- お役立ち記事
- Establishment of common standards and audit procedures for improving supplier quality
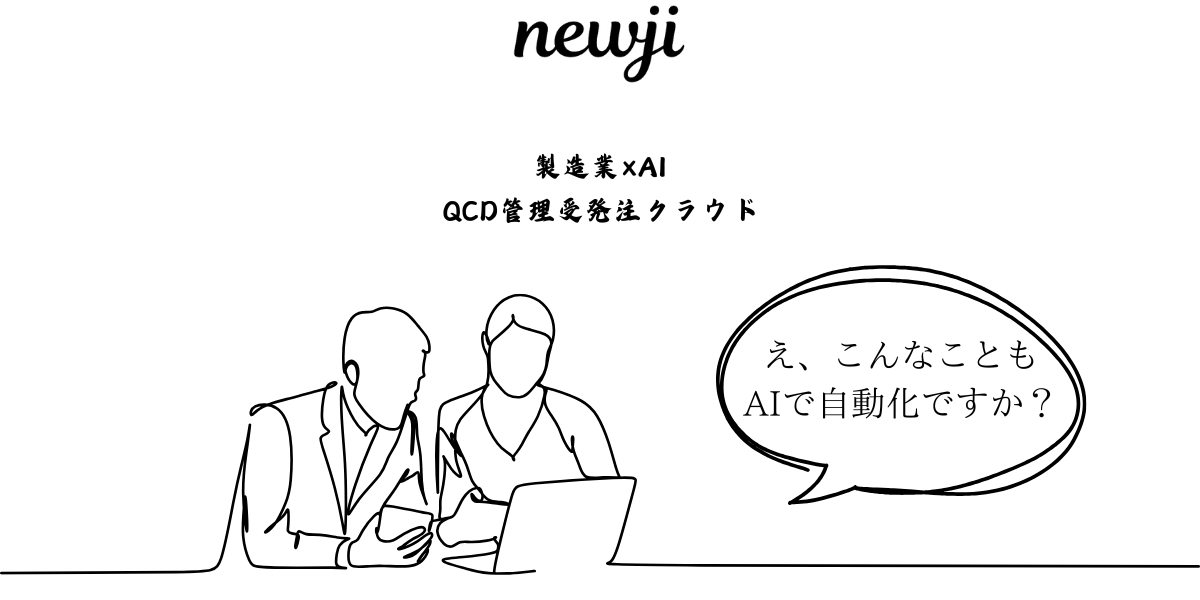
Establishment of common standards and audit procedures for improving supplier quality
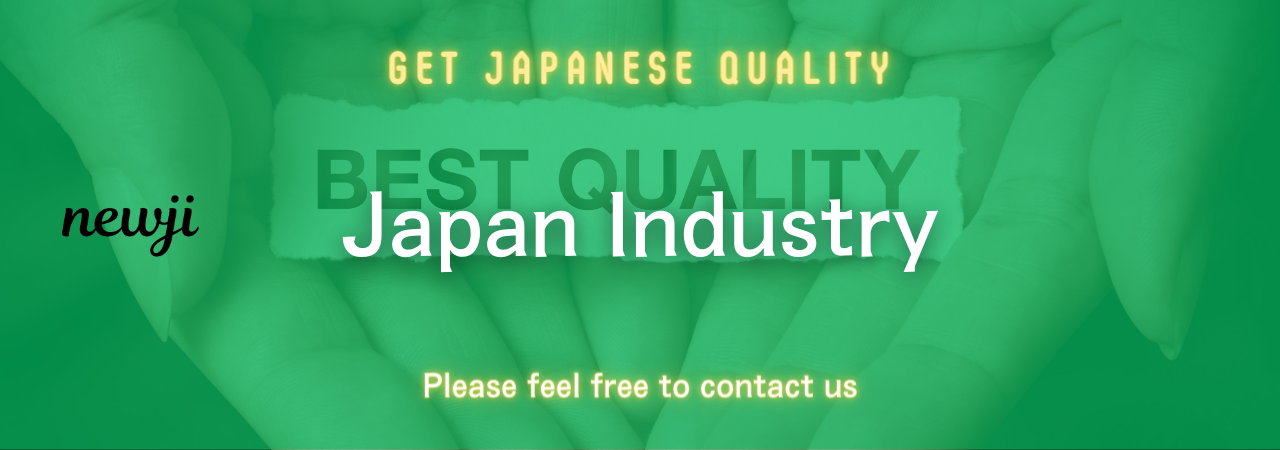
目次
Introduction
Improving supplier quality is a crucial aspect of maintaining the integrity of any business operation.
With globalization and the complex web of supply chains, ensuring that suppliers adhere to expected quality standards has become more necessary than ever.
Establishing common standards and audit procedures is a strategic approach to address this need.
These measures not only enhance product quality but also foster trust and reliability across the supply chain.
Importance of Supplier Quality
Supplier quality is the backbone of product excellence.
Suppliers that provide subpar materials can jeopardize the entire production process, leading to defective products and tarnished brand reputation.
Ensuring high supplier quality can significantly reduce production downtime, minimize waste, and lower the rejection rate of goods.
