- お役立ち記事
- For new leaders in process management departments in chemical manufacturing industries! Efficient reaction management using fluidized bed reaction technology
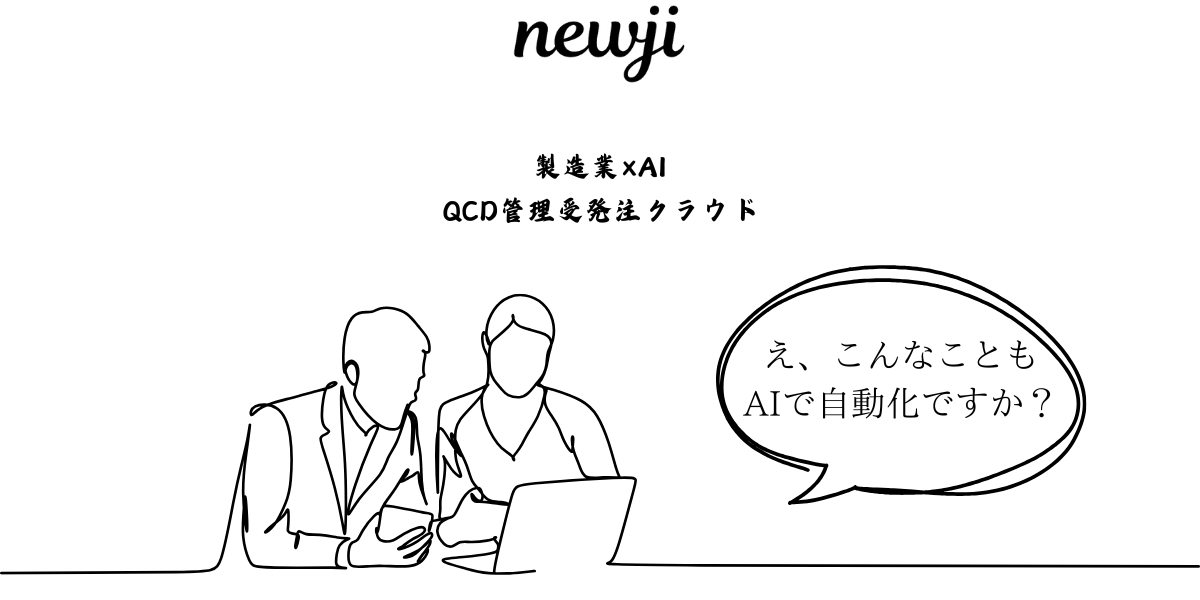
For new leaders in process management departments in chemical manufacturing industries! Efficient reaction management using fluidized bed reaction technology
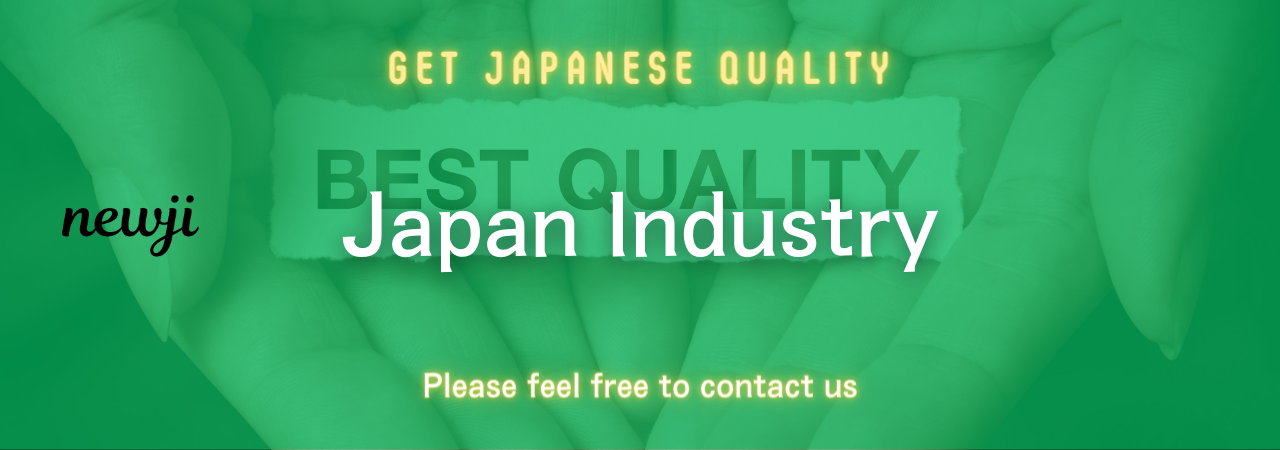
目次
Understanding Fluidized Bed Reaction Technology
In the ever-evolving world of chemical manufacturing, staying ahead requires leveraging innovative technologies.
