- お役立ち記事
- For managers of project management departments in the auto parts manufacturing industry! How to make your project successful with critical chain
For managers of project management departments in the auto parts manufacturing industry! How to make your project successful with critical chain
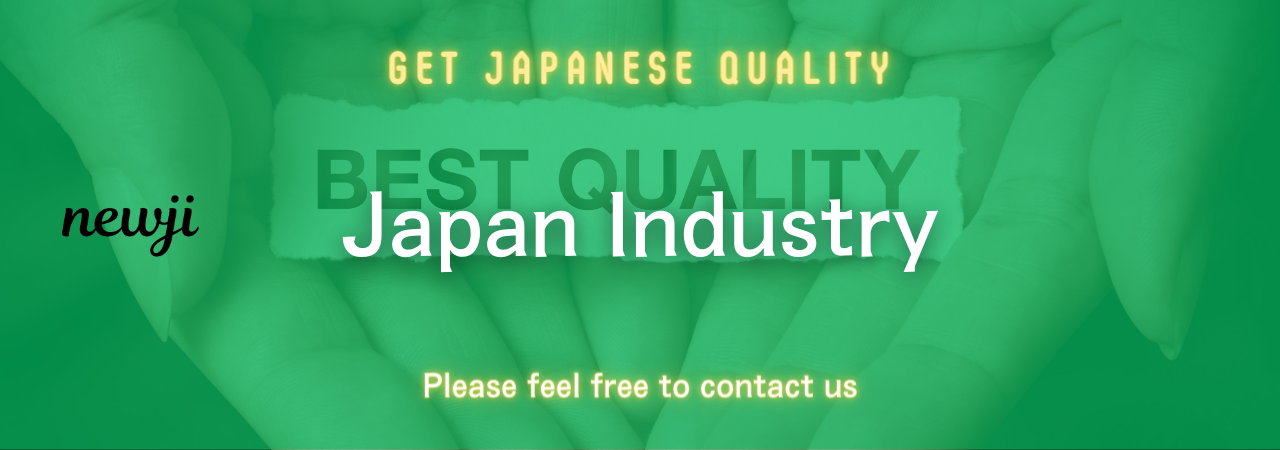
目次
Understanding Critical Chain Project Management
Critical Chain Project Management (CCPM) is a method used extensively in the auto parts manufacturing industry to ensure timely project completion while optimizing resources.
It differs from traditional project management approaches by focusing on resource constraints and minimizing multitasking to enhance project flow.
CCPM provides a structured approach to managing tasks and resources efficiently, which is crucial in the competitive landscape of auto parts manufacturing.
By focusing on buffer management and utilizing a project network diagram, managers can prevent delays and sustain momentum across different stages of production.
Understanding the fundamentals of CCPM can significantly improve project outcomes, reduce lead times, and increase overall efficiency.
Key Principles of Critical Chain Project Management
The critical chain is the longest path in a project network diagram that determines the shortest possible project duration.
This is based on resource availability rather than just task dependencies.
Here are some key principles:
1. **Resource Optimization**: CCPM acknowledges the reality of limited resources and seeks to optimize their utilization.
Managers must identify critical resources and ensure they are used effectively to maintain project flow.
2. **Buffer Management**: Buffers are strategically placed at points in the project plan to absorb uncertainties and prevent delays.
These include project, feeding, and resource buffers.
Monitoring buffer consumption helps managers anticipate potential delays and take corrective actions.
3. **Single-task Focus**: Multitasking can lead to inefficiencies and delays.
CCPM encourages team members to focus on completing one task at a time before moving to the next.
This approach minimizes task switching and enhances productivity.
4. **Task Prioritization**: Managers need to identify priority tasks and ensure they are started promptly.
This requires clear communication and coordination among team members to avoid bottlenecks.
Implementing Critical Chain in Auto Parts Manufacturing
Deploying CCPM in the auto parts manufacturing industry involves several strategic steps and tools.
Here’s how managers can get started:
Step 1: Define the Project Scope and Objectives
Before implementing CCPM, it is crucial to define the project’s scope and objectives clearly.