This results in increased customer satisfaction and improved overall company performance.
Establishing Common Standards
Creating common standards for suppliers is the first step in ensuring consistent quality.
Common standards act as a guideline for suppliers, detailing the exact specifications required for materials, components, or services.
These standards should align with the company’s overall quality expectations and compliance requirements.
Standards must be clear, measurable, and achievable to be effective.
By setting these benchmarks, companies ensure that suppliers understand what is expected of them, thus reducing variability in quality.
Developing Industry-Specific Standards
Different industries have unique requirements for quality standards.
For instance, the automotive industry demands high precision and reliability for safety.
Meanwhile, the food industry requires stringent hygiene and safety measures.
Developing industry-specific standards ensures that supplier quality aligns with the specific demands of each sector.
These standards might be based on international guidelines like ISO or developed internally to suit the company’s needs.
Communication and Training
Once standards are established, it is vital to communicate them clearly to all suppliers.
Regular training sessions and workshops can help suppliers understand these standards and implement them effectively.
This collaborative approach ensures that suppliers are well-equipped to meet the company’s quality requirements.
Implementing Audit Procedures
Audit procedures are essential for monitoring supplier adherence to established standards.
Regular audits provide an opportunity to assess supplier performance and identify areas needing improvement.
Audits should be conducted systematically, covering all aspects of the supplier’s operation that affect quality.
Types of Audits
There are several types of audits that companies can employ to evaluate supplier quality:
– **First-party audits**: Conducted by the supplier to assess their internal processes and ensure they meet the required standards.
– **Second-party audits**: Carried out by the company with direct interest in the supplier’s products.
These audits help ensure that suppliers comply with the company’s quality requirements.
– **Third-party audits**: Performed by independent organizations, offering an unbiased evaluation of the supplier’s processes.
These audits are often required for certification purposes.
Audit Frequency and Scope
The frequency of supplier audits should depend on several factors, including the supplier’s past performance, the criticality of supplied materials, and changes in market or regulatory conditions.
Having a flexible audit schedule allows companies to address quality concerns proactively.
The scope of an audit must be comprehensive, examining everything from raw materials sourcing to the final product.
This ensures any potential quality issues are addressed at every stage of production.
Post-Audit Actions
After completing an audit, it is essential to discuss the findings with the supplier.
Both parties should collaboratively develop corrective action plans to address any identified deficiencies.
Follow-up audits may be necessary to ensure that these corrective actions have been successfully implemented.
Benefits of Improved Supplier Quality
By establishing common standards and implementing regular audit procedures, companies can reap numerous benefits that extend beyond product quality.
Streamlined Processes
When suppliers consistently meet quality standards, businesses can streamline their processes.
Reduced variability in incoming materials minimizes rework and quality control checks, leading to a more efficient production process.
Cost Savings
Improved supplier quality can translate into significant cost savings.
With fewer defects and better utilization of resources, companies can reduce wastage and increase profitability.
Additionally, the costs associated with handling customer complaints and product recalls are minimized.
Enhanced Reputation
A commitment to quality at all levels of the supply chain enhances a company’s reputation.
Customers are more likely to trust brands that prioritize quality and reliability in their products.
This trust can lead to increased customer loyalty and business growth.
Risk Mitigation
Regularly auditing suppliers allows companies to identify potential risks in their supply chain before they escalate.
This proactive approach to risk management protects the company from disruptions and unexpected costs associated with supplier issues.
Conclusion
Establishing common standards and audit procedures is vital for improving supplier quality.
These measures not only ensure product excellence but also contribute to operational efficiency and customer satisfaction.
By clearly communicating standards and regularly auditing supplier performance, companies can build stronger, more reliable supply chains.
This proactive approach to supplier quality management sets the foundation for long-term success and sustainability in the competitive global marketplace.
資料ダウンロード
QCD調達購買管理クラウド「newji」は、調達購買部門で必要なQCD管理全てを備えた、現場特化型兼クラウド型の今世紀最高の購買管理システムとなります。
ユーザー登録
調達購買業務の効率化だけでなく、システムを導入することで、コスト削減や製品・資材のステータス可視化のほか、属人化していた購買情報の共有化による内部不正防止や統制にも役立ちます。
NEWJI DX
製造業に特化したデジタルトランスフォーメーション(DX)の実現を目指す請負開発型のコンサルティングサービスです。AI、iPaaS、および先端の技術を駆使して、製造プロセスの効率化、業務効率化、チームワーク強化、コスト削減、品質向上を実現します。このサービスは、製造業の課題を深く理解し、それに対する最適なデジタルソリューションを提供することで、企業が持続的な成長とイノベーションを達成できるようサポートします。
オンライン講座
製造業、主に購買・調達部門にお勤めの方々に向けた情報を配信しております。
新任の方やベテランの方、管理職を対象とした幅広いコンテンツをご用意しております。
お問い合わせ
コストダウンが利益に直結する術だと理解していても、なかなか前に進めることができない状況。そんな時は、newjiのコストダウン自動化機能で大きく利益貢献しよう!
(Β版非公開)