- お役立ち記事
- Effective Operation of Clean Room Technology
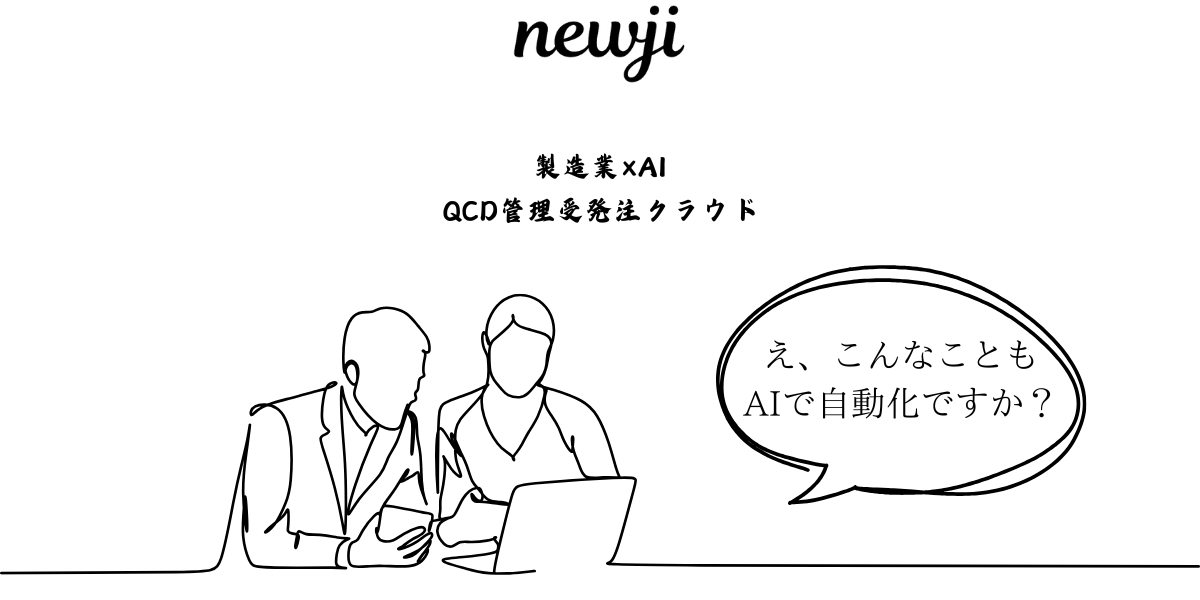
Effective Operation of Clean Room Technology
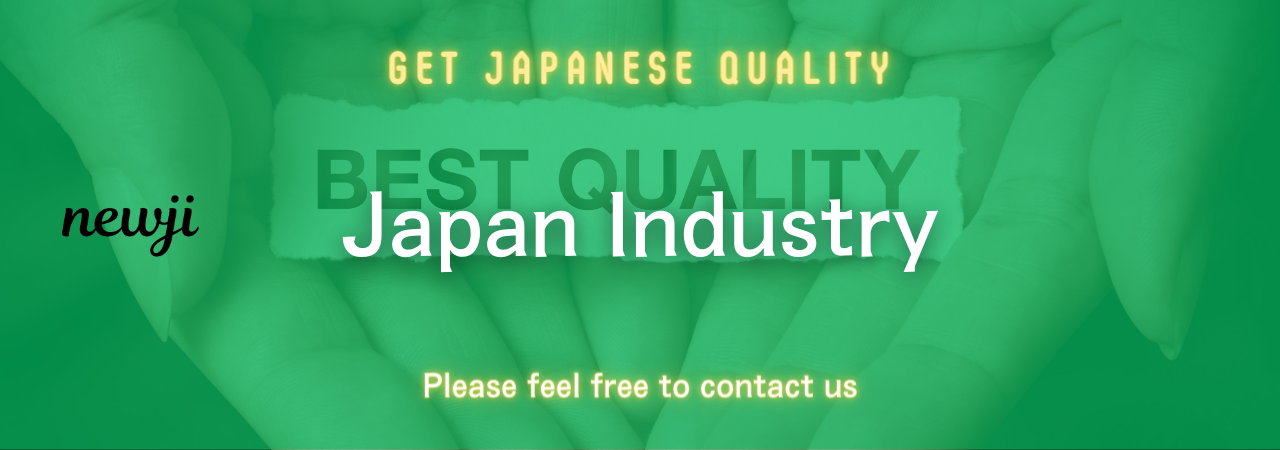
目次
Understanding Clean Room Technology
Clean room technology is crucial in various industries to maintain a controlled environment that minimizes pollutants like dust, airborne microbes, aerosol particles, and chemical vapors.
Such spaces are essential in fields like pharmaceuticals, biotechnology, electronics, and aerospace, where even the tiniest contamination can lead to significant issues.
The fundamental concept of a clean room is to control the conditions such as temperature, humidity, and especially the presence of particles in the air.
These conditions are regulated depending on the specific requirements of the industry or process conducted within the clean room.
The Importance of Clean Room Operation
Operating a clean room effectively is not just about maintaining cleanliness but also about ensuring that the parameters for contamination and environmental conditions are strictly regulated.
