- お役立ち記事
- For managers of production technology departments in the auto parts industry! How to increase production efficiency with laser welding technology
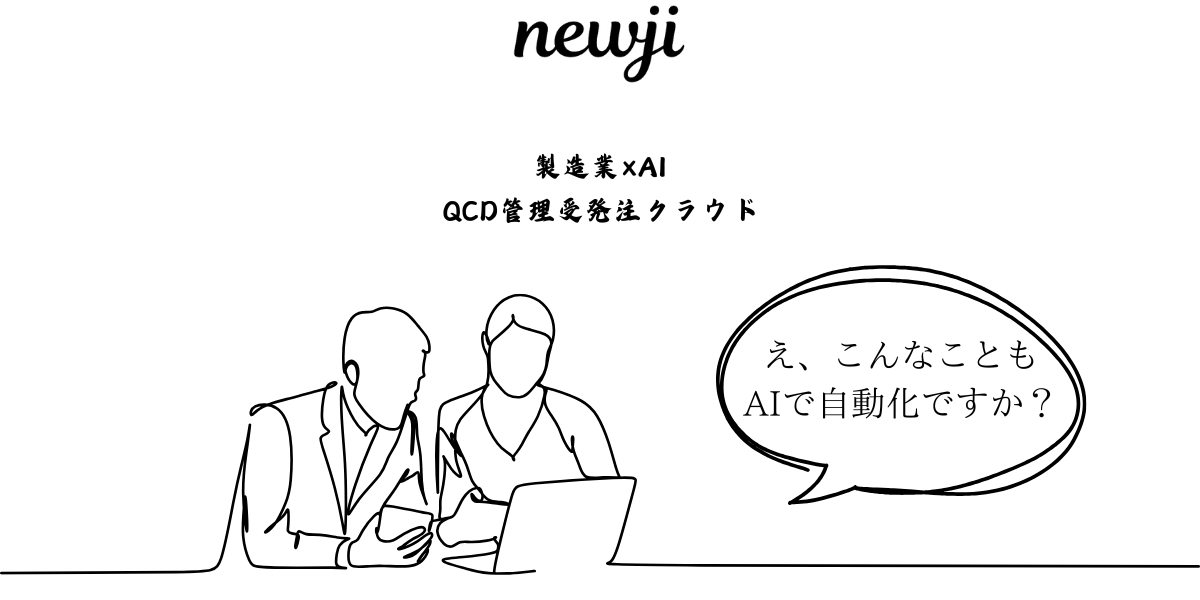
For managers of production technology departments in the auto parts industry! How to increase production efficiency with laser welding technology
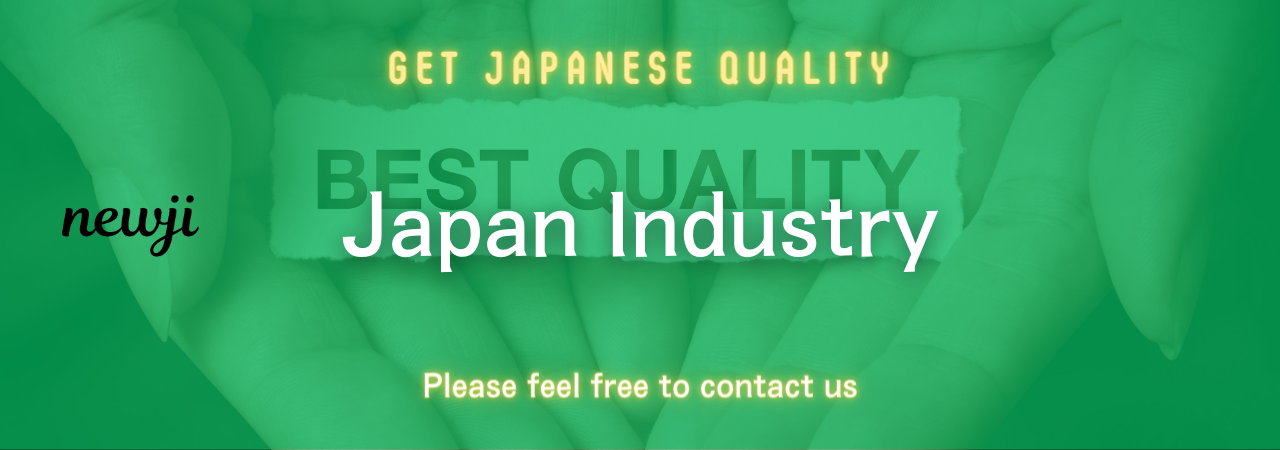
Understanding Laser Welding Technology
Laser welding technology has gained significant attention in the auto parts industry for its ability to enhance production efficiency.
This advanced welding process uses a highly concentrated beam of light to join materials, offering precision and speed that traditional welding methods cannot match.
The technology works by focusing a laser beam on the materials to be welded, melting their surfaces, and fusing them together.
The result is a high-quality weld that is strong, precise, and clean.
The key to understanding laser welding is its ability to rapidly deliver high-energy density to a small area, allowing for rapid heating and melting of the materials being joined.
Types of Laser Welding
There are several types of laser welding techniques used in the auto parts industry, each with its unique advantages:
1. **Conduction Welding**: This technique involves the use of a laser to melt the metal surfaces to join them.
