- お役立ち記事
- Example of business improvement in purchasing department to shorten procurement lead time
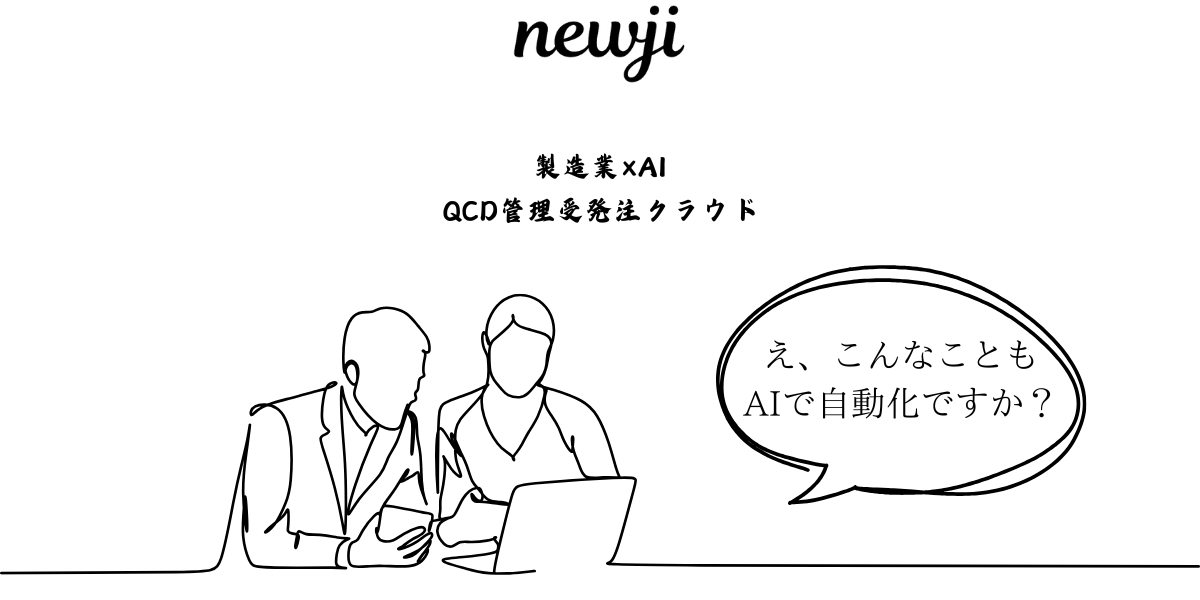
Example of business improvement in purchasing department to shorten procurement lead time
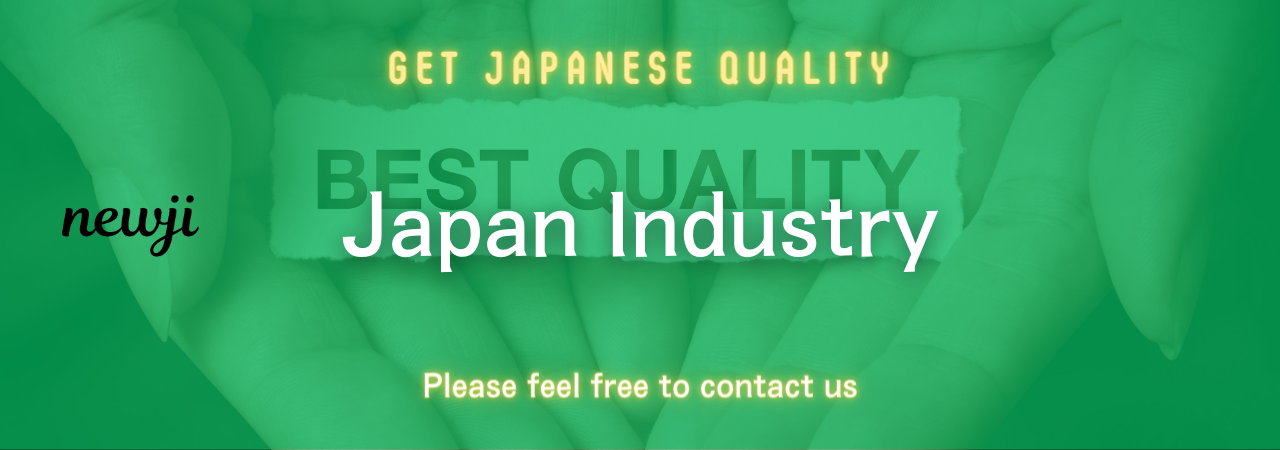
目次
Introduction to Business Improvement
The purchasing department plays a crucial role in any organization by managing the procurement of goods and services.
However, one common challenge many businesses face is long procurement lead times.
Reducing these lead times can significantly enhance efficiency, cut costs, and improve customer satisfaction.
In this article, we will explore some practical examples and strategies to improve procurement lead times in the purchasing department.
Understanding Procurement Lead Time
Procurement lead time refers to the total time taken from identifying a need for a product or service to the receipt of the items.
