- お役立ち記事
- Gas Supply System Design for Semiconductor Manufacturing Equipment
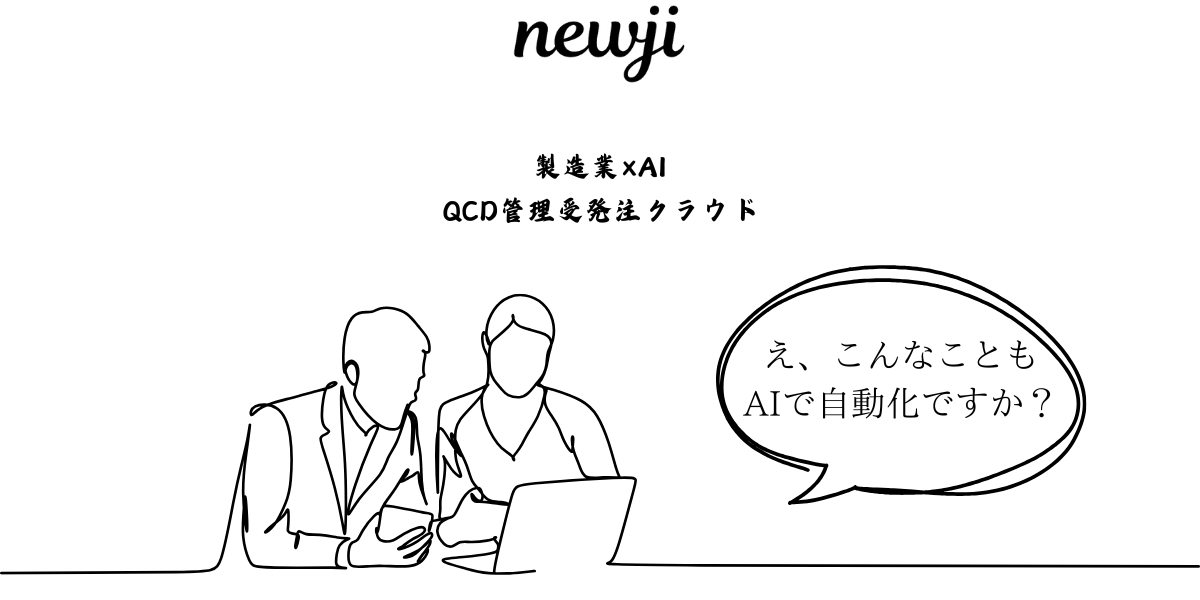
Gas Supply System Design for Semiconductor Manufacturing Equipment
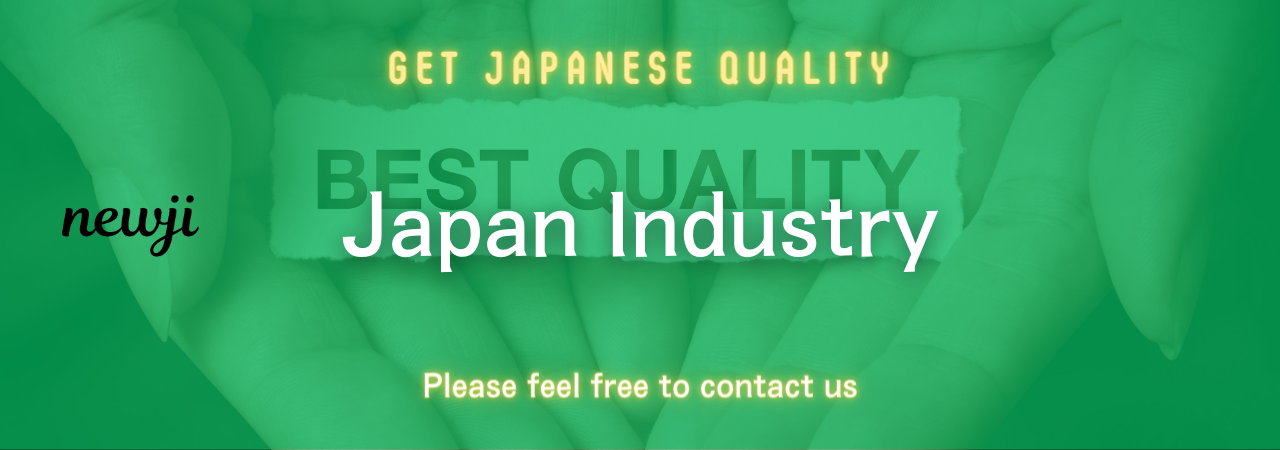
Gas supply systems play a crucial role in the functioning of semiconductor manufacturing equipment.
These systems ensure that the gases required for various manufacturing processes are delivered with precision and stability.
Let’s explore the fundamental aspects of designing a gas supply system for semiconductor fabs.
目次
Understanding the Role of Gas in Semiconductor Manufacturing
Gases are integral to many processes in the semiconductor industry.
They are used in thin-film deposition, etching, doping, and cleaning operations.
Common gases include nitrogen, hydrogen, oxygen, and various specialty gases like silane and phosphine.
