- お役立ち記事
- Effective 5 Whys Analysis Methods Required for Quality Control Departments
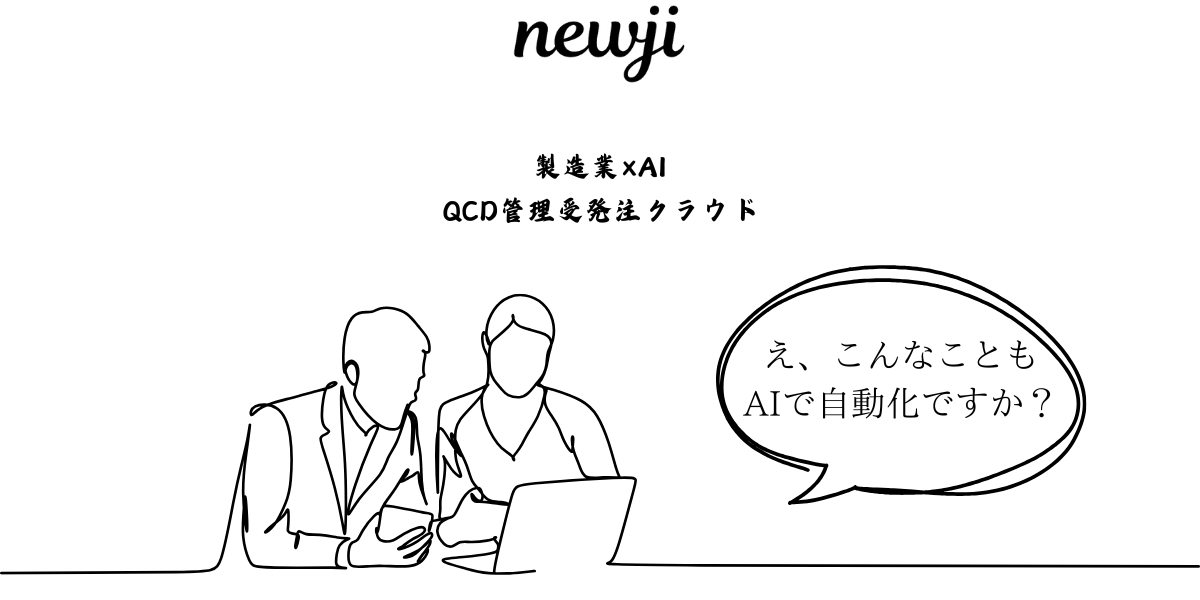
Effective 5 Whys Analysis Methods Required for Quality Control Departments
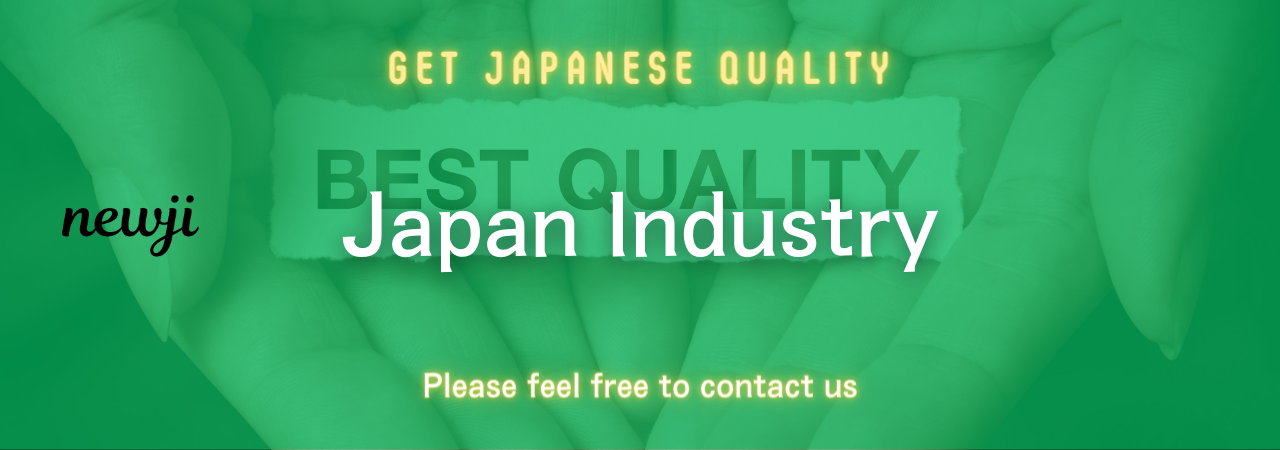
目次
What is 5 Whys Analysis?
5 Whys Analysis is a problem-solving technique used to explore the cause-and-effect relationships underlying a particular problem.
It involves asking the question “Why?” five times, or as many times as needed, to get to the root cause of the problem.
This method helps to identify the core issue rather than addressing only the symptoms.
It is a fundamental tool used in quality control departments to ensure processes are running smoothly and efficiently.
