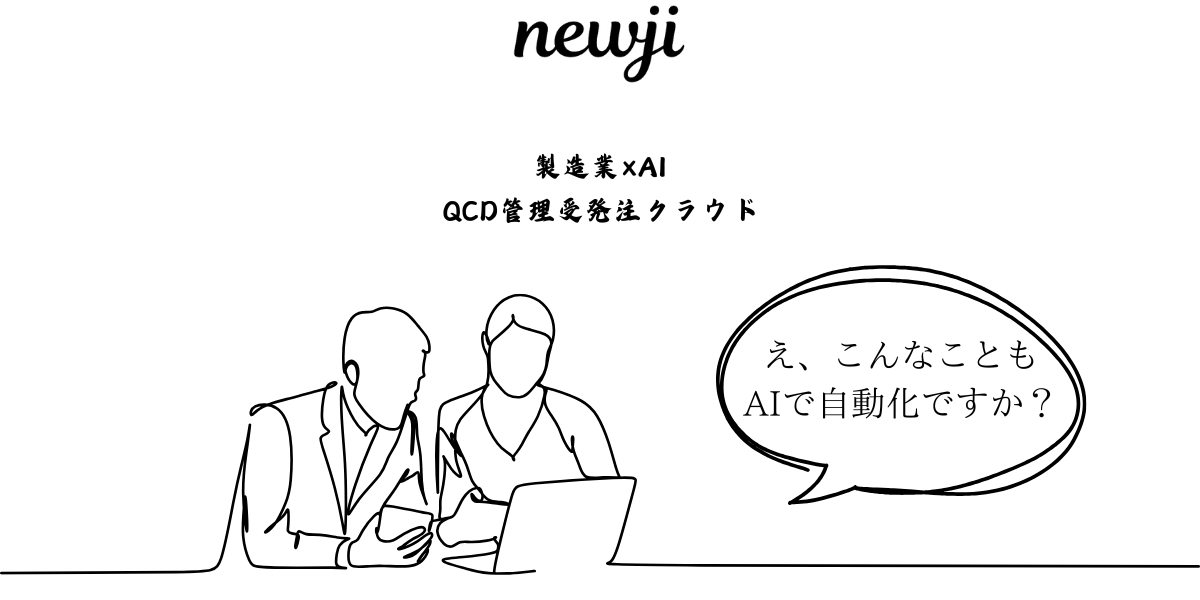
Cutting Board Manufacturing Process and Durability Improvement
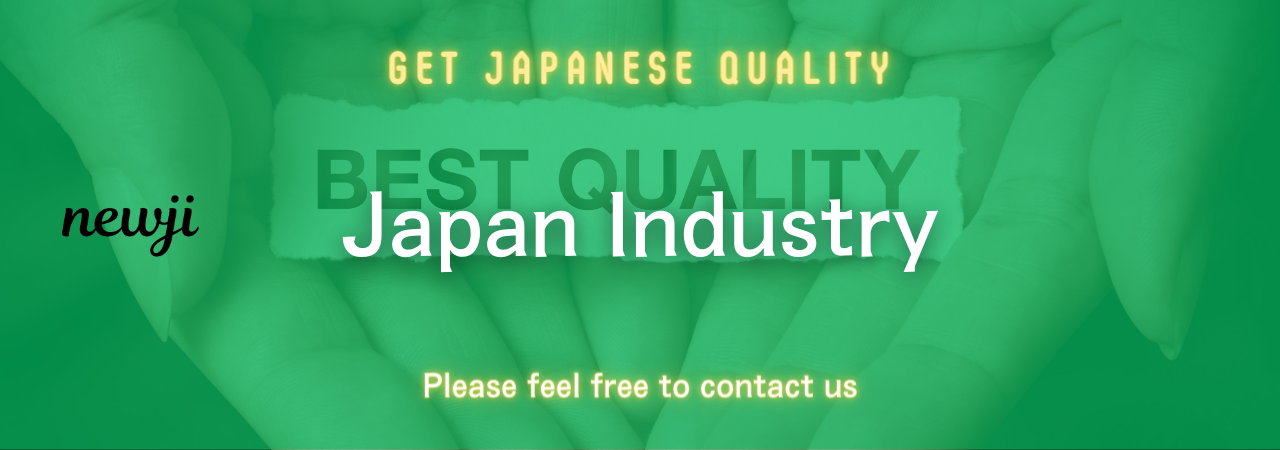
Understanding the Cutting Board Manufacturing Process
Cutting boards are essential kitchen tools found in every home, restaurant, and food processing area.
Their simple design might lead one to believe they are easy to produce, yet the manufacturing process involves several crucial steps.
A better understanding of these steps can not only appreciate the craftsmanship but also highlight the steps manufacturers take to enhance their durability.
Selecting the Right Materials
The journey of a cutting board begins with the selection of materials.
Manufacturers choose from a variety of options, including wood, plastic, bamboo, and even glass.
Each material has its unique advantages and limitations.
Wooden cutting boards are highly popular due to their aesthetics and natural antimicrobial properties.
