- お役立ち記事
- For managers of quality control departments in the slim bottle manufacturing industry! Manufacturing technology to ensure thickness and pressure resistance
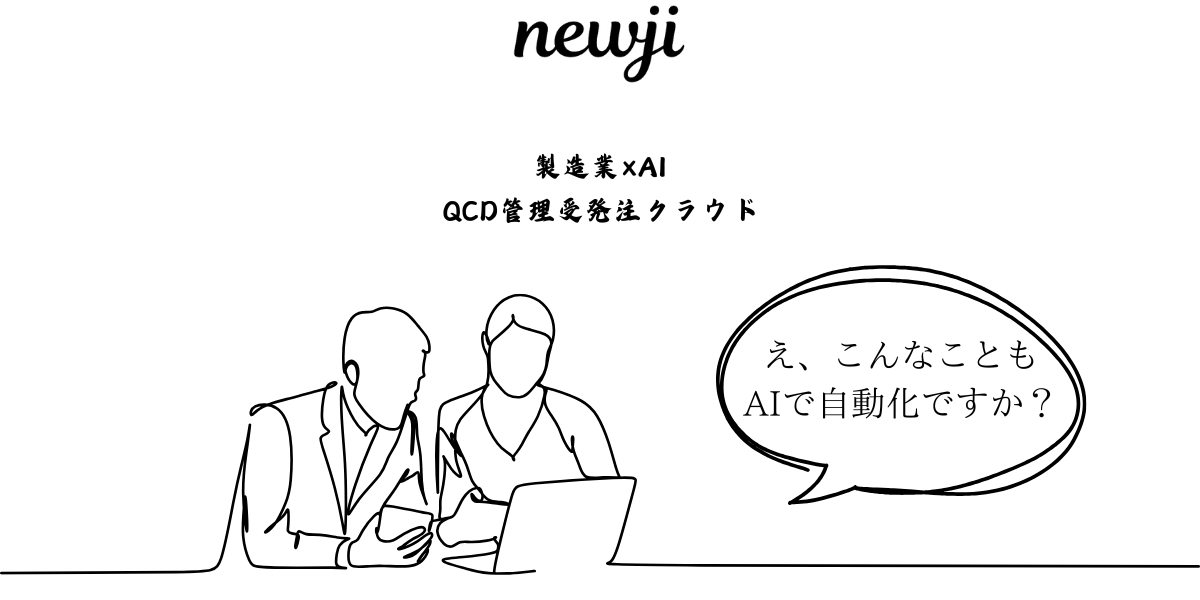
For managers of quality control departments in the slim bottle manufacturing industry! Manufacturing technology to ensure thickness and pressure resistance
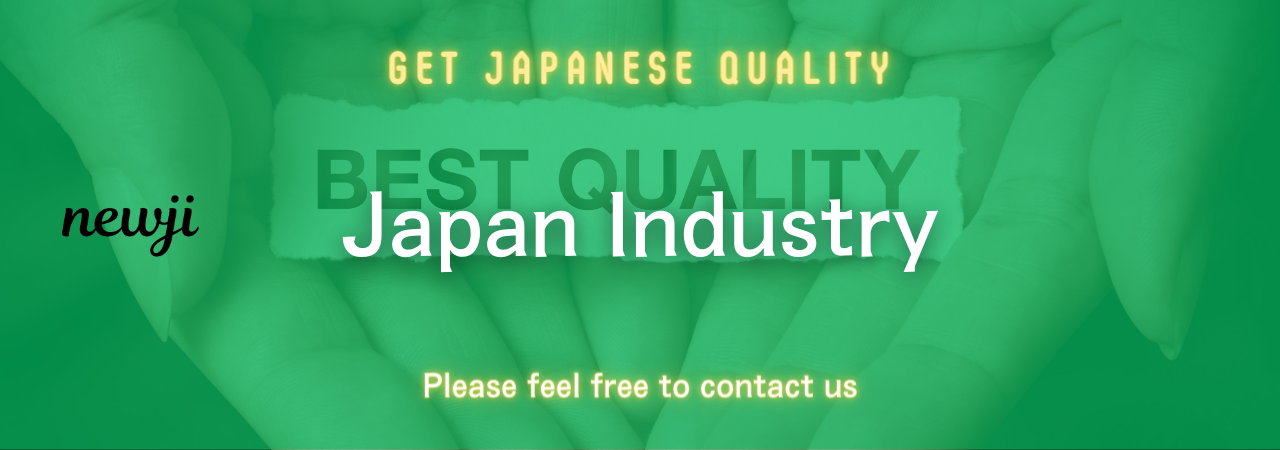
目次
Understanding the Need for Quality Control in Slim Bottle Manufacturing
In recent years, the demand for slim bottles has significantly increased due to their sleek design and convenience.
Their popularity can be seen in various sectors, from the beverage industry to personal care products.
However, manufacturing these bottles requires an adherence to quality standards to ensure they are safe, durable, and meet consumer expectations.
The challenges faced by quality control departments in the slim bottle manufacturing sector are unique.
This is because slim bottles must meet specific parameters of thickness and pressure resistance, ensuring they perform well under different conditions.
Achieving such standards requires a comprehensive understanding of manufacturing technology and quality control processes.
The Importance of Thickness in Slim Bottle Manufacturing
Thickness may seem like a minor detail, but it is crucial in determining a bottle’s strength and durability.
