- お役立ち記事
- Fundamentals of observing fracture surfaces of metal materials and application to estimating the cause of fracture
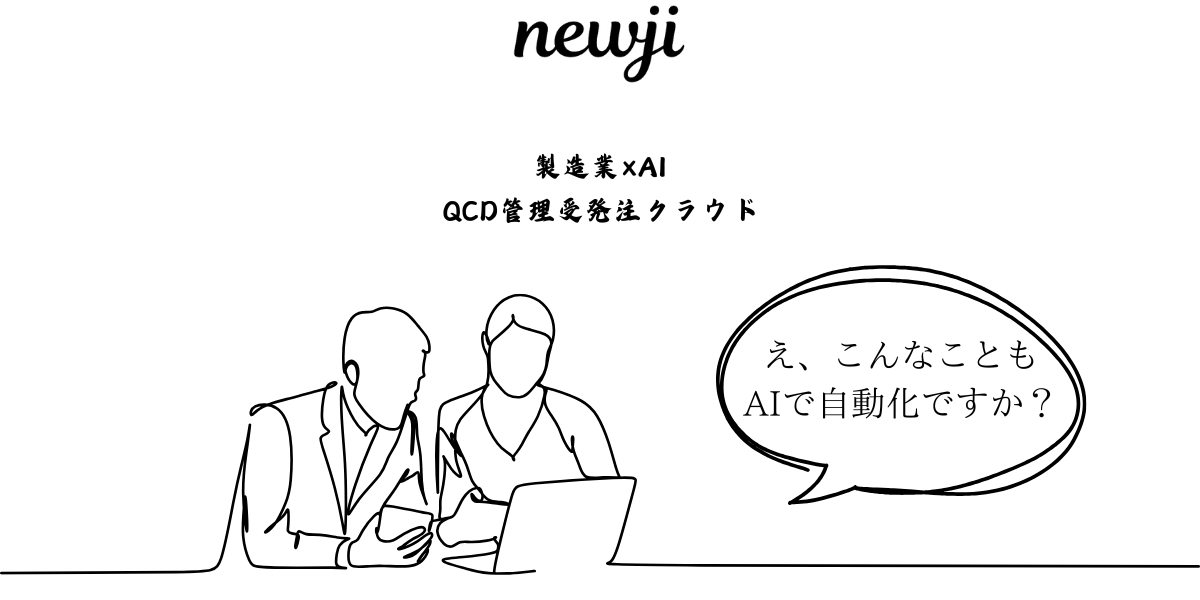
Fundamentals of observing fracture surfaces of metal materials and application to estimating the cause of fracture
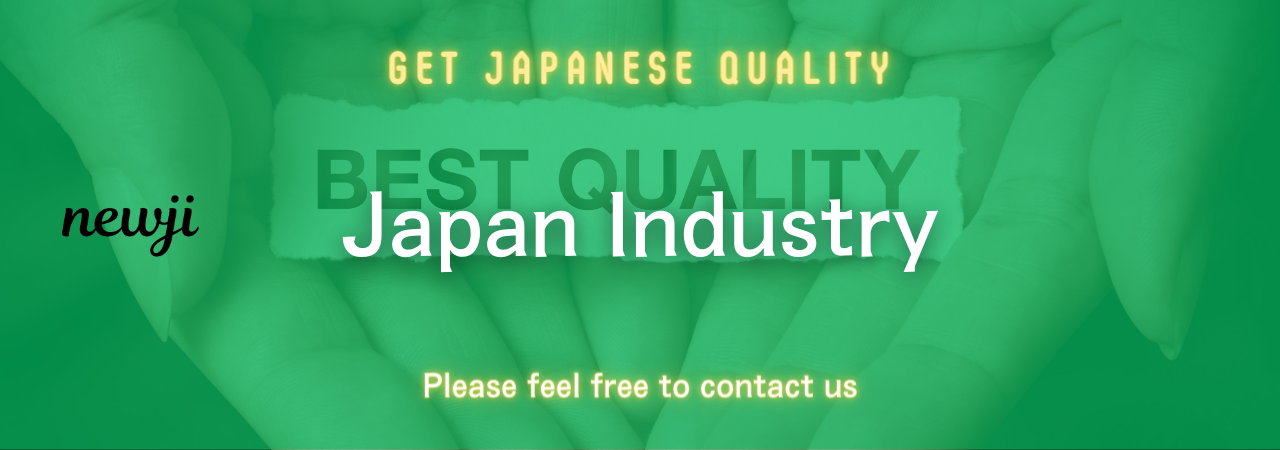
目次
Introduction to Fracture Surfaces
Observing the fracture surfaces of metal materials is a crucial practice in materials science and engineering.
It helps in understanding the reasons behind material failure.
By examining these surfaces, engineers and scientists can deduce how and why a particular metal structure failed.
This understanding can lead to better designs and more resilient materials.
The process is a fundamental part of failure analysis, a field dedicated to the identification and prevention of mechanical failures.