In industries like pharmaceuticals, even a minor contamination can lead to compromised products, endangering public health and causing significant financial losses.
In electronic manufacturing, dust particles can ruin semiconductor wafers leading to reduced yields and increased costs.
Therefore, understanding and implementing effective clean room operations are vital to the success and safety of these products.
Essential Components of Clean Room Technology
Air Filtration Systems
One of the most critical components of a clean room is its air filtration system.
High-Efficiency Particulate Air (HEPA) and Ultra-Low Penetration Air (ULPA) filters are often used to remove particles from the air.
These advanced filtration systems can remove up to 99.999% of particles, ensuring the air quality meets the stringent standards of the specific Class of clean room.
Environmental Control
Maintaining stable environmental conditions such as temperature and humidity is essential in a clean room.
Fluctuations can cause condensation, static electricity, or unwanted chemical reactions, all of which might compromise the clean room’s integrity.
Advanced HVAC systems are used to maintain these environments constant, often utilizing sensors and automated controls to correct any deviations quickly.
Surface Cleaning and Maintenance
Surfaces within a clean room must be regularly cleaned to prevent the build-up of particles and contaminants.
Using appropriate cleaning agents and gear, such as non-shedding wipes and particle-free solutions, is imperative.
Moreover, a routine maintenance schedule assists in preventing the potential for pollutants accumulating inadvertently.
Personnel Protocols
Operators themselves can be significant sources of contamination within clean rooms.
This is why strict personnel protocols, including gowning procedures and restricted entry, are fundamental.
Here, specialized clothing, such as coveralls, gloves, masks, and shoe covers, are utilized, and personnel must follow precise guidelines to minimize contamination risks.
Five Tips for Effective Clean Room Operation
1. Implement a Comprehensive Training Program
Effective operation starts with understanding.
Ensure that all personnel, from operators to maintenance staff, receive comprehensive training on clean room protocols and contamination prevention.
Regular refresher courses can keep staff updated with the latest standards and technologies.
2. Conduct Regular Particle Monitoring
It’s essential to continuously monitor particle levels within the clean room.
By implementing real-time particle counters and set threshold alerts, you can promptly respond to potential contamination issues before they escalate.
3. Maintain Equipment and Systems
All equipment, including HVAC systems and filtration units, should be subject to regular inspections and maintenance.
Routine checks can prevent component failures and ensure all systems operate optimally.
Timely replacement of HEPA/ULPA filters and other crucial elements is a necessary practice.
4. Establish a Robust Cleaning Schedule
Create and adhere to a strict cleaning schedule.
Define specific roles and responsibilities and utilize appropriate cleaning materials.
This schedule should be structured to minimize disruption while ensuring thorough decontamination of the area.
5. Control Access to the Clean Room
Limit access to the clean room to trained personnel only, and use controlled entry systems to monitor and log entries and exits.
Each time someone enters, they introduce potential contaminants.
Thus, limiting unnecessary entry, even with proper gowning, greatly enhances clean room efficacy.
The Future of Clean Room Technology
As technology continues to advance, so too does clean room technology, becoming more sophisticated with enhanced monitoring and control capabilities.
Improved filtration methods are emerging, promising even finer particulate control, which is critical in ultra-sensitive environments like semiconductor manufacturing.
Developments in automation and AI-driven solutions present opportunities for more streamlined and error-free operation.
Robotic systems can minimize human interference, reducing contamination risks associated with human operators.
Furthermore, as industries evolve, the need for clean room compliance standards also changes, requiring ongoing adaptation to newer guidelines and industry needs.
Conclusion
In summary, effective operation of clean room technology is a comprehensive process involving multiple facets, from air quality to personnel management.
By implementing best practices and keeping abreast of technological advancements, industries can continue to leverage these environments to produce high-quality and safe products.
As clean room technology continues to evolve, its applications across various sectors become even more critical.
This highlights the necessity for continuous improvement and stringent adherence to operational protocols and standards.
資料ダウンロード
QCD調達購買管理クラウド「newji」は、調達購買部門で必要なQCD管理全てを備えた、現場特化型兼クラウド型の今世紀最高の購買管理システムとなります。
ユーザー登録
調達購買業務の効率化だけでなく、システムを導入することで、コスト削減や製品・資材のステータス可視化のほか、属人化していた購買情報の共有化による内部不正防止や統制にも役立ちます。
NEWJI DX
製造業に特化したデジタルトランスフォーメーション(DX)の実現を目指す請負開発型のコンサルティングサービスです。AI、iPaaS、および先端の技術を駆使して、製造プロセスの効率化、業務効率化、チームワーク強化、コスト削減、品質向上を実現します。このサービスは、製造業の課題を深く理解し、それに対する最適なデジタルソリューションを提供することで、企業が持続的な成長とイノベーションを達成できるようサポートします。
オンライン講座
製造業、主に購買・調達部門にお勤めの方々に向けた情報を配信しております。
新任の方やベテランの方、管理職を対象とした幅広いコンテンツをご用意しております。
お問い合わせ
コストダウンが利益に直結する術だと理解していても、なかなか前に進めることができない状況。そんな時は、newjiのコストダウン自動化機能で大きく利益貢献しよう!
(Β版非公開)