- お役立ち記事
- For managers of production technology departments! How to effectively implement the Toyota Production System to increase productivity
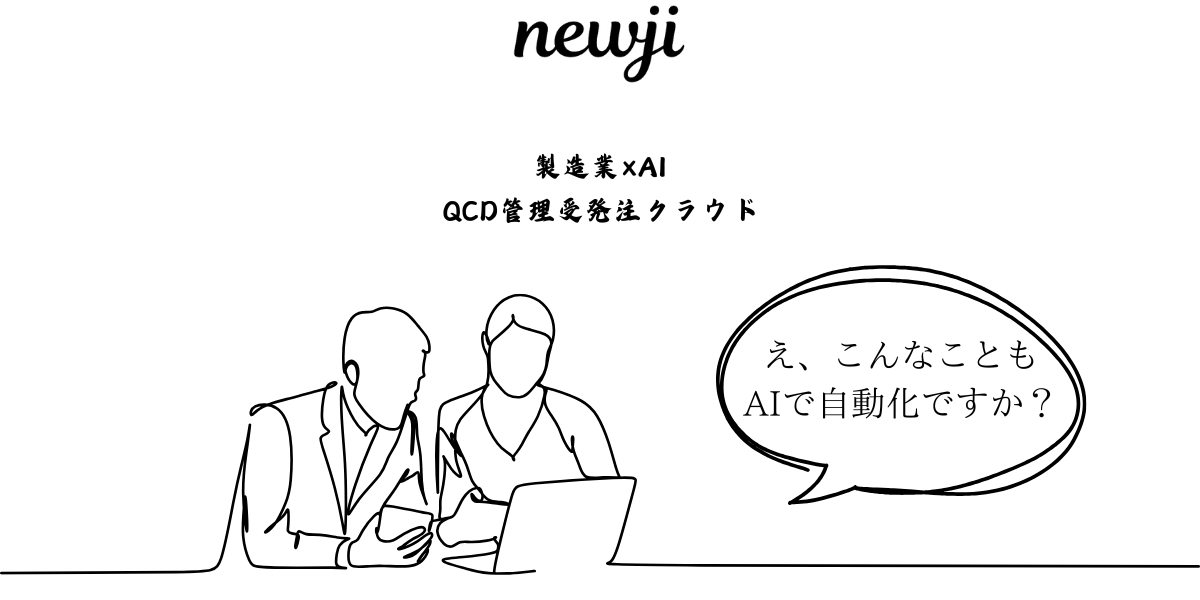
For managers of production technology departments! How to effectively implement the Toyota Production System to increase productivity
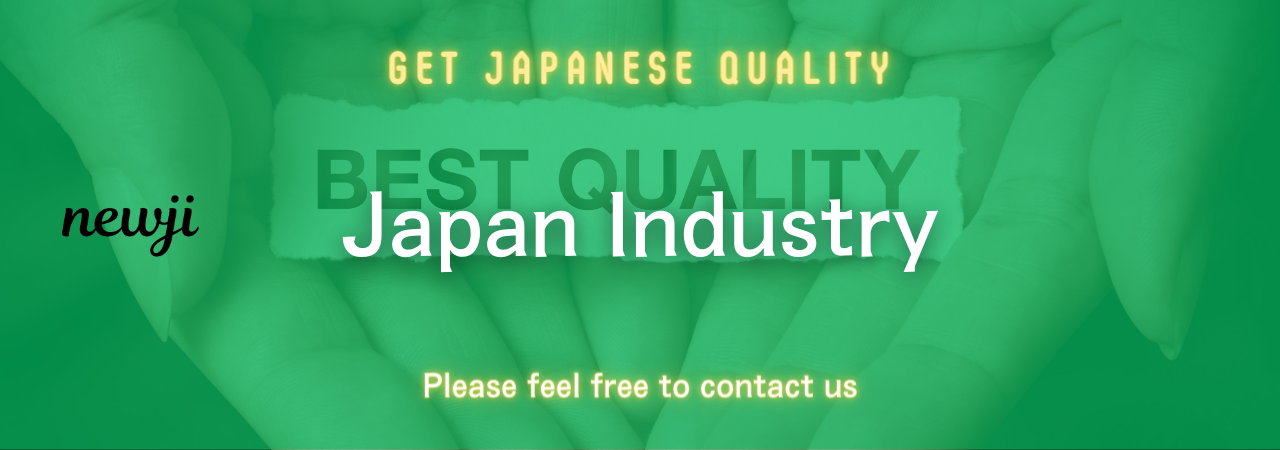
目次
Understanding the Toyota Production System
The Toyota Production System (TPS) is a manufacturing methodology developed by Toyota that focuses on optimizing production efficiency while minimizing waste.
It is renowned for its lean manufacturing principles, which have been adopted by numerous companies worldwide.
Understanding TPS is essential for managers in production technology departments who want to increase productivity and efficiency.
The system is built on two pillars: Just-In-Time (JIT) and Jidoka.
JIT ensures that products are produced in the right quantity and at the right time, eliminating excess inventory.
Jidoka, on the other hand, emphasizes quality control and halts production in the event of a defect, ensuring that quality is built into the manufacturing process itself.
Key Principles of TPS
Implementing TPS in your organization requires an understanding of its key principles.
