- お役立ち記事
- Fundamentals of production scheduling and key points in designing delivery schedules to shorten lead times
Fundamentals of production scheduling and key points in designing delivery schedules to shorten lead times
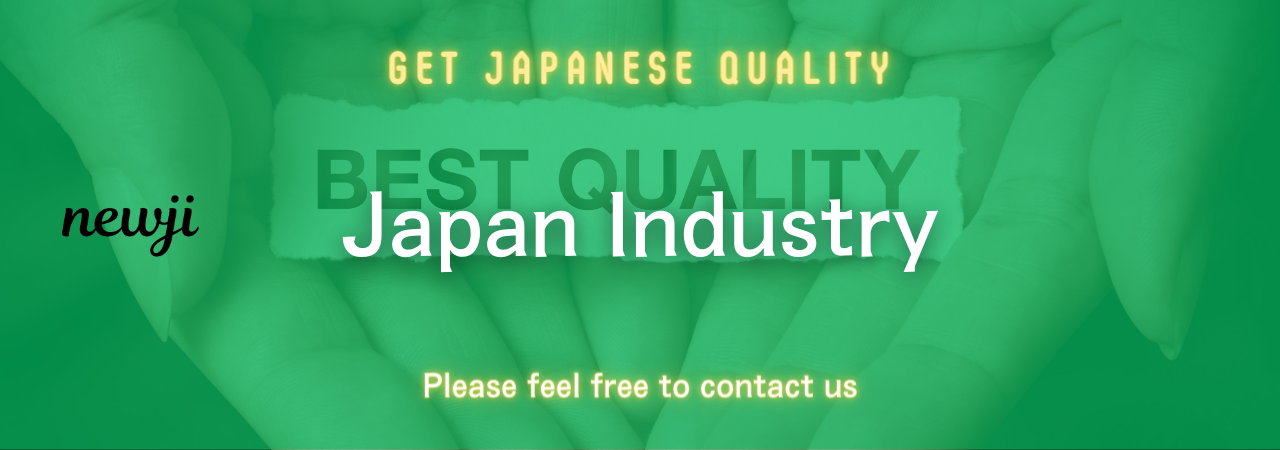
目次
Understanding Production Scheduling
Production scheduling is an essential aspect of manufacturing and service industry operations.
It involves the strategic planning of resources, tasks, and timelines to ensure that products are produced efficiently and delivered on time.
The primary goal of production scheduling is to minimize production costs while optimizing resource utilization and meeting customer demands.
At its core, production scheduling balances the interplay between demand forecasting, inventory management, and resource allocation.
It requires a keen understanding of production capacity, the availability of raw materials, labor, and machinery.
Effective production scheduling can significantly impact a company’s bottom line, customer satisfaction, and overall competitiveness in the marketplace.
Key Elements of Production Scheduling
The production scheduling process involves several key elements that need to be carefully coordinated:
1. **Demand Forecasting**: Accurate demand forecasts are essential to schedule production effectively.
Without a good prediction of customer demand, companies might face overproduction or stockouts, both of which can be costly.
2. **Resource Allocation**: This involves assigning the necessary resources such as labor, machinery, and materials to specific tasks.
Proper allocation ensures that production can proceed smoothly without unnecessary delays.
3. **Production Planning**: This step involves developing a detailed plan that outlines what products are to be produced, the quantities, and the timelines.
Production planning sets the stage for the scheduling process.
4. **Inventory Management**: Keeping track of raw materials and finished goods is crucial.
An efficient inventory system helps prevent shortages and reduces carrying costs.
5. **Capacity Planning**: Understanding the production capacity and adjusting it to meet demand fluctuations is vital to avoid bottlenecks.
Importance of Shortening Lead Times
Lead time refers to the time taken from the initiation of a process to its completion.
In the context of production, it is the period from the placement of an order to the delivery of the product.
Shortening lead times can provide significant advantages such as increased customer satisfaction, reduced inventory costs, and improved cash flow.
