- お役立ち記事
- How to Conduct Quality Audits and Case Studies of Improvements in Manufacturing Quality Assurance
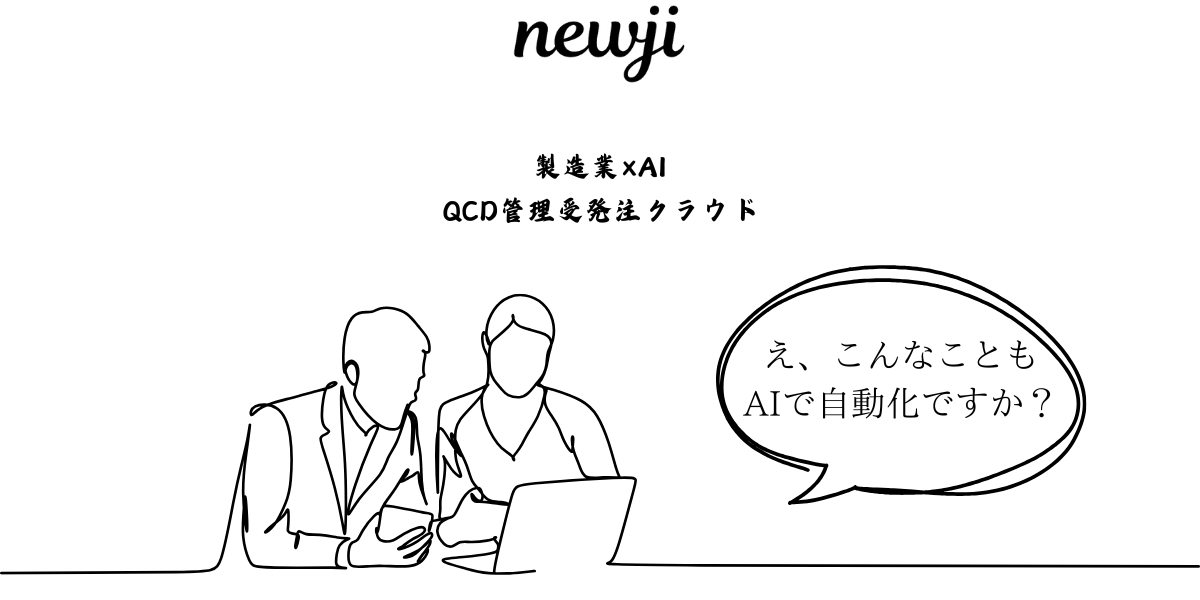
How to Conduct Quality Audits and Case Studies of Improvements in Manufacturing Quality Assurance
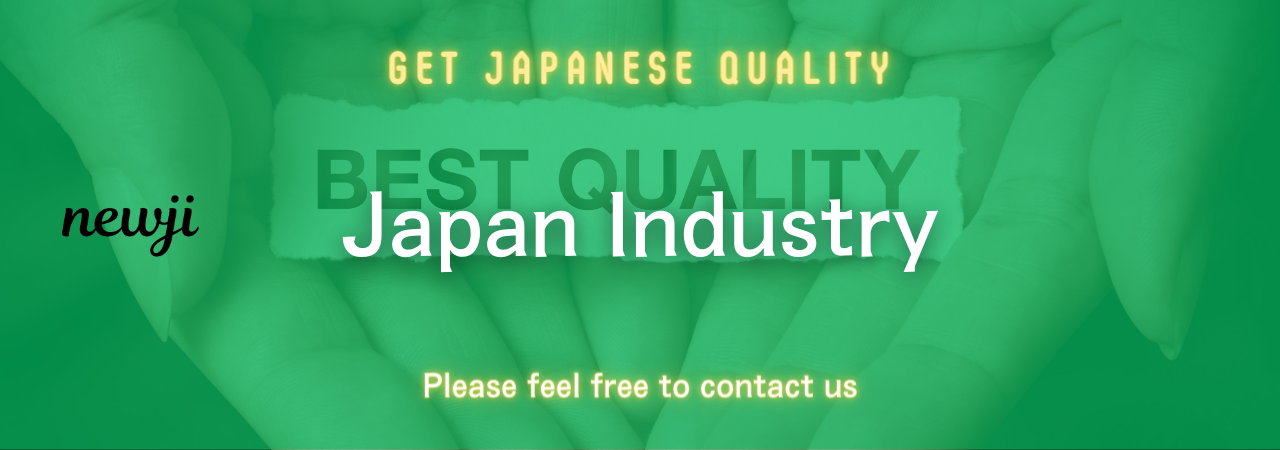
目次
Understanding Quality Audits in Manufacturing
Quality audits in manufacturing are thorough assessments meant to ensure that processes, products, and systems meet certain standards.
These audits help companies maintain high-quality production and identify areas needing improvement.
When conducted regularly, quality audits can prevent costly errors and enhance overall operational efficiency.
A quality audit typically involves examining processes, checking compliance with industry regulations, and verifying that documentation is up to date.
Auditors may look at production lines, review management practices, and interview staff.
