- お役立ち記事
- For managers of equipment management departments! Reliability engineering practices to optimize equipment lifecycle
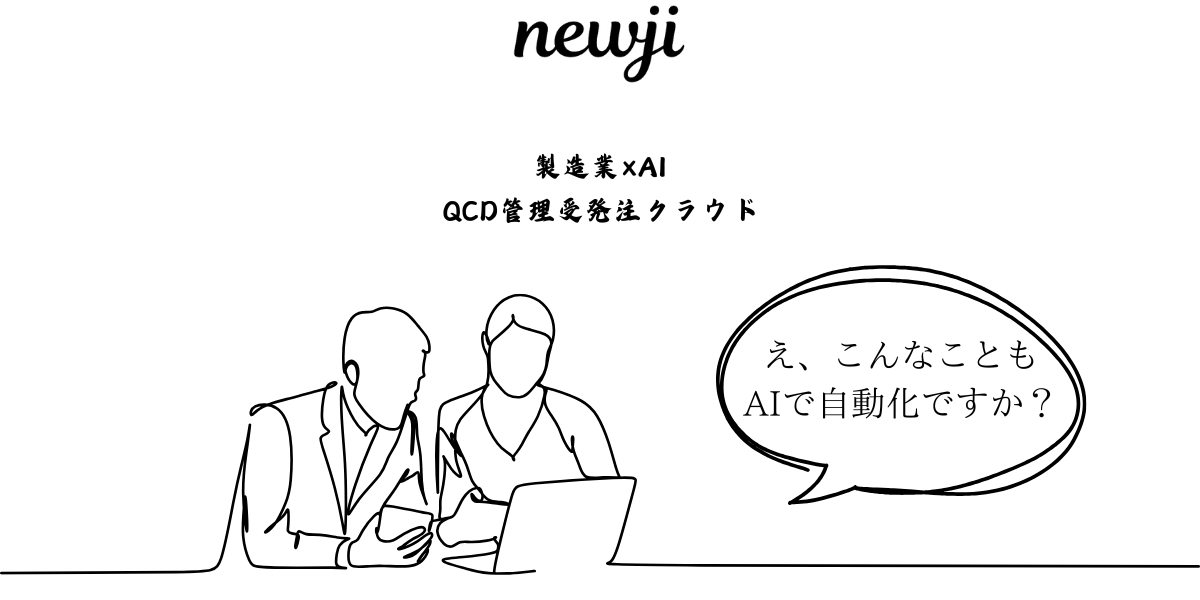
For managers of equipment management departments! Reliability engineering practices to optimize equipment lifecycle
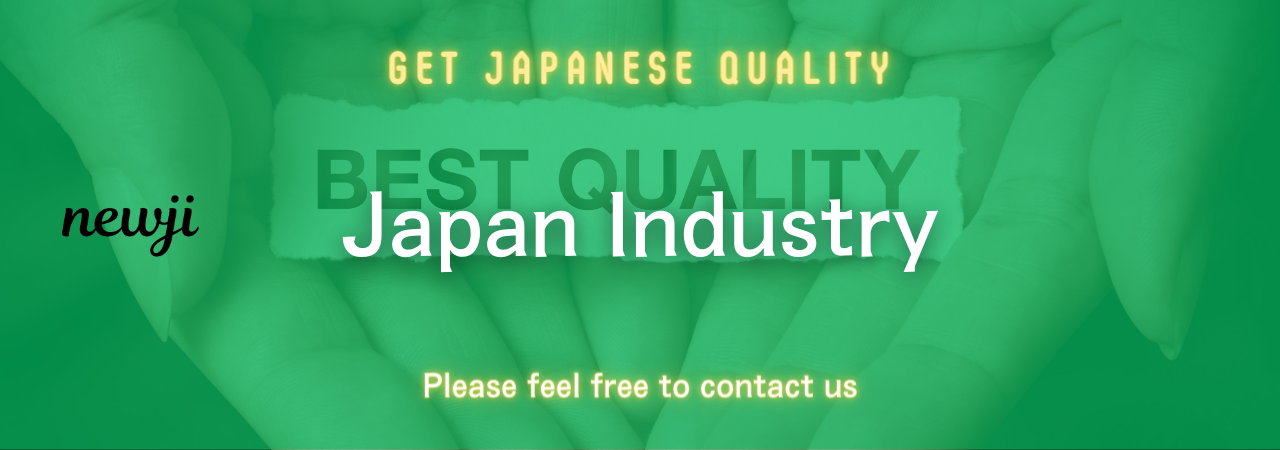
目次
Understanding Reliability Engineering
Reliability engineering is a critical discipline that ensures machinery and equipment function without failure over time.
This field focuses on improving equipment performance, predicting failures, and optimizing the lifecycle of equipment.
For managers of equipment management departments, integrating reliability engineering practices can lead to increased efficiency, reduced costs, and extended equipment lifespans.
At its core, reliability engineering involves analyzing historical data and using statistical methods to predict future performance and potential failures.
This approach helps in identifying weak points within equipment that could lead to potential breakdowns.
By understanding these vulnerable areas, managers can proactively address them, ensuring the equipment remains operational for as long as possible.
Benefits of Implementing Reliability Engineering
Reliability engineering provides several benefits that directly impact the bottom line of a company.
One of the most significant advantages is the reduction in maintenance costs.
With a predictive approach, companies can transition from reactive maintenance, which tends to be costly and disruptive, to a preventive strategy.
