- お役立ち記事
- DXing of Gate All-Around Manufacturing Processes is Essential
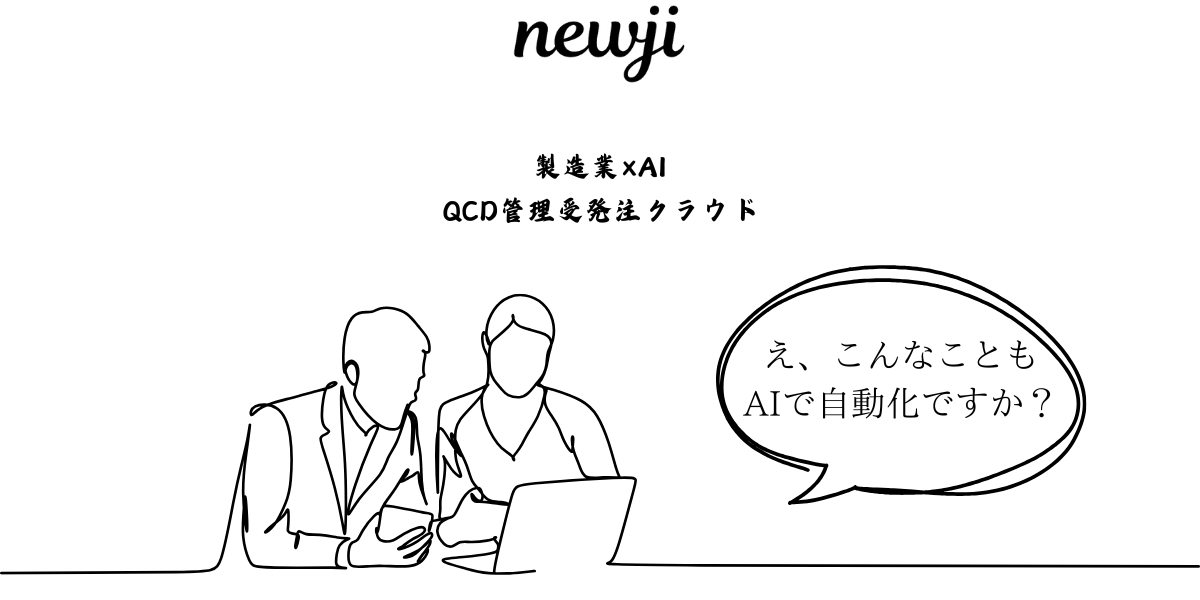
DXing of Gate All-Around Manufacturing Processes is Essential
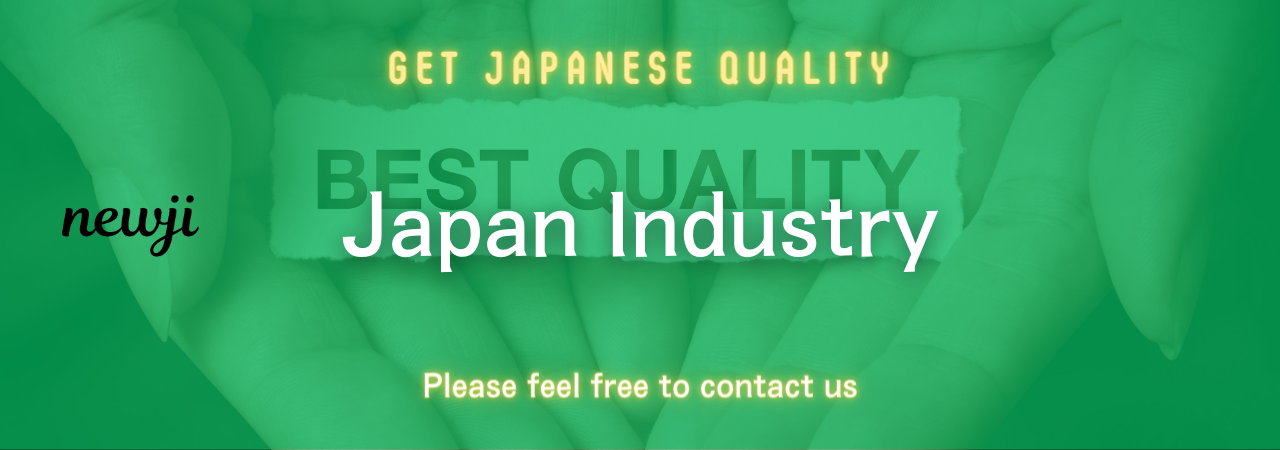
目次
Introduction to DX in Manufacturing
Digital Transformation, often referred to as DX, is revolutionizing industries worldwide.
In the realm of manufacturing, it holds particular significance.
The integration of digital technology into all aspects of the production process is transforming how companies operate, making them more efficient and competitive.
What is DXing in Manufacturing?
DXing, in a manufacturing context, refers to the comprehensive adoption of digital tools and technologies throughout the manufacturing process.
This includes the use of advanced software, automation, data analytics, and the Internet of Things (IoT) to enhance the efficiency, productivity, and overall effectiveness of manufacturing operations.
DXing is not just about adopting new technology.
It’s about fundamentally rethinking and redesigning processes to leverage the full potential of digitalization, enabling smarter and more agile manufacturing operations.
Key Components of DX in Manufacturing
1. Automation
Automation is a cornerstone of DX in manufacturing.
By automating repetitive and time-consuming tasks, manufacturers can significantly increase production speeds and reduce the likelihood of human error.
Robots, automated production lines, and computer-controlled machinery are just a few examples of automation in action.