For instance, too thin walls can lead to breakage or deformation under pressure, while excessively thick bottles may not offer the sleek and portable appeal that consumers desire.
Hence, achieving the right balance is key.
Quality control managers must focus on uniform thickness distribution throughout the bottle.
This ensures structural integrity and prevents weak spots that can compromise the bottle’s performance in holding liquids.
Modern manufacturing technologies allow for precise control over thickness, providing detailed monitoring at all stages of production.
This helps in maintaining consistency across large production batches.
Technological Solutions for Thickness Monitoring
To manage thickness efficiently, several technological solutions are employed in the manufacturing process.
Advanced techniques such as extrusion blow molding and injection stretch blow molding are common in the industry.
These methods not only help in controlling the thickness but also in achieving the desired shape and size.
Furthermore, non-destructive testing methods like ultrasound, X-ray inspection, and laser micrometry enable quality control teams to measure thickness without compromising the integrity of the bottle.
These technologies provide real-time feedback, allowing for adjustments to be made swiftly, ensuring that every product leaving the production line is up to standard.
Understanding Pressure Resistance in Slim Bottles
Pressure resistance is another vital aspect of slim bottle manufacturing.
Bottles must withstand internal pressures from the contents they hold, such as carbonated beverages or products requiring airtight sealing.
Failure to meet pressure resistance standards could lead to catastrophic product failures, affecting consumer safety and brand reputation.
Quality control departments need to test bottles at various stages of production to ensure they meet required pressure tolerances.
This testing involves simulating pressure conditions bottles will face in real-world scenarios and identifying any weaknesses before products reach the customer.
Innovative Testing Methods for Pressure Resistance
Various innovative methods are employed to test and ensure adequate pressure resistance.
One common approach is the use of pressure testing machines that simulate real-life pressure scenarios.
These machines can apply a wide range of pressures to test the bottle’s strength and resilience.
Additionally, finite element analysis (FEA) is an advanced computational technique used to predict how a product will react to external forces.
By modeling the bottle and running simulations, manufacturers can identify potential stress points and optimize designs to enhance pressure resistance.
The Role of Material Selection in Ensuring Quality
Material selection plays a crucial role in the quality of slim bottles.
The choice of materials affects both thickness and pressure resistance of the bottle.
Manufacturers typically use high-density polyethylene (HDPE) or polyethylene terephthalate (PET) for their excellent strength-to-weight ratios.
However, the selection of materials goes beyond just their physical properties.
Environmental factors such as recyclability and the carbon footprint of production processes must also be considered in response to growing sustainability concerns.
Enhancing Quality through Material Innovations
In recent years, materials science has seen significant advancements, leading to the development of new polymers and composites enhancing both the performance and sustainability of slim bottles.
For example, bio-based PET is an eco-friendly alternative that reduces reliance on fossil resources while maintaining excellent mechanical properties.
Moreover, incorporating additives and fillers into plastic materials can enhance properties like impact resistance and flexibility, meeting specific requirements without compromising on aesthetics or functionality.
Implementing a Robust Quality Control System
A robust quality control system is essential for managing the complexities of slim bottle manufacturing.
It ensures adherence to specified standards and reduces the risk of defects.
Implementing a thorough quality management system involves setting clear guidelines, continuous monitoring, and regular audits to identify potential flaws and areas for improvement.
Automation also plays a key role in achieving consistent quality.
Automated inspection systems with cameras and sensors can detect defects or deviations in thickness and pressure resistance rapidly and accurately, allowing for immediate corrective actions.
Training and Development for Quality Control Teams
Investing in the skill development of quality control teams is paramount.
Regular training on the latest technologies and methodologies equips them with the knowledge required to handle complex quality issues effectively.
By keeping abreast of industry trends and best practices, quality control personnel can contribute to innovations in manufacturing processes, thereby enhancing product quality and customer satisfaction.
In conclusion, quality control departments in the slim bottle manufacturing industry have a significant responsibility to ensure products meet high standards of thickness and pressure resistance.
By understanding the nuances of manufacturing technology, embracing innovative testing methods, selecting appropriate materials, and implementing comprehensive quality systems, they can maintain the robustness and reliability of their products, thereby upholding their company’s reputation and consumer trust.
資料ダウンロード
QCD調達購買管理クラウド「newji」は、調達購買部門で必要なQCD管理全てを備えた、現場特化型兼クラウド型の今世紀最高の購買管理システムとなります。
ユーザー登録
調達購買業務の効率化だけでなく、システムを導入することで、コスト削減や製品・資材のステータス可視化のほか、属人化していた購買情報の共有化による内部不正防止や統制にも役立ちます。
NEWJI DX
製造業に特化したデジタルトランスフォーメーション(DX)の実現を目指す請負開発型のコンサルティングサービスです。AI、iPaaS、および先端の技術を駆使して、製造プロセスの効率化、業務効率化、チームワーク強化、コスト削減、品質向上を実現します。このサービスは、製造業の課題を深く理解し、それに対する最適なデジタルソリューションを提供することで、企業が持続的な成長とイノベーションを達成できるようサポートします。
オンライン講座
製造業、主に購買・調達部門にお勤めの方々に向けた情報を配信しております。
新任の方やベテランの方、管理職を対象とした幅広いコンテンツをご用意しております。
お問い合わせ
コストダウンが利益に直結する術だと理解していても、なかなか前に進めることができない状況。そんな時は、newjiのコストダウン自動化機能で大きく利益貢献しよう!
(Β版非公開)