- お役立ち記事
- For equipment maintenance engineers in the steel industry! Strategies to extend roller life with predictive maintenance systems
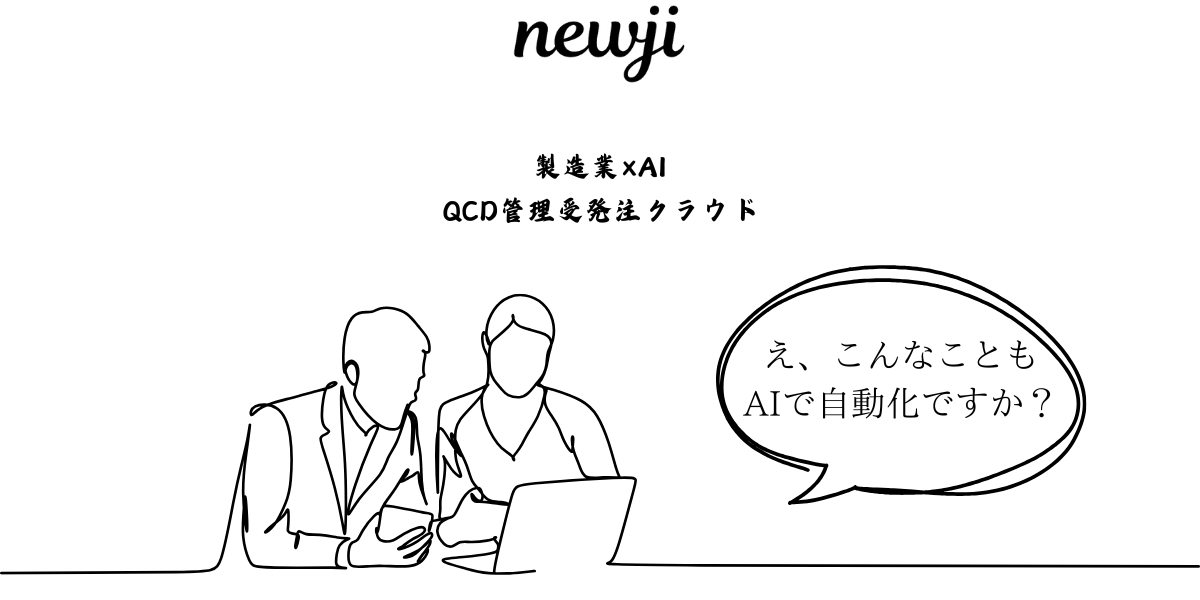
For equipment maintenance engineers in the steel industry! Strategies to extend roller life with predictive maintenance systems
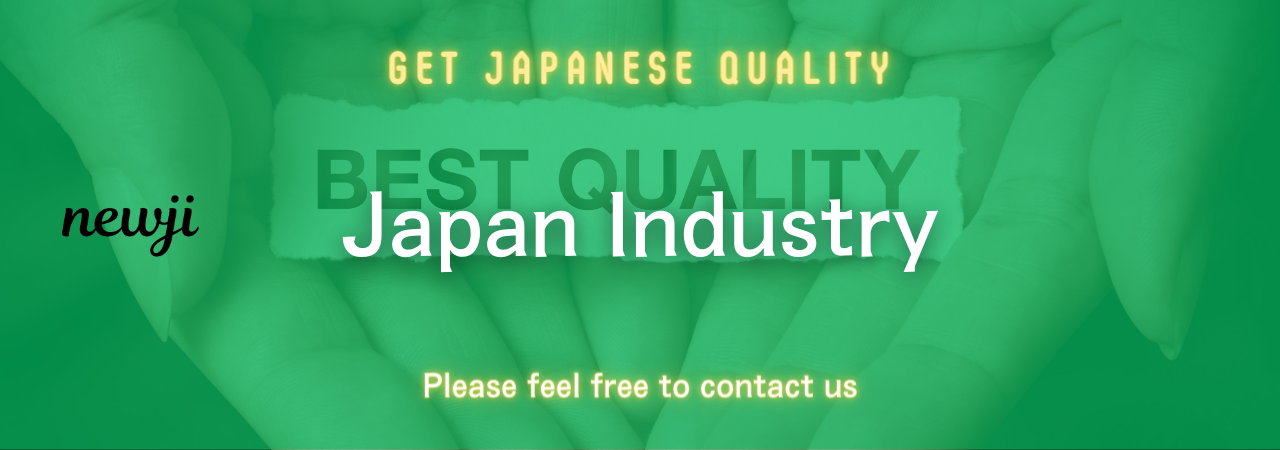
目次
Understanding Predictive Maintenance Systems
Predictive maintenance systems have revolutionized equipment maintenance across various industries, including the steel industry.
By using advanced technologies to predict when equipment might fail, these systems allow for timely interventions.
This means that maintenance can be scheduled just before a failure is likely to occur, thus preventing downtime and extending the life of equipment.
In the steel industry, rollers are crucial for the production process.
They play a significant role in the rolling of steel sheets and tubes, and their wear can markedly affect production efficiency and quality.
Thus, extending the roller life is a key objective for maintenance engineers.
The Role of Predictive Maintenance for Rollers
Predictive maintenance systems rely on a myriad of data collected through sensors and advanced software.
