- お役立ち記事
- For managers of production technology departments in the plastic molding industry! Manufacture of complex-shaped parts using multi-axis injection molding machines
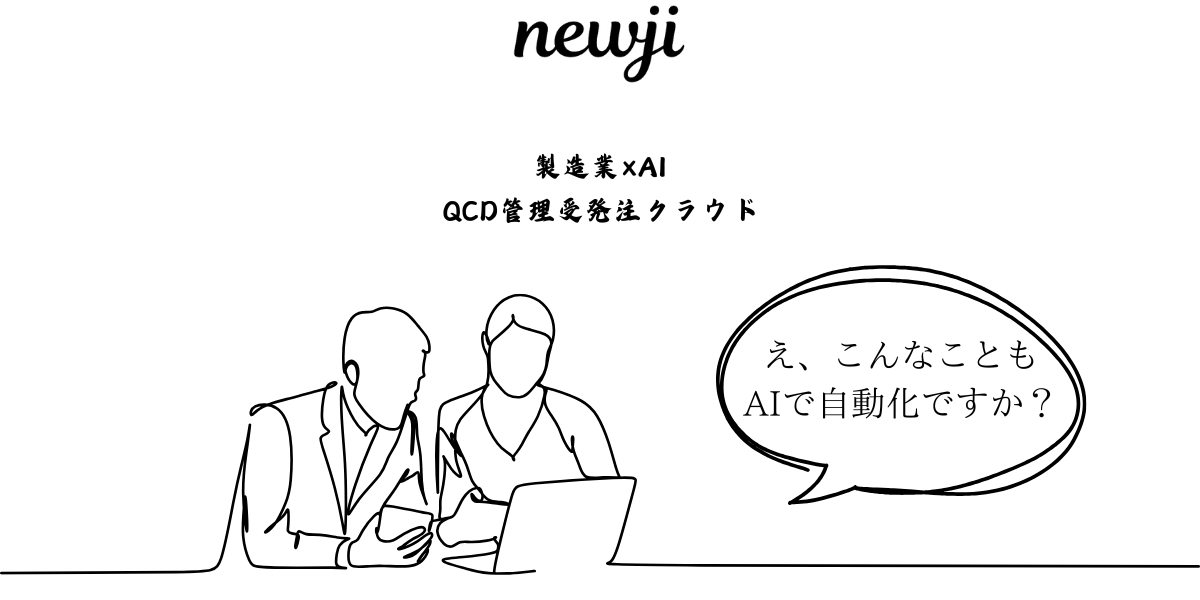
For managers of production technology departments in the plastic molding industry! Manufacture of complex-shaped parts using multi-axis injection molding machines
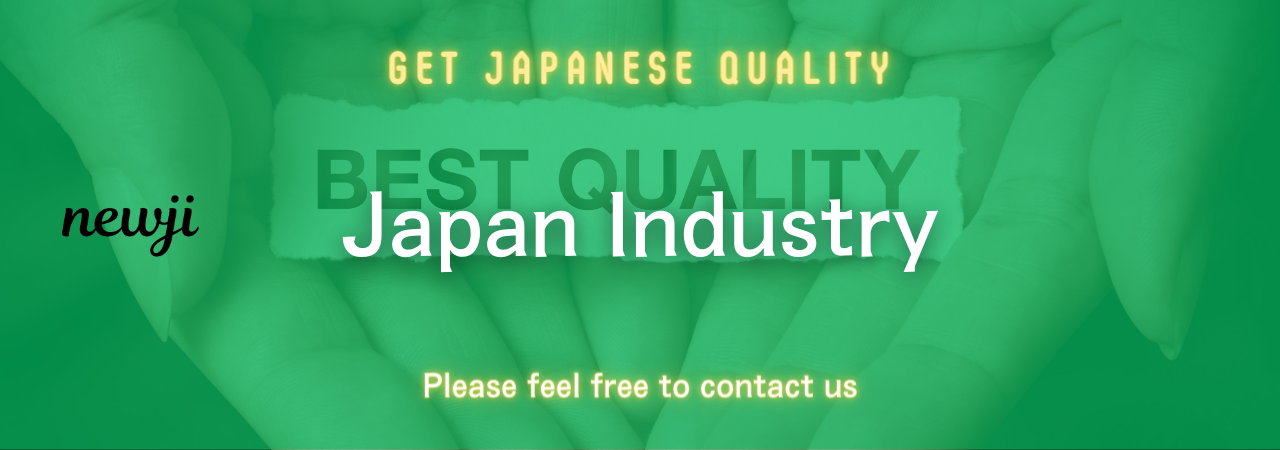
目次
Understanding Multi-Axis Injection Molding Machines
In the plastic molding industry, the demand for complex-shaped parts is continuously growing.
One of the key technologies enabling the production of these intricate designs is the multi-axis injection molding machine.
These machines allow for precise and efficient manufacturing, offering significant advantages over traditional molding techniques.
Multi-axis injection molding machines operate with more than the standard X, Y, and Z axes, allowing for movement and rotation in additional directions.