It is ideal for applications where the surfaces are relatively thick, providing strong and durable welds.
2. **Keyhole Welding**: This method is preferred for deep penetration welding.
It creates a keyhole-like cavity through which the laser beam can penetrate deeply, allowing for a strong weld full of integrity.
3. **Hybrid Laser Welding**: This combines laser welding with other techniques, like arc welding, to offer enhanced flexibility in various applications.
It is ideal for situations where single techniques might not achieve the desired results.
Benefits of Laser Welding in Production
Investing in laser welding technology can provide numerous benefits for production efficiency, particularly in the auto parts industry.
Increased Efficiency and Speed
One of the primary advantages of laser welding is its speed.
The process is significantly faster than traditional welding methods, allowing for higher production rates and shorter lead times.
This increase in speed translates directly to improved efficiency, enabling production technology departments to meet tight deadlines and increase output without compromising quality.
Precision and Quality
Laser welding offers unmatched precision, making it ideal for intricate tasks that require exactness.
The concentrated laser beam allows for minimal thermal distortion and reduced heat-affected zones, resulting in cleaner and more aesthetically pleasing welds.
The precision also ensures that the structural integrity of the weld is preserved, reducing the risk of defects and rework.
Cost-Effectiveness
While the initial investment in laser welding technology may be high, the long-term benefits outweigh this cost.
The reduction in material waste, rework, and the need for post-weld cleaning enhances cost efficiency.
Moreover, the speed and precision reduce labor costs by minimizing the need for manual intervention and oversight.
Versatility
Laser welding is versatile and can be used on various materials, including metals and plastics.
This versatility means that the technology can handle a multitude of welding tasks across different automotive components, making it a valuable asset in the manufacturing process.
Implementing Laser Welding Technology
For managers in the production technology departments, implementing laser welding requires careful planning and consideration.
Assessing Needs and Requirements
The first step in implementing laser welding technology is to assess the specific needs and requirements of your production process.
Identify the components that would benefit the most from this technology and determine the types of laser welding most appropriate for your tasks.
Engaging with skilled professionals and conducting a thorough analysis will set a solid foundation for integration.
Choosing the Right Equipment
Selecting the right laser welding equipment is crucial for success.
Technology varies in capabilities and features, so it’s essential to choose machines that align with your production goals and budget.
Consider factors such as power output, control systems, beam quality, and integration capabilities with existing production lines.
Training and Workforce Development
Introducing laser welding technology means that employees will need training to operate and maintain the machinery effectively.
Investing in comprehensive training programs can help workers adjust to the new technology and maximize its benefits.
Additionally, consider hiring skilled operators who have experience with laser welding to bridge any gaps in expertise.
Challenges and Considerations
While laser welding offers many benefits, managers must be aware of potential challenges.
Initial Investment and Maintenance Costs
The initial cost of purchasing and installing laser welding equipment can be substantial.
Additionally, regular maintenance and occasional repairs can add to the expenses.
Therefore, it is essential to budget properly and plan for these costs to ensure a seamless transition.
Technical Complexity
Laser welding technology is technically complex.
This complexity may present a learning curve for employees and may require ongoing support and training from manufacturers or technical consultants.
Ensuring continuous support and knowledge transfer is necessary to overcome these technical hurdles.
Integration with Existing Systems
Integrating laser welding technology with existing production lines can be challenging.
It requires careful planning to ensure that the new systems are compatible with current workflows and that disruptions to production are minimized.
Collaboration with equipment suppliers who have experience in integration can make this process smoother.
Conclusion
Laser welding technology offers significant improvements in production efficiency for the auto parts industry.
Its speed, precision, cost-effectiveness, and versatility make it a valuable asset for production technology departments.
Managers looking to improve their production efficiency should consider the implementation of laser welding technology.
Despite the challenges, the benefits make it worth the investment.
By understanding the principles, benefits, and necessary steps for implementation, auto parts manufacturers can harness the power of laser welding and take their production efficiency to the next level.
資料ダウンロード
QCD調達購買管理クラウド「newji」は、調達購買部門で必要なQCD管理全てを備えた、現場特化型兼クラウド型の今世紀最高の購買管理システムとなります。
ユーザー登録
調達購買業務の効率化だけでなく、システムを導入することで、コスト削減や製品・資材のステータス可視化のほか、属人化していた購買情報の共有化による内部不正防止や統制にも役立ちます。
NEWJI DX
製造業に特化したデジタルトランスフォーメーション(DX)の実現を目指す請負開発型のコンサルティングサービスです。AI、iPaaS、および先端の技術を駆使して、製造プロセスの効率化、業務効率化、チームワーク強化、コスト削減、品質向上を実現します。このサービスは、製造業の課題を深く理解し、それに対する最適なデジタルソリューションを提供することで、企業が持続的な成長とイノベーションを達成できるようサポートします。
オンライン講座
製造業、主に購買・調達部門にお勤めの方々に向けた情報を配信しております。
新任の方やベテランの方、管理職を対象とした幅広いコンテンツをご用意しております。
お問い合わせ
コストダウンが利益に直結する術だと理解していても、なかなか前に進めることができない状況。そんな時は、newjiのコストダウン自動化機能で大きく利益貢献しよう!
(Β版非公開)