- お役立ち記事
- For production engineers in the toy industry! Know-how to create toys with complex shapes using injection molding technology
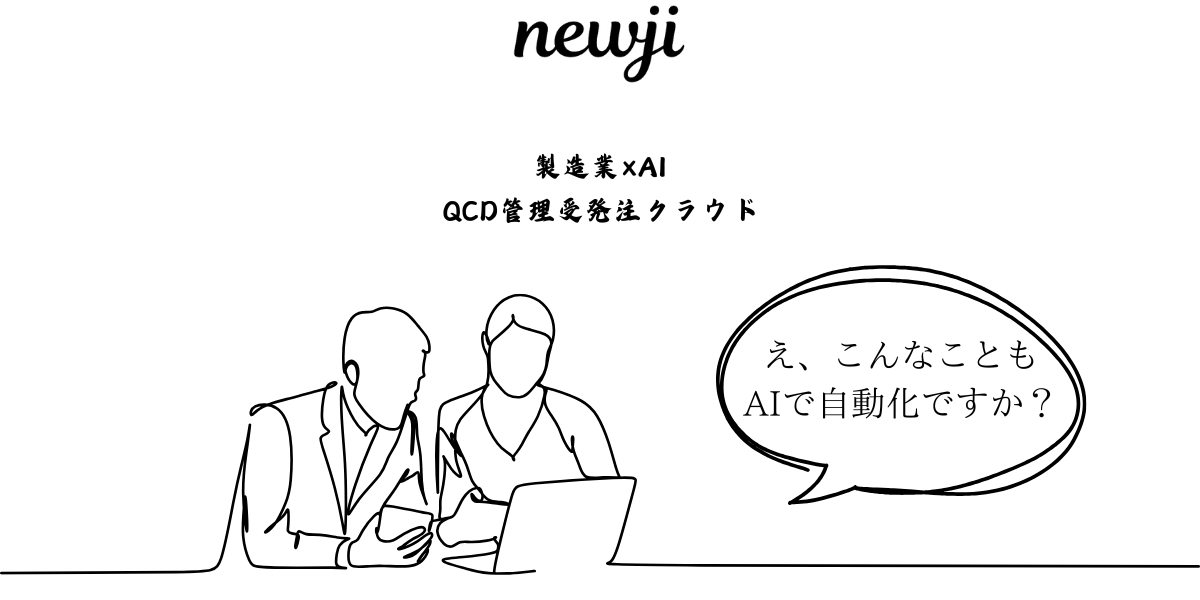
For production engineers in the toy industry! Know-how to create toys with complex shapes using injection molding technology
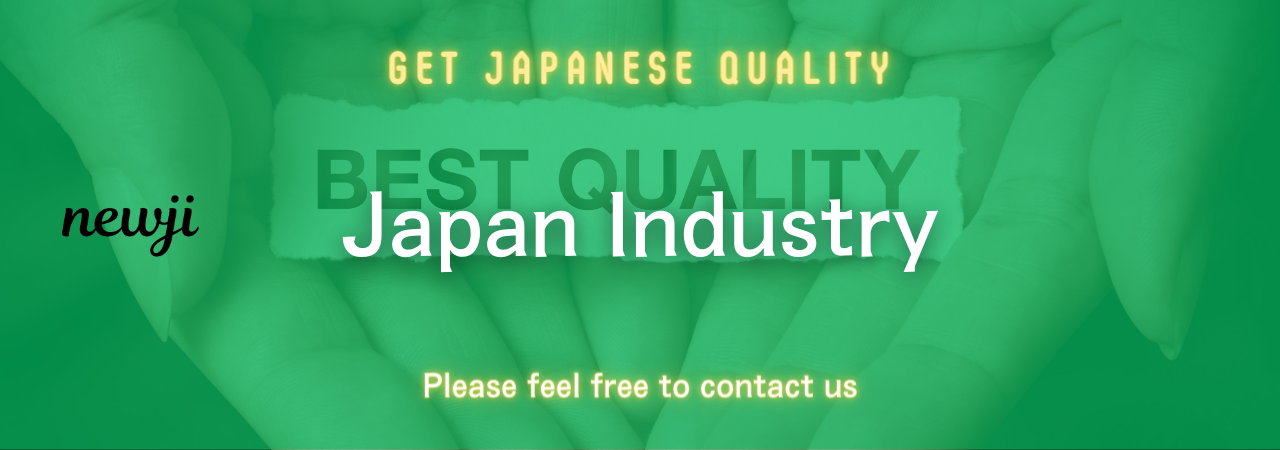
目次
Understanding Injection Molding in Toy Production
Injection molding is a manufacturing process that has revolutionized the toy industry.
It allows for the creation of toys with complex shapes and intricate designs.
For production engineers, mastering this technology is crucial for making high-quality toys.
The process involves injecting molten plastic into a mold where it cools and solidifies into the final product.
