- お役立ち記事
- How to integrate quality control and efficiency in procurement processes led by purchasing departments
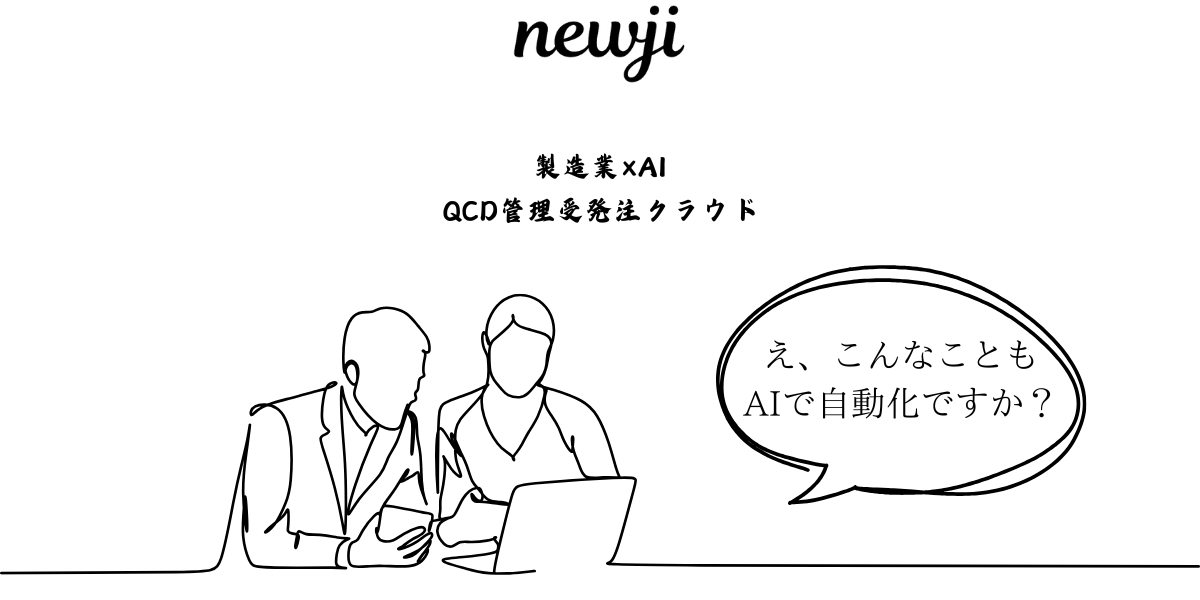
How to integrate quality control and efficiency in procurement processes led by purchasing departments
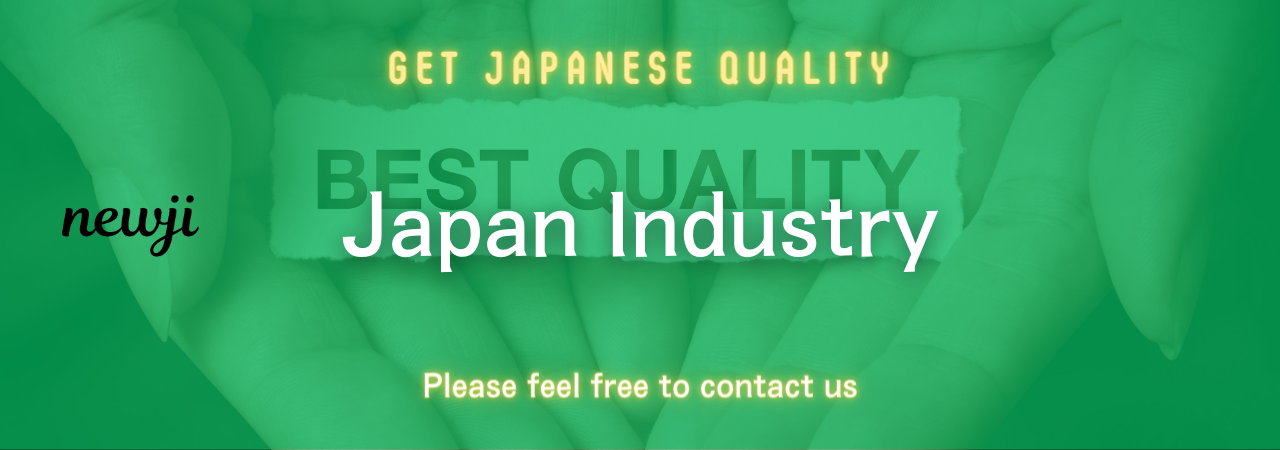
目次
Understanding the Role of Procurement in Business
Procurement is an essential function of any business, playing a critical role in acquiring the goods and services needed to maintain operations.