This shift not only saves money but also increases the uptime of equipment.
Another benefit is improved safety.
Reliability engineering helps in identifying potential failure points before they occur, which reduces the likelihood of hazardous situations.
This proactive approach creates a safer working environment for all employees, reducing the risk of accidents and the associated costs.
Furthermore, optimizing equipment lifecycle through reliability engineering also means better resource utilization.
Organizations can maximize the use of their assets, ensuring they get the most out of their investments.
This approach helps in attaining a higher return on investment, which is crucial for maintaining competitive advantage.
Key Practices in Reliability Engineering
To effectively integrate reliability engineering into your organization, certain key practices should be implemented.
Data Collection and Analysis
The foundation of reliability engineering is accurate and comprehensive data.
Collecting data on equipment performance, maintenance history, and failure incidents is essential.
This information provides insights into the patterns and causes of equipment failures.
Advanced tools and software can facilitate data collection and analysis, helping in accurate predictions and planning.
Root Cause Analysis (RCA)
Understanding the root causes of equipment failure is crucial for developing effective solutions.
Root Cause Analysis is a method used to identify the primary causes of failure in equipment.
By focusing on the root cause rather than symptoms, managers can implement solutions that prevent recurrence, thereby increasing reliability.
Failure Mode and Effects Analysis (FMEA)
FMEA is a systematic approach for evaluating equipment to identify where and how it might fail.
This technique assesses the potential impacts of different failure modes and prioritizes them based on severity and likelihood.
By understanding potential failure modes, managers can develop strategies to mitigate risks, ensuring equipment reliability.
Predictive Maintenance
Predictive maintenance is a cornerstone of reliability engineering that involves monitoring the condition of equipment to predict when maintenance should be performed.
This proactive approach relies on data analytics and sensors to predict potential failures, allowing maintenance to be scheduled before breakdowns occur.
Reliability-Centered Maintenance (RCM)
RCM is a process used to determine the maintenance requirements of equipment in its operating context.
It focuses on maintaining equipment function rather than just performing routine maintenance.
By identifying vital functions and analyzing failures, RCM helps in developing maintenance strategies that ensure reliability and availability.
Steps to Optimize Equipment Lifecycle through Reliability Engineering
To optimize the lifecycle of equipment, managers need to adopt a structured approach.
Below are outlined steps that can guide this process.
1. Assessment and Planning
The first step involves assessing the current reliability of equipment and identifying areas for improvement.
Setting clear objectives and goals for reliability is crucial.
This step also involves planning the integration of reliability engineering practices into the existing system.
2. Implementation of Reliability Tools
Once a plan is in place, the next step is to implement the necessary reliability tools and techniques.
This could involve investing in software for data analysis, training staff on new procedures, and setting up condition monitoring systems.
3. Continuous Monitoring and Analysis
After implementing reliability tools, continuous monitoring of equipment is vital.
Data should be regularly analyzed to track performance and detect any deviations from expected operation.
This ongoing analysis helps in making necessary adjustments to ensure optimal performance.
4. Feedback and Improvement
Feedback is a critical component in the cycle of reliability engineering.
Regular reviews and audits of the reliability processes help in identifying areas that need improvement.
This feedback loop ensures that reliability engineering practices evolve with changing operational needs and technological advancements.
Overcoming Challenges in Reliability Engineering
Implementing reliability engineering practices can come with several challenges.
For managers, overcoming resistance to change is often a significant hurdle.
Effective communication and demonstrating the long-term benefits of reliability engineering can help in gaining buy-in from stakeholders.
Moreover, developing the right skill set among the workforce is essential.
Investing in training and development ensures that employees are equipped to handle new technologies and methodologies associated with reliability engineering.
Lastly, managing the costs associated with the initial implementation of reliability engineering can be challenging.
However, viewing these costs as investments in future savings and efficiency can help justify the expenditure.
By harnessing the principles and practices of reliability engineering, managers can significantly optimize equipment lifecycle, leading to improved performance, cost savings, and enhanced safety.
Adopting a proactive approach not only ensures the longevity of equipment but also contributes to the overall success of the organization.
資料ダウンロード
QCD調達購買管理クラウド「newji」は、調達購買部門で必要なQCD管理全てを備えた、現場特化型兼クラウド型の今世紀最高の購買管理システムとなります。
ユーザー登録
調達購買業務の効率化だけでなく、システムを導入することで、コスト削減や製品・資材のステータス可視化のほか、属人化していた購買情報の共有化による内部不正防止や統制にも役立ちます。
NEWJI DX
製造業に特化したデジタルトランスフォーメーション(DX)の実現を目指す請負開発型のコンサルティングサービスです。AI、iPaaS、および先端の技術を駆使して、製造プロセスの効率化、業務効率化、チームワーク強化、コスト削減、品質向上を実現します。このサービスは、製造業の課題を深く理解し、それに対する最適なデジタルソリューションを提供することで、企業が持続的な成長とイノベーションを達成できるようサポートします。
オンライン講座
製造業、主に購買・調達部門にお勤めの方々に向けた情報を配信しております。
新任の方やベテランの方、管理職を対象とした幅広いコンテンツをご用意しております。
お問い合わせ
コストダウンが利益に直結する術だと理解していても、なかなか前に進めることができない状況。そんな時は、newjiのコストダウン自動化機能で大きく利益貢献しよう!
(Β版非公開)