- お役立ち記事
- Exploring the Pioneers of Innovation: Japanese Welding Machine OEMs Revolutionizing Manufacturing
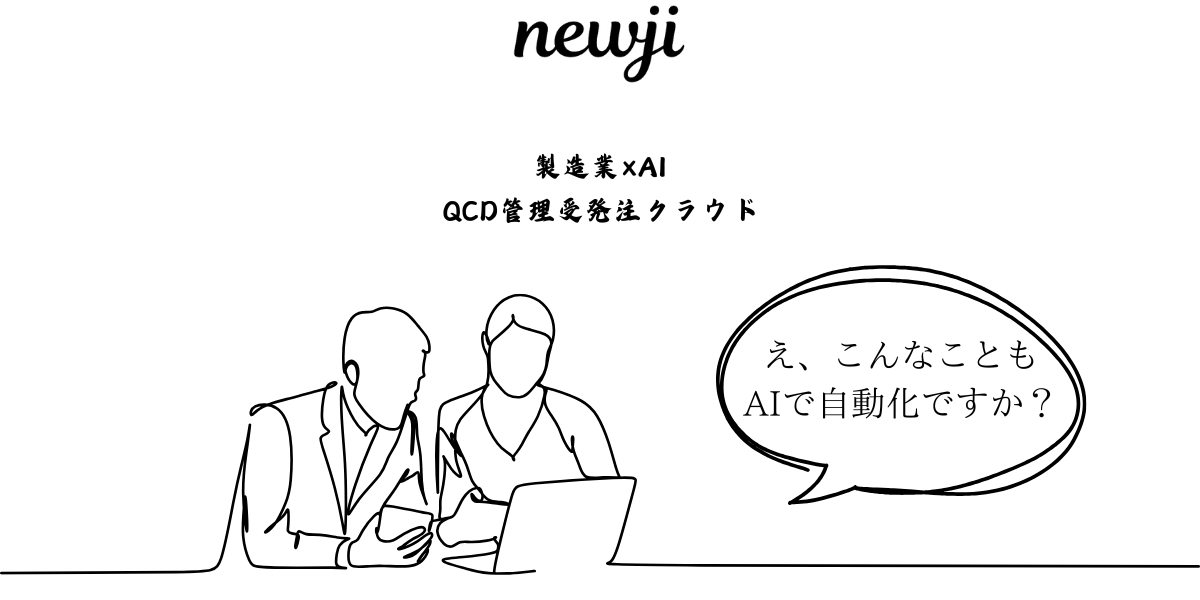
Exploring the Pioneers of Innovation: Japanese Welding Machine OEMs Revolutionizing Manufacturing
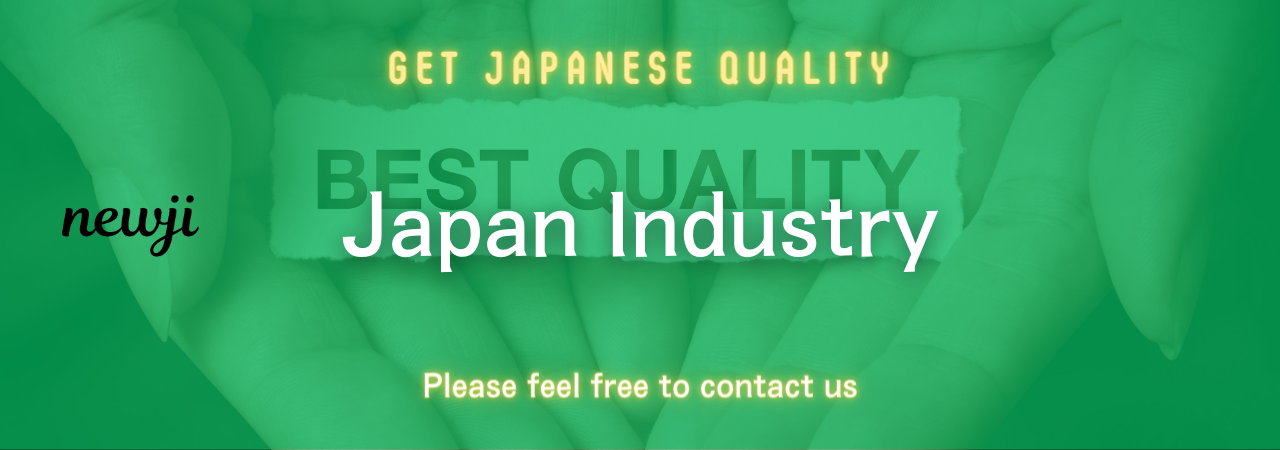
目次
Introduction
Japanese welding machine OEMs have long been at the forefront of innovation in the manufacturing sector. Their commitment to quality, precision, and technological advancements has not only set industry standards but also revolutionized production processes worldwide. This article delves into the pivotal role these OEMs play in modern manufacturing, exploring their advantages, challenges, procurement strategies, and best practices for effective collaboration.
