- お役立ち記事
- For quality managers in the gas turbine blade manufacturing industry! Alloy technology to achieve both heat resistance and high strength
For quality managers in the gas turbine blade manufacturing industry! Alloy technology to achieve both heat resistance and high strength
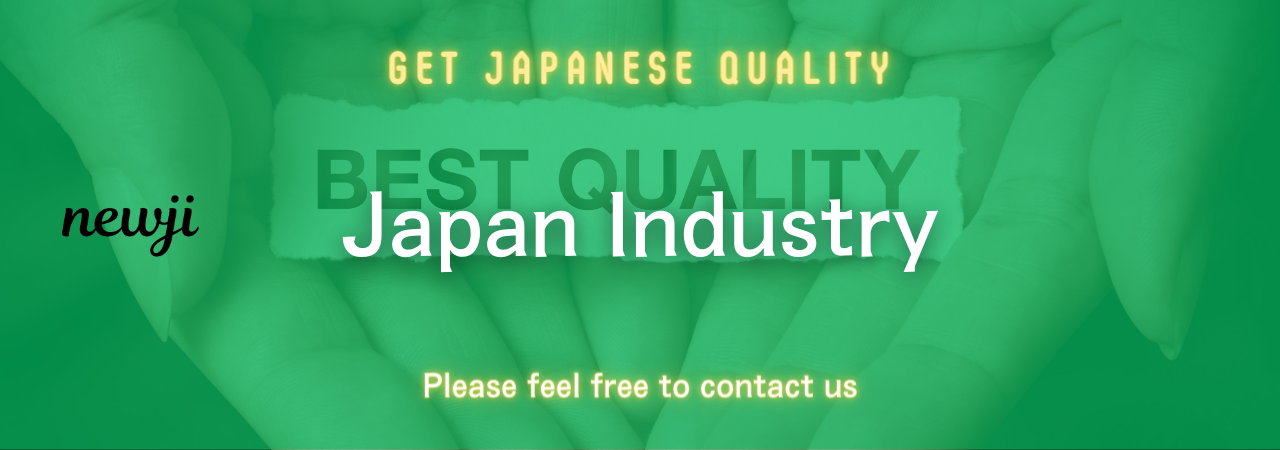
目次
Introduction to Alloy Technology
The gas turbine blade manufacturing industry faces distinct challenges, primarily ensuring materials used can withstand extreme operational conditions.
For quality managers, the pursuit of alloys offering both heat resistance and high strength is a focal point of innovation.
Alloys are crucial in enhancing the performance and durability of components within gas turbines.
This article explores the latest alloy technology developments, offering insights for quality managers seeking materials that can endure the demanding environments typical of gas turbines.
Understanding Gas Turbine Blades
Gas turbine blades are integral to the performance and efficiency of turbines.
They convert energy from high-temperature combustion gases into mechanical energy, driving the turbine.
Due to their constant exposure to high temperatures and pressure, these blades require exceptional heat resistance and structural integrity.
The extreme thermal and mechanical stresses gas turbine blades undergo result in a crucial need for advanced materials.
Innovations in alloy technology are essential for meeting these demands, providing the necessary strength and heat resistance.
The Role of Alloys in Gas Turbine Blades
Alloys are mixtures composed of two or more elements, with one being a metal, that are engineered to enhance material properties.
In gas turbine blades, alloys serve the crucial function of maintaining performance and longevity.
Selecting the right alloy composition ensures blades can withstand the high-temperature conditions of modern gas turbines.
The effectiveness of an alloy in gas turbine blades is chiefly determined by its ability to resist deformation and withstand thermal stress.
Encoding properties like oxidation resistance, creep resistance, and strength retention at high temperatures are critical factors.
Key Advances in Alloy Technology
Recent advancements in alloy technology are transforming the landscape of gas turbine blade manufacturing.
These innovations focus on creating more efficient, durable, and high-performing components amid intense operational demands.
Nickel-Based Superalloys
Nickel-based superalloys are a staple in gas turbine blade manufacturing due to their outstanding properties.
These alloys are specifically designed to maintain strength and resist oxidation and creep at high temperatures, making them ideal for critical components.
Superalloys primarily consist of nickel, with additional elements like chromium, cobalt, molybdenum, and aluminum.
