- お役立ち記事
- Fundamentals of powder, improvement of fluidity/fillability, and key points of mixing technology
Fundamentals of powder, improvement of fluidity/fillability, and key points of mixing technology
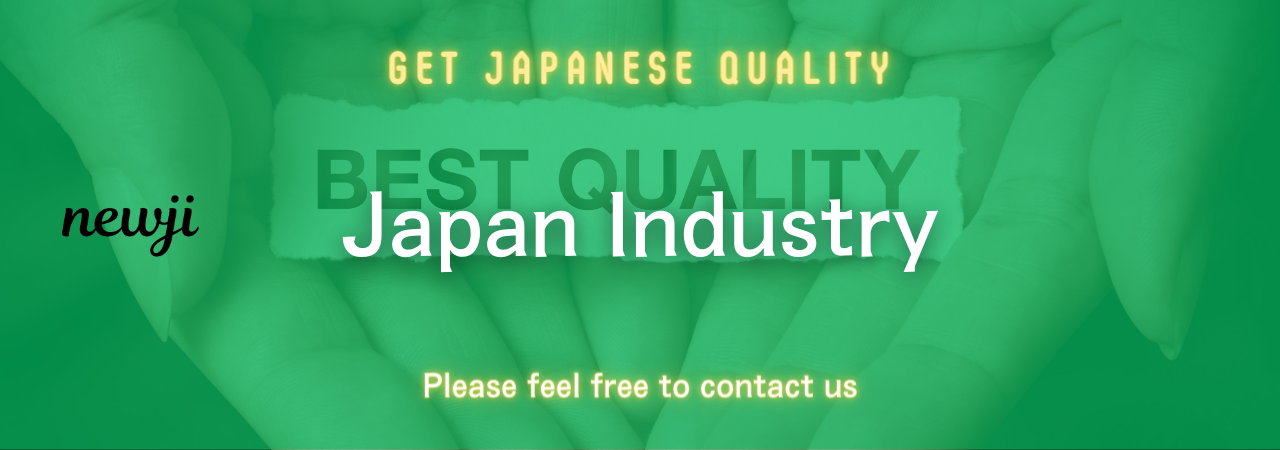
目次
Understanding the Basics of Powder
Powder is a solid substance comprised of fine particles that are quite significant in various industries, including pharmaceuticals, food, cosmetics, and construction.
The behavior of these particles, such as their flow and filling characteristics, determine the quality and efficiency of production processes.
Understanding the fundamentals of powder helps us improve its handling and application.
Powder properties are influenced by several factors, such as particle size, shape, and distribution.
These factors affect how the powder flows, how well it fills containers, and how it blends with other materials.
Moreover, external factors like humidity and temperature also impact the behavior of powder.
Thus, understanding these aspects is crucial for optimizing the use of powder in different applications.
Improving Powder Fluidity
The fluidity of powder refers to its ability to flow smoothly and steadily.
Improved fluidity is essential for smooth processing, as poor flow can cause issues such as blockages in machinery, uneven mixing, and difficulties in packing.
One way to improve flow is by modifying the particle size distribution.
When particles are uniform in size, they tend to flow better due to reduced friction between particles.
Additionally, the addition of flow agents such as silica can also enhance fluidity.
These agents act as lubricants, allowing particles to slide past each other more easily.
Humidity control is another important aspect.
Moisture can lead to clumping, reducing the powder’s ability to flow.
Therefore, maintaining the right environmental conditions can prevent such issues and ensure better flow.
Enhancing Fillability
Fillability is the capability of powder to fill into a designated space or container efficiently.
It is crucial for processes such as packaging, molding, and tableting.
Enhancing fillability ensures that containers are filled uniformly and consistently.
To improve fillability, controlling the particle size is essential.
Smaller and more uniform particles can pack together more efficiently, reducing the air gaps between them.
Selecting the right equipment is also essential.
For example, using devices that vibrate slightly can help ensure that the powder settles evenly within containers.
Such technology facilitates better packing and prevents issues like bridging, where powder forms a bridge across a container, leaving empty spaces below.
Key Points of Mixing Technology
Mixing technology plays a vital role in ensuring that powders integrate thoroughly and evenly with other components.
Effective mixing is necessary for achieving desired product characteristics and ensuring quality.
One key aspect to consider is the choice of mixer.
There are a variety of mixers available, each suitable for different types of powders and applications.
For example, ribbon blenders and paddle mixers are popular choices for their ability to handle large volumes and provide thorough mixing.
The mixing time is another critical factor.
Over or under-mixing can lead to inconsistent product quality, so it is essential to determine the optimal duration for each specific application.
The sequence in which ingredients are added during mixing can also impact the final blend.
In instances where fine and coarse particles are mixed, adding the fine particles first allows them to distribute more evenly throughout the mixture.
Technical Considerations in Mixing
Attention to detail in technical considerations, such as rotation speed, mixing energy, and temperature, can optimize the mixing process.
The right rotation speed varies depending on the characteristics of the powder, while adjusting mixing energy can improve the shearing action that enhances blending.
Temperature control is crucial in preventing issues like melting or degradation of sensitive powder materials, ensuring the integrity of the final product.
Importance of Testing and Evaluation
Regular testing and evaluation of powders during the mixing process are critical to maintaining quality.
Techniques such as laser diffraction for particle size analysis and rheometers for flow behavior measurement are valuable in assessing the performance of powder blends.
These tests help identify potential issues early in the process, allowing for adjustments to improve the final product.
Conclusion
Getting a handle on the basics of powder, its fluidity, fillability, and mixing techniques is vital for multiple industries reliant on these fine materials.
Enhancements in flow and fillability lead to more efficient production, while effective mixing ensures product uniformity.
By focusing on optimizing the particle size, environmental conditions, and employing the right mixing technology, manufacturers can improve both the quality and reliability of their products.
資料ダウンロード
QCD調達購買管理クラウド「newji」は、調達購買部門で必要なQCD管理全てを備えた、現場特化型兼クラウド型の今世紀最高の購買管理システムとなります。
ユーザー登録
調達購買業務の効率化だけでなく、システムを導入することで、コスト削減や製品・資材のステータス可視化のほか、属人化していた購買情報の共有化による内部不正防止や統制にも役立ちます。
NEWJI DX
製造業に特化したデジタルトランスフォーメーション(DX)の実現を目指す請負開発型のコンサルティングサービスです。AI、iPaaS、および先端の技術を駆使して、製造プロセスの効率化、業務効率化、チームワーク強化、コスト削減、品質向上を実現します。このサービスは、製造業の課題を深く理解し、それに対する最適なデジタルソリューションを提供することで、企業が持続的な成長とイノベーションを達成できるようサポートします。
オンライン講座
製造業、主に購買・調達部門にお勤めの方々に向けた情報を配信しております。
新任の方やベテランの方、管理職を対象とした幅広いコンテンツをご用意しております。
お問い合わせ
コストダウンが利益に直結する術だと理解していても、なかなか前に進めることができない状況。そんな時は、newjiのコストダウン自動化機能で大きく利益貢献しよう!
(Β版非公開)