Led by purchasing departments, procurement involves identifying needs, selecting suppliers, negotiating contracts, and ensuring quality.
However, the challenge many businesses face is integrating quality control and efficiency within procurement processes.
The Importance of Quality Control
Quality control in procurement ensures that the products and services a company purchases meet predetermined standards.
Without a focus on quality, businesses risk obtaining subpar goods that could lead to operational disruptions, increased costs, or even damage to company reputation.
Thus, quality control must be a fundamental part of the procurement process to ensure that only reliable and high-standard products are acquired.
Efficiency in Procurement Processes
Efficiency in procurement is about optimizing processes to save time and reduce costs while maintaining effectiveness.
Efficient procurement processes require streamlined operations, minimizing unnecessary steps, and avoiding delays.
This can be achieved through better inventory management, automation, and improved communication with suppliers.
Integrating Quality and Efficiency
Balancing quality control and efficiency in procurement can be challenging but achievable.
Here are some strategies and best practices for purchasing departments to integrate both:
Implementing Standards and Guidelines
One of the first steps towards integration is to establish clear standards and guidelines for procurement activities.
This includes setting benchmarks for product quality and service delivery.
Having defined criteria for supplier evaluation helps purchasing departments maintain consistency and ensures that suppliers meet the required quality standards.
Leveraging Technology
The use of technology is crucial in enhancing both quality and efficiency.
Procurement departments can benefit from e-procurement systems that automate and streamline purchasing processes.
These systems allow for real-time tracking, reduce paperwork, and expedite the purchasing cycle.
Moreover, technology like data analytics can help in forecasting demand and managing supplies more effectively, ensuring better decision-making.
Regular Supplier Assessment
Consistent supplier assessments are important to ensure suppliers continue to meet both quality and efficiency standards.
This involves not just initial evaluations but ongoing performance reviews.
Creating strong relationships with suppliers can also lead to better cooperation and quality improvements.
Training and Development
Investing in training for the procurement team is essential to equip them with the skills necessary for balancing quality and efficiency.
This includes training on negotiation, supplier relationship management, and quality assurance techniques.
A well-trained team can make informed decisions that align with the company’s quality and efficiency goals.
Case Studies and Examples
To better understand how quality control and efficiency can be integrated, let’s look at some examples from leading companies:
Case Study 1: Tech Corp
Tech Corp, a leading technology company, reduced its procurement costs by implementing an advanced e-procurement system.
This allowed them to automate supplier assessments and purchase orders.
They also established a rigorous quality assurance protocol, ensuring that only certified products were accepted, thus integrating quality control into their efficient system.
Case Study 2: Retail Giant
Retail Giant, a large retail chain, focused on building strong supplier partnerships.
They implemented a supplier scorecard system that measured suppliers on quality, delivery time, and cost-effectiveness.
This approach enabled them to maintain high quality standards while enhancing procurement efficiency.
Conclusion and Key Takeaways
Integrating quality control and efficiency in procurement processes is essential for the smooth operation and success of any business.
By setting clear guidelines, leveraging technology, conducting regular supplier assessments, and investing in team development, companies can achieve a balanced approach that maximizes both quality and efficiency.
Purchasing departments that adopt these strategies can not only meet current needs but also position themselves for future growth and success.
資料ダウンロード
QCD調達購買管理クラウド「newji」は、調達購買部門で必要なQCD管理全てを備えた、現場特化型兼クラウド型の今世紀最高の購買管理システムとなります。
ユーザー登録
調達購買業務の効率化だけでなく、システムを導入することで、コスト削減や製品・資材のステータス可視化のほか、属人化していた購買情報の共有化による内部不正防止や統制にも役立ちます。
NEWJI DX
製造業に特化したデジタルトランスフォーメーション(DX)の実現を目指す請負開発型のコンサルティングサービスです。AI、iPaaS、および先端の技術を駆使して、製造プロセスの効率化、業務効率化、チームワーク強化、コスト削減、品質向上を実現します。このサービスは、製造業の課題を深く理解し、それに対する最適なデジタルソリューションを提供することで、企業が持続的な成長とイノベーションを達成できるようサポートします。
オンライン講座
製造業、主に購買・調達部門にお勤めの方々に向けた情報を配信しております。
新任の方やベテランの方、管理職を対象とした幅広いコンテンツをご用意しております。
お問い合わせ
コストダウンが利益に直結する術だと理解していても、なかなか前に進めることができない状況。そんな時は、newjiのコストダウン自動化機能で大きく利益貢献しよう!
(Β版非公開)