- お役立ち記事
- How to achieve cost reduction using VE/VA techniques that mid-level employees in the production management department should know
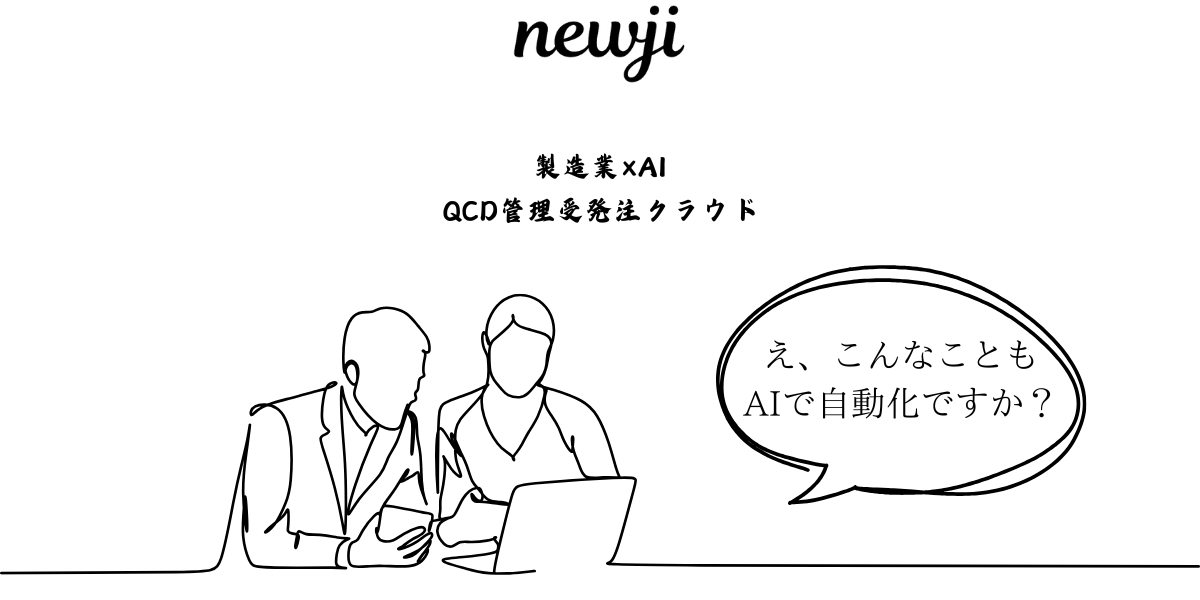
How to achieve cost reduction using VE/VA techniques that mid-level employees in the production management department should know
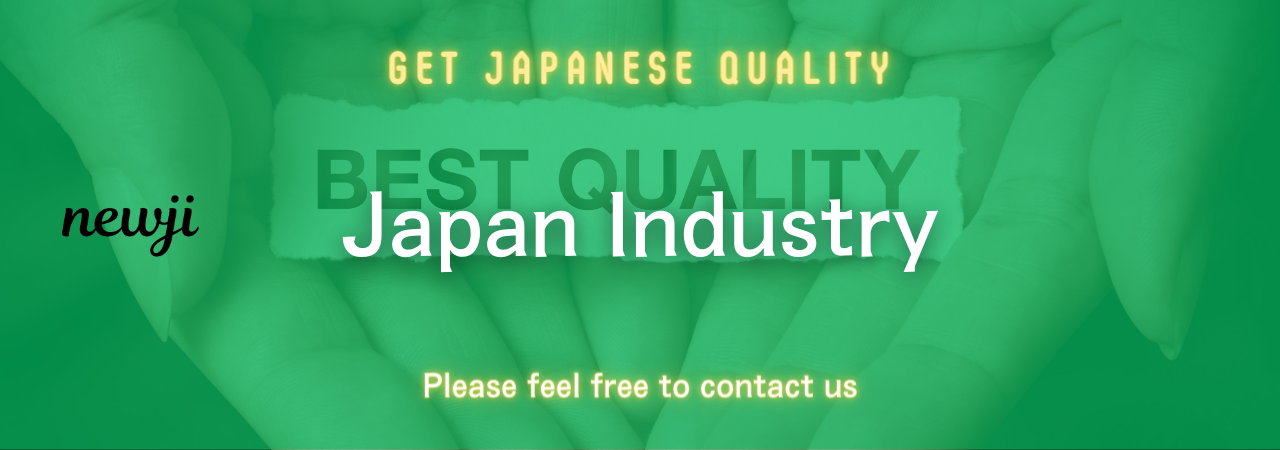
目次
Understanding VE/VA Techniques
Value Engineering (VE) and Value Analysis (VA) are systematic approaches used to improve the value of a product or a process by optimizing its function to reduce costs without compromising on quality.
Originating in the manufacturing sector, these techniques have been instrumental in identifying unnecessary costs, thus helping businesses enhance their products or services’ value.
Understanding these methods can aid mid-level employees in the production management department in contributing significantly to cost reduction efforts.
The Difference Between VE and VA
Though often used interchangeably, there is a subtle difference between VE and VA.
Value Engineering (VE) is a proactive, creative method focused on the design phase.
It aims to prevent unnecessary costs from being built-in at the start of a project.
