- お役立ち記事
- DXing the Production Scheduler to Quickly Respond to Demand Fluctuations
DXing the Production Scheduler to Quickly Respond to Demand Fluctuations
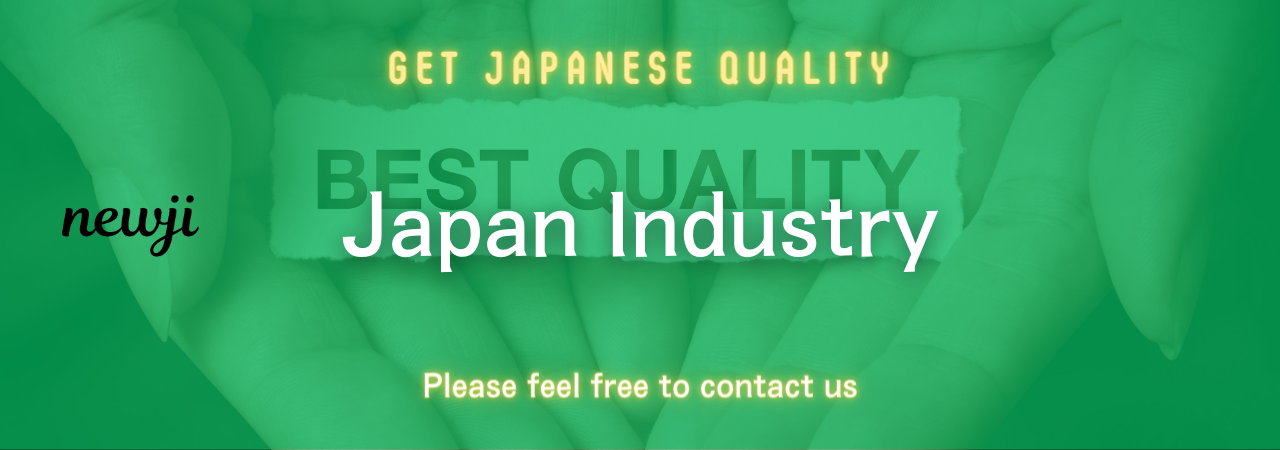
In today’s fast-paced business environment, responding to demand fluctuations is crucial for maintaining customer satisfaction and operational efficiency.
Implementing a digital transformation (DX) for your production scheduler can play a significant role in achieving these objectives.
DXing the production scheduler involves leveraging advanced technologies, such as artificial intelligence (AI) and machine learning (ML), to optimize scheduling and improve responsiveness.
In doing so, companies can enhance their ability to meet fluctuating demands while minimizing waste and maximizing productivity.
目次
Understanding Demand Fluctuations
What Causes Demand Fluctuations?
Demand fluctuations can stem from various factors, including seasonal changes, economic conditions, customer preferences, and competitive actions.
For instance, retailers often experience higher demand during the holiday season due to increased consumer spending.
Similarly, economic downturns can lead to reduced demand as customers become more cautious with their purchases.
Understanding the root causes of these fluctuations is essential for developing effective strategies to manage them.
By analyzing historical data and identifying patterns, businesses can better anticipate changes in demand and adjust their production schedules accordingly.
The Impact of Demand Fluctuations on Production
Demand fluctuations can create significant challenges for production scheduling.
When demand spikes, companies may struggle to ramp up production quickly enough to meet customer needs, resulting in stockouts and lost sales.
Conversely, when demand drops, businesses may be left with excess inventory, leading to increased holding costs and potential obsolescence.
In both scenarios, inefficient production scheduling can negatively impact profitability and customer satisfaction.
Therefore, it is critical to develop a flexible and responsive scheduling system that can adapt to changing demand conditions.
Benefits of DXing Your Production Scheduler
Increased Flexibility and Responsiveness
One of the primary benefits of DXing your production scheduler is increased flexibility and responsiveness.
By leveraging AI and ML, companies can quickly adjust production schedules based on real-time demand data.
This enables businesses to respond more effectively to fluctuations, reducing the risk of stockouts and excess inventory.
For example, an AI-powered scheduler can analyze real-time sales data and automatically adjust production plans to align with current demand levels.
As a result, companies can better meet customer needs while minimizing waste and optimizing resource utilization.
Improved Forecast Accuracy
Another advantage of DXing your production scheduler is improved forecast accuracy.
