- お役立ち記事
- For SMEs: Cost Reduction Techniques in Compression Molding
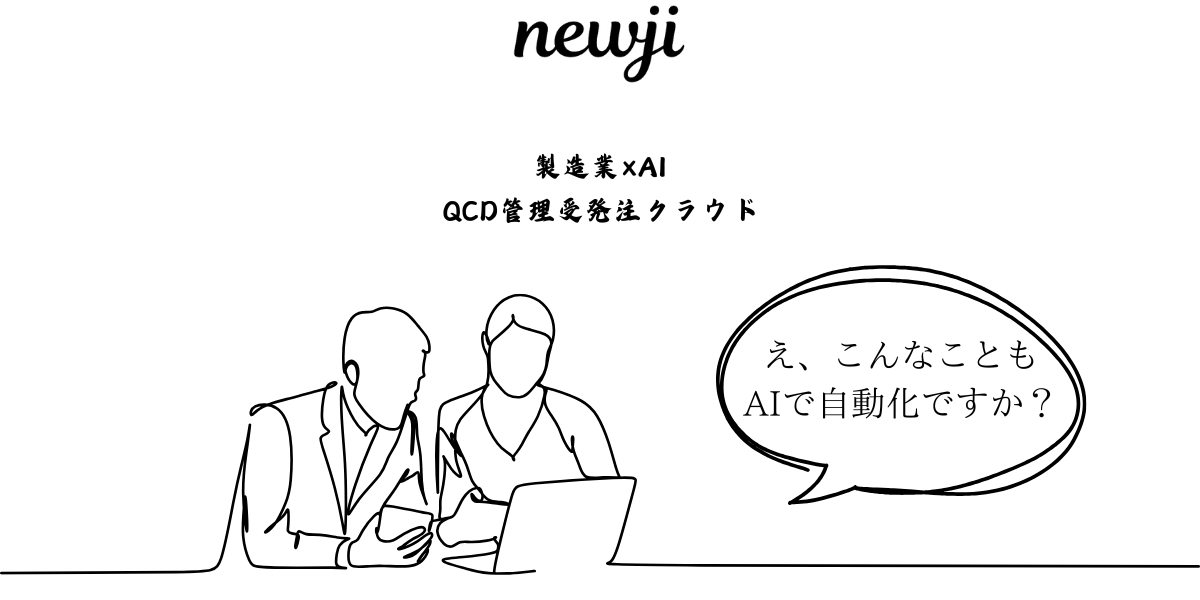
For SMEs: Cost Reduction Techniques in Compression Molding
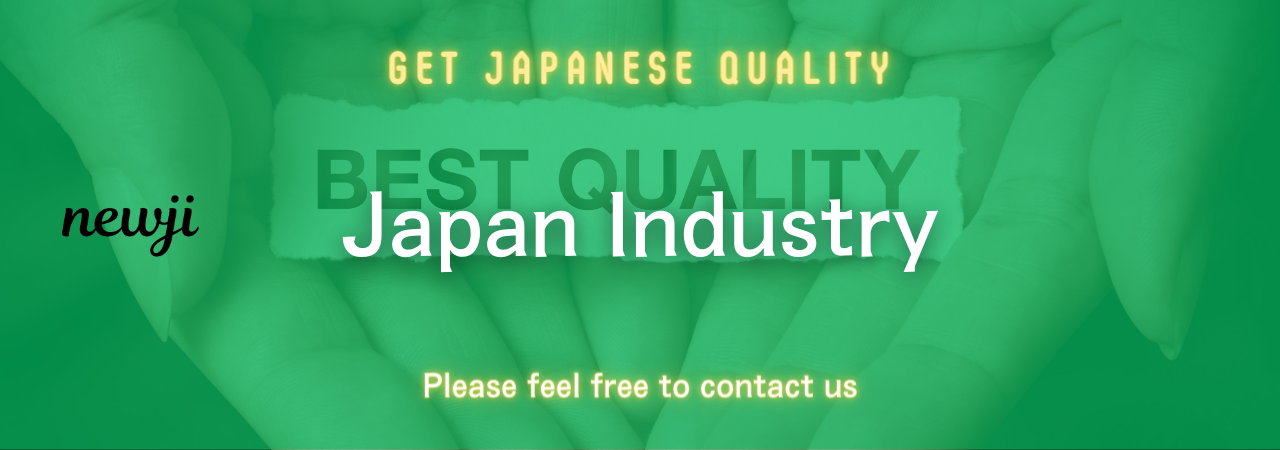
目次
Introduction to Compression Molding
Compression molding is a widely used manufacturing process in the production of high-strength, lightweight parts.
It involves placing a material, often a thermoset plastic, into a heated mold cavity.
The mold then closes and pressure is applied to form the material to the mold shape.
Once cured, the mold is opened, and the part is ejected.
This process is especially suitable for component manufacturing in industries such as automotive, aerospace, and electronics.
