- お役立ち記事
- How to effectively proceed with BOM construction
How to effectively proceed with BOM construction
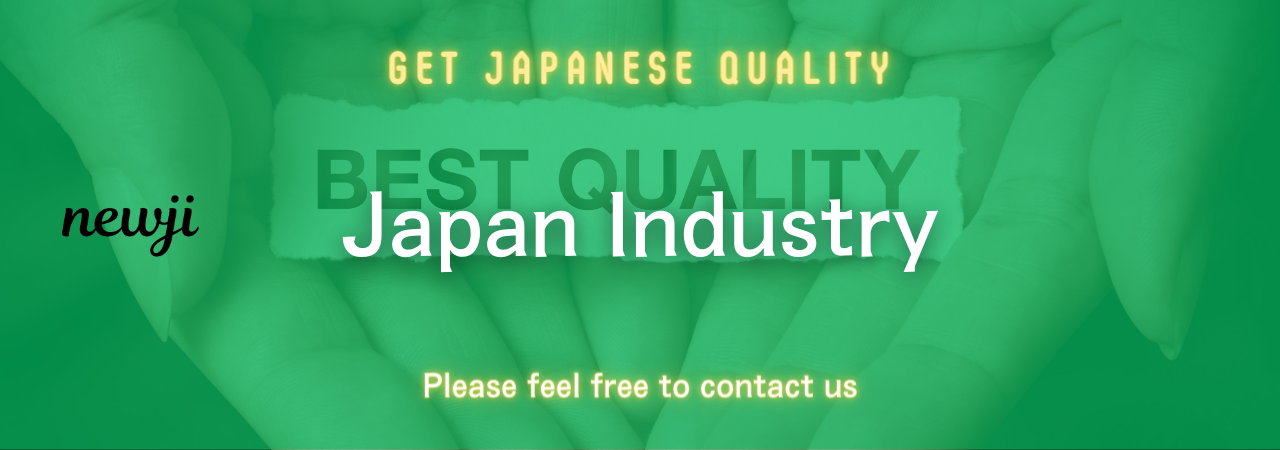
目次
Understanding BOM: What It Is and Why It Matters
A Bill of Materials (BOM) is a comprehensive list of parts, items, assemblies, and other components required to create a product.
It’s an essential part of manufacturing and production processes, helping to ensure that everything stays organized and on track.
The BOM serves as a guide for what needs to be ordered and how the product will be assembled.
Understanding the elements of a BOM and how it fits into your overall production process is key to its effective construction and utilization.
Types of BOMs
There are several types of BOMs, and choosing the right one depends on your specific needs and production process.
Manufacturing BOM (MBOM)
The Manufacturing BOM includes all the parts and assemblies to build a product.
It specifies how parts fit together for the manufacturing process, including part numbers, descriptions, quantities, and units of measure.
The MBOM also includes information on how products will be created from the components specified.
It’s used primarily by the manufacturing team to construct the product.
Engineering BOM (EBOM)
The Engineering BOM is developed by the design team during the product design phase.
It contains the conceptual drawings, diagrams, and specifications outlining the components used to create the product’s design.
The EBOM can differ from the MBOM as it might include parts that aren’t needed in the manufacturing process but are crucial for design.
Sales BOM (SBOM)
A Sales BOM is used for products that are sold as a complete unit, where the final product is composed of various components or parts.
It details what each level contains and how components fit together to form the final product.
The SBOM helps sales teams understand what they are selling and set accurate customer expectations.
Steps to Effectively Build a BOM
If you’re looking to construct a BOM effectively, follow these detailed steps.
Define the Product Structure
Begin by defining your product structure.
Understand the hierarchy and the relationship between various components and subassemblies.
Clearly categorize which items are raw materials, components, or finished goods.
A well-defined product structure simplifies BOM creation and keeps it organized.
Gather All Necessary Information
To create an accurate BOM, gather all relevant information, including part numbers, descriptions, quantities, units of measure, procurement information, and supplier details.
Ensure that each component has a unique identifier to avoid confusion during the manufacturing process.
Choose the Right Software
Using BOM management software can simplify and streamline the entire process.
Look for software that supports version control, integrates with existing systems, and allows for easy updates and modifications.
Good software helps in maintaining consistency and accuracy.
Focus on Accuracy and Detail
BOMs require a high degree of accuracy and detail.
Double-check all part numbers, quantities, and descriptions.
Mistakes in a BOM can lead to production delays, increased costs, and customer dissatisfaction.
Involving several team members in the review process can ensure accuracy and reduce errors.
Maintain Version Control
Always maintain version control for your BOMs.
As products develop, parts might change, or production methods might adapt.
Recording and tracking each version of a BOM helps in understanding changes and managing consistency.
Version control also aids in troubleshooting if issues arise.
Update Regularly
The BOM should be a living document updated with every change in product design or manufacturing process.
Regular updates prevent the use of outdated components, saving time and resources.
Timely updates also ensure that everyone involved in production has the most current data.
Challenges in BOM Construction
Creating and maintaining a BOM can come with its set of challenges.
Data Management
Handling vast data sets can be overwhelming.
Ensuring that all data is organized and accessible is a crucial part of effective BOM management.
Data management tools and software can be invaluable here.
Collaboration Issues
BOM construction often requires input from several departments including engineering, manufacturing, purchasing, and sales.
Ensuring that all departments effectively collaborate and communicate can be challenging but is necessary for BOM accuracy.
Change Management
Managing changes across multiple departments and components can be complicated.
Establishing clear procedures for change requests and ensuring all changes are tracked and updated in real-time is essential.
The Importance of a Well-Constructed BOM
Effective BOM construction yields several benefits:
– **Improved Efficiency:** With a clear understanding of required materials and manufacturing steps, production teams work more efficiently.
– **Cost Reduction:** By accurately knowing what materials and components are needed, organizations can order the right quantities, reducing waste and lowering costs.
– **Enhanced Product Quality:** A detailed and accurate BOM helps ensure products are built correctly with the right materials, improving overall quality.
– **Better Communication:** A well-documented BOM improves communication across departments, ensuring everyone is on the same page.
Concluding, a well-constructed BOM is a critical component of successful product management and manufacturing.
By understanding its importance and following steps for effective construction, businesses can enhance efficiency, reduce costs, and improve product quality.
資料ダウンロード
QCD調達購買管理クラウド「newji」は、調達購買部門で必要なQCD管理全てを備えた、現場特化型兼クラウド型の今世紀最高の購買管理システムとなります。
ユーザー登録
調達購買業務の効率化だけでなく、システムを導入することで、コスト削減や製品・資材のステータス可視化のほか、属人化していた購買情報の共有化による内部不正防止や統制にも役立ちます。
NEWJI DX
製造業に特化したデジタルトランスフォーメーション(DX)の実現を目指す請負開発型のコンサルティングサービスです。AI、iPaaS、および先端の技術を駆使して、製造プロセスの効率化、業務効率化、チームワーク強化、コスト削減、品質向上を実現します。このサービスは、製造業の課題を深く理解し、それに対する最適なデジタルソリューションを提供することで、企業が持続的な成長とイノベーションを達成できるようサポートします。
オンライン講座
製造業、主に購買・調達部門にお勤めの方々に向けた情報を配信しております。
新任の方やベテランの方、管理職を対象とした幅広いコンテンツをご用意しております。
お問い合わせ
コストダウンが利益に直結する術だと理解していても、なかなか前に進めることができない状況。そんな時は、newjiのコストダウン自動化機能で大きく利益貢献しよう!
(Β版非公開)