- お役立ち記事
- Fundamentals of the “5 Whys” Analysis
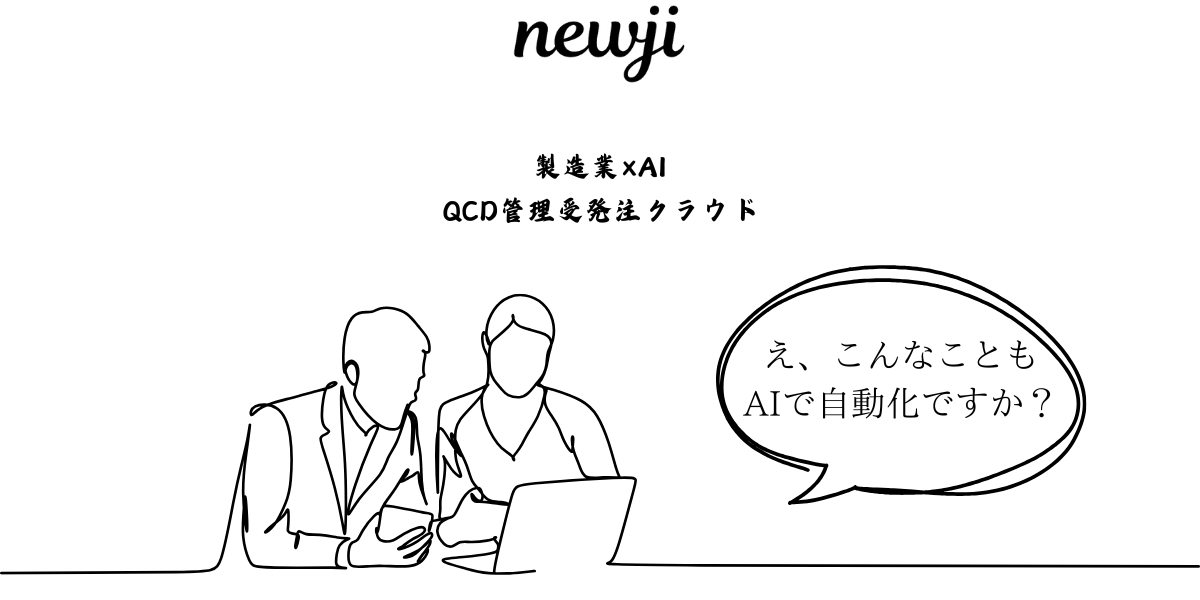
Fundamentals of the “5 Whys” Analysis
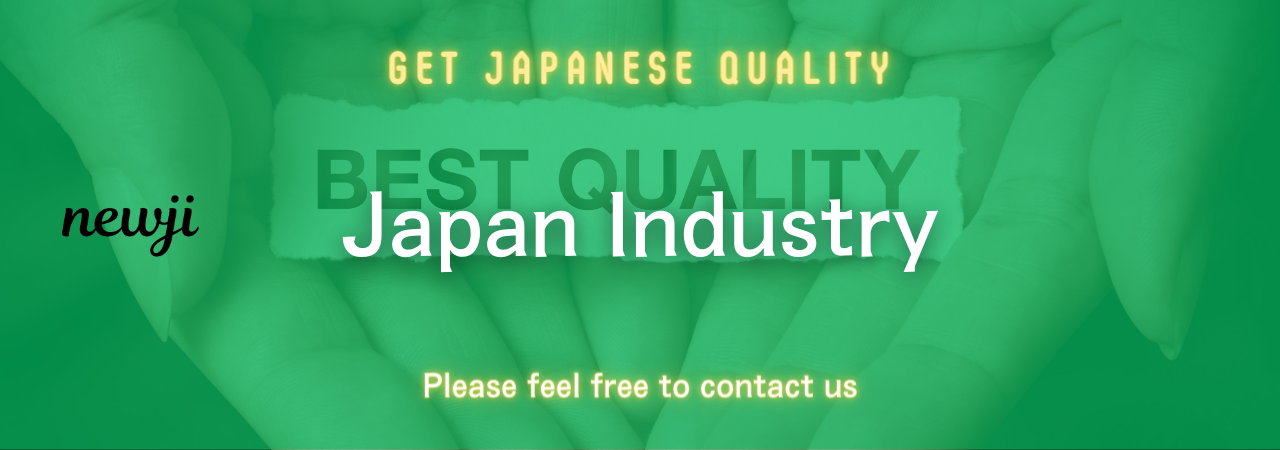
The “5 Whys” analysis is a simple yet powerful tool for problem-solving.
It’s an approach that anyone can use, whether you’re trying to figure out why your computer isn’t working or why your plant isn’t growing.
This method is used across various industries and fields to get to the root cause of issues.
By continually asking “why,” you can dive deeper into the problem, clarifying the fundamental cause behind it.
In this article, we will explore the fundamentals of the “5 Whys” analysis, how to use it, and its benefits.
目次
What is the “5 Whys” Analysis?
The “5 Whys” analysis is a technique developed by Sakichi Toyoda, the founder of Toyota Industries.
It is part of the Lean manufacturing principles and the Toyota Production System.
The main goal is to identify the root cause of a problem by repeatedly asking the question “why?”—five times is the standard number, though it can be more or less depending on the issue’s complexity.
