- お役立ち記事
- For process engineers in the semiconductor industry! How to join different materials with high precision using wafer bonding technology
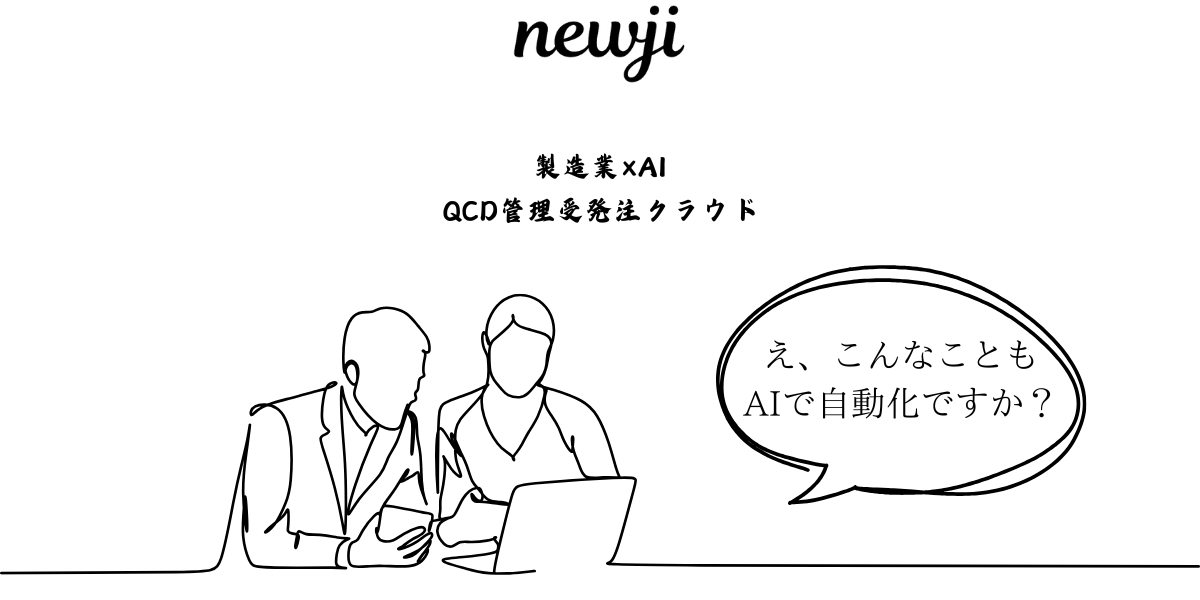
For process engineers in the semiconductor industry! How to join different materials with high precision using wafer bonding technology
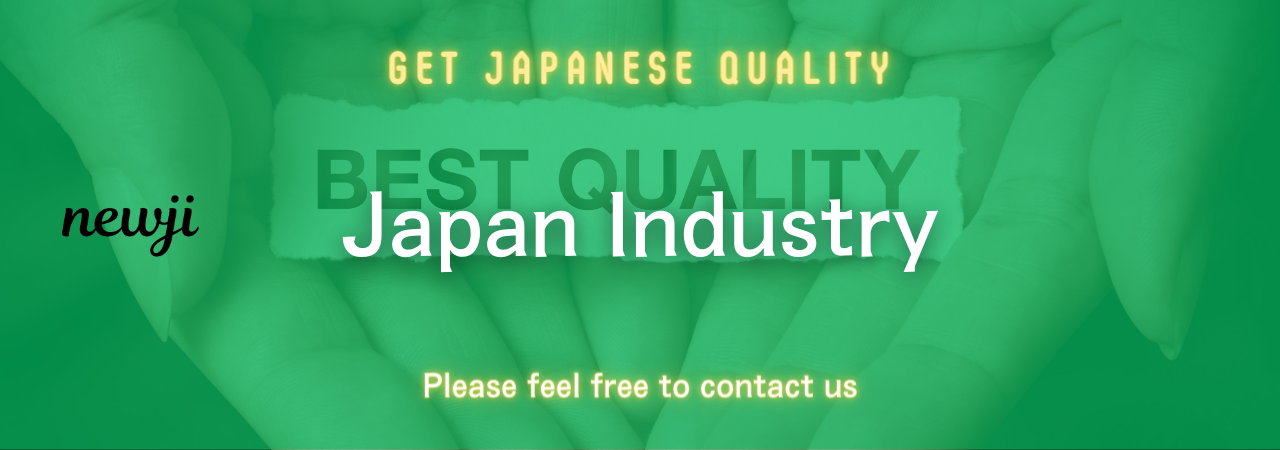
目次
Understanding Wafer Bonding Technology
Wafer bonding technology is a critical process in the semiconductor industry, enabling the precise joining of different materials.
This method is used to enhance the functionality and performance of semiconductor devices by allowing manufacturers to combine diverse materials into a single structure.
Understanding how wafer bonding works and its applications can greatly benefit process engineers looking to optimize their manufacturing techniques.
At its core, wafer bonding involves the joining of two semiconductor wafers to create a single, composite structure.
This process can be applied to the manufacturing of microelectromechanical systems (MEMS), integrated circuits (ICs), and other advanced electronic components.
The main objective is to achieve a strong, reliable bond between the different materials, which is crucial for ensuring device performance and longevity.