The Landscape of Japanese Welding Machine OEMs
Japan’s reputation for manufacturing excellence is well-established, particularly in the realm of welding machines. OEMs (Original Equipment Manufacturers) in this sector are renowned for their advanced technology, reliability, and efficiency. These companies invest heavily in research and development, ensuring their products incorporate the latest innovations and meet stringent quality standards.
Key Players in the Market
Major Japanese welding machine OEMs include Mitsubishi Electric, Panasonic, and Yamazaki Mazak. Each of these companies brings a unique set of strengths to the table, from cutting-edge automation solutions to sustainable manufacturing practices. Their global presence allows them to serve a diverse clientele, adapting their offerings to meet varying market demands.
Technological Innovations
Japanese OEMs are pioneers in integrating smart technologies into welding machines. Features such as IoT connectivity, AI-driven process optimization, and advanced user interfaces enhance the functionality and ease of use of their products. These innovations not only improve production efficiency but also reduce downtime and maintenance costs.
Advantages of Partnering with Japanese Welding Machine OEMs
Collaborating with Japanese OEMs offers numerous benefits for manufacturing companies. Their dedication to quality and continuous improvement can significantly enhance production capabilities and product quality.
Superior Quality and Reliability
Japanese welding machines are synonymous with durability and precision. OEMs adhere to strict quality control measures, ensuring that each machine performs consistently over extended periods. This reliability minimizes operational disruptions and maintenance expenses, providing manufacturers with a dependable production tool.
Advanced Technology and Innovation
The continuous innovation demonstrated by Japanese OEMs means that manufacturers have access to the latest welding technologies. Features such as automated control systems, real-time monitoring, and energy-efficient designs contribute to more efficient and sustainable manufacturing processes.
Comprehensive Support and Service
Japanese OEMs are known for their exceptional customer service and support. From initial consultation and installation to ongoing maintenance and training, these companies offer comprehensive services that help manufacturers maximize the benefits of their welding machines.
Challenges in Collaborating with Japanese OEMs
While the advantages are substantial, there are also challenges associated with partnering with Japanese welding machine OEMs. Understanding these challenges is crucial for developing effective procurement and collaboration strategies.
High Initial Investment
The advanced technology and superior quality of Japanese welding machines often come with a higher price tag compared to competitors. Manufacturers must consider the long-term benefits and potential cost savings due to increased efficiency and reduced downtime when evaluating the initial investment.
Cultural and Communication Barriers
Cultural differences and language barriers can pose challenges in communication and negotiation. Building strong relationships and fostering clear, consistent communication are essential for overcoming these hurdles and ensuring successful collaboration.
Lead Times and Supply Chain Considerations
Japanese OEMs may have longer lead times due to their meticulous manufacturing processes and high demand for their products. Manufacturers need to plan accordingly and establish robust supply chain strategies to mitigate potential delays and ensure timely delivery of welding machines.
Procurement and Purchasing Strategies
Effective procurement and purchasing strategies are vital for maximizing the benefits of partnering with Japanese welding machine OEMs. These strategies encompass sourcing, negotiation, and relationship management to ensure optimal outcomes.
Sourcing the Right OEM
Selecting the appropriate OEM involves evaluating factors such as product quality, technological capabilities, reputation, and support services. Conducting thorough market research and considering the specific needs of your manufacturing operations will help in identifying the best-fit OEM partner.
Negotiation Techniques
Negotiating with Japanese OEMs requires a strategic approach that respects their business culture and emphasizes mutual benefits. Key techniques include:
– **Building Trust:** Establishing a trustworthy relationship is crucial. This can be achieved through transparent communication and demonstrating a genuine commitment to a long-term partnership.
– **Understanding Value:** Focus on the value proposition rather than just the price. Highlight how your partnership can lead to mutual growth and success.
– **Flexibility and Patience:** Be prepared to navigate through a more deliberate negotiation process. Patience and flexibility can facilitate more favorable terms and stronger partnerships.
Establishing Long-Term Relationships
Cultivating long-term relationships with OEMs can lead to various benefits, including better pricing, priority in production schedules, and enhanced support. Regular communication, joint planning, and collaborative problem-solving contribute to a stronger, more resilient partnership.
Market Conditions and Trends
Understanding the current market conditions and emerging trends is essential for making informed procurement decisions and staying competitive in the manufacturing sector.
Global Supply Chain Dynamics
Global supply chains have become increasingly complex, with factors such as geopolitical tensions, trade policies, and logistical challenges impacting the availability and cost of welding machines. Japanese OEMs, with their robust supply chains and strategic partnerships, are well-positioned to navigate these complexities and ensure reliable supply.
