- お役立ち記事
- How SMEs can enhance internal and external collaboration to optimize purchasing management
How SMEs can enhance internal and external collaboration to optimize purchasing management
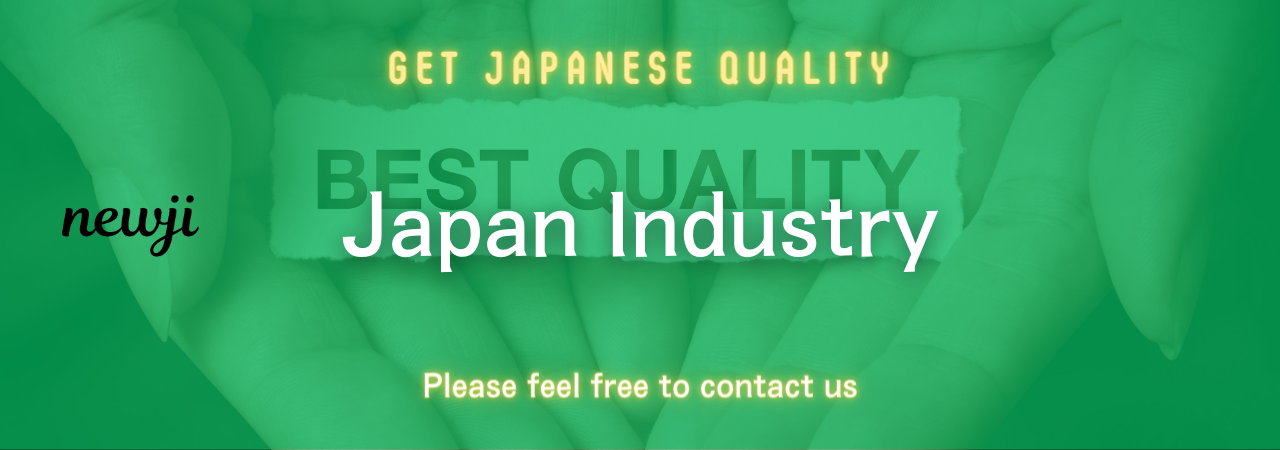
For small and medium-sized enterprises (SMEs), managing purchasing efficiently can be a real challenge. With limited resources, these businesses often struggle to strike a balance between cost-effectiveness and maintaining strong supplier relationships. However, improving internal and external collaboration can help SMEs optimize their purchasing management, ultimately leading to better operational efficiency and cost savings. This article will provide actionable tips on how SMEs can enhance collaboration both internally and externally to improve their purchasing processes.
Importance of Internal Collaboration
Internal collaboration refers to the cooperative efforts among employees and departments within an organization. In the context of purchasing management, internal collaboration ensures that all relevant teams are on the same page regarding procurement strategies, budgets, and priorities. Here’s how SMEs can foster better internal collaboration:
1. Implement Cross-Functional Teams
Creating cross-functional teams that include members from different departments such as sales, finance, and inventory management can lead to more balanced decision-making. These teams can meet regularly to discuss purchasing needs, evaluate suppliers, and ensure that procurement decisions align with the company’s overall objectives.
2. Utilize Technology
Leveraging technology can dramatically improve internal communication and collaboration. Tools like project management software, communication platforms (e.g., Slack, Microsoft Teams), and collaborative document editors (e.g., Google Docs) can make it easier for teams to share information in real-time, track the progress of purchasing projects, and store important documents.
3. Develop Clear Procurement Policies
Establishing clear procurement policies and procedures ensures that everyone involved in purchasing understands their roles and responsibilities. This can help streamline processes and reduce misunderstandings. Make sure to document these policies and communicate them to all relevant employees.
4. Train Employees
Regular training sessions can keep employees informed about the latest procurement practices and technologies. Offering professional development opportunities related to purchasing management can empower staff to contribute more effectively to the procurement process.
Strengthening External Collaboration
External collaboration involves working closely with suppliers, vendors, and other external partners. Building strong relationships with these stakeholders is crucial for optimizing purchasing management. Here are four strategies to enhance external collaboration:
1. Communicate Clearly and Regularly
Maintaining open lines of communication with suppliers is vital. Regular meetings, email updates, and even casual check-ins can help keep suppliers informed about your business needs and any upcoming changes. Always be clear about your expectations and requirements to avoid any misunderstandings.