These tools predict equipment failures by analyzing patterns and trends.
For rollers in steel production, this means monitoring factors like temperature, vibration, and wear rates.
When a predictive maintenance system is in place, it continuously monitors the operational parameters of rollers.
For instance, excessive vibration may indicate an imbalance or misalignment.
By predicting when these anomalies may lead to significant issues, maintenance engineers can take corrective measures before roller failure becomes imminent.
Benefits of Predictive Maintenance Systems
The benefits of deploying predictive maintenance systems in the steel industry are numerous.
Firstly, there is a reduction in unplanned downtime.
Since the equipment is serviced before a failure can happen, production schedules are less likely to be interrupted.
Secondly, predictive maintenance leads to cost savings.
Replacing parts or repairing machinery only when necessary avoids unnecessary expenditure.
Also, by preventing failures, these systems reduce the need for emergency repairs, which are often more expensive.
Lastly, predictive maintenance systems contribute to longer roller life.
By maintaining optimal operating conditions, these systems ensure that rollers are less susceptible to excessive wear and tear.
Implementing Predictive Maintenance Systems
Before implementing a predictive maintenance system, maintenance engineers need to consider various aspects.
The first step involves identifying the critical components of the steel production process, such as rollers, which will benefit most from predictive maintenance.
The next step is the installation of sensors and monitoring equipment.
These tools will collect data from the rollers, which is then analyzed using predictive algorithms.
It’s also essential to ensure that maintenance staff are trained to interpret the data outputs effectively.
They should be able to decide when an alert requires intervention and what type of maintenance is necessary.
Challenges in Implementation
While predictive maintenance systems offer significant advantages, their implementation is not without challenges.
Initial setup can be costly, and integrating new technologies with existing systems may pose difficulties.
Moreover, incorrect data interpretation could lead to premature or delayed maintenance actions, which could, in turn, lead to decreased roller performance.
To counteract these challenges, it is crucial to invest in quality training and to select systems that have a proven track record in industrial settings.
Regular updates and calibration of the monitoring systems are also essential to maintain their accuracy over time.
Strategies Beyond Predictive Maintenance
In addition to predictive maintenance, there are other strategies maintenance engineers can employ to extend the life of rollers.
Regular visual inspections, for example, can help detect physical signs of wear that sensors might not pick up.
Additionally, using high-quality lubricants and replacing them at appropriate intervals can minimize friction and wear.
Another important strategy is material selection.
Using materials that are more resistant to wear and tear can naturally extend the life of rollers in the harsh conditions typically found in steel production facilities.
The Role of Data in Maintenance Decisions
Data-driven decisions are at the heart of predictive maintenance.
By analyzing trends and historical data, maintenance teams can make informed decisions about when to service equipment.
This data can also inform operational strategies, such as adjusting machine loads or altering production cycles to extend equipment life.
Moreover, sharing data insights across the organization can lead to better overall strategies.
For example, production teams can be made aware of maintenance schedules ahead of time, which can help with better planning and resource allocation.
Future of Predictive Maintenance in the Steel Industry
The future of predictive maintenance in the steel industry promises even more sophisticated technologies.
With advancements in artificial intelligence and machine learning, predictive models will become more accurate and capable of learning from new patterns over time.
This evolution will further enhance the ability of maintenance engineers to foresee potential issues before they impact production.
Furthermore, the integration of Internet of Things (IoT) technologies within predictive maintenance systems will lead to more comprehensive monitoring solutions, covering various facets of the production process.
Conclusion
For equipment maintenance engineers in the steel industry, the implementation of predictive maintenance systems presents an opportunity to significantly extend the life of rollers.
Through the adoption of smart technology and data-driven strategies, not only is equipment effectiveness improved, but operational costs and downtime are also reduced.
By embracing these advances, maintenance engineers can ensure the longevity and efficiency of their machinery, securing a competitive edge for their companies in the ever-changing landscape of the steel industry.
資料ダウンロード
QCD調達購買管理クラウド「newji」は、調達購買部門で必要なQCD管理全てを備えた、現場特化型兼クラウド型の今世紀最高の購買管理システムとなります。
ユーザー登録
調達購買業務の効率化だけでなく、システムを導入することで、コスト削減や製品・資材のステータス可視化のほか、属人化していた購買情報の共有化による内部不正防止や統制にも役立ちます。
NEWJI DX
製造業に特化したデジタルトランスフォーメーション(DX)の実現を目指す請負開発型のコンサルティングサービスです。AI、iPaaS、および先端の技術を駆使して、製造プロセスの効率化、業務効率化、チームワーク強化、コスト削減、品質向上を実現します。このサービスは、製造業の課題を深く理解し、それに対する最適なデジタルソリューションを提供することで、企業が持続的な成長とイノベーションを達成できるようサポートします。
オンライン講座
製造業、主に購買・調達部門にお勤めの方々に向けた情報を配信しております。
新任の方やベテランの方、管理職を対象とした幅広いコンテンツをご用意しております。
お問い合わせ
コストダウンが利益に直結する術だと理解していても、なかなか前に進めることができない状況。そんな時は、newjiのコストダウン自動化機能で大きく利益貢献しよう!
(Β版非公開)