Focus on Sustainability
There is a growing emphasis on sustainable manufacturing practices. Japanese welding machine OEMs are responding by developing energy-efficient machines and incorporating environmentally friendly materials and processes. Partnering with OEMs that prioritize sustainability can enhance your company’s environmental credentials and compliance with regulatory standards.
Advancements in Automation and Robotics
The integration of automation and robotics into welding machines is revolutionizing manufacturing processes. These advancements lead to higher precision, increased production speeds, and reduced labor costs. Staying abreast of these technological trends is crucial for maintaining a competitive edge.
Best Practices for Effective Collaboration
Implementing best practices in collaboration with Japanese welding machine OEMs can significantly enhance the success of your procurement and manufacturing operations.
Clear Communication
Effective communication is the cornerstone of any successful partnership. Establishing clear channels and regular communication schedules helps in addressing issues promptly and ensuring that both parties are aligned in their objectives and expectations.
Comprehensive Training and Support
Providing adequate training for your staff on the operation and maintenance of welding machines is essential for maximizing their performance and longevity. Collaborate with OEMs to develop comprehensive training programs and leverage their support services to ensure your team is well-equipped to handle the technology.
Continuous Improvement and Feedback
Adopting a continuous improvement mindset encourages ongoing evaluation and optimization of your manufacturing processes. Regularly soliciting feedback from OEMs and incorporating their insights can lead to enhancements in both product performance and operational efficiency.
Case Studies: Success Stories of Collaboration
Examining real-world examples of successful partnerships with Japanese welding machine OEMs can provide valuable insights and inspiration for your own collaboration efforts.
Case Study 1: Automotive Manufacturing Excellence
A leading automotive manufacturer partnered with a Japanese OEM to upgrade their welding operations. By integrating advanced automated welding machines, the company achieved a 30% increase in production efficiency and a significant reduction in defect rates. The collaboration fostered a culture of continuous improvement, leading to subsequent process optimizations and sustained operational excellence.
Case Study 2: Aerospace Industry Innovation
An aerospace company sought to enhance the precision and reliability of their welding processes. Partnering with a Japanese OEM, they implemented state-of-the-art welding machines equipped with real-time monitoring and AI-driven quality control. This partnership not only improved product quality but also ensured compliance with stringent industry standards, securing the company’s reputation for excellence.
Future Outlook
The future of manufacturing is poised to be shaped by ongoing innovations in welding technology. Japanese OEMs will continue to play a critical role in driving advancements that enhance production capabilities and operational efficiency.
Emerging Technologies
Technologies such as additive manufacturing, advanced robotics, and smart sensors are set to revolutionize welding processes. Japanese OEMs are at the forefront of integrating these technologies into their machines, paving the way for more flexible and adaptable manufacturing environments.
Global Expansion and Market Penetration
As global manufacturing hubs evolve, Japanese welding machine OEMs are expanding their reach to emerging markets. Their ability to adapt to local market conditions while maintaining high standards of quality positions them as preferred partners for manufacturers worldwide.
Sustainability and Environmental Responsibility
With increasing emphasis on sustainability, Japanese OEMs will continue to develop eco-friendly welding solutions. Innovations aimed at reducing energy consumption and minimizing environmental impact will align with global trends towards more responsible manufacturing practices.
Conclusion
Japanese welding machine OEMs are undeniably revolutionizing the manufacturing landscape through their unwavering commitment to quality, innovation, and customer-centric solutions. By understanding the advantages and challenges of partnering with these OEMs, and adopting effective procurement and collaboration strategies, manufacturers can harness the full potential of these advanced welding technologies. Embracing the expertise and innovations of Japanese OEMs not only enhances production efficiency and product quality but also positions manufacturers for sustained success in an increasingly competitive global market.
資料ダウンロード
QCD調達購買管理クラウド「newji」は、調達購買部門で必要なQCD管理全てを備えた、現場特化型兼クラウド型の今世紀最高の購買管理システムとなります。
ユーザー登録
調達購買業務の効率化だけでなく、システムを導入することで、コスト削減や製品・資材のステータス可視化のほか、属人化していた購買情報の共有化による内部不正防止や統制にも役立ちます。
NEWJI DX
製造業に特化したデジタルトランスフォーメーション(DX)の実現を目指す請負開発型のコンサルティングサービスです。AI、iPaaS、および先端の技術を駆使して、製造プロセスの効率化、業務効率化、チームワーク強化、コスト削減、品質向上を実現します。このサービスは、製造業の課題を深く理解し、それに対する最適なデジタルソリューションを提供することで、企業が持続的な成長とイノベーションを達成できるようサポートします。
オンライン講座
製造業、主に購買・調達部門にお勤めの方々に向けた情報を配信しております。
新任の方やベテランの方、管理職を対象とした幅広いコンテンツをご用意しております。
お問い合わせ
コストダウンが利益に直結する術だと理解していても、なかなか前に進めることができない状況。そんな時は、newjiのコストダウン自動化機能で大きく利益貢献しよう!
(Β版非公開)