By digging deeper into the problem, teams can implement effective solutions that prevent recurrence.
The Importance of 5 Whys Analysis in Quality Control
Quality control departments bear the responsibility of maintaining standards and ensuring products meet customer expectations.
Using the 5 Whys Analysis allows these teams to systematically find out why defects arise and fix them at the source.
This prevents issues from resurfacing and ensures the quality remains consistent.
Moreover, it fosters a culture of continuous improvement where feedback loops are established, leading to better processes.
How to Conduct a 5 Whys Analysis
Conducting a 5 Whys Analysis requires a structured approach to yield beneficial results.
Here’s a step-by-step guide to implementing the method:
1. Assemble a Team
Gather a team with diverse knowledge of the process or system experiencing the problem.
Different perspectives can provide unique insights into why the issue occurred.
2. Define the Problem
Clearly articulate the problem statement.
The more precise the problem definition, the easier it becomes to drill down to the root cause.
Avoid being vague; specify where, when, and how the issue arises.
3. Ask “Why?”
Begin asking “Why?” to the first problem statement.
Investigate the answers fully before proceeding to the next “Why?”
Continue this process until you identify the underlying root cause.
It may take more or fewer than five iterations depending on the situation.
4. Document the Process
Record every question and answer as you progress through the analysis.
This documentation helps in creating an actionable plan and serves as a reference for future problem-solving efforts.
5. Implement Solutions
Once the root cause is determined, brainstorm possible solutions as a team.
Evaluate and implement the most effective one.
Ensure the team monitors the implementation to verify its effectiveness over time.
Common Pitfalls and How to Avoid Them
Despite the straightforward nature of the 5 Whys Analysis, there are some common pitfalls that can undermine its success.
Assuming Answers
Avoid jumping to conclusions or assuming answers when conducting the analysis.
This may lead to incorrect root causes and ineffective solutions.
Take the time to gather accurate data and thoroughly investigate each “Why.”
Lack of Collaboration
Conducting the analysis in isolation can limit the variety of insights and solutions.
Encourage teamwork and open discussions to gain comprehensive understanding and solutions.
Stopping Too Soon
Stopping the analysis after reaching a superficial understanding can lead to incomplete solutions.
Ensure the “Why?” questions continue until the true root cause is identified.
Over-Complicating the Process
Keep the analysis simple and focused.
Over-complicating can inhibit problem-solving, leading to confusion and missed insights.
Stick to the direct approach of asking “Why?” systematically.
Benefits of 5 Whys in Quality Control
Implementing 5 Whys Analysis within quality control departments offers multiple advantages.
Improved Problem Solving
It trains teams to think critically and systematically about problems, enhancing their problem-solving abilities.
They become adept at identifying underlying causes rather than just treating surface symptoms.
Cost-Effective Solutions
By addressing the root cause, companies can prevent costly recurrences and wastage.
This leads to savings in resources and increased profitability.
Enhanced Communication
The collaborative nature of the 5 Whys fosters better communication across departments.
Teams learn to work together, share insights, and respect each other’s perspectives.
Supports Continuous Improvement
As teams regularly engage in this analysis, they create a culture of continuous improvement.
Feedback loops are established, helping the organization strive for excellence.
Conclusion
5 Whys Analysis is a powerful tool for quality control departments aiming to maintain high standards and solve problems effectively.
By systematically digging into problems and identifying root causes, teams can implement lasting solutions and prevent recurrence.
When conducted diligently with team collaboration and accurate data, it enhances problem-solving skills and supports continuous process improvement.
Whether dealing with manufacturing defects or service delivery issues, 5 Whys Analysis proves to be invaluable in maintaining quality and consistency.
資料ダウンロード
QCD調達購買管理クラウド「newji」は、調達購買部門で必要なQCD管理全てを備えた、現場特化型兼クラウド型の今世紀最高の購買管理システムとなります。
ユーザー登録
調達購買業務の効率化だけでなく、システムを導入することで、コスト削減や製品・資材のステータス可視化のほか、属人化していた購買情報の共有化による内部不正防止や統制にも役立ちます。
NEWJI DX
製造業に特化したデジタルトランスフォーメーション(DX)の実現を目指す請負開発型のコンサルティングサービスです。AI、iPaaS、および先端の技術を駆使して、製造プロセスの効率化、業務効率化、チームワーク強化、コスト削減、品質向上を実現します。このサービスは、製造業の課題を深く理解し、それに対する最適なデジタルソリューションを提供することで、企業が持続的な成長とイノベーションを達成できるようサポートします。
オンライン講座
製造業、主に購買・調達部門にお勤めの方々に向けた情報を配信しております。
新任の方やベテランの方、管理職を対象とした幅広いコンテンツをご用意しております。
お問い合わせ
コストダウンが利益に直結する術だと理解していても、なかなか前に進めることができない状況。そんな時は、newjiのコストダウン自動化機能で大きく利益貢献しよう!
(Β版非公開)