- お役立ち記事
- Digital Operator Assistance: The Key to Work Efficiency in Manufacturing
Digital Operator Assistance: The Key to Work Efficiency in Manufacturing
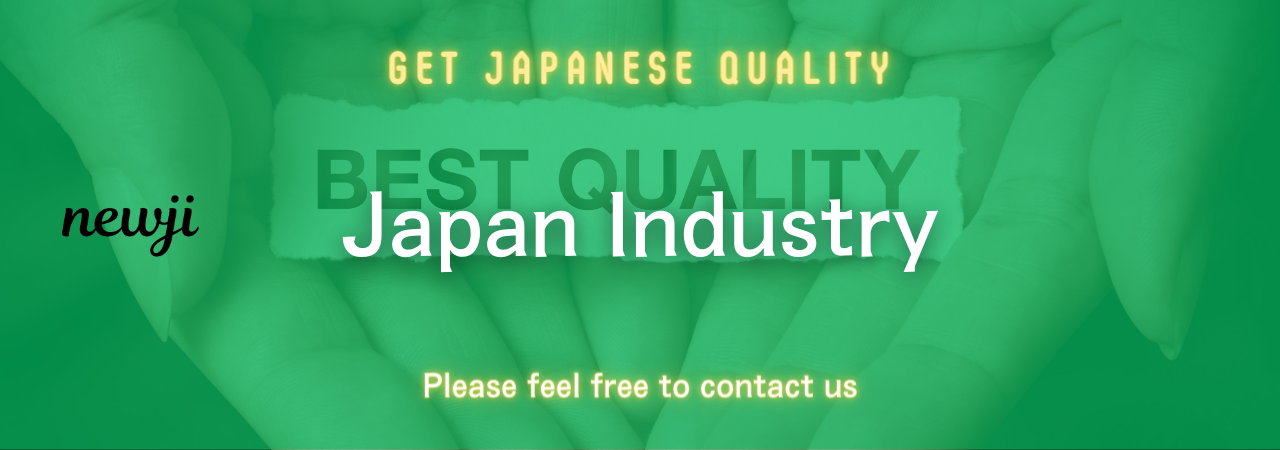
The manufacturing industry has always been at the forefront of technological advancements.
As the sector continuously evolves, it’s becoming increasingly clear that digital operator assistance is essential for boosting work efficiency.
Let’s dive into how digital solutions are reshaping the manufacturing landscape, making life easier for workers and enhancing overall productivity.
目次
What is Digital Operator Assistance?
Digital operator assistance encompasses various technological aids designed to support workers in manufacturing settings.
These digital aids can range from simple wearable devices that provide real-time data, to sophisticated augmented reality (AR) systems that offer step-by-step instructions.
The integration of these tools not only aids operators in performing their tasks more efficiently but also ensures that the operations are carried out accurately and safely.
The Benefits for Manufacturing Efficiency
Real-Time Data and Analytics
One of the significant advantages of digital operator assistance is access to real-time data and analytics.
Operators equipped with digital tools can immediately access the information they need to make informed decisions quickly.
This can range from machine performance data to inventory levels and more.
Instant access to this type of data reduces the chances of errors and delays, thereby speeding up the manufacturing process.
Enhanced Training and Skill Development
Training new employees can be time-consuming and costly.
However, digital operator assistance can facilitate accelerated training.
New workers can receive on-the-job training through interactive AR guides or virtual reality (VR) simulations.
This tech-driven approach allows trainees to learn at their own pace while receiving real-time feedback, making the learning process more efficient and less prone to mistakes.
Improved Safety Measures
Safety is paramount in manufacturing environments.
Digital operator assistance tools can significantly enhance safety measures by providing operators with real-time updates on potential risks.
Wearable sensors can monitor the physical well-being of workers, detecting factors such as fatigue levels or hazardous environmental conditions and alerting them accordingly.
This proactive approach to safety can prevent accidents and ensure a safer working environment.
Seamless Communication
In a manufacturing setting, seamless communication between various departments is crucial.
Digital operator assistance tools facilitate improved communication by integrating different systems and ensuring that all relevant information is shared promptly.
For example, an issue detected on the production line can be instantly communicated to the maintenance team, ensuring a quick resolution.
This reduces downtime and keeps the production line running smoothly.