Benefits of Shortening Lead Times
1. **Increased Customer Satisfaction**: Shorter lead times mean that customers receive their products faster.
Timely deliveries can enhance customer loyalty and improve business relationships.
2. **Reduced Inventory Costs**: With shorter lead times, companies can operate with lower inventory levels, reducing storage costs and the risk of obsolescence.
3. **Improved Cash Flow**: Faster turnaround times allow businesses to invoice and collect payments more quickly, thereby improving cash flow.
4. **Enhanced Competitiveness**: Companies that can deliver products faster than their competitors often gain a competitive edge in the marketplace.
Designing Delivery Schedules to Shorten Lead Times
Designing effective delivery schedules is crucial for shortening lead times.
An effective delivery schedule takes into account various factors that can influence the lead time.
Key Considerations in Designing Delivery Schedules
1. **Accurate Demand Forecasting**: As mentioned earlier, having precise demand forecasts is critical.
This helps ensure that the delivery schedule aligns with customer expectations without overburdening production resources.
2. **Optimizing Delivery Routes**: Efficient route planning can significantly reduce transportation time.
Using route optimization software can help in finding the shortest and fastest paths for delivery vehicles.
3. **Improving Production Processes**: Streamlining production processes to eliminate waste and inefficiencies can shorten internal lead times.
Implementing lean manufacturing principles can be beneficial in this regard.
4. **Leveraging Technology**: Utilizing advanced software solutions for scheduling and tracking deliveries can enhance the accuracy and efficiency of delivery schedules.
5. **Collaborating with Suppliers**: Maintaining good relationships with suppliers can ensure that raw materials are delivered on time, reducing lead times and preventing production delays.
6. **Cross-Training Employees**: Having a flexible workforce by cross-training employees can help minimize disruptions if a particular team member is unavailable, maintaining production flow.
Continuous Improvement and Monitoring
Once the delivery schedules are in place, continuous monitoring and improvement are necessary to maintain their effectiveness.
– **Feedback Loops**: Establishing feedback mechanisms with customers to understand their satisfaction and identifying any delays can help improve delivery schedules.
– **Performance Metrics**: Setting up key performance indicators (KPIs) to evaluate the efficiency and effectiveness of production and delivery processes is crucial.
Regular reviews can highlight areas for improvement.
– **Adapting to Changes**: Being prepared to adapt schedules in response to changes in demand patterns, market conditions, or operational challenges is essential for maintaining efficiency.
In conclusion, the fundamentals of production scheduling and designing effective delivery schedules are crucial for any business aiming to shorten lead times.
By understanding and implementing the key elements of production scheduling and focusing on critical aspects of delivery scheduling, businesses can improve their operational efficiency, customer satisfaction, and competitive standing in the market.
資料ダウンロード
QCD調達購買管理クラウド「newji」は、調達購買部門で必要なQCD管理全てを備えた、現場特化型兼クラウド型の今世紀最高の購買管理システムとなります。
ユーザー登録
調達購買業務の効率化だけでなく、システムを導入することで、コスト削減や製品・資材のステータス可視化のほか、属人化していた購買情報の共有化による内部不正防止や統制にも役立ちます。
NEWJI DX
製造業に特化したデジタルトランスフォーメーション(DX)の実現を目指す請負開発型のコンサルティングサービスです。AI、iPaaS、および先端の技術を駆使して、製造プロセスの効率化、業務効率化、チームワーク強化、コスト削減、品質向上を実現します。このサービスは、製造業の課題を深く理解し、それに対する最適なデジタルソリューションを提供することで、企業が持続的な成長とイノベーションを達成できるようサポートします。
オンライン講座
製造業、主に購買・調達部門にお勤めの方々に向けた情報を配信しております。
新任の方やベテランの方、管理職を対象とした幅広いコンテンツをご用意しております。
お問い合わせ
コストダウンが利益に直結する術だと理解していても、なかなか前に進めることができない状況。そんな時は、newjiのコストダウン自動化機能で大きく利益貢献しよう!
(Β版非公開)