One such breakthrough is fluidized bed reaction technology.
For new leaders in process management departments, understanding this technology can significantly impact the efficiency and effectiveness of your operations.
Fluidized bed reaction technology involves the suspension of solid particles through the upward flow of gas or liquid.
This process creates a fluid-like state, allowing for better contact between reactants and catalysts.
As a result, chemical reactions become more uniform and efficient.
The Advantages of Fluidized Bed Reactors
Fluidized bed reactors offer several advantages over traditional fixed-bed or batch reactors.
First and foremost, they provide excellent mixing, ensuring that all reactants are in contact with each other.
This uniformity leads to more consistent product quality.
Another advantage is the enhanced heat and mass transfer capabilities.
Fluidized beds maintain uniform temperature distribution, reducing the risk of hot spots that can result in undesired side reactions or equipment damage.
Additionally, this technology allows for continuous operation, increasing throughput and reducing downtime.
Implementing Fluidized Bed Technology
For new leaders in process management, implementing fluidized bed technology might seem daunting.
However, with careful planning and a clear understanding of the process, the transition can be smooth and rewarding.
Step 1: Conduct a Feasibility Study
Before diving into any new technology, it’s crucial to assess its feasibility within your specific operation.
Analyze your current processes and determine where fluidized bed reactors can be most beneficial.
Consider factors such as the type of reactions, production volumes, and desired product quality.
Step 2: Choose the Right Equipment
Selecting the appropriate equipment is vital for the successful implementation of fluidized bed technology.
Different reactors are designed for specific operations, such as catalytic cracking or gasification.
Consult with equipment suppliers and engineers to determine the best fit for your processes.
Step 3: Train Your Team
Introducing new technology requires adequate training for your team.
Ensure that your operators and technicians understand the principles of fluidized bed reaction technology.
Provide comprehensive training on the operation and safety measures related to the new equipment.
This will not only ensure smooth operation but also instill confidence and competence in your team.
Step 4: Optimize Your Process
Once the equipment is in place, it’s vital to optimize the process for maximum efficiency.
Monitor key parameters such as temperature, pressure, and fluidization velocity.
Make adjustments as needed to achieve the desired reaction outcomes.
Utilize process modeling and simulation tools to fine-tune your operations.
Challenges and Considerations
While fluidized bed reactors offer numerous benefits, they come with their own set of challenges.
Understanding these challenges is crucial for new leaders in the process management department.
One significant challenge is the risk of particle attrition and erosion.
As solid particles are suspended within the reactor, they can collide and break down over time.
This can lead to reduced efficiency and product quality.
Regular monitoring and maintenance are vital to address these issues.
Additionally, fluidized bed reactors can be more energy-intensive than other types.
It’s essential to weigh the energy costs against the productivity gains and consider energy-saving strategies.
Conclusion
For new leaders in the chemical manufacturing industry, mastering fluidized bed reaction technology can elevate your process management skills to the next level.
The advantages of improved mixing, enhanced heat and mass transfer, and continuous operation outweigh the initial challenges.
By conducting a feasibility study, selecting the right equipment, providing comprehensive training, and optimizing your process, you can successfully implement this innovative technology.
Embrace the challenges and leverage fluidized bed reactors to achieve more efficient reaction management in your chemical manufacturing operations.
資料ダウンロード
QCD調達購買管理クラウド「newji」は、調達購買部門で必要なQCD管理全てを備えた、現場特化型兼クラウド型の今世紀最高の購買管理システムとなります。
ユーザー登録
調達購買業務の効率化だけでなく、システムを導入することで、コスト削減や製品・資材のステータス可視化のほか、属人化していた購買情報の共有化による内部不正防止や統制にも役立ちます。
NEWJI DX
製造業に特化したデジタルトランスフォーメーション(DX)の実現を目指す請負開発型のコンサルティングサービスです。AI、iPaaS、および先端の技術を駆使して、製造プロセスの効率化、業務効率化、チームワーク強化、コスト削減、品質向上を実現します。このサービスは、製造業の課題を深く理解し、それに対する最適なデジタルソリューションを提供することで、企業が持続的な成長とイノベーションを達成できるようサポートします。
オンライン講座
製造業、主に購買・調達部門にお勤めの方々に向けた情報を配信しております。
新任の方やベテランの方、管理職を対象とした幅広いコンテンツをご用意しております。
お問い合わせ
コストダウンが利益に直結する術だと理解していても、なかなか前に進めることができない状況。そんな時は、newjiのコストダウン自動化機能で大きく利益貢献しよう!
(Β版非公開)