How Does It Work?
The process of “5 Whys” is straightforward.
When a problem arises, you start by clearly stating the problem.
Then, you ask why the problem happened and write down the answer.
Next, you take that answer and ask “why” again.
You do this repeatedly, ideally five times, until you uncover the root cause of the issue.
Here’s a simplified example:
1. The car won’t start. (Problem)
2. Why? The battery is dead.
3. Why? The alternator isn’t functioning.
4. Why? The alternator belt broke.
5. Why? The belt was well beyond its useful service life and was never replaced.
6. Why? The car was not maintained according to the recommended service schedule.
As you can see, the fifth why in this example exposes the root cause of the failure, which is a lack of proper maintenance.
Why Use the “5 Whys” Analysis?
There are several reasons why the “5 Whys” analysis is a valuable tool for problem-solving.
Simplicity
One of the primary benefits of this method is its simplicity.
You don’t need specialized knowledge or advanced tools to perform a “5 Whys” analysis.
This makes it accessible for anyone, from children to professionals in various fields.
Gets to the Root Cause
Many problem-solving methods only address surface issues.
The “5 Whys” analysis ensures that you delve deeper, identifying what’s truly causing the problem rather than just treating symptoms.
Encourages Critical Thinking
Using the “5 Whys” requires critical thinking and analysis.
This helps individuals and teams think more deeply about issues and encourages a learning mindset.
It pushes people to move beyond initial assumptions and explore interconnected causes.
When to Use the “5 Whys” Analysis?
The “5 Whys” analysis can be used in various situations, from everyday problems to complex business issues.
Everyday Problems
Whether you’re dealing with a household issue like a clogged sink or a personal challenge such as managing time better, the “5 Whys” can help uncover the true cause.
Business and Industry Applications
In the business world, this method is often used in quality control, project management, and troubleshooting equipment failures.
For example, if a manufacturing process has a defect, using the “5 Whys” can help identify whether the root cause is due to human error, machinery, materials, or methods.
Educational Contexts
Teachers can also use the “5 Whys” analysis to help students think critically about various academic questions or during scientific investigations.
This approach can foster a deeper understanding of subject matter by encouraging inquiry and curiosity.
Steps to Conduct a “5 Whys” Analysis
Executing a “5 Whys” analysis involves several steps.
Step 1: Assemble a Team
If you are solving a problem in a business or educational setting, gather a team with diverse backgrounds and expertise.
This ensures different perspectives are considered.
Step 2: Define the Problem
Clearly articulate the problem you are facing.
Be specific and precise so that everyone involved understands the issue at hand.
Step 3: Ask the First “Why”
Pose the question “Why did this problem occur?” Write down the answer as it will be the basis for the next “why.”
Step 4: Ask Subsequent “Whys”
Continue asking “why” based on the previous answer.
Write down each response until you have asked “why” five times, or until you can’t go any deeper.
Step 5: Take Corrective Action
Once the root cause is identified, brainstorm corrective measures to prevent the issue from recurring.
Put these actions into practice and monitor their effectiveness over time.
Challenges and Limitations
While the “5 Whys” analysis is a robust method, it has some limitations.
Subjectivity
The answers to the “whys” can be subjective, based on the perspectives and biases of the team members conducting the analysis.
This may result in focusing on symptoms rather than the underlying problems.
Not Always Suitable for Complex Issues
For complex problems with multiple root causes, the “5 Whys” might not be sufficient.
In such cases, more detailed analysis techniques like Failure Mode and Effects Analysis (FMEA) or Root Cause Analysis (RCA) might be required.
Conclusion
The “5 Whys” analysis is an invaluable tool for determining the root cause of problems.
Its simplicity makes it accessible, yet it forces deep critical thinking that can reveal hidden issues.
By following the outlined steps and being aware of its limitations, you can effectively use the “5 Whys” to solve problems in various contexts.
Whether it’s for everyday challenges, business troubleshooting, or educational purposes, the “5 Whys” method helps get to the heart of the matter, offering solutions that are both effective and lasting.
資料ダウンロード
QCD調達購買管理クラウド「newji」は、調達購買部門で必要なQCD管理全てを備えた、現場特化型兼クラウド型の今世紀最高の購買管理システムとなります。
ユーザー登録
調達購買業務の効率化だけでなく、システムを導入することで、コスト削減や製品・資材のステータス可視化のほか、属人化していた購買情報の共有化による内部不正防止や統制にも役立ちます。
NEWJI DX
製造業に特化したデジタルトランスフォーメーション(DX)の実現を目指す請負開発型のコンサルティングサービスです。AI、iPaaS、および先端の技術を駆使して、製造プロセスの効率化、業務効率化、チームワーク強化、コスト削減、品質向上を実現します。このサービスは、製造業の課題を深く理解し、それに対する最適なデジタルソリューションを提供することで、企業が持続的な成長とイノベーションを達成できるようサポートします。
オンライン講座
製造業、主に購買・調達部門にお勤めの方々に向けた情報を配信しております。
新任の方やベテランの方、管理職を対象とした幅広いコンテンツをご用意しております。
お問い合わせ
コストダウンが利益に直結する術だと理解していても、なかなか前に進めることができない状況。そんな時は、newjiのコストダウン自動化機能で大きく利益貢献しよう!
(Β版非公開)