- お役立ち記事
- Failure analysis technology for electronic equipment and how to utilize it to prevent failures
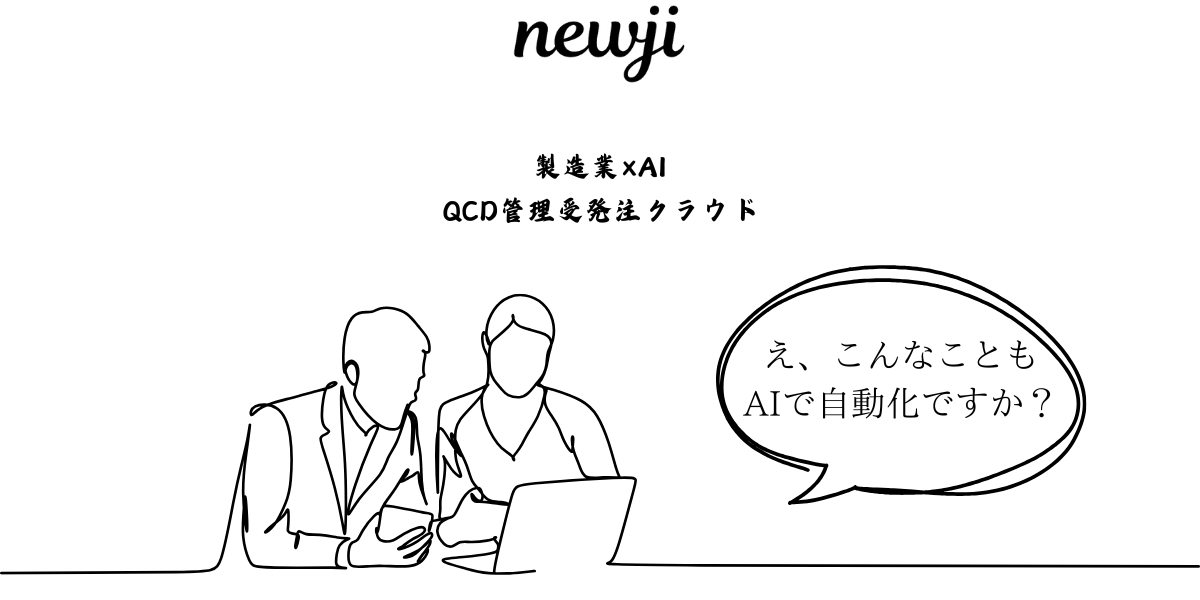
Failure analysis technology for electronic equipment and how to utilize it to prevent failures
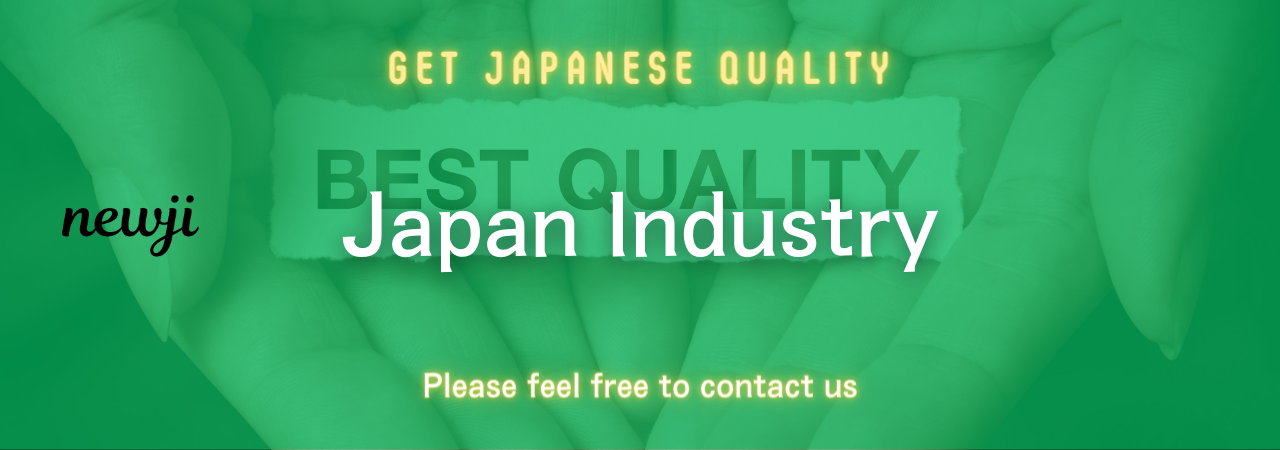
目次
Understanding Failure Analysis Technology
Failure analysis technology is a crucial tool in the field of electronics, utilized to identify the cause of a malfunction in electronic equipment.
It involves a systematic examination of failure modes, mechanisms, and impacts to figure out what went wrong with a device.
By understanding how and why these failures occur, manufacturers and engineers can design more reliable products and take preventive measures to mitigate future breakdowns.
In our digital age, electronic equipment plays a vital role in daily life, from smartphones and computers to complex industrial machinery.
Because of their widespread application, ensuring their reliability and durability is critical.
