- お役立ち記事
- Ensuring Manufacturing Quality by Adhering to GMP (Good Manufacturing Practice)
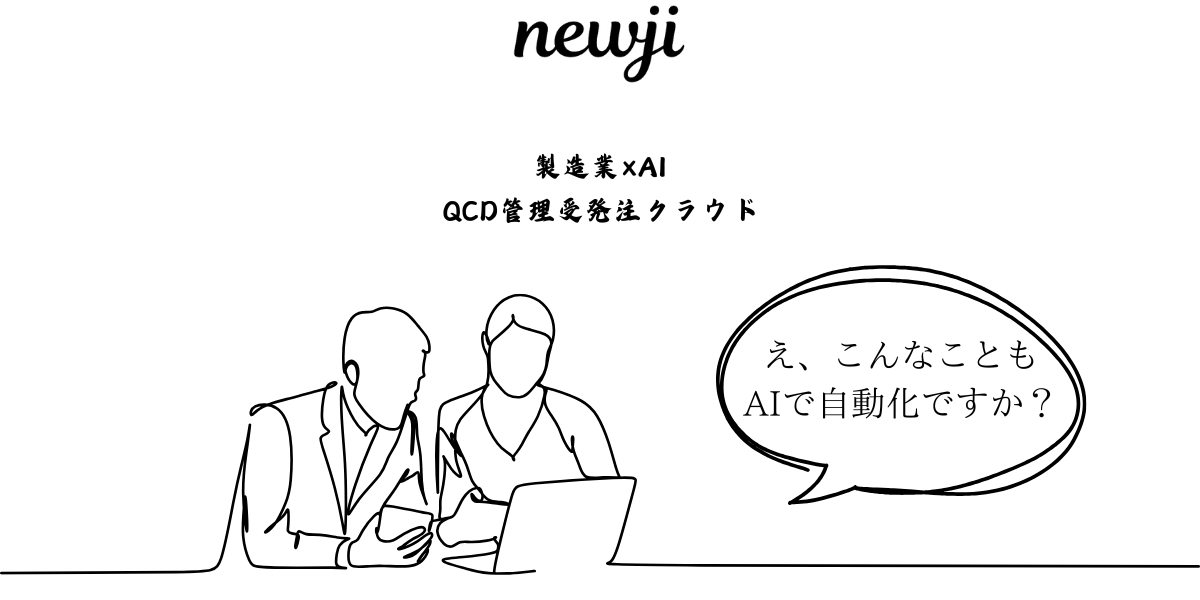
Ensuring Manufacturing Quality by Adhering to GMP (Good Manufacturing Practice)
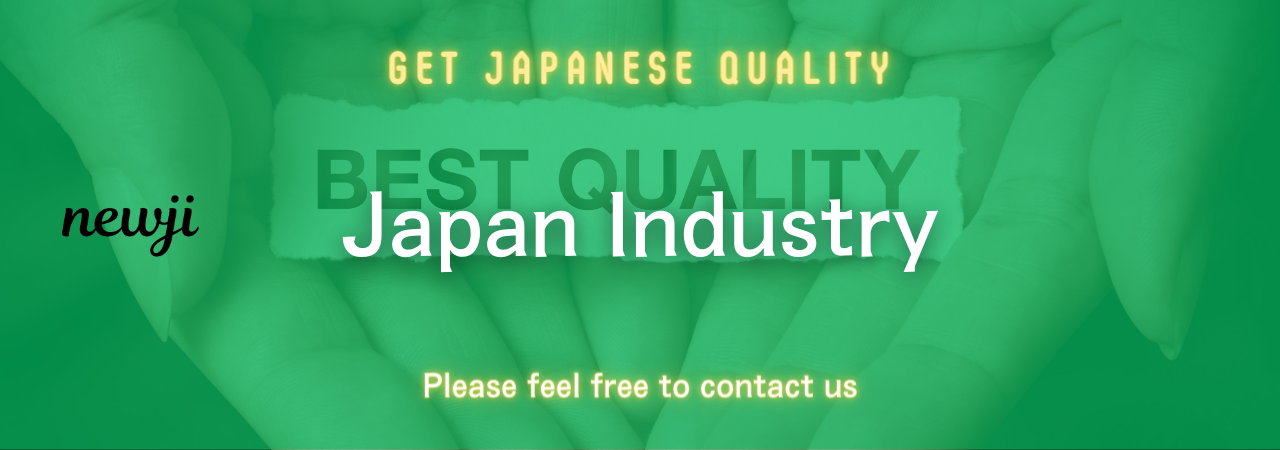
Good Manufacturing Practice, commonly known as GMP, is a vital component in the manufacturing sector.
It is particularly significant in industries such as pharmaceuticals, food production, and cosmetics.
GMP ensures that products are consistently produced and controlled according to quality standards.
In this article, we will explore why adhering to GMP is crucial in ensuring manufacturing quality and how it can be implemented effectively.
目次
What is Good Manufacturing Practice (GMP)?
Good Manufacturing Practice is a system that pharmaceutical and food manufacturers must follow to ensure products are safe and meet quality standards.
GMP guidelines are regulations enforced by regulatory agencies like the FDA in the United States and the EMA in Europe.
These guidelines provide minimum requirements that a manufacturer must meet to ensure their products are of high quality, safe, and effective for their intended use.
Why GMP is Important
Adhering to GMP is important for several reasons.
First and foremost, it ensures product safety.
