- お役立ち記事
- How to develop and utilize data analysis personnel in quality control in the manufacturing industry
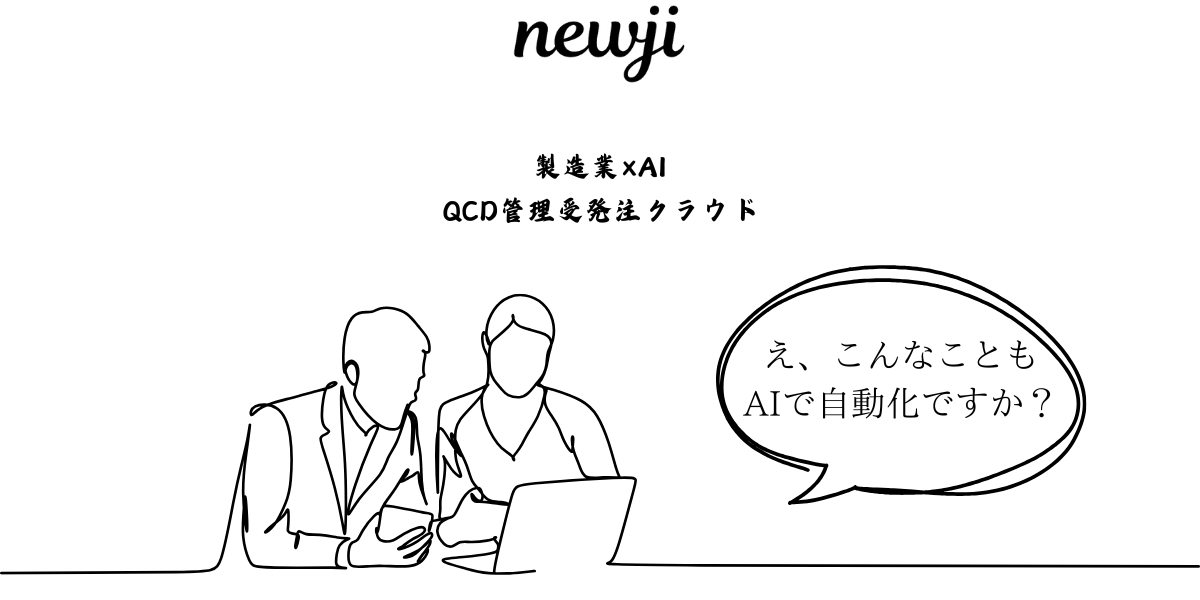
How to develop and utilize data analysis personnel in quality control in the manufacturing industry
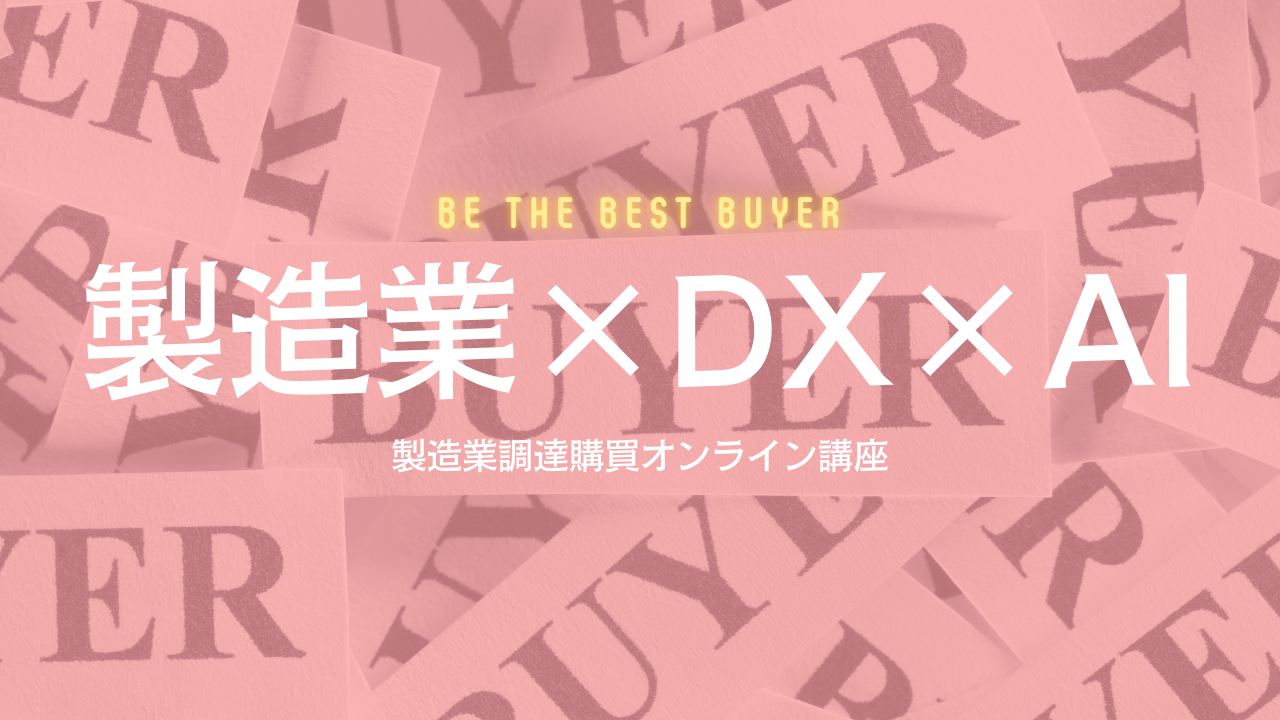
Data is one of the most important assets for any manufacturing company in today’s competitive landscape. Having the right people to analyze all the data your company collects and uses it to drive better quality control and decision making can provide a real competitive advantage. In this article, we will discuss how to develop and utilize data analysis personnel to take your company’s quality control to the next level.
