- お役立ち記事
- Efficient Operation of Injection Molding Machines and Optimization of Molding Cycles
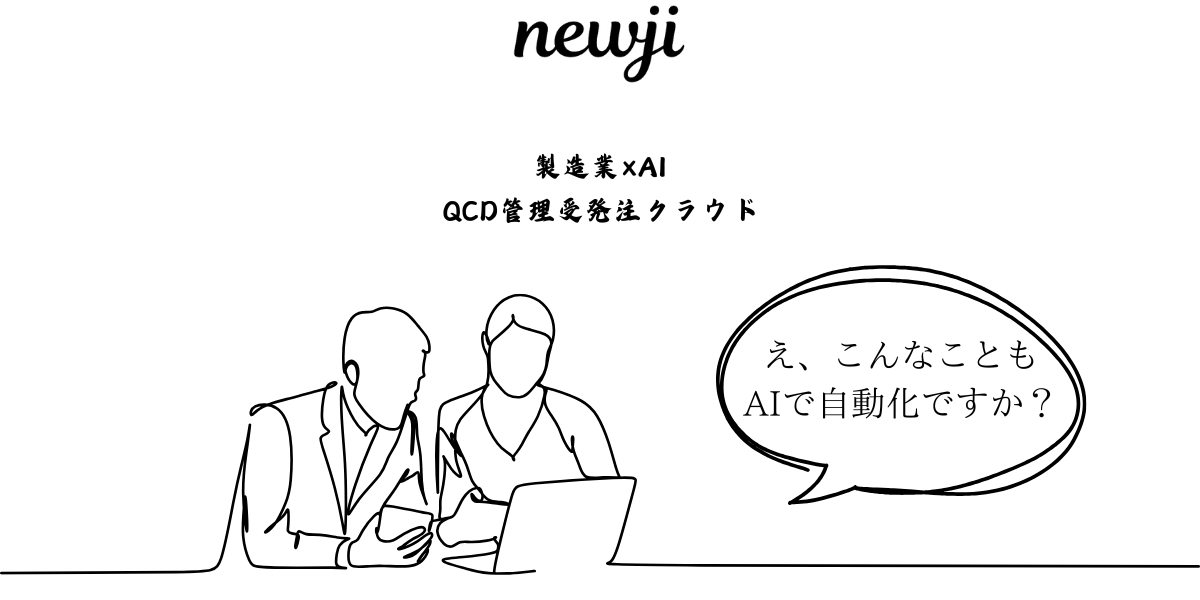
Efficient Operation of Injection Molding Machines and Optimization of Molding Cycles
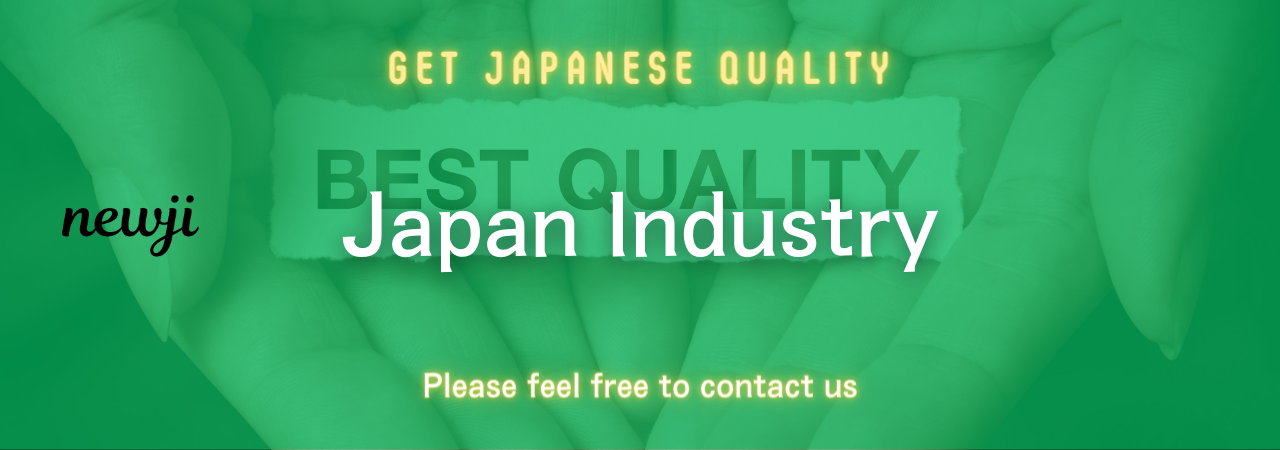
目次
Understanding Injection Molding Machines
Injection molding is a popular manufacturing process used to produce parts by injecting molten material into a mold.
The process is efficient, versatile, and used in various industries, including automotive, electronics, and consumer goods.
The effectiveness of injection molding machines plays a crucial role in determining the quality and productivity of the manufacturing process.
Injection molding machines consist of several key components, including the injection unit, clamping unit, and the mold itself.