Types of Wafer Bonding Techniques
Several wafer bonding techniques are available, each with specific advantages and applications.
The most common methods include direct bonding, anodic bonding, and adhesive bonding.
Let’s explore each of these techniques to understand where they fit in the semiconductor manufacturing process.
Direct Bonding
Direct bonding, also known as fusion bonding, involves joining two wafers without any intermediate layers or adhesives.
In this method, the wafers are brought into close contact, and chemical bonds form between their surfaces.
The process often requires high temperature and pressure to improve bond strength and consistency.
Direct bonding is highly advantageous for applications requiring high thermal conductivity and minimal layer interruptions.
Anodic Bonding
Anodic bonding is commonly used to join glass wafers to silicon wafers.
This method involves applying an electric field and heat to generate strong electrostatic forces, creating a permanent bond between the wafers.
Anodic bonding is particularly useful in the fabrication of MEMS devices because it provides a hermetic seal, which helps protect sensitive components from environmental influences.
Adhesive Bonding
Adhesive bonding involves the use of an additional adhesive layer to facilitate bonding between the wafers.
This technique is beneficial when dealing with wafer materials that do not bond well through other methods.
Adhesives can be organic or inorganic, and their selection depends on the required mechanical, thermal, and chemical properties.
Adhesive bonding is versatile and can be adapted to a wide range of semiconductor applications.
Challenges and Considerations
Wafer bonding, while highly effective, poses several challenges that process engineers must address to achieve high precision and reliability.
Understanding these challenges and how to overcome them is essential for success in semiconductor manufacturing.
Surface Preparation
The quality of the wafer surfaces significantly affects the success of the bonding process.
Before bonding, wafers must be meticulously cleaned to remove any contaminants or particles that could hinder bond formation.
Surface flatness and smoothness are also critical factors that influence bond quality.
Implementing rigorous cleaning protocols and using state-of-the-art surface modification techniques can help achieve the desired surface conditions.
Thermal Expansion Mismatch
Joining wafers made from different materials introduces the challenge of thermal expansion mismatch.
When wafers with differing coefficients of thermal expansion are bonded, stresses can develop during thermal cycling, potentially leading to bond failure.
Process engineers must carefully select materials with compatible coefficients or design processes that accommodate this mismatch to ensure bond integrity.
Bond Strength and Stability
Ensuring that the bond remains strong and stable throughout the device’s lifetime is crucial.
Engineers must choose bonding techniques and conditions that maximize bond strength while maintaining the desired device properties.
Additionally, testing and monitoring methods should be implemented to detect any potential weakening or failures in the bond over time.
Applications in Semiconductor Manufacturing
Wafer bonding technology is indispensable in the development of advanced semiconductor devices with enhanced functionality and performance.
Its applications span a wide range of fields, from consumer electronics to aerospace and medical technology.
MEMS Devices
Microelectromechanical systems (MEMS) benefit significantly from wafer bonding technology.
Bonding techniques enable the integration of silicon, glass, and other materials to create complex MEMS structures.
These devices, which can include sensors, actuators, and optical components, often rely on precise wafer bonding to deliver accurate and reliable performance.
Three-Dimensional Integrated Circuits (3D ICs)
As the demand for compact and high-performance electronics grows, three-dimensional integrated circuits (3D ICs) have become increasingly important.
Wafer bonding allows for the vertical integration of multiple semiconductor layers, leading to improved performance and reduced power consumption.
By using wafer bonding, manufacturers can achieve higher device densities and reduced interconnect distances, enhancing overall functionality.
The Future of Wafer Bonding in Semiconductors
As the semiconductor industry continues to evolve, the importance of wafer bonding technology in enabling cutting-edge devices cannot be overstated.
Ongoing research and development are focused on improving bonding techniques, materials compatibility, and the scalability of wafer bonding processes.
Process engineers will play a vital role in advancing wafer bonding technology by developing new methods and materials that meet the demands of increasingly complex semiconductor applications.
With the proper understanding and application of wafer bonding technology, manufacturing processes in the semiconductor industry can achieve remarkable levels of precision and efficiency.
資料ダウンロード
QCD調達購買管理クラウド「newji」は、調達購買部門で必要なQCD管理全てを備えた、現場特化型兼クラウド型の今世紀最高の購買管理システムとなります。
ユーザー登録
調達購買業務の効率化だけでなく、システムを導入することで、コスト削減や製品・資材のステータス可視化のほか、属人化していた購買情報の共有化による内部不正防止や統制にも役立ちます。
NEWJI DX
製造業に特化したデジタルトランスフォーメーション(DX)の実現を目指す請負開発型のコンサルティングサービスです。AI、iPaaS、および先端の技術を駆使して、製造プロセスの効率化、業務効率化、チームワーク強化、コスト削減、品質向上を実現します。このサービスは、製造業の課題を深く理解し、それに対する最適なデジタルソリューションを提供することで、企業が持続的な成長とイノベーションを達成できるようサポートします。
オンライン講座
製造業、主に購買・調達部門にお勤めの方々に向けた情報を配信しております。
新任の方やベテランの方、管理職を対象とした幅広いコンテンツをご用意しております。
お問い合わせ
コストダウンが利益に直結する術だと理解していても、なかなか前に進めることができない状況。そんな時は、newjiのコストダウン自動化機能で大きく利益貢献しよう!
(Β版非公開)