The goal is to identify gaps in quality control and recommend corrective measures.
Steps to Conducting a Quality Audit
1. Define Objectives and Scope
Before starting a quality audit, it’s crucial to define its objectives and scope.
What specific area or process will you be auditing?
Clearly outlining these parameters helps create a focused and effective audit plan.
2. Assemble an Audit Team
Forming a competent audit team is the next critical step.
This team should consist of individuals who have expertise in the area being audited and an understanding of quality standards.
Their diverse skills and perspectives will provide a comprehensive review of the processes.
3. Develop an Audit Plan
An audit plan serves as a roadmap for the auditing process.
It includes timelines, checklists, and specific criteria that will be evaluated.
A well-structured plan ensures that the audit covers all necessary areas and adheres to deadlines.
4. Collect and Analyze Data
During the audit, the team gathers data through observations, document reviews, and interviews.
This information helps identify any non-conformities or areas for improvement.
Analyzing this data is crucial for understanding the current state of quality and pinpointing issues.
5. Report Findings
Once the data is analyzed, the audit team should compile a detailed report of their findings.
This report should highlight strengths, identify weaknesses, and provide actionable recommendations.
Clear and concise reporting is essential for addressing identified issues effectively.
6. Implement Corrective Actions
The final step involves implementing the recommended corrective actions.
Management should prioritize these actions based on their potential impact on quality.
Ongoing monitoring ensures that the changes lead to continuous improvement.
Case Studies of Improvements in Manufacturing Quality Assurance
Case studies offer real-world examples of how manufacturing companies have effectively used quality audits to enhance their processes.
These stories illuminate best practices and provide valuable insights.
Case Study 1: Automotive Industry
An automotive manufacturer was encountering frequent defects in their assembly line.
A quality audit revealed that several critical components were not meeting the required specifications.
The audit team found inadequacies in the supplier management process, leading to inconsistent quality.
Upon these findings, the company implemented a robust supplier evaluation system.
They enhanced communication with suppliers and set stricter quality benchmarks.
As a result, defect rates dropped significantly, and customer satisfaction improved.
Case Study 2: Pharmaceutical Manufacturing
A pharmaceutical company faced regulatory compliance issues which posed a risk of legal penalties.
A comprehensive quality audit was conducted to assess all manufacturing processes and control measures.
The audit identified areas where documentation and process validations were lacking.
The company responded by updating its documentation practices and implementing electronic records for traceability.
They also introduced rigorous workforce training programs.
These changes ensured compliance with industry regulations and enhanced the overall reliability of their products.
Case Study 3: Food and Beverage Production
A food and beverage producer struggled with inconsistent product quality, leading to customer complaints.
A quality audit revealed that sanitation protocols were not being followed consistently.
Equipment maintenance records were also incomplete.
To address these issues, the company established stricter hygiene policies and conducted regular training sessions for employees on sanitation practices.
They also implemented a maintenance schedule and digital record-keeping.
The result was improved product quality and customer satisfaction.
The Importance of Continuous Improvement
Quality assurance is not a one-time task but an ongoing process.
Continuous improvement is vital to maintaining high standards in manufacturing.
Quality audits should be part of a larger quality management system that promotes regular evaluation and constant enhancement.
Always embrace innovation and be open to adopting new technologies and methodologies.
By doing so, companies can stay ahead of industry trends and maintain a competitive edge.
Conclusion
Quality audits are essential for ensuring excellence in manufacturing.
By following a structured process, companies can identify weaknesses and implement improvements effectively.
Learning from real-world case studies demonstrates the impactful changes that quality audits can bring.
Continuous improvement should be a core principle guiding all quality assurance activities.
This approach not only ensures compliance but also enhances overall operational efficiency and customer satisfaction.
Regular quality audits are a powerful tool in achieving and maintaining superior manufacturing standards.
資料ダウンロード
QCD調達購買管理クラウド「newji」は、調達購買部門で必要なQCD管理全てを備えた、現場特化型兼クラウド型の今世紀最高の購買管理システムとなります。
ユーザー登録
調達購買業務の効率化だけでなく、システムを導入することで、コスト削減や製品・資材のステータス可視化のほか、属人化していた購買情報の共有化による内部不正防止や統制にも役立ちます。
NEWJI DX
製造業に特化したデジタルトランスフォーメーション(DX)の実現を目指す請負開発型のコンサルティングサービスです。AI、iPaaS、および先端の技術を駆使して、製造プロセスの効率化、業務効率化、チームワーク強化、コスト削減、品質向上を実現します。このサービスは、製造業の課題を深く理解し、それに対する最適なデジタルソリューションを提供することで、企業が持続的な成長とイノベーションを達成できるようサポートします。
オンライン講座
製造業、主に購買・調達部門にお勤めの方々に向けた情報を配信しております。
新任の方やベテランの方、管理職を対象とした幅広いコンテンツをご用意しております。
お問い合わせ
コストダウンが利益に直結する術だと理解していても、なかなか前に進めることができない状況。そんな時は、newjiのコストダウン自動化機能で大きく利益貢献しよう!
(Β版非公開)