- お役立ち記事
- For operators in the glass product manufacturing industry! A thorough guide to float glass molding conditions and quality control
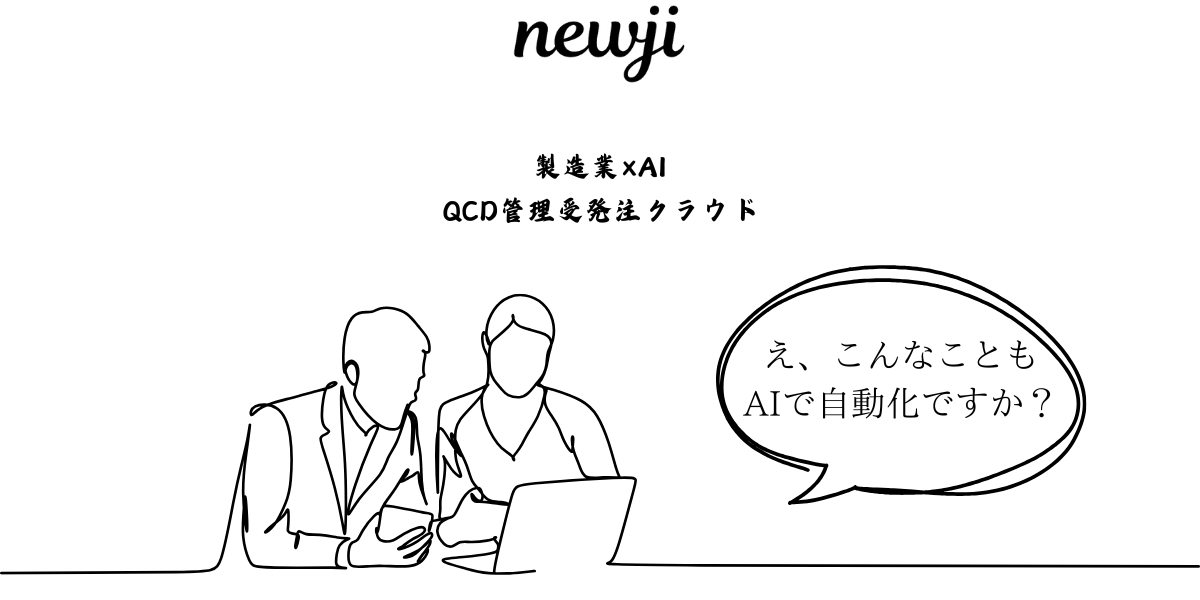
For operators in the glass product manufacturing industry! A thorough guide to float glass molding conditions and quality control
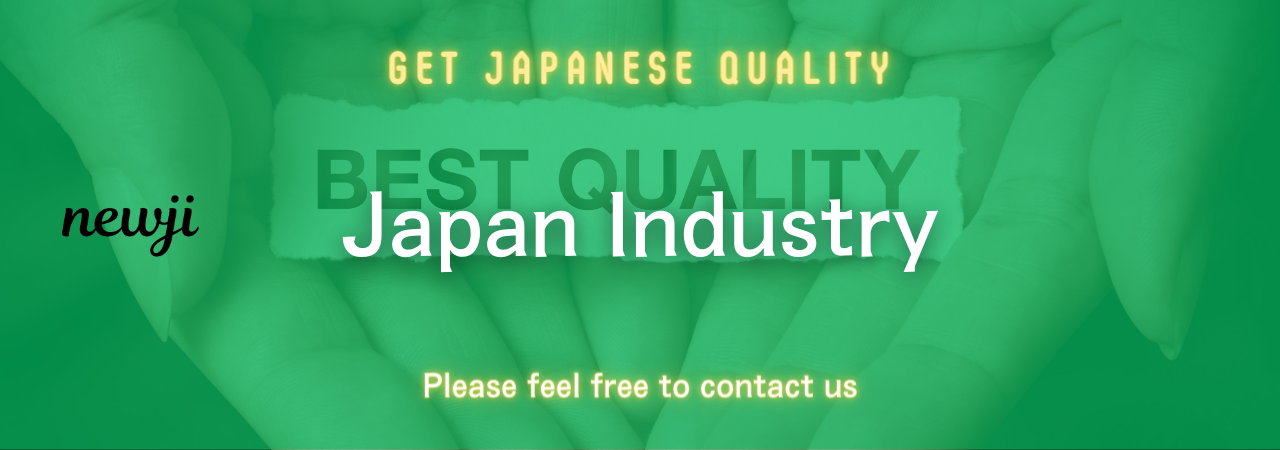
目次
Understanding the Float Glass Process
The float glass process is a fascinating and intricate method widely used in the glass product manufacturing industry.
It involves creating large, flat sheets of glass, which are essential for various applications like automobile windows, building facades, and even decorative items.
To ensure high-quality outputs, manufacturers must carefully control each step of the process.
Float glass is produced by melting raw materials, primarily silica sand, soda ash, and limestone, in a furnace at temperatures around 1700°C.
Once molten, the glass is poured onto a bath of molten tin, forming a perfectly flat sheet due to its high surface tension.
This innovative technique was pioneered in the 1950s and has since become the standard for manufacturing flat glass.
Key Stages in Float Glass Manufacturing
The process begins with the preparation of raw materials.
High-purity silica sand forms the base, while soda ash lowers the melting temperature, and limestone enhances the stability of the finished glass.