Technologies Powering Digital Operator Assistance
Augmented Reality (AR)
AR technology superimposes digital information onto the real world.
In manufacturing, this can be particularly useful for providing operators with precise, step-by-step instructions for complex tasks.
AR can also help in troubleshooting machinery by overlaying diagnostics information directly onto the equipment.
Wearable Devices
Wearable devices, such as smart glasses and wearable scanners, provide operators with hands-free access to crucial information.
These devices can display schematics, process instructions, and even alert operators to crucial updates or changes in real-time.
This allows workers to stay focused on their tasks without having to stop and consult a separate screen.
Internet of Things (IoT)
IoT devices collect and share vast amounts of data from machinery and assets in the manufacturing environment.
This data can be analyzed in real-time to provide insights into equipment performance, predict maintenance needs, and optimize operational efficiency.
IoT-integrated tools ensure that operators have the information they need at their fingertips, enabling proactive rather than reactive maintenance.
Implementation Challenges
Integrating digital operator assistance tools into existing manufacturing processes is not without its challenges.
One of the primary obstacles is the initial cost of deployment.
While these tools can result in long-term savings and efficiency gains, the upfront investment can be substantial.
Additionally, operators may require time to adapt to new technologies, necessitating comprehensive training programs.
Another challenge is ensuring compatibility between different digital systems.
Manufacturers must invest in compatible technologies and sometimes custom solutions to address this issue.
Despite these hurdles, the long-term benefits of digital operator assistance far outweigh the challenges, making it a worthwhile investment for forward-thinking manufacturers.
Case Study: Success in Digital Operator Assistance
Consider a case where a medium-sized manufacturing firm implemented AR glasses across its production line.
The firm faced frequent downtimes due to machine malfunctions that required expert intervention.
By integrating AR glasses, operators were able to access step-by-step instructions for common issues.
This enabled them to fix problems themselves without waiting for specialized technicians.
The result was a 40% reduction in downtime, increased productivity, and significant cost savings.
Moreover, operators reported higher job satisfaction due to the decreased frustration of being unable to resolve issues independently.
Future of Digital Operator Assistance in Manufacturing
The future of digital operator assistance in manufacturing looks promising.
As technology continues to advance, we can expect an even more seamless integration of digital tools into manufacturing processes.
Artificial intelligence (AI) and machine learning will likely play a more significant role, offering predictive insights and further automating routine tasks.
With advancements in 5G technology, real-time data transmission will become even more efficient, enhancing communication and operational coordination.
We can also anticipate broader adoption of mixed reality (MR) technologies, combining the best features of AR and VR to create immersive, highly effective training and operational support tools.
In conclusion, digital operator assistance is transforming the manufacturing industry by enhancing efficiency, improving safety, and streamlining communication.
While there are challenges to implementation, the long-term benefits are clear.
As technology evolves, manufacturers that embrace these digital solutions will undoubtedly lead the way in innovation and productivity.
It’s not just about keeping up with the competition; it’s about setting the pace for the future.
資料ダウンロード
QCD調達購買管理クラウド「newji」は、調達購買部門で必要なQCD管理全てを備えた、現場特化型兼クラウド型の今世紀最高の購買管理システムとなります。
ユーザー登録
調達購買業務の効率化だけでなく、システムを導入することで、コスト削減や製品・資材のステータス可視化のほか、属人化していた購買情報の共有化による内部不正防止や統制にも役立ちます。
NEWJI DX
製造業に特化したデジタルトランスフォーメーション(DX)の実現を目指す請負開発型のコンサルティングサービスです。AI、iPaaS、および先端の技術を駆使して、製造プロセスの効率化、業務効率化、チームワーク強化、コスト削減、品質向上を実現します。このサービスは、製造業の課題を深く理解し、それに対する最適なデジタルソリューションを提供することで、企業が持続的な成長とイノベーションを達成できるようサポートします。
オンライン講座
製造業、主に購買・調達部門にお勤めの方々に向けた情報を配信しております。
新任の方やベテランの方、管理職を対象とした幅広いコンテンツをご用意しております。
お問い合わせ
コストダウンが利益に直結する術だと理解していても、なかなか前に進めることができない状況。そんな時は、newjiのコストダウン自動化機能で大きく利益貢献しよう!
(Β版非公開)