The system emphasizes continuous improvement, also known as Kaizen, which encourages employees at all levels to suggest improvements.
This fosters a culture of collaboration and innovation.
Another fundamental principle is the elimination of waste, known as Muda in Japanese.
This includes seven types of waste, such as overproduction, waiting, and transportation.
By identifying and eliminating waste, organizations can significantly improve their efficiency and productivity.
Kaizen – The Spirit of Continuous Improvement
Kaizen is at the heart of TPS and refers to the practice of making incremental improvements over time.
It encourages employees to take ownership of their work processes and suggest enhancements.
Managers should create an environment where team members feel comfortable presenting their ideas and should be open to experimentation.
Regularly holding Kaizen events or workshops can help foster a culture of improvement.
Characteristics of Just-In-Time
The Just-In-Time approach is all about producing the necessary items in the required quantity at the exact time they are needed.
This reduces inventory costs and minimizes waste.
Implementing JIT involves setting up a balanced production schedule, reducing set-up times, and synchronizing production with demand.
Utilizing pull systems, such as Kanban, where production is driven by actual demand rather than forecasted demand, is vital to successfully incorporating JIT.
Jidoka – Building in Quality
Jidoka focuses on the automation of quality control, allowing operators to stop the production line if a defect is detected.
This prevents defective products from continuing down the production line.
Automation with a human touch ensures that issues are resolved quickly, maintaining high-quality standards.
Organizations should equip their machines with sensors and alerts to detect problems and train employees to address issues promptly.
Steps to Implement TPS
For production managers eager to implement TPS, a methodical approach is crucial for successful integration.
Begin by assessing the current state of the production line and identifying areas with potential for improvement.
Involve employees from different levels and departments to gain diverse perspectives.
Next, conduct training sessions to ensure everyone understands the principles of TPS and the role they play in the process.
Setting clear objectives will help in tracking progress and measuring the impact of TPS on productivity.
Identify and Eliminate Waste
Start by mapping out the production process to identify areas of waste.
Conduct waste walks to gather information on where inefficiencies lie.
Once identified, develop strategies to eliminate each type of waste.
For example, rearranging the production floor layout could minimize transportation waste by shortening the distance materials need to move.
Streamline Production Processes
After identifying wastes, focus on streamlining production processes.
Implement single-point lessons to reduce setup times and optimize equipment performance.
Standardizing work processes can also help in maintaining consistency and reducing variability in the production line.
Using visual management tools can aid workers in tracking progress and identifying potential bottlenecks.
Empower Employees
One of the strengths of TPS is its emphasis on employee involvement.
Encourage your team to engage in problem-solving activities and provide them with the necessary tools and training.
Facilitating open communication and collaboration is essential for fostering innovation and efficiency within the team.
Overcoming Challenges
Implementing TPS, like any transformative initiative, comes with its set of challenges.
The biggest hurdle is often the cultural shift required within the organization.
This requires patience and commitment from leaders to cultivate a culture that embraces change.
Educate employees on the benefits of TPS and invest in their training to reduce resistance.
Additionally, addressing existing infrastructure limitations, like outdated machinery or rigid production systems, may be necessary for effective TPS implementation.
The Benefits of Implementing TPS
The benefits of TPS reach far beyond increased productivity.
By minimizing waste and improving production efficiency, companies can experience significant cost savings.
Enhanced product quality invariably leads to increased customer satisfaction and loyalty.
Further, TPS empowers employees by involving them in the improvement process, which boosts morale and job satisfaction.
Finally, adopting TPS can provide a competitive advantage as it aligns the organization with industry-best practices.
Conclusion
For managers in production technology departments, effectively implementing the Toyota Production System can yield substantial benefits, including heightened productivity, reduced costs, and improved quality.
By understanding key principles like Just-In-Time, Jidoka, and continuous improvement, managers can foster a culture of efficiency and innovation.
While challenges may arise, maintaining open communication and commitment to the process will lead to successful integration and sustainable growth.
資料ダウンロード
QCD調達購買管理クラウド「newji」は、調達購買部門で必要なQCD管理全てを備えた、現場特化型兼クラウド型の今世紀最高の購買管理システムとなります。
ユーザー登録
調達購買業務の効率化だけでなく、システムを導入することで、コスト削減や製品・資材のステータス可視化のほか、属人化していた購買情報の共有化による内部不正防止や統制にも役立ちます。
NEWJI DX
製造業に特化したデジタルトランスフォーメーション(DX)の実現を目指す請負開発型のコンサルティングサービスです。AI、iPaaS、および先端の技術を駆使して、製造プロセスの効率化、業務効率化、チームワーク強化、コスト削減、品質向上を実現します。このサービスは、製造業の課題を深く理解し、それに対する最適なデジタルソリューションを提供することで、企業が持続的な成長とイノベーションを達成できるようサポートします。
オンライン講座
製造業、主に購買・調達部門にお勤めの方々に向けた情報を配信しております。
新任の方やベテランの方、管理職を対象とした幅広いコンテンツをご用意しております。
お問い合わせ
コストダウンが利益に直結する術だと理解していても、なかなか前に進めることができない状況。そんな時は、newjiのコストダウン自動化機能で大きく利益貢献しよう!
(Β版非公開)