Small and medium-sized enterprises (SMEs) can find great opportunities with compression molding due to its efficiency and the strength of the products created.
However, like any manufacturing process, compression molding can be costly.
Understanding cost reduction techniques can significantly enhance competitiveness and profitability for SMEs.
Why Cost Reduction is Crucial for SMEs
SMEs face unique challenges that larger corporations may not encounter as intensely, such as limited resources and cash flow constraints.
Cost reduction processes are vital as they allow these enterprises to maintain competitiveness, increase profit margins, and reinvest savings into growth initiatives.
In the context of compression molding, reducing costs without sacrificing product quality or production speed can be particularly impactful.
Applying strategic cost-saving methods can lead SMEs to sustainability in an ever-competitive market.
Raw Material Optimization
Selecting Cost-Efficient Materials
The choice of raw materials is pivotal in the compression molding process.
For cost reduction, SMEs should explore alternative materials that offer comparable properties at a lower price.
Reinforced plastics, for instance, provide strength and durability similar to metals but often at a cheaper cost.
Additionally, opting for materials with quick curing times can reduce cycle times and energy consumption, leading to further savings.
Minimizing Material Waste
Material waste can eat into the profits of any compression molding operation.
Implementing standard operating procedures and effective training for staff can minimize errors during material handling.
An investment in material recycling technologies can also turn waste into a resource, further reducing costs and enhancing sustainability.
Streamlining Production Processes
Improving Mold Design
A well-designed mold can drastically cut production costs.
SMEs should focus on simplifying mold designs to reduce cycle times and material consumption.
Engaging with experienced mold designers and using simulation software can pinpoint design inefficiencies before production begins.
Innovative mold-making techniques, such as 3D printing, can also lower mold production costs compared to traditional methods.
Automating Production
Automation in manufacturing can offer significant cost savings by increasing production speed and reducing labor costs.
For compression molding, investing in automated systems for feeding materials and extracting finished parts can ensure a more consistent production flow with less manual intervention.
Although initial investments can be substantial, the long-term cost benefits and quality improvements often justify the initial outlay.
Energy Efficiency Improvement
Adopting Energy-Efficient Equipment
Energy consumption is a significant cost driver in compression molding operations.
Switching to energy-efficient machinery may require an upfront investment, but the reduction in energy costs can yield substantial savings over time.
Regular maintenance of equipment can also improve energy efficiency, reducing wear and tear and improving overall performance.
Optimizing Production Schedules
Running machines at optimum times can reduce energy costs considerably.
By aligning production schedules with periods of lower energy rates or using energy monitoring systems, SMEs can ensure that they are not consuming energy unnecessarily or at more expensive times of the day.
Improving Workforce Efficiency
Employee Training
A knowledgeable workforce is an asset in any manufacturing operation.
Investing in regular training programs ensures that employees are well-versed in the latest industry standards and techniques, reducing the likelihood of costly mistakes.
Skilled workers can also contribute to process improvements that may not be immediately apparent to management.
Encouraging Teamwork and Communication
Effective communication and teamwork can enhance manufacturing processes by fostering a cooperative environment where employees feel valued and engaged.
This can lead to shared problem-solving and swift resolution of production issues that may arise, minimizing downtime and thereby reducing costs.
Conclusion
Reducing costs in compression molding is multifaceted and requires a comprehensive approach that considers every aspect of the manufacturing process.
From choosing the right materials and improving process efficiency to investing in automation and energy-saving measures, SMEs have numerous strategies at their disposal.
Implementing these can help improve their bottom line without compromising on quality.
Ultimately, these cost reduction techniques can empower SMEs to thrive and expand in competitive market environments.
資料ダウンロード
QCD調達購買管理クラウド「newji」は、調達購買部門で必要なQCD管理全てを備えた、現場特化型兼クラウド型の今世紀最高の購買管理システムとなります。
ユーザー登録
調達購買業務の効率化だけでなく、システムを導入することで、コスト削減や製品・資材のステータス可視化のほか、属人化していた購買情報の共有化による内部不正防止や統制にも役立ちます。
NEWJI DX
製造業に特化したデジタルトランスフォーメーション(DX)の実現を目指す請負開発型のコンサルティングサービスです。AI、iPaaS、および先端の技術を駆使して、製造プロセスの効率化、業務効率化、チームワーク強化、コスト削減、品質向上を実現します。このサービスは、製造業の課題を深く理解し、それに対する最適なデジタルソリューションを提供することで、企業が持続的な成長とイノベーションを達成できるようサポートします。
オンライン講座
製造業、主に購買・調達部門にお勤めの方々に向けた情報を配信しております。
新任の方やベテランの方、管理職を対象とした幅広いコンテンツをご用意しております。
お問い合わせ
コストダウンが利益に直結する術だと理解していても、なかなか前に進めることができない状況。そんな時は、newjiのコストダウン自動化機能で大きく利益貢献しよう!
(Β版非公開)