VE is predominantly used before production begins, providing an opportunity to redesign the project with cost efficiency in mind.
Value Analysis (VA), on the other hand, is a retrospective exercise applied to existing products or processes.
It involves analyzing the functionality and costs to identify areas where savings can be made without affecting overall performance.
VA can be performed at any point in the product lifecycle.
Benefits of Implementing VE/VA Techniques
Implementing VE/VA techniques can provide several advantages to a company.
The most prominent benefit is cost reduction.
By identifying redundancies or inefficiencies in a process or product, companies can make informed decisions that lead to more economical operations.
Additionally, these techniques promote innovation and creativity as employees are encouraged to think critically about design and function.
They are pushed to find novel solutions to reduce costs, which can lead to breakthrough innovations.
Moreover, by focusing on customer needs and preferences, VE/VA ensures that products retain their quality while potentially offering additional features, thereby increasing customer satisfaction.
This can help companies maintain competitive advantages in the market.
Implementing VE/VA in the Production Management Department
Mid-level employees in the production management department play a crucial role in cost reduction initiatives through VE/VA.
Here are some steps they can follow to implement these techniques effectively.
1. Team Formation and Training
Forming a dedicated VE/VA team is the first step.
This team should include cross-functional members from various departments such as design, production, procurement, and finance to provide diverse perspectives on cost-saving possibilities.
Adequate training should be provided to staff to familiarize them with VE/VA methodologies, tools, and techniques.
2. Identifying Key Areas for Analysis
Employees should focus on identifying products or processes with the highest potential for cost reduction.
Consider factors such as frequent customer complaints, high production costs, or increased competition.
By prioritizing items with the greatest cost-saving potential, teams ensure their efforts yield the best results.
3. Conducting Value Analysis
The next step involves an in-depth analysis of the selected products or processes.
Teams must evaluate the functions each component performs and the cost associated with each.
By employing a systematic approach like the FAST (Function Analysis System Technique) diagram, teams can identify areas where value improvements can be made.
4. Ideation and Alternative Solutions
Once key areas have been identified, the focus shifts to generating creative solutions.
Brainstorming sessions can help generate multiple ideas on how to redesign or modify existing components, materials, or processes to enhance value.
Each alternative solution should be evaluated for feasibility, cost savings, and potential impacts on product quality.
5. Selecting the Best Solutions
After generating potential solutions, the team should select the most effective and viable options.
This involves comparing the costs and benefits of each solution and considering implementation constraints.
Select solutions that offer significant cost reductions while maintaining or enhancing product quality.
6. Implementation and Monitoring
With solutions selected, the next step is implementation.
This involves coordinating with relevant departments to execute changes in the production process, supply chain, or product design.
Continual monitoring and evaluation are vital to ensure that initiatives deliver the expected cost savings and do not negatively affect the quality or customer satisfaction.
Overcoming Challenges in VE/VA Implementation
Transitioning to a VE/VA-oriented process might come with challenges such as resistance to change, initial cost outlay, or time constraints.
To overcome these, employees can:
1. Foster a Culture of Continuous Improvement
Organizations should promote a culture where ideas for cost-saving and efficiency are welcomed and rewarded.
This encourages employee buy-in and participation in VE/VA efforts.
2. Secure Management Support
Strong backing from leadership and management ensures that VE/VA initiatives receive the necessary resources and attention.
Having management champions this as a priority makes it easier to navigate any disruptions these changes might cause.
3. Communicate Benefits Clearly
Effectively communicating the long-term benefits of VE/VA systems to all stakeholders helps break down resistance.
Employees need to understand how these techniques will benefit their roles and the organization at large.
Conclusion
For mid-level employees in the production management department, mastering VE/VA techniques offers an opportunity to contribute significantly to an organization’s cost reduction goals.
By systematically analyzing products and processes, identifying inefficiencies, and implementing innovative solutions, teams can enhance overall value without compromising quality.
As these techniques not only cut costs but also encourage innovation and improve customer satisfaction, they are a valuable addition to any production management strategy.
資料ダウンロード
QCD調達購買管理クラウド「newji」は、調達購買部門で必要なQCD管理全てを備えた、現場特化型兼クラウド型の今世紀最高の購買管理システムとなります。
ユーザー登録
調達購買業務の効率化だけでなく、システムを導入することで、コスト削減や製品・資材のステータス可視化のほか、属人化していた購買情報の共有化による内部不正防止や統制にも役立ちます。
NEWJI DX
製造業に特化したデジタルトランスフォーメーション(DX)の実現を目指す請負開発型のコンサルティングサービスです。AI、iPaaS、および先端の技術を駆使して、製造プロセスの効率化、業務効率化、チームワーク強化、コスト削減、品質向上を実現します。このサービスは、製造業の課題を深く理解し、それに対する最適なデジタルソリューションを提供することで、企業が持続的な成長とイノベーションを達成できるようサポートします。
オンライン講座
製造業、主に購買・調達部門にお勤めの方々に向けた情報を配信しております。
新任の方やベテランの方、管理職を対象とした幅広いコンテンツをご用意しております。
お問い合わせ
コストダウンが利益に直結する術だと理解していても、なかなか前に進めることができない状況。そんな時は、newjiのコストダウン自動化機能で大きく利益貢献しよう!
(Β版非公開)