目次
Hire The Right People
The first step is to identify the types of data analyst roles you need and hire people with the appropriate skills and experience. For quality control, you will likely need business intelligence analysts, statistical analysts, and data scientists. Look for candidates with backgrounds in statistics, data modeling, reporting, and data visualization. Experience in manufacturing quality systems is a big plus. Don’t just look for technical skills – analytical thinking, communication skills, and business acumen are also important.
Provide Training And Support
Even the most experienced hires will need some on-boarding training to understand your specific manufacturing processes, quality metrics, data collection methods, and systems. Create a training plan that combines both classroom and on-the-job learning. Make sure to provide ongoing support, coaching and mentoring as new analysts get familiar with your operations. Encourage collaboration between different roles and departments.
Define Key Metrics And KPIs
Work closely with data analysts, engineers, and production managers to define the key metrics and KPIs that are most important for monitoring and improving quality control. Focus on metrics that directly impact things like defects, scrap rates, rework, downtime, compliance and customer satisfaction. Make sure metrics can be easily measured and tracked over time to spot trends and issues.
Collect The Right Data
Not all data is created equal for quality purposes. Identify the most relevant sources of operational, transactional and sensor data related to defects, processes, materials and equipment performance. Consider investing in new sensors, IIoT systems or databases as needed to close any data gaps. Work with IT to ensure high quality, well-organized data that analysts can easily access, cleanse and model.
Perform Robust Analyses
Leverage the full capabilities of your analysts. Have them conduct sophisticated modeling, predictive analysis, process control charting, machine learning and other advanced techniques to gain deep insights from manufacturing data. Examples include defect prediction and clustering, process capability analysis, sources of variation studies, and equipment health monitoring. The goal is to surface hidden problems and opportunities for improvement.
Communicate Findings Effectively
It does no good if the great work of analysts sits on a shelf. Partner with them to clearly communicate findings and recommendations through compelling reports, dashboards, presentations and discussions. Visualize complex analyses in easy-to-understand graphs and charts. Socialize results throughout the organization to drive awareness and buy-in for quality initiatives. Empower frontline teams to take appropriate actions based on data.
Implement Improvement Actions
The final stage is where the real value is realized. Work with cross-functional teams to prioritize and act upon the highest impact opportunities uncovered through analysis. This may involve tweaks to processes, materials, equipment setups, training programs or supplier relationships. Continuously monitor impact of changes through data to ensure benefits are achieved. Empower analysts to continuously scan for new problem areas or ways to further improve quality and efficiency over time.
Developing and empowering a team of data analysts dedicated to mining your manufacturing quality data can yield tremendous benefits if properly cultivated and supported. With the right skills, strategies and collaborative approach described, companies have achieved breakthrough reductions in defects, higher throughput, and enhanced customer satisfaction levels. Start small, pilot initiatives, and continuously evolve your approach – the opportunities to drive impact are endless when quality decisions are informed by facts over assumptions.
In summary, effective utilization of data analysis personnel requires investing in the right talent, defining clear goals, collecting robust data sources, conducting sophisticated analyses, socializing results organization-wide, acting on high-impact findings, and continuously innovating quality strategies based on emerging insights. Any manufacturing company that masters this approach will undoubtedly gain a significant competitive edge through world-class quality, efficiency and customer experience.
資料ダウンロード
QCD調達購買管理クラウド「newji」は、調達購買部門で必要なQCD管理全てを備えた、現場特化型兼クラウド型の今世紀最高の購買管理システムとなります。
ユーザー登録
調達購買業務の効率化だけでなく、システムを導入することで、コスト削減や製品・資材のステータス可視化のほか、属人化していた購買情報の共有化による内部不正防止や統制にも役立ちます。
NEWJI DX
製造業に特化したデジタルトランスフォーメーション(DX)の実現を目指す請負開発型のコンサルティングサービスです。AI、iPaaS、および先端の技術を駆使して、製造プロセスの効率化、業務効率化、チームワーク強化、コスト削減、品質向上を実現します。このサービスは、製造業の課題を深く理解し、それに対する最適なデジタルソリューションを提供することで、企業が持続的な成長とイノベーションを達成できるようサポートします。
オンライン講座
製造業、主に購買・調達部門にお勤めの方々に向けた情報を配信しております。
新任の方やベテランの方、管理職を対象とした幅広いコンテンツをご用意しております。
お問い合わせ
コストダウンが利益に直結する術だと理解していても、なかなか前に進めることができない状況。そんな時は、newjiのコストダウン自動化機能で大きく利益貢献しよう!
(Β版非公開)