A reliable gas supply system must be in place to ensure these processes run smoothly and efficiently.
The Importance of Gas Purity
One of the primary concerns in semiconductor manufacturing is the purity of gases.
Impurities can lead to defects in the semiconductor devices, which can affect their performance and reliability.
Therefore, gas supply systems must include filters and purifiers to ensure the gases are of ultra-high purity before they reach the manufacturing equipment.
Key Components of a Gas Supply System
Designing a gas supply system requires careful consideration of several key components:
Gas Storage
Gas storage units, such as cylinders and bulk tanks, are used to store gases before they are transported to the point of use.
These storage units must be designed to handle the specific pressure and volume requirements of each gas.
Safety is a paramount concern, so storage units must comply with industry standards and regulations.
Gas Delivery Lines
Gas delivery lines transport gases from storage units to the manufacturing equipment.
These lines need to be resistant to corrosion and contamination.
Materials like stainless steel and specialty polymers are commonly used.
The design should include proper routing and installation to minimize any potential leaks.
Regulators and Flow Controls
Regulators control the pressure of gas as it moves through the delivery system.
They ensure that the gas is delivered at the correct pressure required by the manufacturing process.
Flow control devices like mass flow controllers (MFCs) are used to precisely control the amount of gas flowing to the process equipment.
Accurate pressure and flow control are critical to achieving high-quality manufacturing outcomes.
Designing for Safety and Efficiency
A well-designed gas supply system not only meets the operational needs but also ensures safety and efficiency.
Safety Systems
Safety systems include alarms, shut-off valves, and pressure relief devices.
These components are essential to prevent accidents and handle emergency situations.
For instance, gas detection systems can monitor for leaks and automatically shut off the supply if a hazardous level of gas is detected.
Redundancy and Backup Systems
To maintain continuous operation, it is advisable to include redundancy and backup systems in the design.
This can involve having multiple storage units, additional delivery lines, and backup regulators.
If a failure occurs in one part of the system, the backup can take over without interrupting the manufacturing process.
Efficiency in Gas Usage
Efficient use of gases not only reduces costs but also minimizes environmental impact.
Flow controllers should be calibrated regularly to ensure accuracy.
Monitoring systems can be implemented to track gas usage and identify any inefficiencies or wastage.
Considerations for Specialty Gases
Specialty gases, used for specific manufacturing processes, require additional considerations in the system design.
Handling Hazardous Gases
Many specialty gases can be hazardous.
Gases like silane and phosphine are highly reactive and toxic.
Special storage containers and delivery systems should be used to handle these gases safely.
Ventilation systems and gas scrubbing units are often installed to neutralize any hazardous gases in the event of a leak.
Ensuring Compatibility
Different gases can react with each other, causing contamination or hazardous conditions.
The design must ensure that delivery lines, valves, and other components are compatible with the specific gases they will transport.
Materials chosen for these components should be inert to avoid any adverse reactions.
Regular Maintenance and Monitoring
An effective gas supply system requires regular maintenance and monitoring.
Routine Inspections
Regular inspections should be carried out to check for any signs of wear, corrosion, or leaks.
These inspections ensure that all components are functioning properly and safely.
Monitoring Systems
Advanced monitoring systems can provide real-time data on gas flow, pressure, and usage.
This data can be used to optimize system performance and quickly identify any issues.
Remote monitoring capabilities allow technicians to oversee the system from anywhere, improving responsiveness.
Conclusion
Designing a gas supply system for semiconductor manufacturing equipment involves a detailed understanding of the gases used, their specific requirements, and the manufacturing processes they support.
Focus on purity, safety, efficiency, and regular maintenance ensures a reliable system that supports high-quality semiconductor production.
By considering these aspects, you can develop a system that enhances performance and ensures the safe and efficient operation of semiconductor manufacturing equipment.
資料ダウンロード
QCD調達購買管理クラウド「newji」は、調達購買部門で必要なQCD管理全てを備えた、現場特化型兼クラウド型の今世紀最高の購買管理システムとなります。
ユーザー登録
調達購買業務の効率化だけでなく、システムを導入することで、コスト削減や製品・資材のステータス可視化のほか、属人化していた購買情報の共有化による内部不正防止や統制にも役立ちます。
NEWJI DX
製造業に特化したデジタルトランスフォーメーション(DX)の実現を目指す請負開発型のコンサルティングサービスです。AI、iPaaS、および先端の技術を駆使して、製造プロセスの効率化、業務効率化、チームワーク強化、コスト削減、品質向上を実現します。このサービスは、製造業の課題を深く理解し、それに対する最適なデジタルソリューションを提供することで、企業が持続的な成長とイノベーションを達成できるようサポートします。
オンライン講座
製造業、主に購買・調達部門にお勤めの方々に向けた情報を配信しております。
新任の方やベテランの方、管理職を対象とした幅広いコンテンツをご用意しております。
お問い合わせ
コストダウンが利益に直結する術だと理解していても、なかなか前に進めることができない状況。そんな時は、newjiのコストダウン自動化機能で大きく利益貢献しよう!
(Β版非公開)