These machines work by melting plastic pellets and then injecting the molten plastic into a mold cavity.
Once the plastic cools and solidifies, it takes the shape of the mold, resulting in a finished product.
Achieving efficient operation of these machines requires a thorough understanding of these components and how they interact.
The Significance of Molding Cycles
Molding cycles refer to the complete sequence of operations required to produce a molded part.
This includes the time taken to inject the plastic, cool it, and eject the finished product from the mold.
Molding cycles are a significant determinant of production speed and efficiency.
By optimizing these cycles, manufacturers can increase productivity and reduce costs.
A typical molding cycle consists of several stages: injection, cooling, and ejection.
Each stage must be carefully monitored and adjusted to ensure efficient operation.
For example, reducing the cooling time can significantly shorten the molding cycle, but it must be done without compromising the quality of the parts.
Strategies for Optimizing Molding Cycles
1. Proper Machine Selection
Selecting the right injection molding machine is the first step toward optimizing molding cycles.
Consideration must be given to the machine’s specifications, such as tonnage, shot size, and speed.
A machine that is well-matched to the production needs can operate more efficiently, reducing cycle times and improving overall productivity.
2. Regular Maintenance and Calibration
Regular maintenance and calibration of injection molding machines ensure that they operate at peak efficiency.
It helps prevent unexpected breakdowns and maintains the precision of the production process.
Routine checks should include inspecting and calibrating the injection and clamping units, as well as ensuring that the mold is in good condition.
3. Optimizing Cooling Time
Cooling is one of the longest phases of the molding cycle.
Optimizing cooling time without affecting part quality can significantly shorten cycle times.
This can be achieved through the use of efficient cooling systems, such as conformal cooling channels, which provide more uniform cooling.
4. Cycle Time Reduction
Reducing cycle time is a key objective in optimizing injection molding processes.
This involves analyzing each stage of the cycle to identify areas for improvement.
Implementing process innovations or technological advancements can help achieve faster cycle times.
Automation also plays a crucial role in cycle time reduction by minimizing manual intervention and ensuring consistent quality.
5. Training and Skill Development
Skilled operators play a significant role in optimizing molding cycles.
Proper training ensures that operators understand the nuances of machine operation and cycle optimization.
Regular workshops and training sessions can enhance operators’ skills and keep them updated with the latest industry practices.
Benefits of Efficient Injection Molding Operation
Efficient operation of injection molding machines has several benefits for manufacturers.
Primarily, it increases production efficiency, allowing for higher output in less time.
This improved productivity translates into cost savings and can result in lower lead times for product delivery.
Moreover, efficient operations reduce the wear and tear of machines, extending their lifespan and reliability.
It also minimizes energy consumption, contributing to more sustainable and environmentally friendly manufacturing processes.
Challenges and Future Directions
While optimizing injection molding cycles offers significant benefits, it also presents challenges.
Balancing speed with quality can be difficult, and improper optimization can lead to defects and scrap.
Additionally, as technology evolves, manufacturers must continually adapt and invest in new equipment and training to stay competitive.
Looking forward, advancements in machine learning and automation provide exciting opportunities for further optimization.
Smart injection molding machines with integrated sensors and data analytics can offer real-time insights, leading to even more precise and efficient operations.
Leveraging these technologies can position manufacturers at the forefront of efficiency and innovation in the industry.
In conclusion, efficient operation of injection molding machines and the optimization of molding cycles are crucial for improving productivity and reducing costs in manufacturing.
By selecting the right machinery, maintaining them properly, optimizing cycle components, and investing in training and automation, manufacturers can achieve these goals while ensuring high-quality products.
Embracing future technological advancements will further enhance these operations, offering significant advantages in a competitive market.
資料ダウンロード
QCD調達購買管理クラウド「newji」は、調達購買部門で必要なQCD管理全てを備えた、現場特化型兼クラウド型の今世紀最高の購買管理システムとなります。
ユーザー登録
調達購買業務の効率化だけでなく、システムを導入することで、コスト削減や製品・資材のステータス可視化のほか、属人化していた購買情報の共有化による内部不正防止や統制にも役立ちます。
NEWJI DX
製造業に特化したデジタルトランスフォーメーション(DX)の実現を目指す請負開発型のコンサルティングサービスです。AI、iPaaS、および先端の技術を駆使して、製造プロセスの効率化、業務効率化、チームワーク強化、コスト削減、品質向上を実現します。このサービスは、製造業の課題を深く理解し、それに対する最適なデジタルソリューションを提供することで、企業が持続的な成長とイノベーションを達成できるようサポートします。
オンライン講座
製造業、主に購買・調達部門にお勤めの方々に向けた情報を配信しております。
新任の方やベテランの方、管理職を対象とした幅広いコンテンツをご用意しております。
お問い合わせ
コストダウンが利益に直結する術だと理解していても、なかなか前に進めることができない状況。そんな時は、newjiのコストダウン自動化機能で大きく利益貢献しよう!
(Β版非公開)