2. Data Analytics
Data analytics enables manufacturers to gain valuable insights from vast amounts of data generated during the production process.
By analyzing this data, companies can identify trends, pinpoint inefficiencies, and make informed decisions to optimize operations.
Predictive analytics also allow for proactive maintenance, reducing downtime and prolonging the life of machinery.
3. Internet of Things (IoT)
IoT connects machinery, sensors, and devices through the internet, creating a network of interconnected systems.
This connectivity allows for real-time monitoring and control of the manufacturing process.
IoT-enabled devices can communicate with each other, enabling more responsive and adaptive manufacturing environments.
4. Advanced Software Solutions
Advanced software solutions, such as Manufacturing Execution Systems (MES) and Enterprise Resource Planning (ERP) systems, play a crucial role in DXing manufacturing processes.
These systems help integrate and manage various aspects of production, from procurement and inventory management to scheduling and quality control.
They provide a unified platform for managing and optimizing manufacturing operations.
Benefits of DXing Manufacturing Processes
1. Improved Efficiency
DXing streamlines manufacturing processes, reducing waste and optimizing resource utilization.
Automation and data analytics enable faster production cycles and minimize downtime, leading to increased efficiency and output.
2. Enhanced Quality Control
Digital technologies enable real-time monitoring and quality control mechanisms.
Sensors and IoT devices can detect defects and inconsistencies early in the production process, reducing the likelihood of defective products reaching the market.
This leads to higher customer satisfaction and reduced costs associated with rework and returns.
3. Increased Flexibility
DXing allows manufacturers to be more responsive to changes in demand and market conditions.
Advanced software solutions and connected systems enable agile production processes, allowing for rapid adjustments to production schedules and product specifications.
This flexibility is crucial in today’s fast-paced and ever-changing market landscape.
4. Cost Savings
While the initial investment in digital technologies can be substantial, the long-term cost savings are significant.
Increased efficiency, reduced downtime, and optimized resource utilization lead to lower operating costs.
Additionally, predictive maintenance reduces the need for costly repairs and replacements.
Challenges in Implementing DX in Manufacturing
1. High Initial Costs
The adoption of digital technologies requires significant upfront investment.
This can be a barrier for small and medium-sized manufacturers with limited budgets.
However, the long-term benefits often justify the initial costs.
2. Workforce Training
Digital transformation requires a workforce that is skilled in new technologies and processes.
Training and upskilling employees can be time-consuming and costly.
Manufacturers must invest in comprehensive training programs to ensure their workforce can effectively operate and manage new digital systems.
3. Data Security
The increased connectivity and reliance on digital systems raise concerns about data security.
Manufacturers must implement robust cybersecurity measures to protect sensitive data and prevent unauthorized access to their systems.
This includes regular security assessments and updates to safeguard against emerging threats.
4. Integration with Legacy Systems
Many manufacturers still rely on legacy systems that may not be compatible with modern digital technologies.
Integrating new digital systems with existing infrastructure can be challenging and may require significant modifications or replacements.
Careful planning and phased implementation can help mitigate these challenges.
Future Trends in DX Manufacturing
1. Artificial Intelligence (AI)
AI is set to play a significant role in the future of manufacturing.
AI-driven systems can analyze vast amounts of data, identify patterns, and make decisions in real-time.
This will further enhance efficiency, quality control, and predictive maintenance.
2. Augmented Reality (AR) and Virtual Reality (VR)
AR and VR technologies are increasingly being used for training, maintenance, and design processes.
These immersive technologies provide a realistic and interactive environment, improving the accuracy and efficiency of various manufacturing tasks.
3. Blockchain
Blockchain technology offers a secure and transparent way to manage supply chains and track the provenance of products.
This can enhance traceability, reduce fraud, and improve trust among supply chain partners.
4. 5G Connectivity
The advent of 5G technology will provide faster and more reliable connectivity, enabling seamless communication between IoT devices and systems.
This will further enhance real-time monitoring, control, and automation capabilities in manufacturing.
Conclusion
DXing of gate all-around manufacturing processes is not just a trend; it’s a necessity for staying competitive in today’s rapidly evolving market.
By embracing digital technologies, manufacturers can unlock new levels of efficiency, quality, and flexibility.
While the journey to complete digital transformation can be challenging, the rewards are significant.
Investing in DX today will prepare manufacturers for the future, ensuring they remain at the forefront of innovation and industry leadership.
資料ダウンロード
QCD調達購買管理クラウド「newji」は、調達購買部門で必要なQCD管理全てを備えた、現場特化型兼クラウド型の今世紀最高の購買管理システムとなります。
ユーザー登録
調達購買業務の効率化だけでなく、システムを導入することで、コスト削減や製品・資材のステータス可視化のほか、属人化していた購買情報の共有化による内部不正防止や統制にも役立ちます。
NEWJI DX
製造業に特化したデジタルトランスフォーメーション(DX)の実現を目指す請負開発型のコンサルティングサービスです。AI、iPaaS、および先端の技術を駆使して、製造プロセスの効率化、業務効率化、チームワーク強化、コスト削減、品質向上を実現します。このサービスは、製造業の課題を深く理解し、それに対する最適なデジタルソリューションを提供することで、企業が持続的な成長とイノベーションを達成できるようサポートします。
オンライン講座
製造業、主に購買・調達部門にお勤めの方々に向けた情報を配信しております。
新任の方やベテランの方、管理職を対象とした幅広いコンテンツをご用意しております。
お問い合わせ
コストダウンが利益に直結する術だと理解していても、なかなか前に進めることができない状況。そんな時は、newjiのコストダウン自動化機能で大きく利益貢献しよう!
(Β版非公開)