Products manufactured under GMP guidelines are less likely to be contaminated, mislabeled, or otherwise compromised.
This is crucial for industries like pharmaceuticals and food, where a single error can have severe consequences.
Secondly, GMP compliance helps in maintaining product consistency.
When manufacturers follow standard operating procedures and guidelines, it ensures that every batch of product is the same as the previous one.
This consistency is important for both consumer trust and regulatory compliance.
Regulatory Compliance
One of the main reasons for adhering to GMP is regulatory compliance.
GMP guidelines are mandatory in many countries.
Non-compliance can result in severe penalties, including product recalls, fines, and even plant shutdowns.
By adhering to GMP, companies can avoid these repercussions and ensure their operations run smoothly.
Core Principles of GMP
The core principles of GMP can be divided into several key areas, each focused on ensuring product quality and safety.
Quality Management
Quality management is the cornerstone of GMP.
It involves setting up policies, processes, and procedures to ensure products meet quality standards.
This includes everything from the selection of raw materials to the final inspection of the finished product.
A strong quality management system can help manufacturers identify and rectify issues before they become significant problems.
Sanitation and Hygiene
Sanitation and hygiene are crucial in preventing contamination.
This involves maintaining clean facilities, equipment, and personnel.
Workers must follow strict hygiene practices, and the facility should be designed to minimize contamination risks.
Building and Facilities
The facilities where products are manufactured should be designed and maintained to ensure a clean and controlled environment.
This includes everything from the layout of the facility to the materials used in construction.
Proper maintenance and regular inspections are also vital to ensure the facilities remain in good condition.
Equipment
The equipment used in manufacturing should be designed and maintained to ensure it operates correctly and consistently.
This includes regular maintenance, calibration, and validation activities.
Proper training for operators is also essential to ensure equipment is used correctly.
Materials
The quality of raw materials is critical in ensuring the final product meets quality standards.
GMP guidelines require manufacturers to have strict controls on their suppliers and to conduct thorough testing of raw materials.
This helps to ensure that only high-quality materials are used in production.
Documentation and Recordkeeping
Accurate documentation and recordkeeping are essential in GMP compliance.
This includes everything from batch records to equipment logs.
Proper documentation helps ensure traceability and accountability, making it easier to identify and address issues if they arise.
Personnel
Personnel involved in the manufacturing process must be adequately trained and competent.
This includes initial training as well as ongoing education to keep up with new regulations and technologies.
Properly trained personnel are less likely to make mistakes, ensuring product quality and safety.
Implementing GMP in Manufacturing
Successfully implementing GMP in manufacturing requires a comprehensive approach.
Here are some essential steps to consider.
Conduct a Gap Analysis
Before implementing GMP, it’s crucial to conduct a gap analysis to identify areas where current practices fall short of GMP guidelines.
This involves reviewing existing processes, procedures, and systems to pinpoint where changes are needed.
Develop a GMP Plan
Once gaps are identified, develop a detailed GMP plan to address them.
This plan should outline specific actions and timelines for achieving compliance.
It should also include resource allocation, such as personnel and budget, to ensure successful implementation.
Train Employees
Training employees is a critical part of GMP implementation.
All personnel involved in the manufacturing process should receive comprehensive training on GMP guidelines and procedures.
Ongoing training should be provided to ensure employees stay informed about new regulations and best practices.
Monitor and Evaluate
Regular monitoring and evaluation are essential to ensure GMP compliance.
This includes conducting internal audits, reviewing documentation, and inspecting facilities and equipment.
Any deviations from GMP guidelines should be promptly addressed to maintain compliance.
Continuous Improvement
GMP is not a one-time effort; it requires continuous improvement.
Regularly review and update processes and procedures to ensure they remain effective.
Encourage feedback from employees and stakeholders to identify areas for improvement.
Conclusion
Adhering to Good Manufacturing Practice is essential in ensuring manufacturing quality.
It helps to ensure product safety, maintain consistency, and comply with regulatory requirements.
By understanding and implementing the core principles of GMP, manufacturers can achieve high-quality standards and build consumer trust.
Continuous improvement and regular evaluation are key to maintaining GMP compliance and ensuring long-term success in the manufacturing industry.
資料ダウンロード
QCD調達購買管理クラウド「newji」は、調達購買部門で必要なQCD管理全てを備えた、現場特化型兼クラウド型の今世紀最高の購買管理システムとなります。
ユーザー登録
調達購買業務の効率化だけでなく、システムを導入することで、コスト削減や製品・資材のステータス可視化のほか、属人化していた購買情報の共有化による内部不正防止や統制にも役立ちます。
NEWJI DX
製造業に特化したデジタルトランスフォーメーション(DX)の実現を目指す請負開発型のコンサルティングサービスです。AI、iPaaS、および先端の技術を駆使して、製造プロセスの効率化、業務効率化、チームワーク強化、コスト削減、品質向上を実現します。このサービスは、製造業の課題を深く理解し、それに対する最適なデジタルソリューションを提供することで、企業が持続的な成長とイノベーションを達成できるようサポートします。
オンライン講座
製造業、主に購買・調達部門にお勤めの方々に向けた情報を配信しております。
新任の方やベテランの方、管理職を対象とした幅広いコンテンツをご用意しております。
お問い合わせ
コストダウンが利益に直結する術だと理解していても、なかなか前に進めることができない状況。そんな時は、newjiのコストダウン自動化機能で大きく利益貢献しよう!
(Β版非公開)