Precise measurements ensure consistency in the final product.
Once the ingredients are mixed, they are fed into a furnace where they melt together to form a homogenous liquid.
Maintaining the correct temperature is crucial here; otherwise, defects such as bubbles or distortions can occur.
The molten glass then advances onto a floating bath of molten tin.
Here, the glass spreads out and attains a uniform thickness, thanks to controlled conditions and the properties of molten tin.
Both the glass and tin are kept at high temperatures to prevent solidification too soon.
As the glass continues down the line, it gradually cools in a controlled environment known as an annealing lehr.
This area allows the glass to slowly cool and relieve any internal stresses.
Sudden temperature changes can lead to fragile glass prone to breaking under minimal stress.
Optimizing Molding Conditions
For operators, understanding the perfect molding conditions is vital to producing high-quality float glass.
Each stage presents unique challenges that require careful monitoring and adjustments.
Temperature Regulation
Temperature is a critical factor throughout the process.
From the initial melting of raw materials to the cooling phase, precise temperature control ensures that the glass remains defect-free.
In the furnace, temperatures must be consistently high enough to fully melt the raw materials.
Inadequate melting can result in a cloudy or discolored product, which may be unsuitable for use.
When the molten glass spreads over the tin bath, consistent temperature helps achieve the desired thickness and smooth finish.
Operators need to monitor and adjust the temperature to retain these qualities.
The annealing lehr’s temperature is controlled to allow gradual cooling.
This prevents the formation of stresses within the glass, which could lead to breakage or deformation during handling or further processing.
Maintaining Cleanliness
Since any impurities can compromise the quality of the glass, maintaining cleanliness at every stage is essential.
Dust, dirt, or contamination can introduce flaws into the glass surface, rendering it unusable in applications that demand precision.
Regular equipment maintenance and cleaning protocols help minimize these contaminants.
Filters in the air system and regular inspections of the tin bath can significantly reduce the risk of debris entering the glass stream.
Thickness Consistency
The float glass process is renowned for producing glass with uniform thickness, but achieving this consistently is a challenge.
Operators need to ensure that the glass spreads evenly across the bath and that the cooling process does not introduce any variations.
By adjusting the speed at which the glass is transported across the bath and through the annealing lehr, thickness can be finely tuned.
Accurate measurement tools and automation systems can help maintain these parameters consistently.
Quality Control Techniques
Quality control in the float glass industry is not just an option but a necessity to meet industry standards and customer expectations.
Several techniques are employed to keep the product in line with the highest quality standards.
Visual Inspection
Once the glass is formed, it undergoes a visual inspection.
Trained inspectors look for flaws such as bubbles, scratches, or discoloration.
These defects, though sometimes small, can make glass unsuitable for particular applications.
While these inspections are critical, coupling them with automated systems can enhance efficiency and accuracy.
Technologies such as camera systems and laser detection can identify defects that might be missed by the human eye.
Advanced Instrumentation
Utilizing technology, operators can implement advanced instrumentation for more precise measurements.
Equipment like laser thickness gauges, surface profilometers, and automated stress analysis tools provide detailed feedback on glass conditions.
These instruments can immediately highlight inconsistencies, allowing operators to make necessary adjustments on the fly.
This reduces wastage and ensures that the final product aligns with desired specifications.
Regular Performance Audits
An often overlooked aspect of quality control is conducting regular performance audits.
These audits review both the machinery and the operational procedures to identify areas for improvement.
Audits involve a comprehensive evaluation of the production process, from raw material acquisition to final product delivery.
By identifying inefficiencies or inconsistencies, operators can implement changes that enhance both productivity and product quality.
Conclusion
The float glass manufacturing process is an intricate dance of precise controls and careful monitoring.
For operators in this industry, understanding each stage’s unique demands and implementing effective quality control measures are key to delivering outstanding products.
By focusing on temperature regulation, maintaining cleanliness, ensuring thickness consistency, and adopting the latest quality control technologies, manufacturers can meet and exceed industry standards.
With these practices in place, operators are well-equipped to produce superior float glass that not only meets customer expectations but also sets the benchmark for quality.
資料ダウンロード
QCD調達購買管理クラウド「newji」は、調達購買部門で必要なQCD管理全てを備えた、現場特化型兼クラウド型の今世紀最高の購買管理システムとなります。
ユーザー登録
調達購買業務の効率化だけでなく、システムを導入することで、コスト削減や製品・資材のステータス可視化のほか、属人化していた購買情報の共有化による内部不正防止や統制にも役立ちます。
NEWJI DX
製造業に特化したデジタルトランスフォーメーション(DX)の実現を目指す請負開発型のコンサルティングサービスです。AI、iPaaS、および先端の技術を駆使して、製造プロセスの効率化、業務効率化、チームワーク強化、コスト削減、品質向上を実現します。このサービスは、製造業の課題を深く理解し、それに対する最適なデジタルソリューションを提供することで、企業が持続的な成長とイノベーションを達成できるようサポートします。
オンライン講座
製造業、主に購買・調達部門にお勤めの方々に向けた情報を配信しております。
新任の方やベテランの方、管理職を対象とした幅広いコンテンツをご用意しております。
お問い合わせ
コストダウンが利益に直結する術だと理解していても、なかなか前に進めることができない状況。そんな時は、newjiのコストダウン自動化機能で大きく利益貢献しよう!
(Β版非公開)