When an electronic device fails, it can lead to substantial financial losses, inconvenience, or even pose safety hazards.
Thus, implementing effective failure analysis techniques is essential for maintaining performance and preventing unexpected downtime.
Methods Used in Failure Analysis
Failure analysis technology incorporates a variety of methods and tools to scrutinize electronic devices.
These methods are designed to pinpoint the exact cause of failure, allowing for corrective actions.
Visual Inspection
The first step in failure analysis usually involves a thorough visual inspection.
Technicians examine the physical condition of a device to check for any obvious signs of damage such as burnt components, broken parts, or physical deformities.
This preliminary step sets the foundation for more in-depth analysis.
X-ray Inspection
X-ray analysis is employed to inspect components without disassembling the device.
It allows technicians to view the internal structures and pinpoint defects such as cracks or voids that may not be visible to the naked eye.
Thermography
Thermal imaging is used to detect hotspots or irregular temperature patterns in an electronic device.
By identifying unusual thermal signatures, experts can target areas with excessive heat that may be the source of a malfunction.
Electron Microscopy
For a more granular examination, electron microscopy is used.
This technique provides high-resolution images of a component’s surface and internal structure, revealing microscopic defects that could lead to failure.
Electrical Testing
Electrical tests are conducted to check the functional status of a device and measure performance parameters such as voltage and current.
This data helps identify whether an electronic failure is due to electrical inconsistencies.
Common Causes of Failures in Electronic Equipment
Electronic devices can fail for various reasons, often resulting from one or a combination of several factors.
Understanding these common causes can help in proactive failure prevention.
Environmental Factors
Exposure to extreme temperatures, humidity, or dust can deteriorate components, leading to failure.
Corrosion, short circuits, and other issues often stem from environmental stresses.
Manufacturing Defects
Defects introduced during the manufacturing process, such as soldering flaws or material inconsistencies, can weaken an electronic device’s performance over time.
Component Wear and Tear
Over time, the repeated use of an electronic device can lead to wear and tear of its components.
Fatigue, aging, and mechanical stress can cause the materials to weaken and eventually fail.
Design Flaws
Inadequate design can leave a device vulnerable to problems like overheating, excessive electromagnetic interference, or inadequate power distribution.
Redesigning components to withstand these challenges is crucial to device longevity.
Utilizing Failure Analysis to Prevent Future Failures
Once the root cause of a failure is identified, steps can be taken to prevent similar issues from occurring in the future.
Utilizing failure analysis to its fullest potential allows businesses and engineers to improve product reliability and customer satisfaction.
Design Improvements
Failure analysis findings allow engineers to make informed design improvements, such as strengthening materials, altering architecture, or enhancing thermal management.
These improvements contribute to more robust electronic equipment.
Quality Control Enhancements
By understanding failure origins, companies can enhance their quality control processes to catch potential defects early in the production line.
This proactive approach not only saves costs but also minimizes product recalls.
Predictive Maintenance
Predictive maintenance relies on data collected from failure analysis to anticipate when a device might fail.
By scheduling maintenance before a breakdown occurs, companies can reduce unexpected downtimes.
Training and Awareness
Training personnel with the latest failure analysis techniques and findings ensures that everyone involved in the production process is equipped to identify and address potential issues.
Awareness of typical failure causes and solutions also fosters a culture of precision and excellence.
Conclusion
Failure analysis technology is indispensable in the electronics industry, providing deep insights into the root causes of equipment malfunction.
By employing a range of sophisticated techniques, experts can prevent failures, extend product lifespan, and enhance overall reliability.
Integrating failure analysis results into the design, manufacturing, and maintenance phases fosters innovation and leads to the creation of high-quality, durable electronic products.
Understanding and applying these concepts not only benefits manufacturers but also enhances the user experience by reducing unexpected failures and improving product satisfaction.
資料ダウンロード
QCD調達購買管理クラウド「newji」は、調達購買部門で必要なQCD管理全てを備えた、現場特化型兼クラウド型の今世紀最高の購買管理システムとなります。
ユーザー登録
調達購買業務の効率化だけでなく、システムを導入することで、コスト削減や製品・資材のステータス可視化のほか、属人化していた購買情報の共有化による内部不正防止や統制にも役立ちます。
NEWJI DX
製造業に特化したデジタルトランスフォーメーション(DX)の実現を目指す請負開発型のコンサルティングサービスです。AI、iPaaS、および先端の技術を駆使して、製造プロセスの効率化、業務効率化、チームワーク強化、コスト削減、品質向上を実現します。このサービスは、製造業の課題を深く理解し、それに対する最適なデジタルソリューションを提供することで、企業が持続的な成長とイノベーションを達成できるようサポートします。
オンライン講座
製造業、主に購買・調達部門にお勤めの方々に向けた情報を配信しております。
新任の方やベテランの方、管理職を対象とした幅広いコンテンツをご用意しております。
お問い合わせ
コストダウンが利益に直結する術だと理解していても、なかなか前に進めることができない状況。そんな時は、newjiのコストダウン自動化機能で大きく利益貢献しよう!
(Β版非公開)