- お役立ち記事
- Fundamentals of Manufacturing Accounting Course
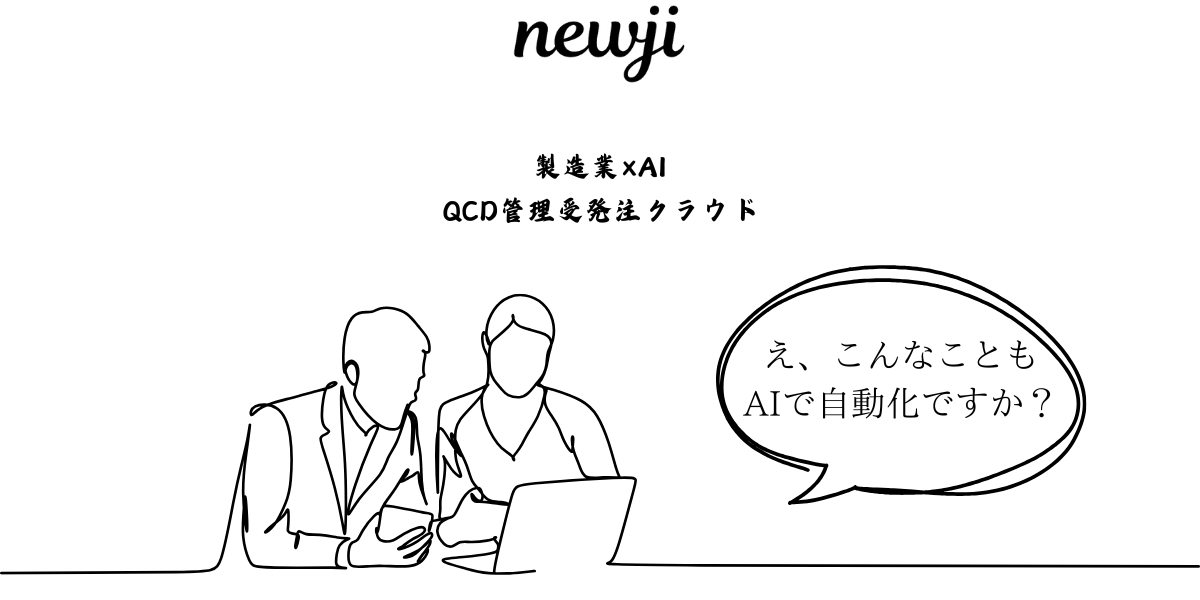
Fundamentals of Manufacturing Accounting Course
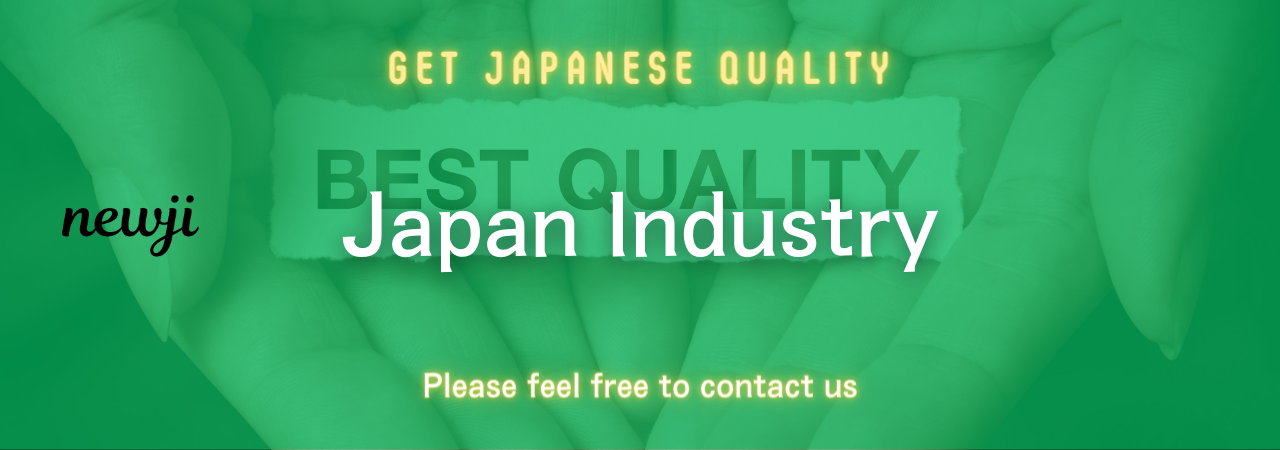
目次
Understanding the Basics of Manufacturing Accounting
Manufacturing accounting is a specialized area of accounting that focuses on tracking and managing the financial aspects of the manufacturing process.
It involves determining the costs of producing goods, managing inventory, and analyzing financial performance to make informed business decisions.
By understanding the basics of manufacturing accounting, companies can improve efficiency, reduce costs, and enhance profitability.
The Role of Manufacturing Accounting
The primary role of manufacturing accounting is to accurately track the costs associated with producing goods.
This includes direct costs like raw materials and labor, as well as indirect costs like overhead and utilities.
Manufacturing accounting also involves managing inventory levels, ensuring that materials and finished products are available when needed without excessive stockpiling.
Direct Costs
Direct costs are expenses that can be directly attributed to the production of specific goods.
These costs include raw materials, labor, and any other expenses that are directly tied to the manufacturing process.