They are often made from hardwoods like maple, teak, or walnut.
Plastic cutting boards, typically made of polyethylene or polypropylene, are favored for their ease of cleaning and maintenance.
Bamboo boards, although technically grass, are sturdy, eco-friendly, and resistant to moisture.
Processing Raw Materials
Once the material is selected, it is processed to prepare it for shaping.
For wooden boards, this involves acclimating the wood to ensure it has the right moisture content.
Too much moisture can lead to warping or cracking during use.
Wood is cut into blanks and then dried in a kiln to bring it to a stable moisture level.
In the case of plastic boards, raw plastic pellets are melted and extruded into sheets.
These sheets are then cooled and cut into required sizes, forming the base for the cutting boards.
Shaping and Sanding
The next step is shaping the boards into their final forms.
For wooden and bamboo boards, this involves cutting the dried blanks into the desired size and shape using saws.
Intricate or decorative edges may require additional routing.
Plastic boards are typically formed through a molding process, allowing for more uniform thickness and dimensions.
Once the boards are shaped, sanding is essential to ensure a smooth surface.
Sanding removes any rough edges and creates the perfect texture for cutting.
Assembling and Gluing
In the case of end grain cutting boards, the wood pieces are assembled in a specific pattern with the grain facing up, which is known for being more gentle on knives.
This intricate design requires precision in gluing and clamping to ensure the pieces hold together securely.
Manufacturers use food-safe adhesives to bond the pieces, which are clamped tightly for several hours to ensure strength.
Once set, any excess adhesive is removed, and the board is given another round of sanding for a seamless finish.
Finishing Touches
After shaping and assembly, the cutting boards go through a finishing process.
Wooden and bamboo boards are often treated with food-safe mineral oil to enhance their appearance and prevent moisture absorption.
This finish also improves the board’s resistance to stains and warping.
Plastic boards might undergo a texturizing process to create a surface that minimizes knife slips.
Smooth plastic boards may also be embossed with brand logos or measurement grids as additional features.
Quality Control Checks
Before the cutting boards hit the market, they undergo rigorous quality control checks.
These checks include testing for durability, surface integrity, and adherence to safety standards.
Manufacturers pay special attention to the edges and surfaces to ensure there are no defects that could potentially cause harm.
Improving Cutting Board Durability
While the manufacturing process aims to create strong cutting boards, several steps can enhance their longevity further.
Regular Maintenance
One of the simplest ways to extend a cutting board’s life is through regular maintenance.
For wooden and bamboo boards, applying mineral oil periodically helps to maintain their resistance to moisture and prevents cracking.
Avoid soaking these boards in water as it can lead to warping.
Plastic boards are generally low-maintenance but should be regularly cleaned to prevent bacteria build-up.
Dishwashing detergent and warm water are usually sufficient, but some boards are also dishwasher safe.
Avoiding Cross-Contamination
To ensure both durability and safety, use separate cutting boards for different food types.
Designating one board for raw meats and another for vegetables minimizes wear and reduces the risk of cross-contamination.
Proper Storage
Storing cutting boards properly can also aid in their longevity.
Avoid stacking boards with heavy objects on top, especially for wooden varieties, as the weight could cause indentations or fractures.
Upright storage or using a dedicated cutting board rack is ideal.
Choosing the Right Board for the Task
Selecting the right type of cutting board for the task at hand can make a significant difference in longevity.
For example, using a softer wooden board for heavy chopping tasks ensures less strain on the material compared to more rigid surfaces like glass.
In conclusion, the cutting board manufacturing process is intricate, involving careful selection of materials, precise assembly, and attentive finishing.
By understanding these processes and incorporating proper care practices, users can significantly extend the lifespan of their cutting boards, ensuring that they continue to be a reliable tool in the kitchen.
資料ダウンロード
QCD調達購買管理クラウド「newji」は、調達購買部門で必要なQCD管理全てを備えた、現場特化型兼クラウド型の今世紀最高の購買管理システムとなります。
ユーザー登録
調達購買業務の効率化だけでなく、システムを導入することで、コスト削減や製品・資材のステータス可視化のほか、属人化していた購買情報の共有化による内部不正防止や統制にも役立ちます。
NEWJI DX
製造業に特化したデジタルトランスフォーメーション(DX)の実現を目指す請負開発型のコンサルティングサービスです。AI、iPaaS、および先端の技術を駆使して、製造プロセスの効率化、業務効率化、チームワーク強化、コスト削減、品質向上を実現します。このサービスは、製造業の課題を深く理解し、それに対する最適なデジタルソリューションを提供することで、企業が持続的な成長とイノベーションを達成できるようサポートします。
オンライン講座
製造業、主に購買・調達部門にお勤めの方々に向けた情報を配信しております。
新任の方やベテランの方、管理職を対象とした幅広いコンテンツをご用意しております。
お問い合わせ
コストダウンが利益に直結する術だと理解していても、なかなか前に進めることができない状況。そんな時は、newjiのコストダウン自動化機能で大きく利益貢献しよう!
(Β版非公開)