This technique is perfect for mass-producing identical items, making it ideal for the toy industry.
With injection molding, engineers can easily replicate toys with precise details and vibrant colors.
The Basics of Injection Molding
Injection molding begins with plastic pellets being melted into a liquid state.
These are then injected into a mold at high pressures.
Once the plastic fills the mold, it cools and hardens.
The mold is then opened, and the finished toy is ejected.
This method is efficient and allows for high production rates.
The molds used can be designed to create complex shapes, providing endless possibilities for toy designs.
By understanding the basics, engineers can better appreciate the potential of injection molding technology.
Designing Molds for Complex Toy Shapes
Creating toys with complex shapes requires careful design and planning.
The mold must be precisely engineered to ensure the plastic flows correctly and fills every part of the design.
Mold design is a critical step, as it directly impacts the quality of the final product.
Engineers use computer-aided design (CAD) software to create detailed 3D models of the desired toy.
These models help in visualizing the final product and making adjustments before the actual mold is produced.
Selecting the right material for the mold is also crucial, as it needs to withstand the pressure and temperature of the injection process.
The Role of Material Selection
The choice of plastic is fundamental in the production of toys using injection molding.
Different plastics offer varying properties such as durability, flexibility, and finish.
For instance, ABS plastic is commonly used for toys because of its strength and glossy finish.
Engineers must consider the toy’s purpose and the environment it will be used in when selecting materials.
Safety is a primary concern, especially for toys intended for young children.
Non-toxic and hypoallergenic materials are often chosen to ensure the toys are safe for all users.
Optimizing the Injection Molding Process
Efficiency in injection molding is vital to keep production costs low and ensure a quick turnaround time.
Production engineers aim to minimize cycle time—the time it takes to complete one production cycle.
This includes the time taken to inject the plastic, cool, and eject the finished product.
Process optimization involves controlling variables like temperature, pressure, and cooling time.
By fine-tuning these parameters, engineers can enhance product quality and reduce waste.
Regular maintenance of machinery and molds also plays a significant role in maintaining production efficiency.
Quality Control and Testing
Quality control is an essential part of the toy production process.
Each toy must be tested to ensure it meets safety standards and quality specifications.
Visual inspections, durability tests, and safety audits are conducted to verify the toys’ reliability.
Engineers evaluate the toys for defects such as warping, cracks, or incomplete filling.
Identifying and addressing defects early helps in maintaining the overall quality of the toys.
Quality testing also ensures that toys remain consistent batch after batch, which is critical for brand reputation.
Innovations in Toy Design with Injection Molding
Advancements in technology continue to expand the possibilities of injection molding.
Innovative mold designs can now incorporate complex moving parts and intricate detailing in toys.
This technology opens up new avenues for creativity and functionality in toy design.
Engineers are exploring the use of multi-material injection molding, where different types of plastic are combined in a single toy.
This method allows for more diverse textures, colors, and functional parts, enhancing the play experience for children.
The Future of Injection Molding in Toy Production
As the toy industry evolves, so does the injection molding technology.
Sustainability is becoming a critical focus, with more manufacturers opting for biodegradable plastics and recycling initiatives.
Efforts to reduce energy consumption and minimize waste are also underway.
The rise of smart toys, incorporating electronics and sensors, poses new challenges and opportunities for injection mold engineers.
Innovative solutions will be necessary to integrate these components seamlessly into toy designs.
In conclusion, mastering the art of injection molding is vital for engineers in the toy industry.
From designing intricate molds to selecting the right materials and optimizing processes, every step influences the final product’s success.
By embracing technological advancements and sustainability practices, engineers can continue to create captivating and safe toys for future generations.
資料ダウンロード
QCD調達購買管理クラウド「newji」は、調達購買部門で必要なQCD管理全てを備えた、現場特化型兼クラウド型の今世紀最高の購買管理システムとなります。
ユーザー登録
調達購買業務の効率化だけでなく、システムを導入することで、コスト削減や製品・資材のステータス可視化のほか、属人化していた購買情報の共有化による内部不正防止や統制にも役立ちます。
NEWJI DX
製造業に特化したデジタルトランスフォーメーション(DX)の実現を目指す請負開発型のコンサルティングサービスです。AI、iPaaS、および先端の技術を駆使して、製造プロセスの効率化、業務効率化、チームワーク強化、コスト削減、品質向上を実現します。このサービスは、製造業の課題を深く理解し、それに対する最適なデジタルソリューションを提供することで、企業が持続的な成長とイノベーションを達成できるようサポートします。
オンライン講座
製造業、主に購買・調達部門にお勤めの方々に向けた情報を配信しております。
新任の方やベテランの方、管理職を対象とした幅広いコンテンツをご用意しております。
お問い合わせ
コストダウンが利益に直結する術だと理解していても、なかなか前に進めることができない状況。そんな時は、newjiのコストダウン自動化機能で大きく利益貢献しよう!
(Β版非公開)