Understand what needs to be achieved and set realistic goals and deliverables.
Step 2: Create a Project Network Diagram
A project network diagram outlines the sequence of tasks and the interdependencies between them.
Identify the critical chain by considering both task durations and resource constraints.
Step 3: Identify Constraints and Resource Dependencies
Identify constraints in the form of limited resources or potential bottlenecks.
Analyze resource dependencies to ensure that the critical chain can be executed smoothly without excessive idle time.
Step 4: Implement Buffer Management
Establish appropriate buffers (project, feeding, and resource buffers) to manage uncertainties and ensure smooth progress.
Buffers act as protection against unforeseen delays, allowing for timely project completion.
Step 5: Promote a Single-Task Focus
Encourage team members to concentrate on one task at a time.
This focus minimizes distractions and enhances work quality and efficiency.
Step 6: Monitor and Adjust
Regularly track project progress and buffer consumption.
Ensure timely communication among team members and stakeholders to resolve issues promptly.
Adjust plans as needed to address unforeseen challenges or changes in resource availability.
Benefits of Using Critical Chain in Auto Parts Manufacturing
Employing CCPM yields numerous benefits that enhance the overall productivity of an auto parts manufacturing project.
Improved Project Delivery Times
CCPM’s focus on optimizing resources and eliminating multitasking leads to faster project completion.
Buffer management aids in mitigating delays, resulting in reduced lead times.
Enhanced Team Productivity
By eliminating multitasking and encouraging a single-task focus, team productivity improves.
Individuals can concentrate fully on their tasks without distractions or interruptions.
Efficient Resource Utilization
CCPM ensures efficient utilization of resources by prioritizing tasks based on their criticality.
This approach avoids overloading resources and reduces the likelihood of bottlenecks.
Risk Mitigation
Strategic buffer placement provides a safety net against unforeseen delays or problems, reducing project risks.
Managers can proactively address potential issues, ensuring smoother project flow.
Challenges and Considerations in CCPM Implementation
While CCPM offers many benefits, it also presents certain challenges that managers need to address:
Resistance to Change
Transitioning from traditional project management methods to CCPM can meet resistance from team members.
Ensure proper training and clear communication to help everyone understand the benefits.
Accurate Estimation
Accurate estimation of task durations and resource requirements is essential for effective CCPM implementation.
Inaccurate estimates can lead to insufficient buffers and potential delays.
Continuous Monitoring
Managers need to consistently monitor buffer consumption and critical resource availability.
This requires a dedicated effort to ensure timely adjustments and decision-making during the project lifecycle.
By understanding and addressing these challenges, managers can successfully integrate CCPM into their project management practices.
Through effective implementation, they can enhance efficiency and ensure timely delivery of projects in the auto parts manufacturing industry.
資料ダウンロード
QCD調達購買管理クラウド「newji」は、調達購買部門で必要なQCD管理全てを備えた、現場特化型兼クラウド型の今世紀最高の購買管理システムとなります。
ユーザー登録
調達購買業務の効率化だけでなく、システムを導入することで、コスト削減や製品・資材のステータス可視化のほか、属人化していた購買情報の共有化による内部不正防止や統制にも役立ちます。
NEWJI DX
製造業に特化したデジタルトランスフォーメーション(DX)の実現を目指す請負開発型のコンサルティングサービスです。AI、iPaaS、および先端の技術を駆使して、製造プロセスの効率化、業務効率化、チームワーク強化、コスト削減、品質向上を実現します。このサービスは、製造業の課題を深く理解し、それに対する最適なデジタルソリューションを提供することで、企業が持続的な成長とイノベーションを達成できるようサポートします。
オンライン講座
製造業、主に購買・調達部門にお勤めの方々に向けた情報を配信しております。
新任の方やベテランの方、管理職を対象とした幅広いコンテンツをご用意しております。
お問い合わせ
コストダウンが利益に直結する術だと理解していても、なかなか前に進めることができない状況。そんな時は、newjiのコストダウン自動化機能で大きく利益貢献しよう!
(Β版非公開)