This capability enables the creation of parts with complex geometries, intricate details, and unique design features that would be challenging or impossible to achieve using conventional methods.
Benefits of Multi-Axis Molding
The adoption of multi-axis injection molding machines comes with several benefits.
Firstly, these machines provide enhanced flexibility in design, allowing for more freedom in creating innovative products.
Manufacturers can produce parts with undercuts, intricate surface textures, and integrated components, all in a single molding cycle.
Another advantage is the potential for reducing manufacturing costs.
By combining multiple components into a single complex part, businesses can decrease assembly times and minimize the risk of errors associated with assembling multiple pieces.
Additionally, fewer tools and molds are needed, resulting in cost savings.
Moreover, multi-axis injection molding contributes to improved product quality.
The precise control over each axis ensures consistent dimensions and high accuracy, reducing variability in the final product.
This precision is particularly beneficial in industries where tolerances and specifications are stringent, such as automotive and medical device manufacturing.
Applications of Multi-Axis Injection Molding
The versatility of multi-axis injection molding machines makes them suitable for a wide range of applications.
In the automotive industry, manufacturers use these machines to produce parts with complex geometries, such as dashboards and functional interior components.
The capability to mold around inserts or create integrated hinges and fasteners enhances the functionality and aesthetics of automotive parts.
In the medical sector, precision is paramount, and multi-axis molding is ideal for producing components such as surgical instruments and diagnostic devices.
These machines can achieve the tight tolerances required for medical applications, ensuring the performance and reliability of critical components.
The consumer electronics industry also benefits from multi-axis injection molding technology.
Manufacturers can create components with intricate designs and integrated features, such as connectors and enclosures, improving both the functionality and visual appeal of electronic devices.
Challenges and Considerations
Despite the benefits, there are challenges associated with multi-axis injection molding that managers in production technology departments must consider.
One of the primary challenges is the complexity of the machines themselves.
Operating and maintaining multi-axis injection molding machines require skilled personnel with expertise in both mechanical and software aspects.
Training staff and ensuring they have the necessary skills is vital to maximizing the efficiency of these machines.
Another consideration is the initial cost.
Multi-axis injection molding machines often come with a higher price tag compared to traditional molding equipment.
Managers need to weigh the long-term benefits and potential cost savings against the upfront investment when deciding whether to adopt this technology.
Additionally, the design process becomes more intricate when using multi-axis molding.
Engineers and designers need to account for the additional axes in their models, potentially increasing the complexity of CAD files and simulations.
Collaborating closely with design teams helps ensure that the advantages of multi-axis molding are fully realized without compromising the integrity of the design.
Future of Multi-Axis Molding in the Plastic Industry
As technology continues to advance, the capabilities of multi-axis injection molding machines are expected to grow even further.
Innovations such as increased automation, improved data integration, and advanced materials are on the horizon.
These developments will likely make multi-axis molding more accessible and beneficial for an even broader range of industries.
The integration of smart manufacturing technologies and the Internet of Things (IoT) could revolutionize how these machines are operated and maintained.
Predictive maintenance and real-time monitoring could lead to higher efficiency, reduced downtime, and better resource management.
For managers in the plastic molding industry, staying up-to-date with the latest developments in multi-axis injection molding is crucial.
Continuous learning and adaptation will ensure that their production facilities can meet the evolving demands for complex-shaped parts and maintain a competitive edge.
Conclusion
In summary, multi-axis injection molding machines offer numerous advantages for the production of complex-shaped parts.
The flexibility, cost savings, and improved product quality they provide make them a valuable asset in the plastic molding industry.
Despite the challenges they present, the potential benefits often outweigh the downsides, making them an enticing option for forward-thinking production technology departments.
By understanding the applications, challenges, and future trends, managers can make informed decisions about integrating multi-axis injection molding into their production processes, ensuring their operations remain competitive and efficient in a dynamic market.
資料ダウンロード
QCD調達購買管理クラウド「newji」は、調達購買部門で必要なQCD管理全てを備えた、現場特化型兼クラウド型の今世紀最高の購買管理システムとなります。
ユーザー登録
調達購買業務の効率化だけでなく、システムを導入することで、コスト削減や製品・資材のステータス可視化のほか、属人化していた購買情報の共有化による内部不正防止や統制にも役立ちます。
NEWJI DX
製造業に特化したデジタルトランスフォーメーション(DX)の実現を目指す請負開発型のコンサルティングサービスです。AI、iPaaS、および先端の技術を駆使して、製造プロセスの効率化、業務効率化、チームワーク強化、コスト削減、品質向上を実現します。このサービスは、製造業の課題を深く理解し、それに対する最適なデジタルソリューションを提供することで、企業が持続的な成長とイノベーションを達成できるようサポートします。
オンライン講座
製造業、主に購買・調達部門にお勤めの方々に向けた情報を配信しております。
新任の方やベテランの方、管理職を対象とした幅広いコンテンツをご用意しております。
お問い合わせ
コストダウンが利益に直結する術だと理解していても、なかなか前に進めることができない状況。そんな時は、newjiのコストダウン自動化機能で大きく利益貢献しよう!
(Β版非公開)