Traditional forecasting methods often rely on historical data and manual input, which can be prone to errors and inaccuracies.
In contrast, AI and ML algorithms can analyze vast amounts of data from various sources, including social media, market trends, and economic indicators.
This enables businesses to generate more accurate and reliable demand forecasts, which can inform production scheduling decisions.
By enhancing forecast accuracy, companies can better anticipate demand fluctuations and adjust their production schedules accordingly, leading to improved operational efficiency and customer satisfaction.
Enhanced Collaboration and Communication
DXing your production scheduler can also improve collaboration and communication across your organization.
Advanced scheduling systems can integrate with other business functions, such as sales, marketing, and supply chain management, providing a centralized platform for information sharing and decision-making.
For instance, sales and marketing teams can input promotional plans into the scheduling system, allowing production managers to adjust schedules in anticipation of increased demand.
Similarly, supply chain teams can provide real-time updates on material availability, enabling production managers to make informed scheduling decisions.
By fostering better collaboration and communication, businesses can create a more cohesive and agile organization capable of responding to demand fluctuations more effectively.
Steps to DX Your Production Scheduler
1. Assess Your Current Scheduling System
The first step in DXing your production scheduler is to assess your current scheduling system.
Identify any limitations or inefficiencies and consider how digital technologies can address these challenges.
For instance, if your current system relies heavily on manual input and spreadsheets, consider implementing an advanced scheduling software that automates data collection and analysis.
This can help reduce errors and improve the accuracy of your production schedules.
2. Choose the Right Technology
Next, choose the right technology to support your DX initiatives.
There are various AI and ML-based scheduling solutions available, each with its own features and capabilities.
Consider factors such as ease of use, scalability, and integration with your existing systems when selecting a solution.
Additionally, involve key stakeholders in the decision-making process to ensure that the chosen technology meets the needs of your organization.
3. Implement and Integrate the Technology
Once you have selected the appropriate technology, the next step is to implement and integrate it into your existing operations.
This may involve training your staff on how to use the new system and ensuring that it seamlessly integrates with other business functions.
To facilitate a smooth implementation, consider working with a technology partner who can provide support and guidance throughout the process.
This can help minimize disruptions and ensure that your organization fully realizes the benefits of the new scheduling system.
4. Continuously Monitor and Optimize
Finally, continuously monitor and optimize your production scheduler to ensure that it remains effective in responding to demand fluctuations.
Regularly review performance metrics and gather feedback from key stakeholders to identify any areas for improvement.
Additionally, consider leveraging advanced analytics and reporting tools to gain deeper insights into your scheduling processes.
This can help you identify trends and patterns, enabling you to make more informed scheduling decisions and further enhance your responsiveness to demand fluctuations.
In conclusion, DXing your production scheduler can provide significant benefits in terms of flexibility, responsiveness, forecast accuracy, and collaboration.
By leveraging advanced technologies such as AI and ML, businesses can better manage demand fluctuations and optimize their production processes.
By following the steps outlined above, companies can successfully implement a digital transformation for their production scheduler and gain a competitive edge in today’s dynamic business environment.
資料ダウンロード
QCD調達購買管理クラウド「newji」は、調達購買部門で必要なQCD管理全てを備えた、現場特化型兼クラウド型の今世紀最高の購買管理システムとなります。
ユーザー登録
調達購買業務の効率化だけでなく、システムを導入することで、コスト削減や製品・資材のステータス可視化のほか、属人化していた購買情報の共有化による内部不正防止や統制にも役立ちます。
NEWJI DX
製造業に特化したデジタルトランスフォーメーション(DX)の実現を目指す請負開発型のコンサルティングサービスです。AI、iPaaS、および先端の技術を駆使して、製造プロセスの効率化、業務効率化、チームワーク強化、コスト削減、品質向上を実現します。このサービスは、製造業の課題を深く理解し、それに対する最適なデジタルソリューションを提供することで、企業が持続的な成長とイノベーションを達成できるようサポートします。
オンライン講座
製造業、主に購買・調達部門にお勤めの方々に向けた情報を配信しております。
新任の方やベテランの方、管理職を対象とした幅広いコンテンツをご用意しております。
お問い合わせ
コストダウンが利益に直結する術だと理解していても、なかなか前に進めることができない状況。そんな時は、newjiのコストダウン自動化機能で大きく利益貢献しよう!
(Β版非公開)