By tracking direct costs, companies can determine the true cost of producing each item and identify opportunities for cost savings.
Indirect Costs
Indirect costs, also known as overhead, are expenses that cannot be directly attributed to specific goods.
These costs include utilities, rent, maintenance, and administrative expenses.
Manufacturing accounting involves allocating these indirect costs to products based on a predetermined method, such as machine hours or labor hours.
Cost Allocation Methods
Cost allocation is the process of assigning indirect costs to products based on a rational and consistent method.
Common cost allocation methods include the traditional costing method and activity-based costing (ABC).
Traditional Costing Method
The traditional costing method allocates indirect costs based on a single cost driver, such as machine hours or labor hours.
This method is relatively simple but may not provide an accurate picture of the true costs of production, especially in complex manufacturing environments.
Activity-Based Costing (ABC)
Activity-based costing (ABC) is a more detailed and accurate method of cost allocation.
This method assigns indirect costs based on multiple cost drivers, reflecting the actual activities that contribute to those costs.
By using ABC, companies can gain a clearer understanding of how different activities impact costs and make more informed decisions about pricing, production, and process improvements.
Inventory Management
Effective inventory management is crucial for manufacturing companies to ensure that raw materials and finished products are available when needed.
Manufacturing accounting involves tracking inventory levels, valuing inventory, and managing inventory turnover to minimize carrying costs and reduce the risk of stockouts.
Inventory Valuation Methods
There are several methods for valuing inventory, each with its advantages and disadvantages.
The three most common inventory valuation methods are First-In, First-Out (FIFO), Last-In, First-Out (LIFO), and Weighted Average Cost.
First-In, First-Out (FIFO)
FIFO assumes that the first items purchased are the first ones to be used or sold.
This method is straightforward and aligns with the actual flow of inventory in many manufacturing environments.
FIFO tends to result in higher inventory values during periods of rising prices, as older, lower-cost items are used first.
Last-In, First-Out (LIFO)
LIFO assumes that the most recently purchased items are the first to be used or sold.
This method can result in lower inventory values during periods of rising prices, as the cost of more recent, higher-priced items is matched with current revenues.
However, LIFO is not permitted under International Financial Reporting Standards (IFRS) and may not reflect the actual flow of inventory.
Weighted Average Cost
The weighted average cost method calculates the average cost of all inventory items and uses this average cost to value inventory and determine the cost of goods sold.
This method smooths out price fluctuations and provides a consistent cost basis for inventory valuation.
Analyzing Financial Performance
Manufacturing accounting provides valuable insights into a company’s financial performance by tracking costs, revenues, and profitability.
By analyzing this information, companies can identify trends, assess the efficiency of their operations, and make strategic decisions to improve their financial health.
Gross Margin
Gross margin is a key financial metric that measures the difference between sales revenue and the cost of goods sold.
It provides insight into a company’s ability to generate profit from its core manufacturing activities.
A higher gross margin indicates better profitability, while a lower gross margin may signal the need for cost reductions or pricing adjustments.
Operating Margin
Operating margin measures the difference between sales revenue and operating expenses, including both direct and indirect costs.
This metric provides a broader view of a company’s profitability by considering all operating expenses, not just the cost of goods sold.
A higher operating margin indicates efficient cost management and strong financial performance.
Break-Even Analysis
Break-even analysis is a tool used to determine the level of sales needed to cover all fixed and variable costs.
It helps companies understand the minimum sales volume required to avoid losses and can be used to set sales targets and pricing strategies.
By conducting break-even analysis, manufacturers can make informed decisions about production levels, marketing efforts, and pricing policies.
Conclusion
Understanding the fundamentals of manufacturing accounting is essential for any company involved in the production of goods.
By accurately tracking direct and indirect costs, managing inventory, and analyzing financial performance, companies can make informed decisions that enhance efficiency, reduce costs, and improve profitability.
Whether through traditional costing methods or more advanced techniques like activity-based costing, manufacturing accounting provides the insights needed to navigate the complexities of modern manufacturing and achieve long-term success.
資料ダウンロード
QCD調達購買管理クラウド「newji」は、調達購買部門で必要なQCD管理全てを備えた、現場特化型兼クラウド型の今世紀最高の購買管理システムとなります。
ユーザー登録
調達購買業務の効率化だけでなく、システムを導入することで、コスト削減や製品・資材のステータス可視化のほか、属人化していた購買情報の共有化による内部不正防止や統制にも役立ちます。
NEWJI DX
製造業に特化したデジタルトランスフォーメーション(DX)の実現を目指す請負開発型のコンサルティングサービスです。AI、iPaaS、および先端の技術を駆使して、製造プロセスの効率化、業務効率化、チームワーク強化、コスト削減、品質向上を実現します。このサービスは、製造業の課題を深く理解し、それに対する最適なデジタルソリューションを提供することで、企業が持続的な成長とイノベーションを達成できるようサポートします。
オンライン講座
製造業、主に購買・調達部門にお勤めの方々に向けた情報を配信しております。
新任の方やベテランの方、管理職を対象とした幅広いコンテンツをご用意しております。
お問い合わせ
コストダウンが利益に直結する術だと理解していても、なかなか前に進めることができない状況。そんな時は、newjiのコストダウン自動化機能で大きく利益貢献しよう!
(Β版非公開)