2. Build Long-Term Relationships
Establishing long-term partnerships with key suppliers can offer numerous benefits, including better pricing, priority in supply during shortages, and more favorable payment terms. Invest time in understanding your suppliers’ businesses and challenges, and show a willingness to collaborate on solutions.
3. Implement Supplier Performance Management
Monitoring supplier performance through regular assessments can help identify areas of improvement. Set key performance indicators (KPIs) related to timely delivery, quality of goods, and responsiveness. Share these metrics with suppliers to encourage transparency and collective problem-solving.
4. Leverage Technology for Supplier Management
Just as technology can enhance internal collaboration, it can also improve how you interact with suppliers. Supplier relationship management (SRM) software can be used to automate and streamline many aspects of supplier interaction, from order processing to performance monitoring.
Alignment Between Internal and External Collaboration
For the best results, internal and external collaboration efforts must be aligned. Here are some ways to ensure seamless integration:
1. Collaborative Planning
Involve both internal teams and key suppliers in strategic planning sessions. This facilitates a better understanding of each other’s capabilities and limitations and helps in synchronizing expectations and goals.
2. Transparency
Maintain transparency with both your internal teams and suppliers about budgets, timelines, and challenges. When everyone is aware of the big picture, they’re more likely to work together effectively.
3. Standardized Processes
Standardize your procurement processes so that both internal teams and suppliers understand the workflow. This can prevent bottlenecks and ensure consistency in procurement activities.
4. Feedback Loops
Create feedback loops where internal teams can share their experiences and insights with suppliers and vice-versa. This two-way communication can uncover valuable insights and drive continuous improvement in the procurement process.
Case Study: Successful Collaborative Purchasing Management
Consider a mid-sized manufacturer that was struggling with supply chain disruptions and rising costs. By forming a cross-functional team that included members from procurement, production, and finance, the company was able to better assess its actual needs and align its purchasing strategies accordingly. The team implemented a centralized procurement system that allowed for real-time tracking of orders and inventory levels.
In parallel, the manufacturer initiated a supplier development program aimed at building stronger relationships with its key suppliers. They conducted regular performance reviews and collaborated with suppliers on cost-reduction initiatives, ultimately leading to improved supplier performance and reduced procurement costs.
By enhancing both internal and external collaboration, the company was able to stabilize its supply chain, improve cost-efficiency, and ensure the consistent quality of its products.
Conclusion
Optimizing purchasing management through enhanced internal and external collaboration is not just beneficial but essential for SMEs aiming for long-term success. By fostering better teamwork within the organization, maintaining clear communication with suppliers, and aligning both efforts, SMEs can significantly improve their purchasing processes. These improvements can result in cost savings, more reliable supply chains, and better overall operational efficiency.
So, take the time to evaluate and improve how your business collaborates internally and externally. The benefits will be well worth the effort.
資料ダウンロード
QCD調達購買管理クラウド「newji」は、調達購買部門で必要なQCD管理全てを備えた、現場特化型兼クラウド型の今世紀最高の購買管理システムとなります。
ユーザー登録
調達購買業務の効率化だけでなく、システムを導入することで、コスト削減や製品・資材のステータス可視化のほか、属人化していた購買情報の共有化による内部不正防止や統制にも役立ちます。
NEWJI DX
製造業に特化したデジタルトランスフォーメーション(DX)の実現を目指す請負開発型のコンサルティングサービスです。AI、iPaaS、および先端の技術を駆使して、製造プロセスの効率化、業務効率化、チームワーク強化、コスト削減、品質向上を実現します。このサービスは、製造業の課題を深く理解し、それに対する最適なデジタルソリューションを提供することで、企業が持続的な成長とイノベーションを達成できるようサポートします。
オンライン講座
製造業、主に購買・調達部門にお勤めの方々に向けた情報を配信しております。
新任の方やベテランの方、管理職を対象とした幅広いコンテンツをご用意しております。
お問い合わせ
コストダウンが利益に直結する術だと理解していても、なかなか前に進めることができない状況。そんな時は、newjiのコストダウン自動化機能で大きく利益貢献しよう!
(Β版非公開)