Innovations in these materials enhance corrosion resistance and creep strength, allowing turbine blades to operate efficiently at higher temperatures.
Cobalt-Based Alloys
Cobalt-based alloys offer an exciting alternative for manufacturing turbine blades.
Although less prevalent than nickel-based counterparts, cobalt alloys provide excellent high-temperature strength and resistance to hot corrosion.
Cobalt-based alloys’ capability to retain strength at high temperatures makes them suitable candidates for specific turbine applications.
In some instances, combining nickel and cobalt presents opportunities to exploit the benefits of both metals.
Titanium Aluminides
Titanium aluminides are gaining traction for their lightweight and robust high-temperature performance.
These materials offer an attractive combination of mechanical strength, reduced weight, and increased efficiency.
As gas turbine engines emphasize fuel efficiency and reduced emissions, titanium aluminides become more compelling due to their lower density compared to traditional superalloys.
They offer impressive resistance to high-temperature oxidation while enhancing overall engine performance.
Emerging Materials and Research
Research into emerging materials is ongoing, aiming to capitalize on the unique characteristics of new alloy compositions.
Materials such as ceramic matrix composites (CMCs) and high-entropy alloys (HEAs) are being explored.
CMCs are strengthening their position in high-performance applications due to their ability to withstand extreme temperatures beyond the capabilities of metal alloys.
HEAs, composed of multiple principal elements, exhibit promising traits like strength, corrosion resistance, and high-temperature stability.
Challenges in Alloy Innovation
While the advancements in alloy technology are promising, challenges remain in developing and deploying these new materials.
Quality managers must navigate issues such as cost, manufacturing processes, and material fatigue.
Cost Considerations
One of the significant challenges in adopting advanced alloys is their cost.
Quality managers must balance the benefits of increased performance and longevity against the expense of introducing new materials.
Efforts to minimize costs involve optimizing alloy compositions and including recycled materials without compromising quality.
Maximizing the efficiency of manufacturing processes can also help in managing expenses.
Manufacturing Processes
Complex manufacturing processes are often required to produce turbine blades using newly developed alloys.
Quality managers must ensure that production techniques maintain the intricate properties of these advanced materials.
Establishing precise control over casting, forging, and heat-treatment processes is essential to preserve the high-quality attributes of the alloys.
Material Fatigue and Testing
The long-term performance of turbine blades necessitates thorough fatigue testing to ensure reliability in extreme conditions.
Quality managers must carefully evaluate new alloys under varied stress levels and thermal cycles to predict lifecycle performance.
Rigorous testing and assessment help confirm that emerging materials can meet the demanding requirements of gas turbine operations.
Conclusion
Alloy technology continues to evolve, offering promising solutions for the gas turbine blade manufacturing industry.
Advances in materials such as nickel-based superalloys, cobalt-based alloys, and titanium aluminides show remarkable potential in improving heat resistance and strength.
Quality managers play a critical role in exploring and adopting these innovations to enhance turbine performance.
While challenges such as cost and manufacturing remain, the pursuit of advanced alloys promises a future of more durable and efficient gas turbines.
資料ダウンロード
QCD調達購買管理クラウド「newji」は、調達購買部門で必要なQCD管理全てを備えた、現場特化型兼クラウド型の今世紀最高の購買管理システムとなります。
ユーザー登録
調達購買業務の効率化だけでなく、システムを導入することで、コスト削減や製品・資材のステータス可視化のほか、属人化していた購買情報の共有化による内部不正防止や統制にも役立ちます。
NEWJI DX
製造業に特化したデジタルトランスフォーメーション(DX)の実現を目指す請負開発型のコンサルティングサービスです。AI、iPaaS、および先端の技術を駆使して、製造プロセスの効率化、業務効率化、チームワーク強化、コスト削減、品質向上を実現します。このサービスは、製造業の課題を深く理解し、それに対する最適なデジタルソリューションを提供することで、企業が持続的な成長とイノベーションを達成できるようサポートします。
オンライン講座
製造業、主に購買・調達部門にお勤めの方々に向けた情報を配信しております。
新任の方やベテランの方、管理職を対象とした幅広いコンテンツをご用意しております。
お問い合わせ
コストダウンが利益に直結する術だと理解していても、なかなか前に進めることができない状況。そんな時は、newjiのコストダウン自動化機能で大きく利益貢献しよう!
(Β版非公開)