Why Study Fracture Surfaces?
Fracture surfaces can reveal a wealth of information about the failed component.
When a metal part breaks, the surface of the break can tell a story about the forces and conditions that led to the fracture.
Understanding these aspects is key to improving the overall safety and reliability of metal components.
For instance, when a bridge or an airplane part fails, knowing the cause helps prevent similar incidents in the future.
Studying these surfaces enables the development of safer products and environments by improving material and design selection.
Types of Fractures
Brittle Fracture
Brittle fractures occur with little to no plastic deformation prior to the break.
These fractures typically have a clean and often jagged surface.
They often occur suddenly and can propagate at high speeds.
This type of fracture is common in materials subjected to low temperatures or fast loading rates.
Ductile Fracture
Ductile fractures are characterized by significant plastic deformation before the actual fracture.
These surfaces often appear dimpled or torn and usually involve a necking process in tensile tests.
Ductile fracture typically involves a slow progression and absorption of energy before complete failure.
Fatigue Fracture
Fatigue fractures occur under repeated or cyclic loading.
They start as small cracks that grow with continued stress application.
The fracture surface often displays a distinctive pattern, including beach marks or striations, indicative of the progressive failure nature.
Factors Influencing Fracture Surfaces
Material Properties
Different materials respond to stress and loading conditions uniquely.
The inherent toughness, ductility, and composition of a metal influence the fracture characteristics it exhibits.
Materials with high ductility tend to display more significant plastic deformation before failure, influencing the appearance of the fracture surface.
Loading Conditions
The way forces are applied to a metal affects its fracture surface.
Tensile forces might lead to a different fractural appearance compared to shear or compressive forces.
The rate of loading also influences whether the fracture will be brittle or ductile, thus affecting the surface morphology.
Environmental Factors
Environmental conditions, such as temperature and presence of corrosive agents, play a vital role.
Cold environments tend to promote brittle fracture.
Corrosive environments can lead to stress-corrosion cracking, drastically affecting the fracture mechanism and its surface characteristics.
Tools for Observing Fracture Surfaces
Optical Microscopy
Optical microscopy is one of the simplest and most cost-effective methods for examining fracture surfaces.
It offers straightforward, macro-level observations that can highlight larger, more obvious features and aid in initial assessments.
Scanning Electron Microscopy (SEM)
SEM is widely used for detailed surface analysis.
It provides high-resolution images of fracture surfaces, exposing fine details that aren’t visible with the naked eye or optical microscopes.
These details help in understanding the micro-mechanisms of failure.
X-ray Diffraction
X-ray diffraction can help determine the crystalline structure of the material surrounding the fracture.
Understanding these structures aids in identifying loading and environmental histories that might have contributed to the fracture.
Applications in Failure Analysis
Understanding fracture surfaces is integral to failure analysis.
By decoding the history of stresses and material responses, engineers can prevent future failures.
This analysis helps create safer designs in various industries, including aerospace, automotive, and civil engineering.
Failure analysis teams use these insights to recommend material changes or design modifications that could withstand similar operational stresses more effectively.
Learning from failures leads to innovations in materials science and engineering practices, ultimately contributing to the development of smarter, safer materials.
Conclusion
Observing and analyzing the fracture surfaces of metal materials is a fundamental aspect of failure analysis.
The knowledge gained from these observations drives advancements in materials engineering and safety.
Whether preventing catastrophic failures or improving daily-use components, studying fracture surfaces helps ensure the reliability and safety of metal structures across various industries.
This meticulous process requires a blend of theoretical knowledge about fracture mechanics and practical experience with observational tools.
Ultimately, the goal is to use this understanding to minimize failures, protect lives, and forge a future with stronger and more dependable materials.
資料ダウンロード
QCD調達購買管理クラウド「newji」は、調達購買部門で必要なQCD管理全てを備えた、現場特化型兼クラウド型の今世紀最高の購買管理システムとなります。
ユーザー登録
調達購買業務の効率化だけでなく、システムを導入することで、コスト削減や製品・資材のステータス可視化のほか、属人化していた購買情報の共有化による内部不正防止や統制にも役立ちます。
NEWJI DX
製造業に特化したデジタルトランスフォーメーション(DX)の実現を目指す請負開発型のコンサルティングサービスです。AI、iPaaS、および先端の技術を駆使して、製造プロセスの効率化、業務効率化、チームワーク強化、コスト削減、品質向上を実現します。このサービスは、製造業の課題を深く理解し、それに対する最適なデジタルソリューションを提供することで、企業が持続的な成長とイノベーションを達成できるようサポートします。
オンライン講座
製造業、主に購買・調達部門にお勤めの方々に向けた情報を配信しております。
新任の方やベテランの方、管理職を対象とした幅広いコンテンツをご用意しております。
お問い合わせ
コストダウンが利益に直結する術だと理解していても、なかなか前に進めることができない状況。そんな時は、newjiのコストダウン自動化機能で大きく利益貢献しよう!
(Β版非公開)