It includes several stages such as identifying suppliers, negotiating contracts, placing orders, and receiving goods.
Long lead times can negatively impact business operations by delaying production schedules, increasing inventory costs, and potentially leading to lost sales opportunities.
Therefore, it’s essential for purchasing departments to implement strategies that minimize these times effectively.
Assessing Current Processes
To improve procurement lead times, it’s important to first understand and assess the current processes in place.
Begin by mapping out the existing procurement workflow from start to finish.
Identify bottlenecks, redundant tasks, and other factors that contribute to delaying procurements.
Collect data from each step of the process to determine average timeframes and identify areas for improvement.
Engage with stakeholders, including suppliers, internal teams, and other departments, to gain insights and potential solutions.
Implementing Smart Technology
The adoption of technology is a powerful way to streamline procurement processes.
Implementing procurement software can automate many time-consuming tasks such as order processing, supplier communications, and contract management.
These digital tools provide real-time updates and track every stage of the procurement cycle, enabling faster decision-making and reducing the risk of human errors.
Consider utilizing platforms with advanced features like predictive analytics to forecast future needs and optimize inventory levels.
Enhancing Supplier Relationships
Efficient supplier relationships are pivotal in minimizing lead times.
Establishing strong partnerships with suppliers fosters better communication and collaboration.
Engage in regular performance reviews with your suppliers to ensure they meet delivery timelines and quality standards.
Additionally, consider negotiating favorable terms that prioritize fast shipping and bulk discounts.
Having multiple reliable suppliers can also prevent delays caused by relying on a single source.
Streamlining Approval Processes
Lengthy approval processes can often stall procurement activities.
Review and simplify internal approval procedures to expedite decision-making.
Implement a system where approvals can be granted electronically rather than through cumbersome paperwork.
Setting clear authority levels within the team can also prevent unnecessary delays.
This allows for quick yet accountable decision-making when pressing orders and resolving urgent needs.
Case Study: A Successful Implementation
Let’s look at an example of a company that successfully reduced its procurement lead time through effective strategies.
A mid-sized manufacturing firm was experiencing delays due to lengthy supplier negotiations and inefficient internal communication channels.
The company streamlined its vendor selection process by implementing a comprehensive supplier management system.
This digital tool allowed them to evaluate potential suppliers more efficiently based on predefined criteria.
Moreover, they established periodic alignment meetings with key suppliers to discuss expectations and feedback.
Internally, the company revamped its approval process by adopting an automated workflow system that linked directly to their ERP (Enterprise Resource Planning) software.
As a result of these improvements, the company reduced its procurement lead time by 40%.
This not only lowered production costs but also enabled them to meet customer demands more swiftly.
Continuous Improvement and Adaptation
Improving procurement lead times is not a one-off task.
It requires continuous monitoring and adaptation to ever-changing business environments.
Keep track of performance metrics and gather team feedback regularly to identify new improvement opportunities.
Market dynamics, supplier capabilities, and technological advancements are constantly evolving.
Stay informed about trends and adjust your strategies accordingly to maintain efficient and competitive procurement practices.
Conclusion
The purchasing department’s ability to enhance business performance significantly depends on effectively managing procurement lead times.
By assessing current processes, harnessing technology, and fostering productive supplier relationships, companies can achieve substantial improvements.
Streamlining approval processes and maintaining a cycle of continuous enhancement will further solidify these efforts.
Ultimately, the benefits of reduced procurement lead times extend beyond cost savings, contributing to better service delivery and higher customer satisfaction.
Implementing these strategies might require an upfront investment of time and resources, but the long-term gains for the business are well worth it.
Begin transforming your purchasing department today to stay ahead in the competitive landscape.
資料ダウンロード
QCD調達購買管理クラウド「newji」は、調達購買部門で必要なQCD管理全てを備えた、現場特化型兼クラウド型の今世紀最高の購買管理システムとなります。
ユーザー登録
調達購買業務の効率化だけでなく、システムを導入することで、コスト削減や製品・資材のステータス可視化のほか、属人化していた購買情報の共有化による内部不正防止や統制にも役立ちます。
NEWJI DX
製造業に特化したデジタルトランスフォーメーション(DX)の実現を目指す請負開発型のコンサルティングサービスです。AI、iPaaS、および先端の技術を駆使して、製造プロセスの効率化、業務効率化、チームワーク強化、コスト削減、品質向上を実現します。このサービスは、製造業の課題を深く理解し、それに対する最適なデジタルソリューションを提供することで、企業が持続的な成長とイノベーションを達成できるようサポートします。
オンライン講座
製造業、主に購買・調達部門にお勤めの方々に向けた情報を配信しております。
新任の方やベテランの方、管理職を対象とした幅広いコンテンツをご用意しております。
お問い合わせ
コストダウンが利益に直結する術だと理解していても、なかなか前に進めることができない状況。そんな時は、newjiのコストダウン自動化機能で大きく利益貢献しよう!
(Β版非公開)